people
New materials for the engines of the future
Sustainable engines call for advanced materials: MTU’s Dr. Jörg Eßlinger, Senior Consultant Materials, and Dr. Inga Stoll, Director Materials, share their expertise.
author: Nicole Geffert | 6 mins reading time published on: 14.09.2022
author:
Nicole Geffert
has been working as a freelance journalist covering topics such as research and science, money and taxes, and education and careers since 1999.
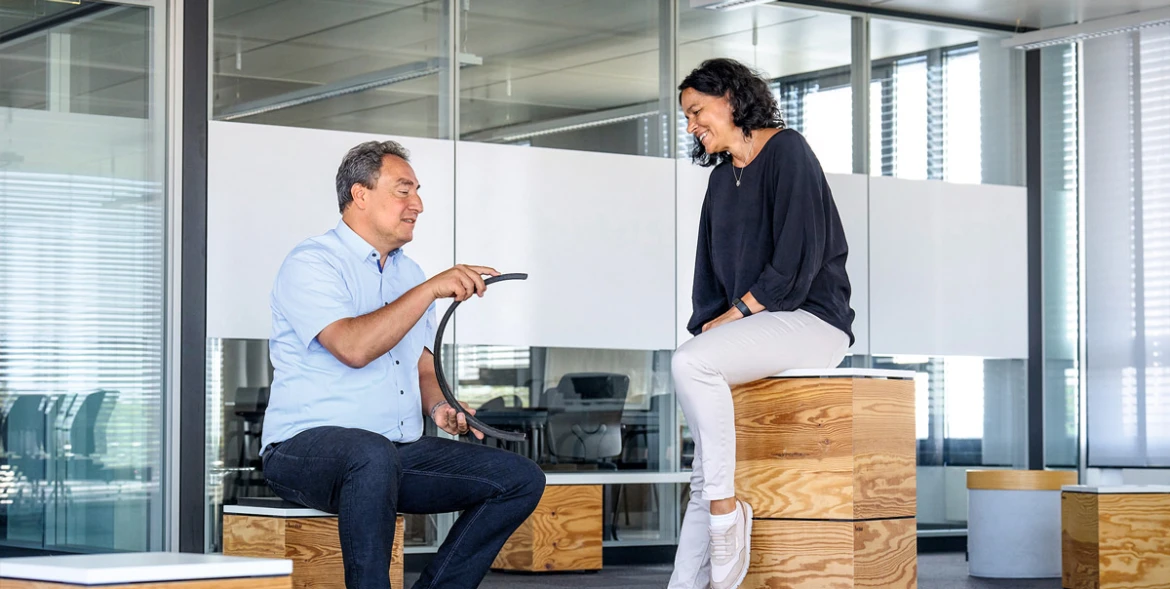
The demand for innovative materials and coatings for engine components is enormous. Existing propulsion systems with MTU technology, such as the highly efficient geared turbofan (GTF), are being refined and powered by sustainable fuels. In addition, new high-performance engines must be developed for military applications. At the same time, MTU Aero Engines is advancing the development of revolutionary propulsion concepts that will continue to drastically reduce the climate impact of aviation. This also calls for advanced materials with new functionalities. What are the challenges facing MTU’s materials experts?
Jörg Eßlinger: For over 50 years now, metallic materials such as nickel and titanium have played a key role in making engines lighter and more efficient. To make future engines even more efficient, these materials are continuously being optimized. In the second-generation GTF, the core engine’s thermal efficiency will be further improved, as will profitability in both production and operation. The materials used must be extremely heat-resistant as well as lightweight, durable and robust. It’s also important to ensure they can be manufactured and repaired cost-effectively and with process stability.
Inga Stoll: We already have our eye on the best material classes for the second-generation GTF, such as monocrystals, specific protective coatings, high-temperature-resistant disk materials and materials in additively manufactured components. And we’re improving our analytic description of these materials. All this enables us to fully exploit their lightweight construction potential, temperature limits and service life.
Jörg Eßlinger: Much the same applies to military engines: the requirements placed on the materials can be met only with special high-performance materials. When it comes to the NEFE, the Next European Fighter Engine, the bar is even higher. To ensure high power density and performance, what’s needed are lightweight construction and materials for extremely high temperatures as well as special coatings for components.
Inga Stoll: This calls for, for example, fiber-reinforced materials and powder metals. Substantial investments from us and our partners are needed to optimize, refine and qualify the properties and manufacturing of these materials for our applications. And it’s crucial to begin this lengthy development process in good time.
AEROREPORT: What other requirements must be taken into account besides use temperature, weight and stable, cost-effective manufacturing?
Inga Stoll: The materials need to be easy to repair as well in order to bring down MTU customers’ maintenance costs. Reparability is something we consider early on in the materials design process. After all, we want to make sure that our customers are able use their engines for a long time. The right material with the ideal protective coating can double or even triple a component’s service life. In fact, in the demanding environment of an aircraft engine, it’s coatings that make the material usable in the first place.
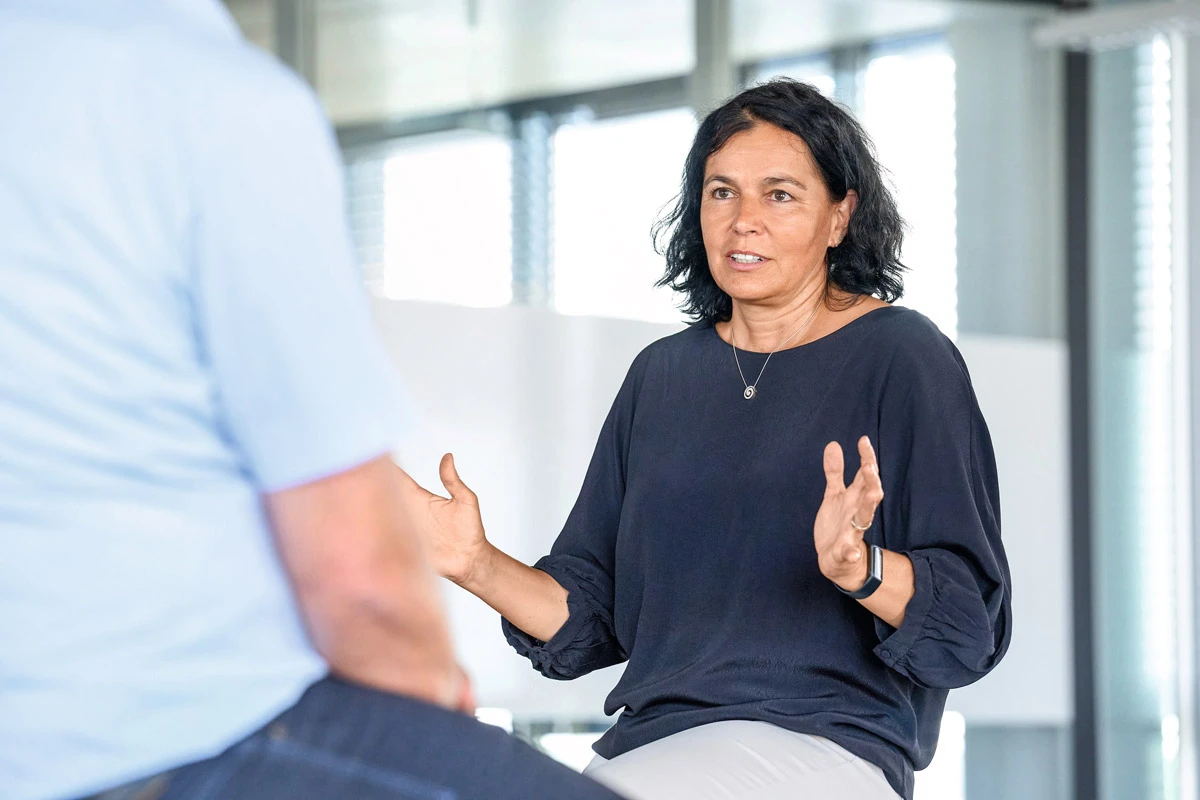
“We already have our eye on the best material classes for the second-generation GTF, such as monocrystals, specific protective coatings, high-temperature-resistant disk materials and materials in additively manufactured components. And we’re improving our analytic description of these materials.”
Director Materials at MTU
Jörg Eßlinger: Coatings will become even more important in the future. Over 60 percent of engine components are already coated to protect them against high temperatures, abrasion, chemical attacks and erosion. If the power density in engines is to keep increasing while demand for longer service life continues to grow, then engine materials are going to need even better, higher-performance coatings.
AEROREPORT: MTU is already working on revolutionary propulsion concepts for the future. What challenges does this entail for the materials?
Inga Stoll: Future requirements couldn’t be higher. Take, for example, the water-enhanced turbofan, which recuperates thermal energy and water from the exhaust gas flow before the water is vaporized by a heat exchanger and injected into the combustor. This means the materials are exposed to a humid environment. It’s important not to underestimate the fact that this significantly higher water vapor content accelerates corrosion. Corrosion of any kind impairs a component’s performance. We need to find out what special coatings are necessary to protect the materials.
Jörg Eßlinger: These demanding requirements also apply to MTU’s flying fuel cell propulsion concept. Here, the issue isn’t so much the high temperatures, but rather the fact that the concept involves electrification and the influence of hydrogen, which can be hard on the materials. We’re faced with novel components, such as the constituent parts of the fuel cell itself, as well as with new aircraft engine materials and their functions. These include magnets, cryogenic hydrogen as well as electrochemical issues. A fuel cell reacts stored hydrogen with oxygen from the air to form water, thereby releasing electric energy. Hydrogen and oxygen sound harmless enough. However, if hydrogen seeps into the material, it can cause brittleness. That’s why we’re working hard to determine how severe the impact is and how best to protect the materials against it.
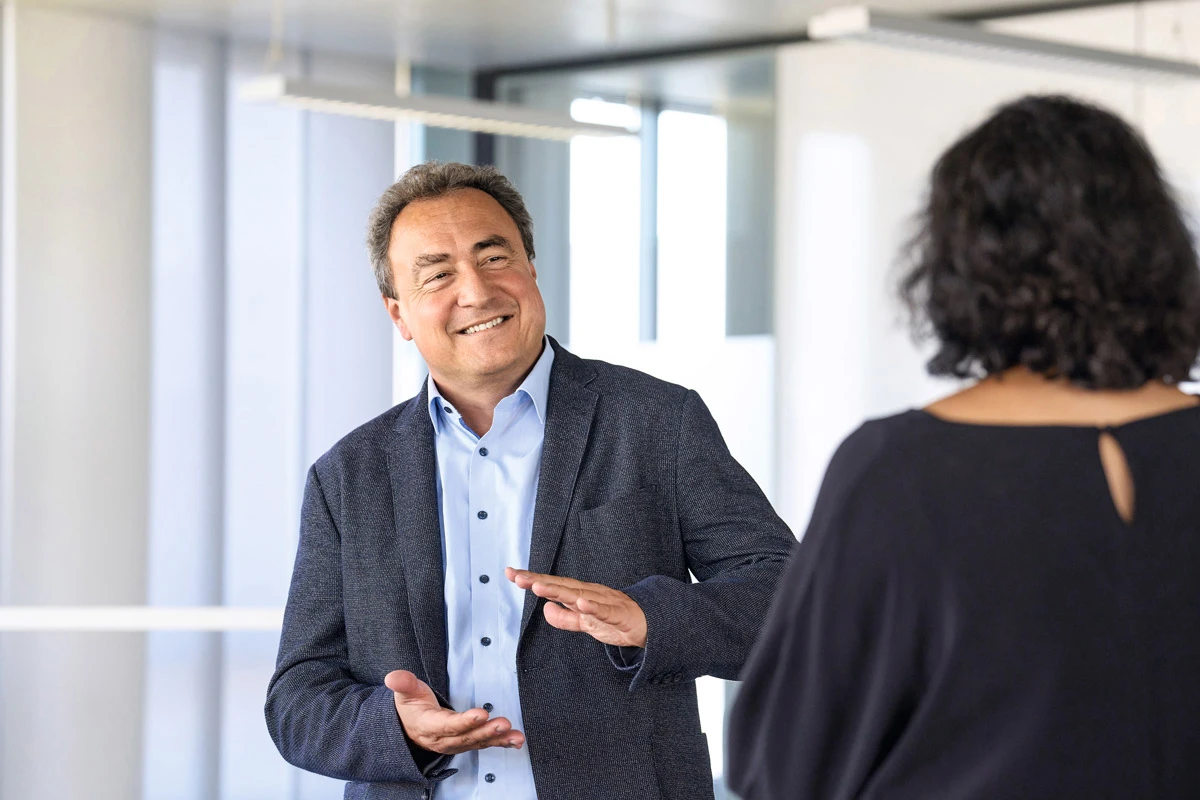
“To speed up development and to produce optimum technological and commercial results, it’s essential to employ simulation techniques. MTU’s previous experience with such techniques, in particular when it comes to developing and assessing the quality of materials and designing manufacturing processes, has been thoroughly positive.”
Senior Consultant Materials at MTU
AEROREPORT: What materials are we talking about?
Inga Stoll: I’m talking about materials such as special polymers, coatings and functional materials, either with electromagnetic properties or that function as sensors. Just like the new atmosphere within the engine, these are not exactly standard for us. Then there’s the matter of having to qualify these materials; here again, stable, cost-effective manufacturability and reparability are important. For new materials and coatings in particular, MTU must provide proof of safety—down to the smallest detail.
AEROREPORT: Aviation-specific requirements are very high, aren’t they?
Jörg Eßlinger: Indeed. The qualification of new materials and their functions for commercial flight operations is very demanding. Factors such as high mechanical loads, long durability and damage tolerance play a role. All the various plastics, composite materials, metals, magnets, catalysts, films and coatings we’ll be working with will be performing functions that in some cases are unprecedented in aircraft engines. In addition, we need to test the new materials, for instance to see how they hold up in a humid or aggressive atmosphere. MTU is building testing facilities for this purpose. With our component test center, we’re already well positioned, and our partners from research and the service industry are supporting us to the best of their ability. There’s much to do.
Inga Stoll: This makes our strong, reliable network all the more valuable. Our close ties with universities, research institutes and manufacturers are important as they enable us to share know-how, investments and risks. Above all, we rely on our development partners to actively come up with novel materials and evolve their own manufacturing processes. For instance, the use of fiber-reinforced composites has already led to collaborations with suppliers from industries outside MTU’s immediate network, such as the textile industry. What’s important for us is for development work to be related to applications. If MTU decides to use a new material in ten years’ time, then research activities must be closely aligned with the requirements of the end product.
Jörg Eßlinger: There’s no time to lose. To speed up development and to produce optimum technological and commercial results, it’s essential to employ simulation techniques. MTU’s previous experience with such techniques, in particular when it comes to developing and assessing the quality of materials and designing manufacturing processes, has been thoroughly positive. It’s key to connect several simulations at different scales and to not shy away from novel methods. But quality assessments in large-scale manufacturing will also increasingly rely on digital processes.
AEROREPORT: Which ones?
Jörg Eßlinger: One example is MTU’s deep learning software called Neuronal Analysis Tool To Evaluate Rapid, or Natter for short. It uses AI to classify microscope images of metals with unprecedented speed. This saves days’ worth of image editing on the computer. The digitalization of materials engineering calls for specialists with interdisciplinary skills in materials science and IT. We’re glad to have been able to strengthen our teams by attracting outstanding experts to join us.