good-to-know
Thermal coating techniques
Temperature resistance, corrosion resistance, hardness, stability, compressive strength, durability—every single engine component must fulfill specific requirements. Coatings help make sure they do just that. The range of techniques available is massive. Here’s a selection.
author: Monika Weiner | 6 mins reading time published on: 06.11.2023
author:
Monika Weiner
has been working as a science journalist since 1985. A geology graduate, she is especially interested in new developments in research and technology, and in their impact on society.
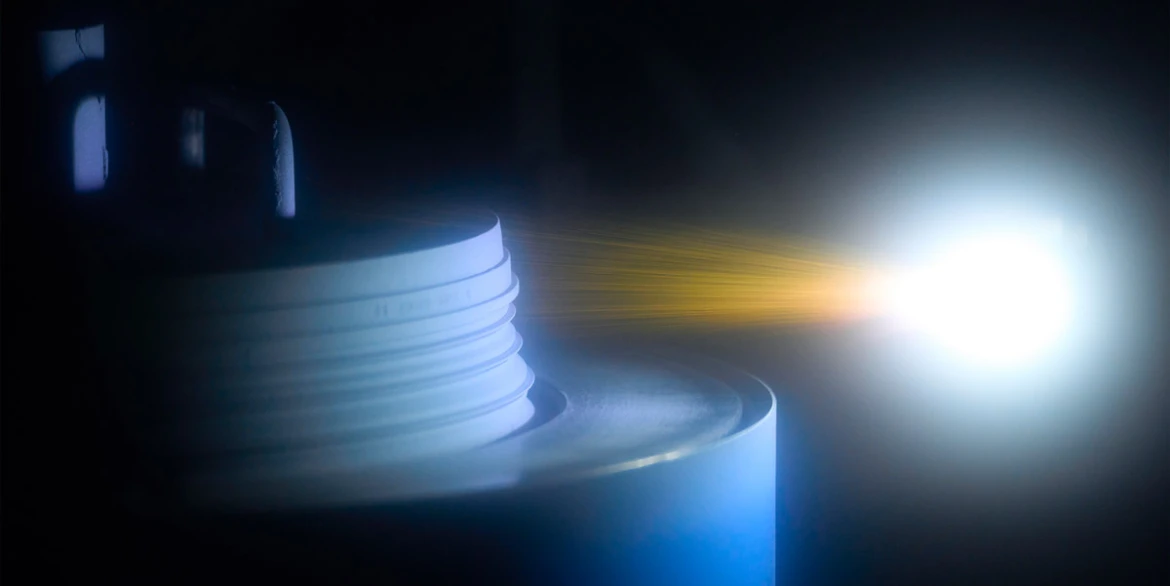
Engine components have to meet extraordinarily demanding requirements. A range of thermal coating techniques are available for enhancing the surfaces of these components, specifically to make them last longer and improve engine efficiency. Thermal coating techniques can generally be sorted into three types:
- Thermal spraying: coatings made of molten particles
- Physical vapor deposition (PVD): coatings made of a material in its vapor phase (atomized or ionized coating material)
- Chemical vapor deposition (CVD): coatings made of a material in a chemically reactive vapor phase
AEROREPORT presents a selection of coating properties and application examples:
1. Thermal spraying:
In thermal spraying, the substances that will coat the workpiece are generally melted first. The energy required for this is supplied by an electric arc, flame, or gases in their plasma state. The powder or wire materials (pure metals, alloys, ceramics, or organic polymers) are sprayed onto the surface of the workpiece as a fine jet of molten particles.
Plasma spraying
In plasma spraying, ionized gases play a key role. These are created using an electric arc—in other words, when high voltages between two electrodes discharge, thereby ionizing the gas located between them. The properties of the plasma depend mainly on the type and combination of the gases fed between the electrodes. Most of these combinations are of noble gases, such as argon or helium, mixed with hydrogen, or combinations of nitrogen and hydrogen. The higher the concentration of hydrogen, however, the higher the temperature will rise. Powdered, metallic, or ceramic materials are injected through a nozzle, generally radially, into the plasma flame and heated to several thousand degrees. Once melted, they are directed onto the workpiece to be coated.
In engine construction, plasma spraying tends to use materials that have a high melting point such as hard metals or ceramics. Coatings made of these extremely hardwearing materials are required in many different places in an engine.
High-velocity oxygen fuel spraying
In high-velocity oxygen fuel (HVOF) spraying, the spray powder is delivered at high pressure from a combustor into a flame measuring roughly 60 centimeters in length. The flame is created by burning kerosene or hydrogen mixed with pure oxygen. The high velocity of the gas propels the spray particles toward the recipient component surface at a supersonic speed. Since the particles are moving at high speed, they spend such a short time in the flame that the ambient atmosphere can oxidize them only very slightly. HVOF spraying also drastically reduces the incidence of transformation and decomposition reactions. This results in thick, superbly adherent coatings with a relatively smooth surface, which for some applications can remove the need for mechanical reworking.
HVOF spraying can create thick coatings with excellent bonding properties. This is the technique of choice for hard, wear-protection coatings on shaft bearing seats (tungsten carbide), on turbine stators (Stellite), and for oxidation protection on turbine blades (MCrAlY).
Powder flame spraying
Powder flame spraying uses a flame spray gun, which emits an oxy-acetylene flame similar to that used in autogenous welding. This flame reaches temperatures of up to 3,000 degrees Celsius. As the gas velocity is relatively low, this technique is ideal for producing porous metallic layers or porous coatings of aluminum oxide. It is unsuitable for carbidic materials and ceramics with high melting points such as zirconium oxide.
Powder flame spraying is suitable for producing porous coatings, including the sacrificial coatings (abradables) on housings, which prevent damage to rotor blades caused by abrasion during operation.
Wire arc spraying
In wire arc spraying, the energy is supplied by an electric arc, which is created by the discharge of high voltages between electrodes. In this case, the two electrodes are wires made of the coating material. The electric arc melts the end of the wires to form a stream of molten particles, which is directed at the surface to be coated by a jet of diffusing gas, typically compressed air. The wires are continuously fed through so that the position of the electric arc burn remains the same.
Coatings made in this way can be applied in thicknesses of several millimeters, offer good adhesion, and can be easily reworked mechanically. As such, wire arc spraying is commonly used during maintenance work to restore the original geometry of worn components.
Cold spray coatings
To produce a cold spray coating, the powder for the coating is heated rather than melted. Relatively moderate temperatures of up to 1,000 degrees Celsius are sufficient. These are generated electrically in a preheater and also in a spray gun that emits nitrogen expanding at a pressure of around 50 bar. Along with the gas, the gun also shoots the heated powder toward the recipient component at high velocity. Upon impact, the particles release their kinetic energy as deformation heat and fuse together. This technique can produce extremely hard, non-porous coatings several centimeters thick.
A typical application for this technique is to restore engine components that have become worn. By selecting a suitable powder and setting the right parameters, it is possible to produce coatings that are virtually as strong as the original material.
2. Physical vapor deposition (PVD)
In physical vapor deposition, or PVD for short, the coating material is vaporized. The following techniques fall under PVD:
Arc technology
In this case, the energy required for the vaporization process is supplied by an electric arc. This is created by the discharge of high voltages between two electrodes. By connecting the anode to a metal plate, the arc vaporizes the atoms on the plate’s surface. This metallic vapor condenses on the recipient workpiece, where it forms thin crystalline layers. PVD systems work in airless environments because air would disrupt the process. Coating takes place either in a vacuum or in an atmosphere of inert gas. Reactions with the inert gas can also be by design: for instance, vaporized metal ions bond with nitrogen to produce metal nitride, which condenses on the components to form a tough ceramic coating.
Sputter technology
For the sputter technique, the coating material is vaporized through ion bombardment. The ions come from a type of plasma produced above the surface of this material. Collision processes triggered by the ion bombardment drive atoms out of the surface, generating an atomic spray, or sputter, of the given coating material. The displaced atoms then condense on the workpiece, forming a thin coating. As with arc technology, this process takes place in a vacuum, with small amounts of gas (e.g. argon) fed in solely for the purpose of producing the plasma. But in contrast to arc-based techniques, sputter technology is characterized by lower coating velocities, which has the advantage of creating smoother coatings.
Electron-beam physical vapor deposition (EBPVD)
For EBPVD, the coating material—a zirconium oxide ceramic with a high melting point—is vaporized in a vacuum at up to 3,000 degrees Celsius using an electron beam. The subsequent condensation on the components produces a coating that is up to 300 micrometers thick. Since the thermal conductivity of zirconium oxide is comparatively low, it is used as a thermal barrier coating on high-pressure turbine airfoils, which get particularly hot during operation. What’s special about EBPVD coatings is their columnar structure, which makes them particularly resilient to changes in temperature. This coating technique is carried out in the Ceramic Coating Center in France. The Center is a joint venture for high-tech coatings between MTU Aero Engines and France’s Safran Aero Engines.
3. Chemical vapor deposition (CVD)
In CVD, the coating material—a gaseous metal halide with aluminum or chromium as the metal—is directed at the surface of the component (usually a turbine blade) in a retort heated to up to 1,100 degrees Celsius. A portion of the coating gas decomposes into its original materials, with the metal atoms diffusing into the substrate. This process permits precise control not just of the coating duration and temperature but also its thickness and composition. Enriching surfaces with aluminum or chromium greatly increases the component’s oxidation or corrosion resistance and thus its service life.