innovation
Electroplating processes for engine parts
MTU has 150 baths that it uses for plating and stripping engine parts. Electroplating plays an important role in the testing and manufacturing of geometrically complex blisks.
author: Monika Weiner | 6 mins reading time published on: 05.10.2023
author:
Monika Weiner
has been working as a science journalist since 1985. A geology graduate, she is especially interested in new developments in research and technology, and in their impact on society.
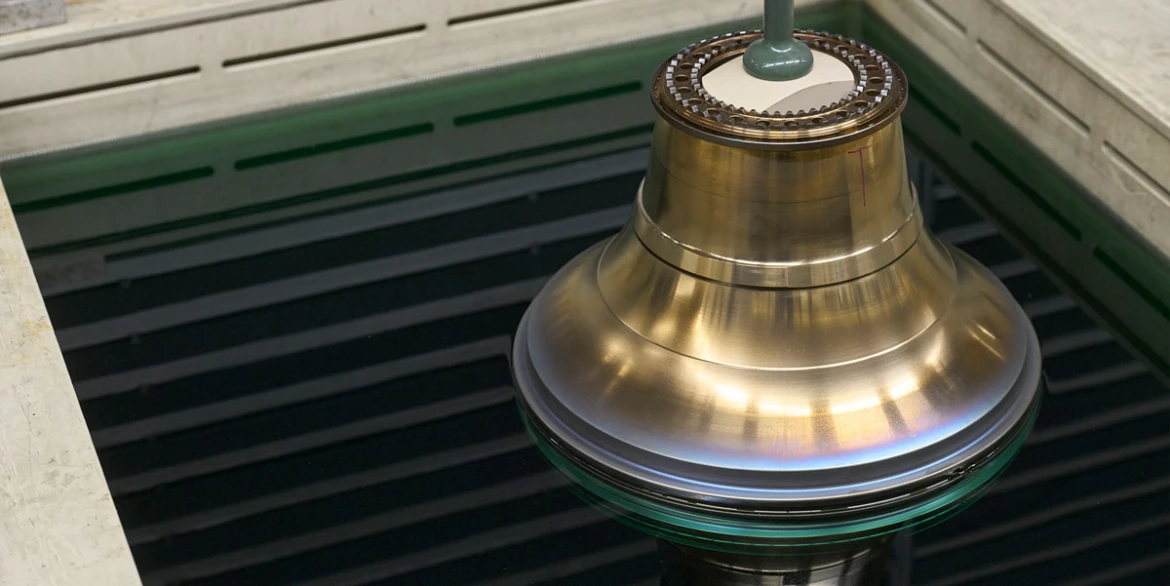
Suspended two meters above a row of huge plastic tanks filled with chemicals, a gigantic, box-like steel construction glides smoothly along the rails with nothing more than a gentle hum. With a slight judder, the transport robot comes to a halt directly above a tank of nickel sulfamate. A hatch opens in the bottom of the steel box, and a rack loaded with two blisks begins its descent. Blisks—a portmanteau of blade and disk—are high-tech components where the disk and the blades are made from a single piece of material. As well as making them lighter and more stable than traditional compressor rotors, this integral production method also makes them more aerodynamic. Due to their complex geometry, however, they are extremely complicated to manufacture.
Centimeter by centimeter, the blisks are lowered into the nickel bath. Once the rack reaches the electrode bar, it clicks into place—and the plating process can begin. An electrical current starts to flow between the anode (positive electrode) and the cathode (negative electrode), to which the blisks are connected. This causes positively charged nickel ions to migrate to the cathode, where they are deposited. “It’s this deposition process that allows us to build up a stable nickel coating on the blisks’ blade tips atom by atom,” says Michael Blümel, who is responsible for optimizing the electroplating process at MTU Aero Engines.
One-of-a-kind plating line for blisks
As the nickel atoms accumulate on the blade tips, an electric motor integrated into the rack slowly rotates the disks, keeping them constantly in motion. “Rotating the components ensures a highly uniform nickel coating. It also enables us to modify the properties of the plating by incorporating specific substances,” Blümel says. During the plating process, boron nitride particles are sprinkled onto the narrow blade tips from a container. These sharp-edged particles similar to industrial diamond find their way directly into the layer of nickel, which partially encloses them and locks them in place to form the perfect hardfacing coating.
"This plating line is the only one in the world that can handle complex blisk geometries with micrometer precision."
Head of electroplating at MTU
“This plating line is the only one in the world that can handle complex blisk geometries with micrometer precision,” says Ali Cimen, who heads up electroplating at MTU. “Hardfacing the blade tips is incredibly important because it ensures that the blisks can bed into the hard lining of the casing that surrounds them in the engine without being damaged. Using this kind of plating enables the design engineers to minimize the gap between the blisk and the casing, which significantly improves engine efficiency.”
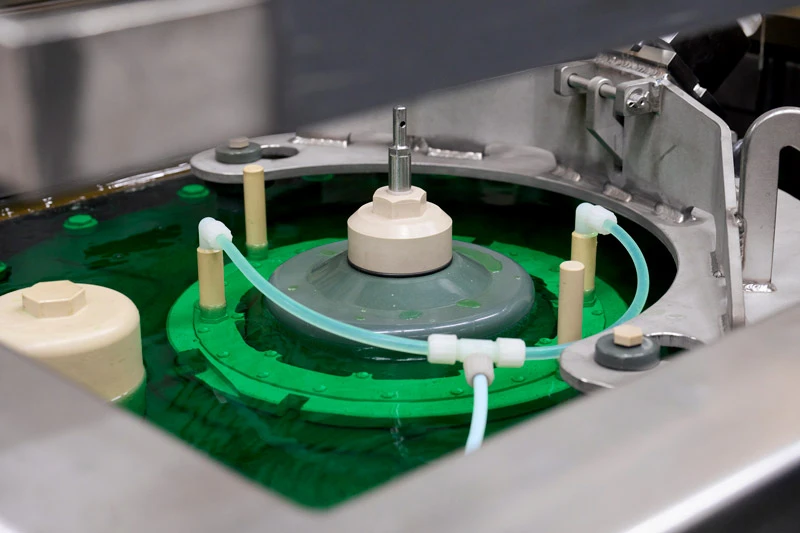
Electroless nickel plating: In this nickel bath, components are plated without the need for an external electrical current. This method is used to apply a very thin and even plating to components that do not require any mechanical post-processing. The image shows a TP400-D6 blisk immersed in the shimmering green liquid.
Technology dating back centuries
The principle behind electrochemical deposition was discovered in the 18th century by Luigi Galvani while conducting experiments on a frog. He noticed that the legs of the frog twitched when he touched them with two electrodes made of different metals connected together. However, it wasn’t until the early 19th century that electroplating was first put into technical use to plate metals with gold and silver.
“It’s that amazing versatility that makes electroplating so fascinating. In engine construction, for example, we can use it to etch away surfaces to reveal their microstructure, and it’s also a useful technique for applying anti-corrosion and anti-friction coatings as well as hardfacing.”
Head of electroplating at MTU
Nowadays, electroplating is widely used to give substrates the precise properties they need for specific applications. For example, chrome plating is used to increase surface hardness, platinum plating to promote corrosion resistance, and nickel or dispersion plating to improve wear resistance. Whatever the type of electroplating process, the metal to be deposited is connected to the anode (positive electrode) and the component to be plated is connected to the cathode (negative electrode). The greater the current and the longer the plating time, the more ions migrate to the cathode and the thicker the coating becomes. Connect a component to the anode, however, and the whole process runs in reverse: the metal atoms on the component’s surface dissolve, disassociate into metal ions, and migrate through the solution, moving away from the substrate and toward the cathode. This reverse process is also used in electroplating shops, for example to reveal defects on a component’s surface.
That means plating baths can be used not only to apply coatings, but also to strip them away. “It’s that amazing versatility that makes electroplating so fascinating,” Cimen says. “In engine construction, for example, we can use it to etch away surfaces to reveal their microstructure, and it’s also a useful technique for applying anti-corrosion and anti-friction coatings as well as hardfacing.”
Electroplating for quality assurance
The principles of electrochemical deposition play an important role in blisk manufacturing. As soon as the blanks have passed through the initial steps in the production process, they are immersed in an acidic solution that removes a micrometer-thick layer of metal. This process, which is known as pickling, activates the surface of the metal. The components are then immersed in an alkaline bath. This causes a blue oxide layer to form on the component’s surface, making it easier to see the grain boundaries in the metal. MTU experts use this method to spot distinctive patterns in surface microstructure that might indicate weak points in the metal. Such material defects are dangerous, because they could lead to cracks forming during flight; in the worst-case scenario, they could even cause the entire disk to shatter. That’s why any defective blisks are removed at the visual inspection stage.
Only blisks that have successfully passed each and every stage of the quality assurance process—which focuses heavily on crack testing as well as microstructure testing—are returned to the plating bath for the final step of blade-tip hardfacing. To ensure the nickel-diamond coating is deposited only on the outermost tips of the blades, all the other parts of the component must be masked: “That’s no easy task when you’re dealing with such complex geometries,” Blümel says. To start with, a protective layer of paint is applied to the blades and then scraped off the areas to be plated. Experts use a scalpel and magnifying glass to expose the surface of the blade tips, a task that requires a steady hand. Finally, the disk bodies are encased in protective covers and each of the specially developed rotating racks is loaded with two blisks.
Michael Blümel, electroplating process improver.
The remainder of the process is fully automatic: the transport robot picks up one rack at a time, moves along the rails to the first of the plating baths, and lowers its cargo into the solution. It takes only a few minutes for the acids to etch away a micrometer-thick layer from the tips of the blades. The rack is then immersed in another acid bath where the surface of the components is activated. Finally, the blade-tip hardfacing is applied. All in all, this process takes a few hours. Once it is completed, the transport robot picks up the rack and immerses it in a tank filled with a special solvent that removes the paint from the blades. This is followed by a final visual inspection; the blisks are then ready for final testing and acceptance.
Electroplating applications for used engine components
Plating baths are used not only to apply the final coating to new blisks, but also for repairing engine components. Over time, frequent contact with sand and dust in the air can alter the components’ shape and technical properties. However, new plating can only be applied to a component once any old coatings have been stripped off. MTU has a special installation where it removes coatings using a high-pressure water-jet system. The rotating jet of water is sprayed at the component’s surface at pressures of up to 3,500 bar. Alternatively, coatings can also be removed from used parts using chemical solutions. The surfaces must then be thoroughly cleaned, degreased and activated before the electroplating process can start anew.
The science and applications of electroplating
MTU’s electroplating shop has some 150 different baths containing acids, alkalis and organic solutions. As well as plating new parts, the baths are used to repair used parts whose geometry has been affected by engine vibrations, rotation and wear.
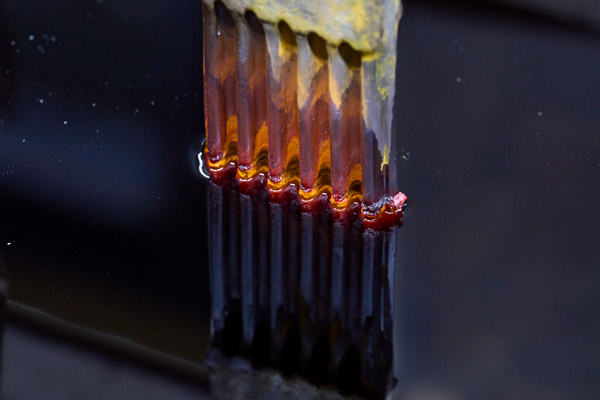
In this image, a lead anode is suspended in a bath of chromic acid, ensuring a consistent flow of electrical current.
Chrome plating
For chrome plating, components are immersed in a tank containing 4,000 liters of chromic acid. This is the largest plating bath at MTU. Because chromium forms very hard coatings that are also highly temperature-resistant, it is used to restore engine parts to their original state following exposure to high temperatures and significant mechanical stress, for example in engine bearings.
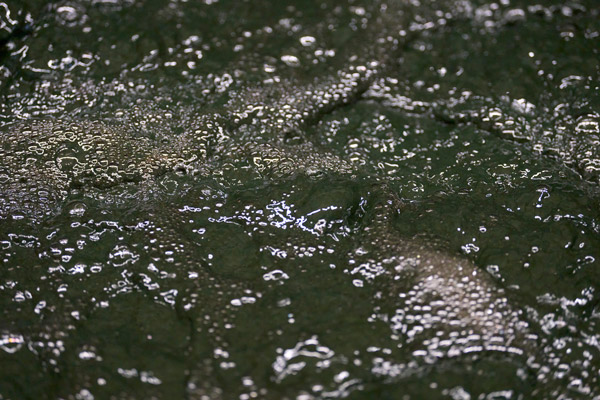
The cobalt bath contains solids that are incorporated into the dispersion coating to make it more wear resistant. This gives the cobalt a greenish hue instead of its normal reddish tint.
Cobalt plating
Cobalt plating involves immersing components in a cobalt sulfate bath. Powdered solids can also be sprinkled onto the component during cobalt plating. By incorporating powders into the coating, it is possible to obtain the precise sliding and grinding properties required for each application. Cobalt plating is used to repair combustor casings, for example.
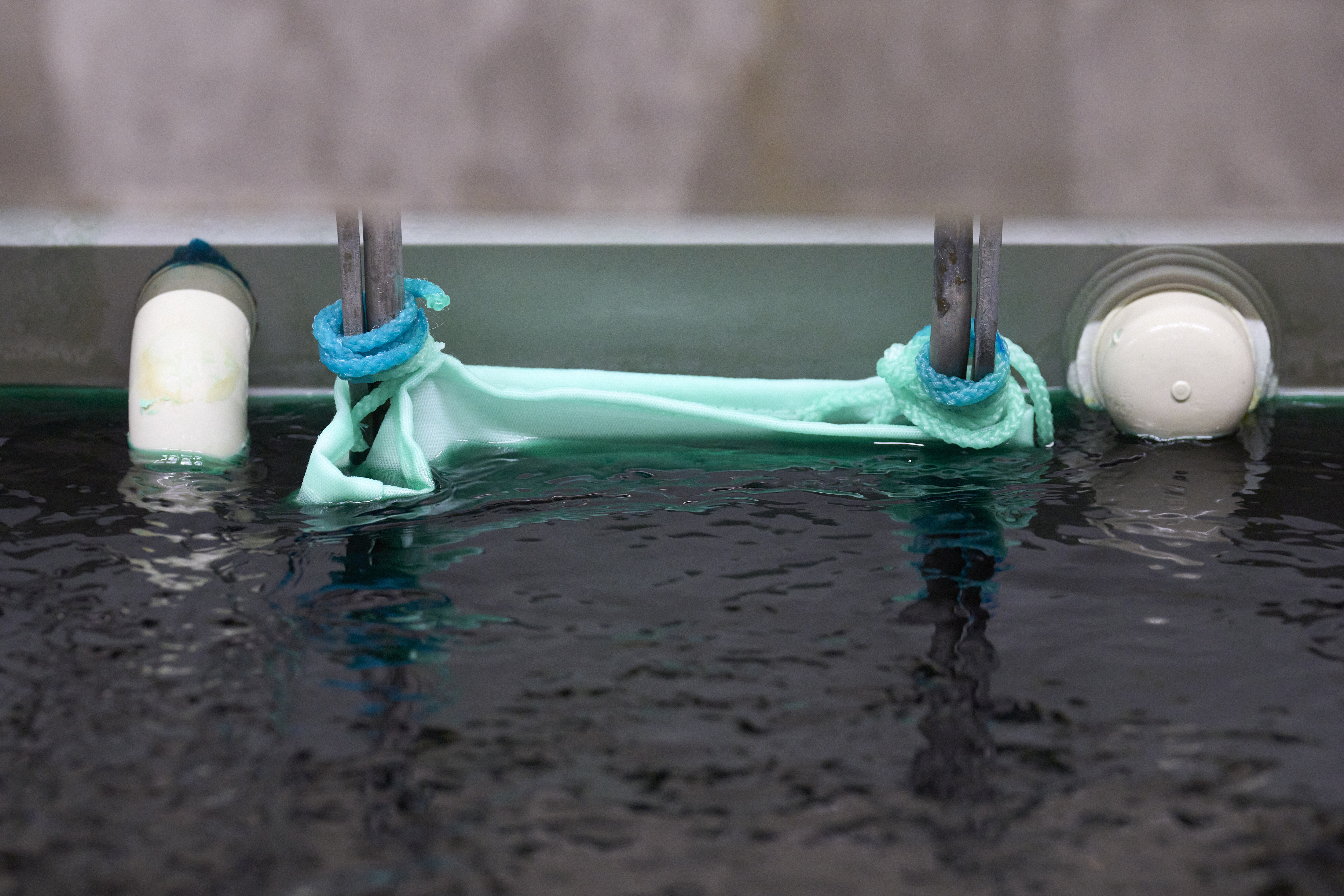
The anode in this nickel sulfamate bath consists of small pieces of nickel; these allow the current to flow and gradually dissolve into the solution.
Nickel plating
Nickel plating uses baths of nickel chloride and nickel sulfamate. This form of plating is used for components that suffer rapid wear and require the deposition of several millimeters of metal to regain their original dimensions. It is also possible to modify the component’s sliding and grinding properties by incorporating diamond powder. The hardfacing obtained by depositing a nickel-diamond coating gives the blisk tips the best chance of properly bedding into the casing.
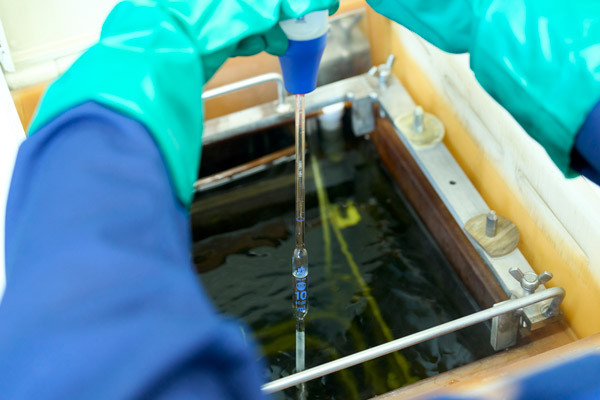
The yellowish hue of the solution indicates the presence of the precious metal platinum. Samples of solution must be taken every two hours to check the platinum content. The heat of the bath skews these measurements, so samples are collected with a pipette and then cooled before their platinum content is analyzed in the lab.
Platinum plating
Platinum plating uses baths of platinum solutions. Deposited in ultra-thin layers just a few micrometers thick, these coatings provide extremely robust protection against high-temperature oxidation. Platinum plating is applied to the blades during the production of new high-pressure turbines, for example.