innovation
Better maintenance planning with Engine Trend Monitoring
Engine Trend Monitoring provides important information about engine condition. Early diagnosis prevents costly consequential damage and paves the way for predictive maintenance planning.
author: Nicole Geffert | 6 mins reading time published on: 26.10.2018
author:
Nicole Geffert
has been working as a freelance journalist covering topics such as research and science, money and taxes, and education and careers since 1999.
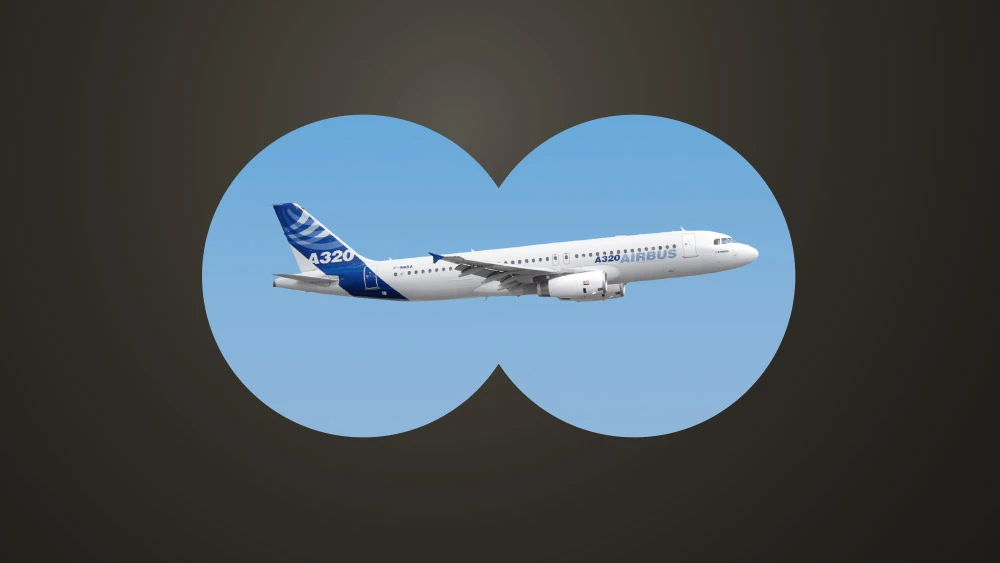
Running a practiced eye over the data, Ivaylo Krastev, engine engineer at MTU Maintenance Hannover, sees that an engine is experiencing a drop in efficiency while cruising. The outlet temperature has risen, the high-pressure spool is speeding up and the engine is consuming more fuel. A warning is immediately sent to the airline, which has its entire fleet of engines looked after by MTU Maintenance. At the aircraft’s next stop, the engine is examined while still on the wing by two of the airline’s maintenance mechanics using a borescope.
They discover that a foreign body has found its way into the compressor. The engine is immediately removed from the wing and sent to the MTU Maintenance shop for repair. There, the fears are confirmed: the foreign body has damaged several blades. Had this comparatively minor damage gone unnoticed, it could have caused major consequential damage to the engine and led to costly repairs— the airline is now spared both of these.
Engine Trend Monitoring
Early warning system for engines Data recorded previously by the aircraft computer is evaluated by the ETM system while the aircraft is still in flight. The system never sleeps, so when MTU specialists see an alert, they can take action immediately and send the engine to the MTU Maintenance shop. ETM also makes it possible to generate forecasts, thus improving the planning of engine overhauls.
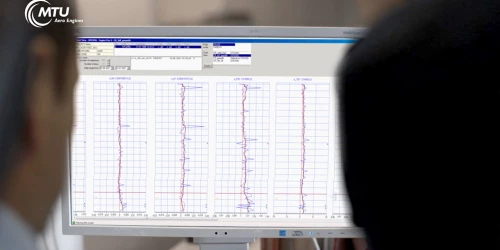
Engine Trend Monitoring
The engine early warning system monitors all key parameters during a flight. It detects even the slightest issues, which can then be fixed before they develop into anything more serious. To the video
This early detection and analysis of abnormalities is thanks to MTU Maintenance’s Engine Trend Monitoring (ETM): a comprehensive software solution developed by MTU in house for monitoring engine parameters. “During flight, the aircraft computer records the key engine parameters including speed, pressure, temperature and vibration,” says Norman Schwarz from Performance Engineering at MTU Maintenance Hannover. The ETM system evaluates these parameters at certain points during a flight cycle—typically during takeoff and cruising—by comparing the data with expected values for a corresponding engine model. “This means that we can detect abnormal changes, such as in the engine’s thermodynamic behavior, and identify even the tiniest of deviations,” Schwarz says.
Thanks to the early detection system, MTU experts can analyze the data and look into potential abnormalities long before a serious problem surfaces. If they notice a deviation, they recommend a clear course of action for the necessary maintenance.
Fleet under control
ETM is a key component of the fleet management service that MTU Maintenance offers its customers. The concept ensures that all the fleet’s engines have maximum availability and efficiency and can be operated as cost-effectively as possible. Performance Engineer Schwarz explains: “ETM also offers a forecast function that can predict the number of remaining cycles. This helps improve the planning of more comprehensive engine overhauls and to optimize shop visit intervals from both a technical and an economic perspective.
Two more benefits for fleet customers is that all engine types can be monitored with a single tool and that MTU Maintenance is in a position to tailor its expertise to individual customer requirements, and new alert rules can be introduced that focus on certain parameters.
24/7 engine monitoring
ETM and its fully automatic alert function for deviations are active around the clock, seven days a week. Schwarz says, “For many of the new kinds of engine and aircraft, data analysis can already begin during the flight. Trend analyses can be called up online 24 hours a day, virtually in real time. Specialists at MTU’s Hannover, Zhuhai or Vancouver locations can then evaluate them.
Developed in house by MTU experts, the flexible system has been in use since 2006 and is continuously being expanded and optimized. And in the future, customers will benefit from further innovations.
Mobile and straightforward
“We’re currently preparing to change platforms and use new software so that we can track the data not only on PCs, but in the future also on tablets and with a smartphone app,” says Christian Preuss, who is responsible for test systems and ground support equipment at MTU Aero Engines. IT specialists in Munich and Rzeszów are handling the programming. The new interface will be more cutting edge, more streamlined and more straightforward—genuine added value for customers.And there’s a further optimization in the pipeline. “With the current system, we can ascertain the loss in efficiency of the engine as a whole, but we’re developing the ETM so that it will show which engine modules are contributing to the loss in efficiency,” says Jürgen Mathes from MRO Performance Support at MTU Aero Engines. “Analysis at the modular level offers the benefit of allowing maintenance to be planned in a more targeted way. This is because it lets our maintenance specialists know which components to concentrate on during the shop visit.”
“Analysis at the modular level offers the benefit of allowing maintenance to be planned in a more targeted way. This is because it lets our maintenance specialists know which components to concentrate on during the shop visit.”
One dataset every second
In the future, engine data is to be recorded, transmitted and stored throughout the flight—in essence, one dataset every second. “This means that trend deviations can be detected even earlier compared to the current system, which can do just two to three snapshots per flight,” Mathes says. As such, maintenance experts will be able to react even faster to trend deviations. It’s all about predictive maintenance, or in other words efficiency through advance knowledge.
“New avionics can continuously record and transmit data. The necessary hardware is already installed on newer aircraft types,” Mathes says. And it can be retrofitted to older models. However, the future ETM system does pose certain challenges for the IT experts. The sheer volume of data that is continuously being received must not only be stored, but analyzed and evaluated as well. Alongside sufficient storage space, the efficient analysis method is the key to success for targeted and predictive maintenance. As Preuss puts it: “We’re testing various data analysis concepts, such as machine learning, so that we can then offer our customers an ideal early detection system.”