innovation
Effizient und gut vernetzt: Fahrerlose Transportsysteme bei der MTU
Die autonomen Helfer spielen eine wichtige Rolle für die fortschreitende Automatisierung des Materialstroms in der komplexen Logistik und Triebwerksfertigung.
Autorin: Nicole Geffert | 5 Min. Lesezeit veröffentlicht am: 16.01.2025
Autorin:
Nicole Geffert
arbeitet seit 1999 als freie Journalistin mit den Themen Forschung und Wissenschaft, Geld und Steuern, Ausbildung und Beruf.
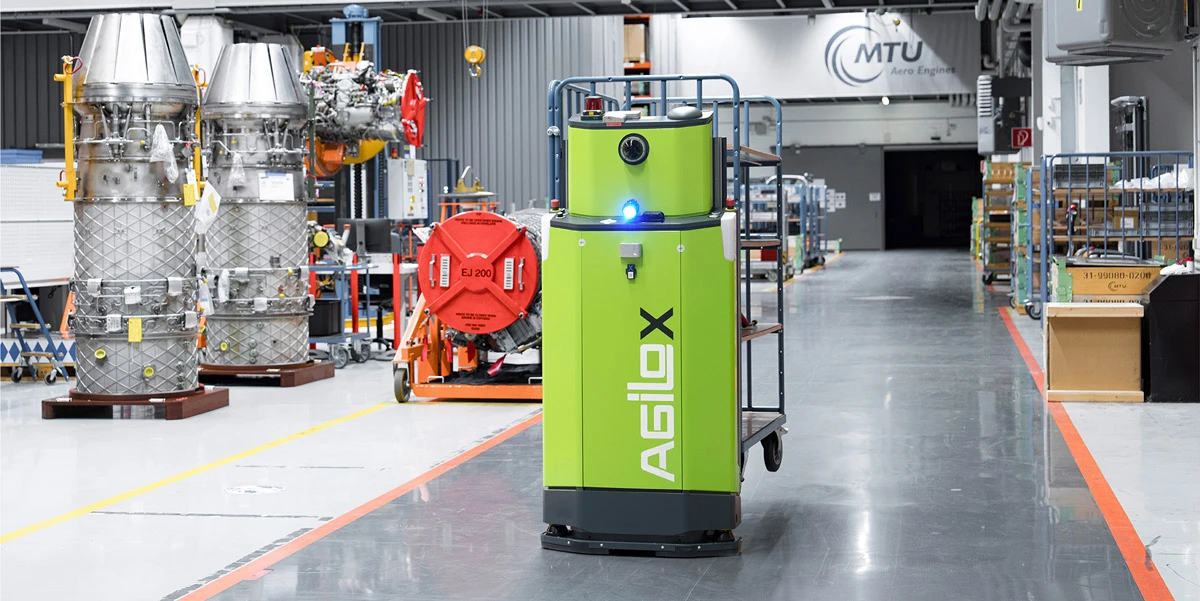
In den weitläufigen Fertigungs- und Logistikhallen der MTU Aero Engines läuft die Produktion auf Hochtouren. Zwischen Triebwerksspezialist:innen und imposanten Fertigungsanlagen bewegen sich drei autonome Helfer, die unauffällig, aber zielstrebig durch die Hallen in München und Erding gleiten. „Lena“, „Denki“ und „Yoda“– so heißen die fahrerlosen Transportfahrzeuge, die hochwertige Triebwerksbauteile von einer Station zur anderen befördern.
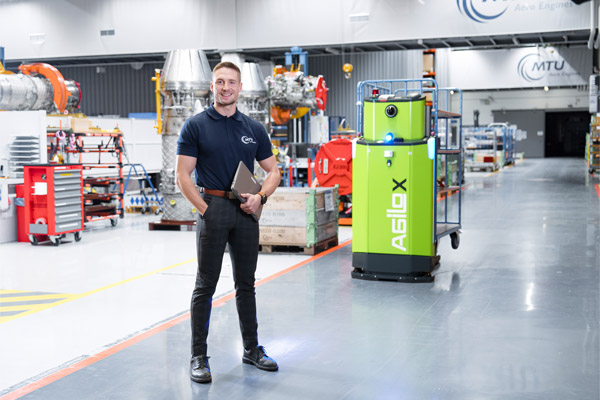
„In der fortschreitenden Automatisierung des Materialstroms haben Fahrerlosetransportsysteme (FTS) eine wichtige Funktion, um Materialfluss und Effizienz zu optimieren. Die MTU ist auf dem Gebiet der FTS-Innovation in der Luftfahrtindustrie ein Vorreiter.“
Logistik-Manager und FTS-Experte bei der MTU
Jedes von ihnen folgt einer präzisen Route und ist so programmiert, dass es die hohen Anforderungen in der Produktion und Instandhaltung von Triebwerken zuverlässig erfüllt. „In der fortschreitenden Automatisierung des Materialstroms haben Fahrerlosetransportsysteme (FTS) eine wichtige Funktion, um Materialfluss und Effizienz zu optimieren“, sagt Philipp Schmuttermayr, Logistik-Manager und FTS-Experte bei der MTU. „Die MTU ist auf dem Gebiet der FTS-Innovation in der Luftfahrtindustrie ein Vorreiter.“
Denn während FTS in der Automobilindustrie längst Standard sind, ist dies in der Luftfahrtindustrie noch eine Ausnahme. „Die Arbeitsumgebung mit zulassungskritischen Bauteilen ist eine andere als die in der Serienfertigung eines Autoherstellers mit durchgehend standardisierten Prozessen. Diese erleichtern die Integration von FTS in bestehende Produktions- und Logistiksysteme“, erläutert Benjamin Hofmann, FTS-Projektleiter in der MTU-Produktion. „Die Fertigung bei der MTU dagegen gleicht mehr einer Manufaktur. Dort gibt es viele hochspezialisierte Prozesse. Für den Einsatz von FTS ist das eine Herausforderung.“
Zudem sind die sicherheitskritischen Triebwerksbauteile sehr teuer. „Eine Transportladung, die durch die Hallen bewegt wird, kann schnell bis zu einer Million Euro an Warenwert kosten“, sagt der Logistik-Manager. Sollte eine Triebwerksscheibe vom Wagen fallen, wäre sie sofort unbrauchbar und müsste im schlimmsten Fall vernichtet werden.
Das alles galt es zu berücksichtigen, als Schmuttermayr und sein Team 2020 das erste FTS-Projekt in der Intralogistik bei der MTU in München starteten. Die Intralogistik umfasst sämtliche logistischen Material- und Warenflüsse innerhalb des Werksgeländes. Ziel war es, die innerbetrieblichen Transporte so zu optimieren, dass Materialfluss und Produktion noch effizienter werden. Das Projekt begann mit umfangreichen Tests von fahrerlosen Transportsystemen verschiedener Hersteller. Schließlich erhielt das FTS des österreichischen Start-ups Agilox den Zuschlag.
In einer digital gesteuerten Fertigung sind fahrerlose Transportsysteme (FTS) unverzichtbar. Die MTU setzt sie in ihrer hoch-spezialisierten Triebwerksproduktion ein und ist damit in der Luftfahrtindustrie ein Vorreiter.
„Lena“ optimiert die Transportroute
2021 wurde das FTS mit dem Fahrzeug „Lena“ am MTU-Betriebsstandort in Erding, östlich von München, erfolgreich getestet und eingeführt. Auf dem Gelände des dortigen Fliegerhorsts werden unter anderem das EJ200 für den Bundeswehr-Kampfjet Eurofighter Typhoon, das RB199 für den Tornado, das T408 für den Transporthubschrauber Sikorsky CH-53K sowie das MTR390 für den Hubschrauber „Tiger“ montiert und instandgesetzt. Die zwei Produktionshallen für Instandhaltung und Logistik erstrecken sich über mehr als 10.000 Quadratmeter.
Lucas Leifheit arbeitet als Teamkoordinator in Erding und war an der Einführung und Erprobung des FTS beteiligt. „Früher fuhr ein Logistik-Mitarbeiter mit dem Routenzug – einem Gabelstapler mit Waggons – vier- bis fünfmal am Tag auf einer festgelegten Strecke durch die Halle und hielt an den einzelnen ‚Bahnhöfen‘, um Bauteile ab- oder aufzuladen“, berichtet er. „Mit ‚Lena‘ sind wir schneller, denn das fahrerlose Transportfahrzeug liefert ‚on demand‘.“
Das bedeutet, dass „Lena“ direkt die Bereiche ansteuert, die ein Bauteil benötigen oder verschicken wollen, was Zeit und Kosten spart. Die Mitarbeiter:innen fordern das fahrerlose Transportfahrzeug per Mausklick an. „Lena“ optimiert die Transportroute selbständig und arbeitet die Aufträge in der effektivsten Reihenfolge ab.
Logistikfachkräfte als FTS-Supervisor
„Die Vorteile wurden schnell erkannt“, sagt Schmuttermayr. „Das FTS ist rund um die Uhr im Einsatz. Wartezeiten verringern sich, die Arbeitsabläufe werden effizienter.“ Die fahrerlosen Transportfahrzeuge sind außerdem in der Lage, miteinander zu kommunizieren. Wenn beispielsweise eine Route nicht passierbar ist, kann ein fahrerloses Transportfahrzeug diese Information an die anderen fahrerlosen Transportfahrzeuge weitergeben. „Lena“ generiert auch Ausweichrouten, um ans Ziel zu kommen.
„Mit dem System schaffen wir eine Entlastung für die Mitarbeiterinnen und Mitarbeiter – das ist uns wichtig“, sagt Leifheit. „Deshalb haben wir sie von Beginn an in das Projekt integriert und es zusammen getestet und aufgebaut.“ Die Logistikfachkräfte, die zuvor den Routenzug gefahren sind, können sich jetzt auf neue fachliche Aufgaben konzentrieren.
Sie wurden weiter qualifiziert und übernehmen jetzt die Aufgabe als FTS-Supervisor. So stellen sie beispielsweise sicher, dass die FTS stets einsatzbereit sind. „Im Vergleich zum sperrigen Routenzug beanspruchen die fahrerlosen Transportfahrzeuge weniger Platz und erhöhen die Arbeitssicherheit“, sagt Leifheit. Indem „Lena“ die komplette Umgebung mit Sensoren abscannt, ist sichergestellt, dass es zu keinen Kollisionen mit Gegenständen oder Personen kommt.
WLAN-Infrastruktur in der Fertigung
FTS wie „Lena“ in Erding oder „Denki“ und „Yoda“ in München in die hochspezialisierte Triebwerksproduktion zu implementieren, ist eine Herausforderung – auch für die IT-Spezialist:innen der MTU. „Um ein FTS betreiben zu können, mussten wir eine erweiterte WLAN-Infrastruktur in der gesamten Halle aufbauen“, berichtet Michael Leicht, Planer für Industrial IT bei der MTU. „Die WLAN-Strukturen in Logistik- und Fertigungsbereichen sind komplexer, die Implementierung ist anspruchsvoller als die in einer reinen Büroumgebung.“ Vor allem, wenn es zusätzlich um die Integration in einen militärischen Luftfahrtbetrieb wie in Erding geht, für den spezielle Sicherheitsanforderungen gelten. Hier waren individuelle MTU-spezifische Lösungen erforderlich.
Ziel ist es, die fahrerlosen Transportsysteme vollständig in die IT-Systeme der MTU zu integrieren. Am Ende steht das Ziel, eine komplett vernetzte Warenbewegung abzubilden und zu einem digitalen Gesamtsystem zu verknüpfen – ganz im Sinne von Industrie 4.0. „Die FTS sind ein wichtiges Bindeglied auf dem Weg zu einer digital gesteuerten Fertigung, da sie die Vernetzung und Effizienz in der Produktion steigern“, sagt Schmuttermayr.
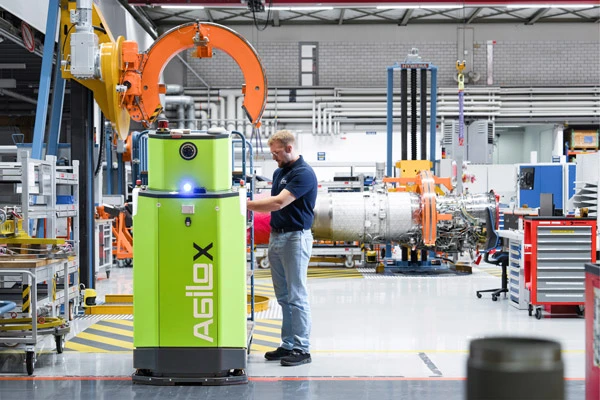
FTS transportieren die wertvollen Bauteile sicher und effizient von einer Station zur nächsten – und das in einer Arbeitsumgebung, die höchsten Sicherheitsanforderungen gerecht werden muss.
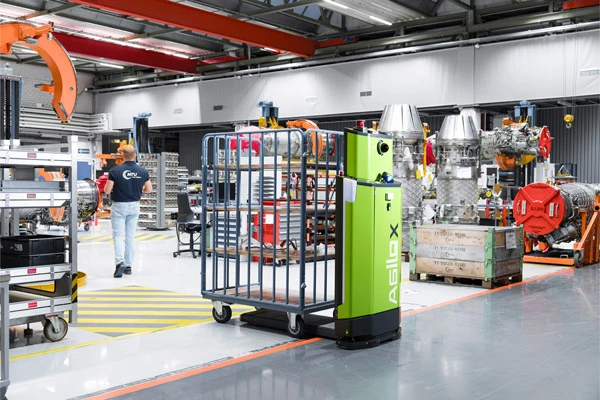
Dank intelligenter Routenplanung und umfassender Sensorik gewährleisten die Fahrzeuge maximale Sicherheit und Präzision.
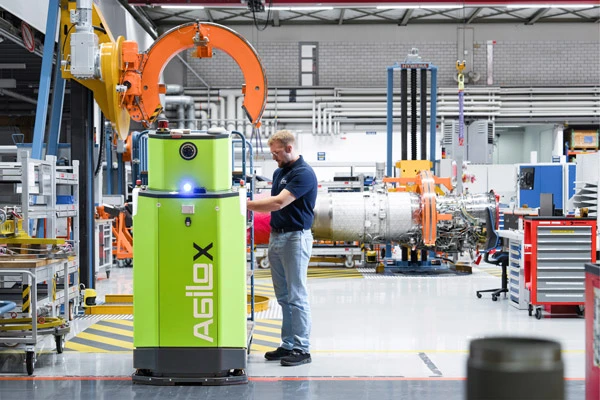
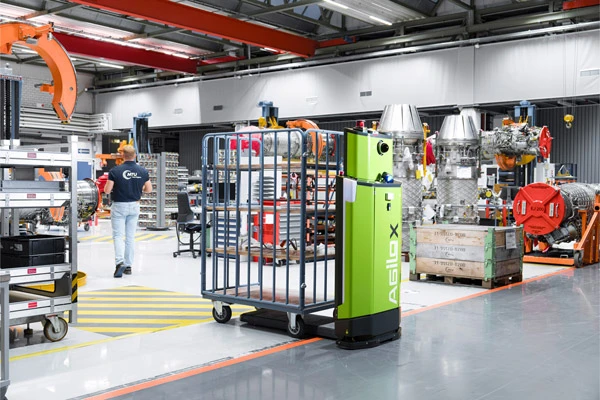
Tracker für mehr Transparenz
Jeder Wagen, den das FTS durch die Hallen transportiert, ist mit eine Tracker versehen. Das Track & Trace-System ermöglicht die Echtzeit-Lokalisierung sämtlicher produzierter Bauteile und sorgt so für mehr Transparenz und Effizienz im Produktionsnetzwerk. „Die Mitarbeiter:innen wissen also zu jedem Zeitpunkt, wo sich ein bestimmtes Bauteil befindet, dass sie erwarten oder verschickt haben“, sagt Leifheit.
Fahrerlose Transportsysteme sind inzwischen an MTU-Standorten weltweit im Einsatz, beispielsweise in der kürzlich eröffneten modernsten Turbinenscheibenfertigung der Welt bei der MTU in München. FTS gibt es auch an den MTU Maintenance-Standorten in Hannover und Zhuhai. Der Einsatz weiterer Systeme ist bei der MTU Maintenance Berlin-Brandenburg sowie an den MTU-Standorten in Polen und Serbien geplant. Den Know-how-Austausch sichert dabei ein auf die FTS-Innovation spezialisiertes standortübergreifendes MTU-Team.
Die ungewöhnlichen Namen „Lena“, „Yoda“ und „Denki“ stammen übrigens vom Hersteller Agilox und den MTU Kolleg:innen. Statt „Ich fordere das fahrerlose Transportfahrzeug an“ heißt es dann einfach: „Ich ruf Denki“.