innovation
Coatings in engines: Thermal techniques
More than half of all engine components receive thermal coatings. Dozens of different materials are available and these are applied using a wide variety of techniques.
author: Monika Weiner | 5 mins reading time published on: 06.11.2023
author:
Monika Weiner
has been working as a science journalist since 1985. A geology graduate, she is especially interested in new developments in research and technology, and in their impact on society.
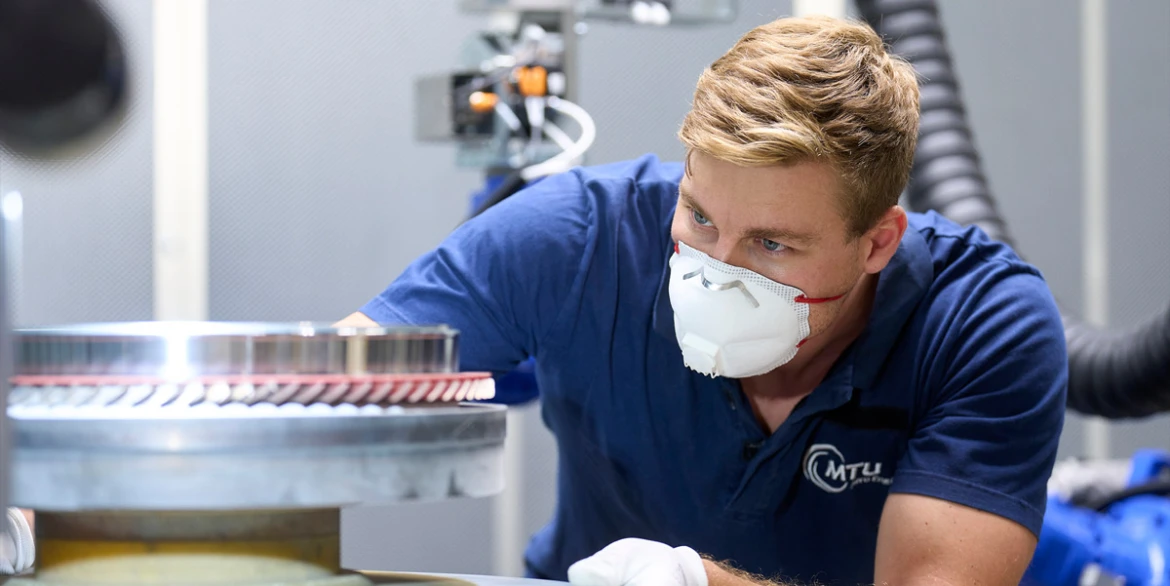
More than half of all engine components are enhanced with coatings. Thermal spraying alone offers a vast array of options, including flame spraying, high-velocity oxygen fuel spraying, wire arc spraying, and plasma spraying. These can be applied using a variety of burners and gases. Coating materials include hard and soft metals, alloys, ceramics, and composites. “The trick is knowing which of the many different materials and techniques available are right for the job,” says Stefan Schneiderbanger, Head of Production Development for Coatings at MTU Aero Engines.
Custom solutions rather than one-size-fits-all
Coatings can be wafer-thin or several millimeters thick. They can be porous or impermeable, brittle, malleable, or even feature ingredients that allow them to act like lubricants. “There are no one-size-fits-all solutions, only custom ones: each coating must be suitable and engineered for the recipient material. That’s the only way to end up with exactly the surface properties that the specific application prescribes,” Schneiderbanger explains.
But how do experts come up with these custom solutions? Schneiderbanger clearly recalls the day when a designer came to him to report a serious wear issue concerning the outer air seals in an engine that was being developed. Located in a circular arrangement in the low-pressure turbine, these shroud segments were being pushed against a piston ring at high pressure during operation. Such pressure can cause the surfaces of the two metal components to connect and then, through vibration for example, break apart and damage the material. To eliminate this vibration-friction wear, or fretting as it is known, Schneiderbanger’s team had to find a coating that would prevent direct contact between the materials as well as a highly precise way of applying it so as to avoid major reworking of the components. They coated more than a hundred test pieces before they hit upon the right balance of adhesion, hardness, porosity, and oxide content. It took a full year of development until the shroud segments could be coated as standard during production and installed in the engines. But it was well worth the effort. “We know we’ve done a good job when everything runs smoothly,” Schneiderbanger says.
Thermal coatings in production
Such breakthroughs are successful only when the specifications set by the development team are actually met in large-scale production. Dr. Andreas Jakimov, Head of Operations Scheduling for Thermal Spraying, and his team are responsible for making this happen: “We have 14 production systems for thermal coating at our disposal. As our colleagues in the workshop are responsible for the full spectrum of thermal techniques, having precise instructions for every component is essential.”
All these thermal coatings are applied behind closed doors in hermetically sealed chambers and is controlled by computer. Only once the coating process is complete and the air clean again do the doors open. At this point the components are ready for further processing.
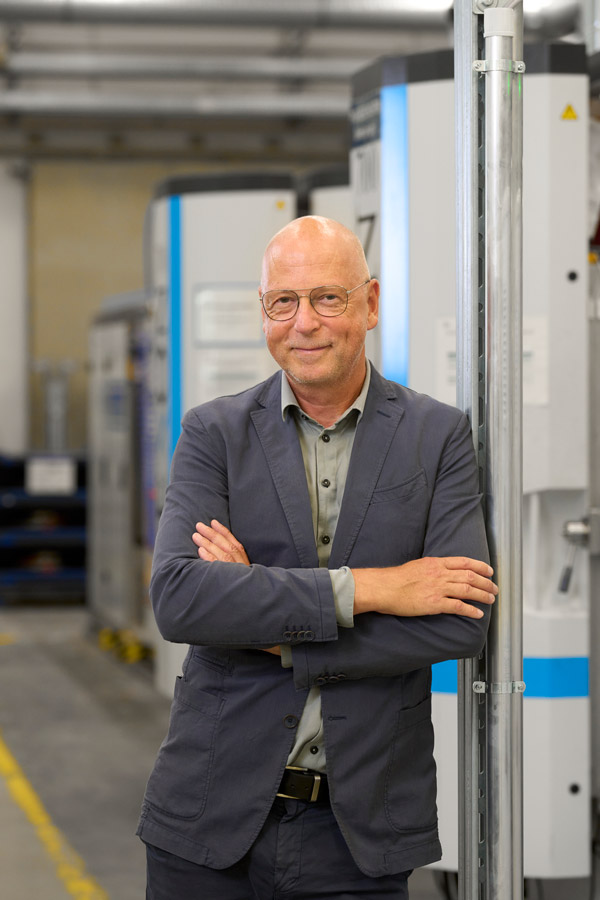
“The erosion protection coating ERCoat®, which MTU developed in-house, extends the life of airfoils by protecting them from a bombardment of sand and dust.”
Head of Operations Scheduling for PVD
Enhancements in an airless room
In contrast to thermal spraying, the coatings created using physical vapor deposition (PVD) technology have thicknesses in the micrometer range. A precondition for PVD is that it must take place in an airless room because air molecules would interfere with the deposition process. One job for PVD coatings is to provide blisks (blade integrated disks) in the compressor with erosion protection. As it’s only the blades and not the disks of blisks that receive the erosion protection coating, the experts load the blisks onto racks and cover the disks with metal protectors. When a rack is pushed into the vacuum chamber and the doors locked, only the blades are left exposed. A pump sucks the air out of the chamber, inert gas is pumped in, and the rack holding the blisks begins to rotate.
First, an ion beam is directed at the component surfaces to clean and physically activate them. For the actual coating process, an electric arc is ignited and vaporizes a chromium plate, which is the coating material. High electric voltages then discharge—similar to lightning during a thunderstorm. The metallic vapor condenses on the component surface, forming a crystalline layer just a few micrometers thick. For the next step, the arc vaporizes a chromium-aluminum alloy. Nitrogen has been introduced to the chamber so that the metal ions bond with it to produce metal nitride, which now condenses to add a thin ceramic layer. More layers are added, alternating between metal and ceramic, until the desired multilayered coating is complete.
“The layered structure ensures that the protective coating is very stable, thanks to the ceramic layers, but still possesses a certain plasticity due to the metal layers. This also has the advantage of making the coating less likely to crack,” explains Dr. Achim Meier, Head of Operations Scheduling for PVD. “The erosion protection coating ERCoat®, which MTU developed in-house, extends the life of airfoils by protecting them from a bombardment of sand and dust.” These particles have an effect on the airfoil surface similar to sandblasting. For airlines operating in regions with a high density of sand and dust in the air, erosion is a serious problem: it starts to distort the shape of the airfoils within just a few flight hours. ERCoat® reduces erosion and thus also maintenance costs.
Over the past few years, demand for erosion protection has increased dramatically. MTU is currently expanding its PVD production area. In the future, the company will have a new facility containing multiple PVD coating systems, including for pre- and post-processing. Once completed, this will create sufficient capacity to coat thousands of engine blisks every year.