good-to-know
Die Werkstoffe in Triebwerken
Die Anforderungen an Werkstoffen in Triebwerken sind enorm. Doch welche Materialen spielen aktuell die größte Rolle – und welche in der Zukunft? Der AEROREPORT stellt die wichtigsten vor.
Autorin: Isabel Henrich | 8 Min. Lesezeit veröffentlicht am: 04.10.2022
Autorin:
Isabel Henrich
ist studierte Politologin und Kommunikationswissenschaftlerin. Bei der MTU steuert sie den redaktionellen Prozess des AEROREPORTs und ist zuständig für die Konzeption und Entwicklung der Inhalte.
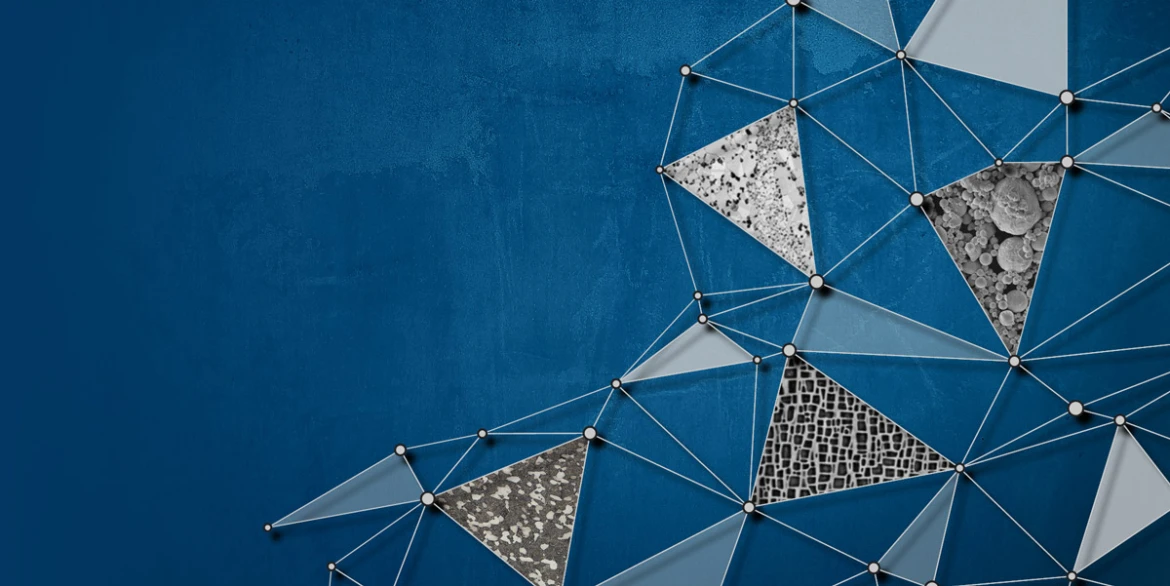
Seit mehreren Jahrzehnten sind vor allem metallische Werkstoffe, wie Nickel und Titan, fester Bestandteil von Bauteilen in Triebwerken. Die altbewährten Materialien werden stetig weiter optimiert, mit dem Ziel, Triebwerke noch leichter und sparsamer zu machen.
Für die zweite Generation Getriebefan, die Anfang nächster Dekade abheben soll, und im zukünftigen militärischen Antrieb Next European Fighter Engine (kurz: NEFE) müssen die Bauteile noch hitzebeständiger, leichter und langlebiger werden. Außerdem sollen die Werkstoffe noch robuster in Herstellung und Betrieb werden. Hier rücken daher verbesserte Nickel-Superlegierungen und Beschichtungen, Herstellprozesse wie Einkristallguss und pulvermetallurgische Verfahren sowie additive Fertigung und Materialien wie faserverstärkte Werkstoffe stärker in den Fokus. Sie helfen das Gewicht zu reduzieren und erlauben gleichzeitig erhöhte Lebensdauern bei erhöhten Anwendungstemperaturen.
In zivilen Triebwerken liegen die zukünftigen Herausforderungen zudem in ganz neuen Atmosphären, in denen sich die Bauteile befinden. Bei dem MTU-Konzept Water-Enhanced Turbofan, einer Fluggasturbine mit Energierückgewinnung und nasser Verbrennung, ebenso wie bei der Wasserstoff-Direktverbrennung, sind die Bauteile einer in hohem Maße wasserdampfhaltigen Umgebung ausgesetzt und kommen mit mehr molekularem Wasserstoff als bei konventionellen Fluggasturbinen in Kontakt. Hier sind also spezielle Beschichtungen gefragt, die die Werkstoffe vor beschleunigter Oxidation sowie Korrosion und Versprödung ausreichend schützen. Bei der Flying Fuel Cell (FFC), einem weiteren revolutionären Antriebskonzept der MTU, müssen zusätzlich für den Triebwerksbau gänzlich neue Werkstoffe mit neuen Funktionen eingesetzt werden. Dies machen neuartige Komponenten wie Wasserstoff-Brennstoffzellen, Kühlsysteme und Hochleistungs-Elektromotoren samt ausgeklügelter Leistungselektronik für das Antriebssystem notwendig. Durch den elektrifizierten Antriebsstrang spielen hier etwa Funktionswerkstoffe mit spezifischen elektrisch-chemisch-magnetischen und katalytischen Eigenschaften eine große Rolle.
Um den Aufwand für die notwendigen Entwicklungen zu reduzieren, die Materialien stetig zu optimieren und um bei Qualitätsbewertungen effizienter zu werden, ist der Einsatz weiter verbesserter Computersimulationen unerlässlich.
Die wichtigsten Werkstoffe und zugehörige Methoden in Triebwerken – bereits im Einsatz oder noch Zukunftsmusik – stellt der AEROREPORT hier vor.
1. Nickel, Titan und ihre Herstellvarianten
1.1 Nickelbasis-Superlegierungen:
Nickelbasis-Superlegierungen sind Werkstoffe, die zu fast zwei Dritteln aus Nickel bestehen. Sie sind typischerweise mit einer hohen Zahl von Zusatzelementen legiert, die eine, für diese Metalle kennzeichnende, netzartige Mikrostruktur ermöglichen. Sie werden mit verschiedenen Verfahren hergestellt, darunter Gießen (auch als Einkristalle), Schmieden, Pulververfahren, additive Fertigung und Spritzgießen.
Vorteile: Das hervorstechendste Merkmal von Nickelbasis-Superlegierungen ist die – selbst bei sehr hohen Temperaturen - unvermindert hohe Festigkeit. Diese haben sie einer speziellen, fein ausgebildeten Mikrostruktur zu verdanken. Zudem besitzen sie eine gute Korrosionsbeständigkeit. Beides sind die wichtigsten Gründe, warum sie im Triebwerksbau Stählen vorgezogen werden.
Einsatzbereiche im Triebwerk: Alle Bauteiltypen, vor allem im heißen Bereich des Triebwerks, wie im hinteren Verdichter, der Brennkammer und Turbine.
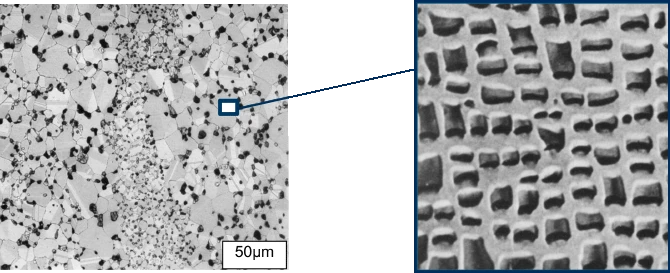
Typisches Werkstoffgefüge einer Nickelbasis-Superlegierung. Die Vergrößerung zeigt das charakteristische, mikrostrukturelle Merkmal der quaderförmigen, sogenannten γ‘-Ausscheidung, (einer intermetallischen Phase) in der metallischen γ-Matrix. Diese spezielle Struktur ermöglicht – neben Legierungszusätzen mit schweren Elementen – hohe Festigkeiten bis zu hohen Temperaturen.
1.2 Nickelbasis-Superlegierungen als Einkristallvarianten:
Sie werden durch spezielle Gussverfahren ohne Korngrenzen, also als ein durchgehender Kristall, hergestellt. Sie verhalten sich deshalb anisotrop – bedeutet: in verschiedene Richtungen unterschiedlich. Typischerweise sind sie für den Einsatz bei höchsten Temperaturen vorgesehen und müssen deshalb durch Schichten geschützt werden. Ihre Eigenschaften verdanken sie zudem einigen besonders teuren und schweren Legierungselementen.
Vorteile: Durch das Fehlen der schwächenden Korngrenzen, den Zusatz spezieller, schwerer Elemente und die Möglichkeit, das anisotrope Verhalten gezielt auszunutzen, können Einkristalle bei höchsten Temperaturen, nicht weit von ihrem Schmelzpunkt entfernt, eingesetzt werden.
Einsatzbereiche im Triebwerk: Bauteile mit höchster Temperaturbelastung im vorderen Teil der Turbine, vor allem als rotierende und statische Schaufeln.
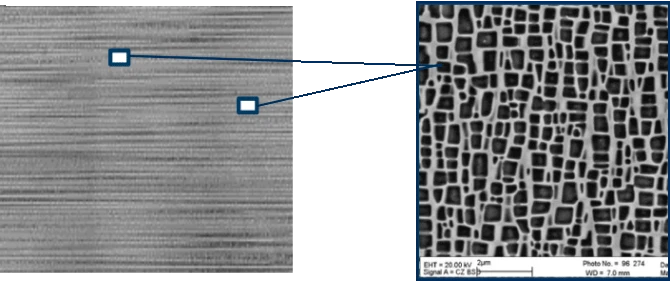
Als Spezialfall der Nickelbasis-Superlegierungen, zeigen die Bilder das Gefüge eines einkristallin hergestellten Werkstoffes. Links erkennt man das Fehlen von Korngrenzen, rechts die bei einkristallinen Nickellegierungen besonders ausgeprägt netzartige Mikrostruktur der γ‘-Ausscheidungen.
1.3 Titanlegierungen:
Hauptbestandteil von Titanlegierungen ist Titan. Mit den im Triebwerksbau zugesetzten Legierungselementen und durch die Wahl der Herstellparameter können sehr unterschiedliche, typischerweise lamellenförmig oder globular erscheinende Mikrostrukturen mit unterschiedlichen Vorteilen erstellt werden. Dabei spielen die Anteile und Formen der beteiligten mikroskopischen Phasen die entscheidende Rolle. Titan ist zwar ein häufig vorkommendes Element der Erdkruste, verbindet sich aber gerne mit Sauerstoff. Das verteuert die Gewinnung reinen Titans und ist in der Herstellung und im Betrieb zu beachten. Die für Titanlegierungen verwendeten Herstellverfahren sind dieselben, wie auch die bei den Nickellegierungen erwähnten, mit Ausnahme des Einkristallgusses.
Vorteile: Titanlegierungen haben eine ähnlich hohe Festigkeit wie Nickelbasislegierungen, wiegen aber nur die Hälfte und zeichnen sich durch gute Verarbeitbarkeit sowie Korrosionsbeständigkeit aus. Ihre maximale Einsatztemperatur ist im Vergleich zu Nickellegierungen jedoch deutlich niedriger. Gegenüber Stählen bzw. Aluminium sind Titanlegierungen wegen der Korrosionsbeständigkeit und der Festigkeit im Vorteil.
Einsatzbereiche im Triebwerk: Alle Bauteiltypen, vor allem im vorderen Bereich des Triebwerks bis zum mittleren Verdichter.
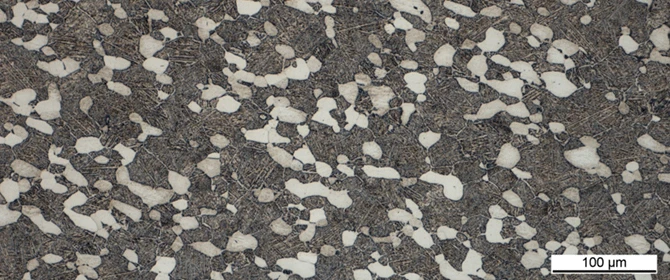
Gefüge von Titanlegierungen in Flugtriebwerken sind vor allem durch die Anteile und Struktur zweier Phasen (α / weiß und β / dunkel) gekennzeichnet. Typischerweise sind die Strukturen lamellenartig und globular. Im Beispiel des Bildes sind beide Ausprägungen gemischt, eine sogenannte bimodale Struktur.
1.4 Pulvermetallurgische Werkstoffe:
Bei der Pulvermetallurgie werden aus der Schmelze durch Verdüsen Pulverpartikel erzeugt. Sie werden in der Luftfahrt mit verschiedenen Verfahren, wie Heiß-Isostatisches Pressen (HIP) und anschließendem Schmieden, additivem Aufbau (AM) oder Metallformspritzen (MIM) zum Bauteil weiter verarbeitet. Als chemische Zusammensetzungen kommen verschiedene der bereits beschriebenen Metalle oder deren Modifikationen in Frage.
Vorteile: Durch die Herstellung über Pulverpartikel können mit dieser Technik Zusammensetzungen verwendet und Qualitäten erreicht werden, die mit anderen Produktionsverfahren nicht möglich sind. Das führt etwa zu sehr feinkörnigen und homogenen Werkstoffen, die besonders gute mechanische und thermische Eigenschaften haben. Einen anderen Vorteil bieten die Verfahren, die das Pulver nicht mehr schmieden, sondern gleich in Form bringen, da man hier bereits nahe der finalen Kontur ist und somit teures Material und Bearbeitungszeit spart.
Einsatzbereiche im Triebwerk: Aufgrund der unterschiedlich einsetzbaren Werkstoffe und Weiterverarbeitungsverfahren ist die Pulvermetallurgie für verschiedenste Bauteile in verschiedenen Komponenten geeignet. Je nach Verfahren handelt es sich typischerweise um Bauteile mit komplexer Geometrie oder besonders hohen Anforderungen.
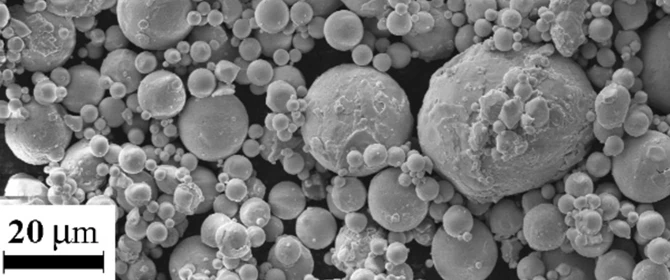
Metallische Pulverpartikel (hier: Nickel-Superlegierung). Qualitätsmerkmale sind vor allem die Reinheit von Fremdpartikeln, die Durchmesserverteilung, die Form und Oberflächenbeschaffenheit sowie die chemische Verteilung und das Gefüge im Innern der Partikel.
1.5 Additiv hergestellte Werkstoffe:
Bei der additiven Bauteilherstellung wird Material sukzessive positioniert und mit dem schon vorhandenen Material verbunden. Das kann etwa durch Aufschmelzen von Draht oder Pulverpartikeln mittels Laser oder Elektronenstrahl erfolgen und erfordert besonderes Augenmerk auf die Qualitätssicherung. Die verwendeten Werkstoffe decken ein breites Spektrum ab – darunter vor allem die bereits beschriebenen Metalle, für Demonstrationszwecke auch Kunststoffe.
Vorteile: Das Verfahren ermöglicht komplexe Geometrien, meist nahe der Endkontur – es kann bei entsprechenden Recyclingkonzepten eine hohe Materialausbeute erreicht werden. Zudem können bei Bedarf auch nicht anderweitig verarbeitbare Legierungen hergestellt sowie die Werkstoffqualität im Bauteil je nach Position variiert und damit den unterschiedlichen Belastungen angepasst werden.
Einsatzbereiche im Triebwerk: Wegen der unterschiedlich einsetzbaren Werkstoffe sind additiv hergestellte Werkstoffe grundsätzlich für verschiedenste Bauteile in verschiedenen Komponenten geeignet. Auswahlkriterien gegenüber herkömmlichen Herstellverfahren sind mögliche Kosten- oder Gewichtsvorteile bei komplexen Geometrien. Auch erlauben diese Herstellverfahren eine kurzfristige Bereitstellung und Modifikation für kleine Mengen, etwa in Demonstratoren.
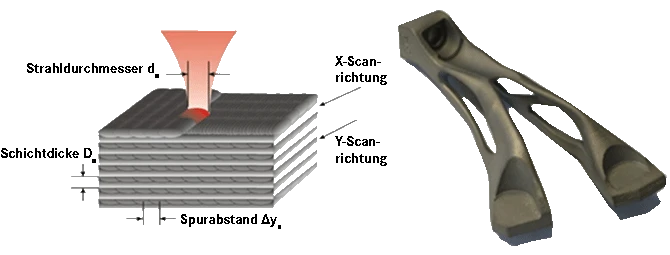
Links: Additiver Werkstoffaufbau: Hier am Beispiel des sukzessiven, lokalen Aufschmelzens von Pulverlagen mit dem Laser.
Rechts: Die additive Fertigung bietet hohe Freiheitsgrade um komplexe Strukturen für den Leichtbau herzustellen.
2. Faserverstärkte Kunststoffe als Vertreter der Verbundwerkstoffe:
Faserverstärkte Kunststoffe sind sogenannte Verbundmaterialien, das heißt sie bestehen aus zwei völlig unterschiedlichen Komponenten. Dabei werden hochfeste Fasern aus verschiedenen Werkstoffen, etwa Kohlenstoff, die in verschiedener Weise miteinander verwebt wurden, in eine Matrix aus Kunststoff (Polymere) eingebettet. Diese Werkstoffe haben eine ausgeprägte Richtungsabhängigkeit und sind trotz ihrer komplexen Herstelltechnik meist nicht teurer als die alternativen, metallischen Sonderwerkstoffe im Triebwerk.
Vorteile: Sehr geringes Gewicht, richtungsabhängig hohe Festigkeiten, eine höhere Schadenstoleranz als die Matrix alleine – allerdings gegenüber Metallen eine eingeschränkte Verformbarkeit.
Einsatzbereiche im Triebwerk: Bauteile im niedrigeren Temperaturbereich, deren Geometrie sich mit der typischen Herstelltechnik produzieren lassen. Damit liegen die Zielkomponenten im vorderen Bereich des Verdichters und den umgebenden Bauteilen. Zum Schutz vor Fremdpartikeln und bei hohen Belastungen müssen ergänzende Maßnahmen getroffen werden.
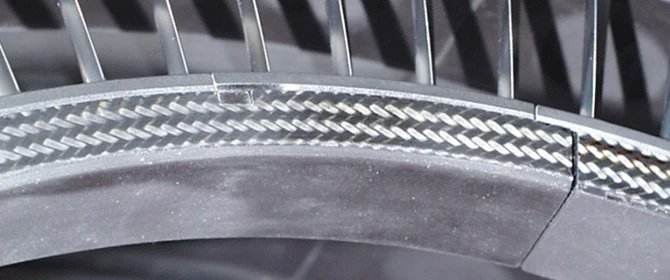
Faserverstärkte Kunststoffe setzen sich aus zwei völlig unterschiedlichen Komponenten zusammen: Wie Textilien gewebte, feste Fasern, die in eine Kunststoffmatrix eingebettet sind. Am Beispiel eines Innenrings lässt sich diese Struktur an der Oberfläche gut erkennen.
3. Funktionswerkstoffe:
Der Begriff Funktionswerkstoffe ist sehr weit gefasst. Er vereint Materialien, bei denen – im Gegensatz zu Strukturwerkstoffen – nicht ihre eigene Tragfähigkeit und Form, sondern ihre Funktion für benachbarte Materialien oder das Gesamtsystem im Vordergrund stehen. So sind etwa auch Schichten Funktionswerkstoffe. Ebenso zählen Werkstoffe und Bauteile im Triebwerk dazu, die beispielsweise elektrochemische, magnetische oder akustische Funktionen erfüllen.
3.1 Schichten als Vertreter der Funktionswerkstoffe:
Die Beschichtungen in Triebwerken zeichnen sich durch eine besonders große Vielfalt bezüglich Werkstoff, Herstellverfahren, Struktur und Funktion aus. So werden Kunststoffe, Metalle und Keramiken zum Teil miteinander verwendet. Die Schichten werden eindiffundiert, aufgespritzt, aufgedampft oder halbflüssig aufgebracht; sie sehen im Mikroskop homogen oder stark strukturiert aus. Mehr als 60 Prozent der Triebwerksbauteile sind beschichtet.
Vorteile: Mit Schichten lässt sich die Lebensdauer von Bauteilen um ein Vielfaches verlängern. Der Schutz ist vielfältig: Er dient dem Widerstand gegen mechanischen Abrieb von Fremdpartikeln oder benachbarten Bauteilen, dem Verhindern chemischer Angriffe wie Korrosion und Oxidation, der Wärmeisolation und der Begrenzung von Feuer. Schichten können aber auch abgeriebenes Material oberflächlich ausgleichen.
Einsatzbereiche im Triebwerk: Nahezu an allen Positionen im Triebwerk und bei allen Bauteilen entsprechend der beschriebenen Funktionen.
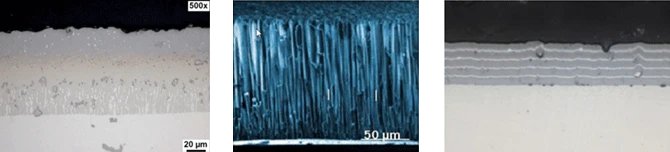
Schutzschichten in Flugtriebwerken zeichnen sich durch eine große Vielfalt der enthaltenen Werkstoffe und der Strukturen aus. Als Beispiele zeigen die Bilder links eine durch Diffusion in das Grundmaterial entstandene, aluminiumhaltige Korrosionsschutzschicht, in der Mitte eine aufgedampfte, in Stängeln gewachsene, keramische Wärmedämmschicht und rechts eine lagig aufgebrachte Erosionschutzschicht mit wechselnden harten und schadenstoleranteren Schichtanteilen.
4. Die werkstoffübergreifende Methode der Simulationen:
Unter Werkstoffsimulationen sind alle computergestützten Analysen zur Entstehung eines Werkstoffes und zur Beschreibung seiner Eigenschaften zu verstehen. Da das Materialverhalten durch eine Kombination der Strukturen in verschiedenen, mikroskopischen Größenskalen – bis hin zu den Atomen – bestimmt wird, bedarf es auch unterschiedlicher mathematisch-physikalischer Methoden. Ihre Weiterentwicklung ist heute noch sehr dynamisch, nicht zuletzt wegen der Vielfalt an Werkstoffklassen und großer Rechenzeiten. Begrifflich sind Werkstoffsimulationen Teil der digitalen Werkstofftechnik und werden wegen ihrer Verknüpfung von Chemie und Herstellverfahren auch dem ICME (Integrated Materials and Manufacturing Engineering) zugerechnet.
Vorteile: Mit Werkstoffsimulationen lässt sich die Iterationsphase bei der Entwicklung eines Materials und seines Herstellverfahrens durch Einsparung von Tests an Proben deutlich verkürzen. Auch kann das Optimum von Werkstoffpotenzial und wirtschaftlicher Herstellung besser erreicht werden. Schließlich sind Qualitätsbewertungen für Design, Produktion und Einsatz schneller und präziser.
Einsatzbereiche im Triebwerk: Prinzipiell für alle Materialien und Positionen, jedoch aufgrund des Entwicklungsstandes noch nicht für alle Materialien und Fragestellungen verfügbar.
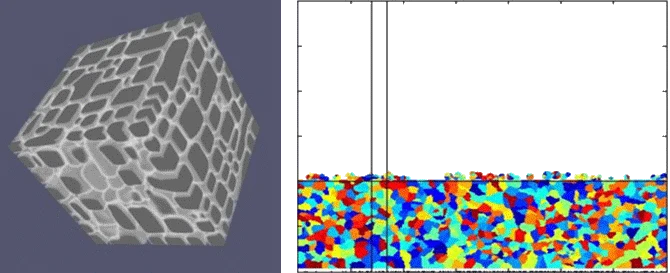
Werkstoffsimulationen dienen unter anderem der Vorhersage der Materialstruktur. Links ist das computergenerierte γ / γ‘ - Mikrogefüge eines Nickel-Basis-Einkristalls zu sehen, rechts die Entstehung einer additiv hergestellten Kornstruktur durch den senkrecht einfallenden Laserstrahl auf das Pulverbett an der Oberfläche. Die Farben kennzeichnen die verschiedenen Ausrichtungen der einkristallinen Körner.