innovation
Beschichtungen am Triebwerk: Galvanische Verfahren
Bei der MTU stehen 150 Bäder bereit, mit denen Triebwerksbauteile be- und entschichtet werden können. Die Galvanik spielt für die Prüfung und Fertigung anspruchsvoll geformter Blisks eine wichtige Rolle.
Autorin: Monika Weiner | 6 Min. Lesezeit veröffentlicht am: 05.10.2023
Autorin:
Monika Weiner
arbeitet seit 1985 als Wissenschaftsjournalistin. Die Diplomgeologin interessiert sich vor allem für neue Entwicklungen in Forschung und Technik sowie deren gesellschaftliche Auswirkungen.
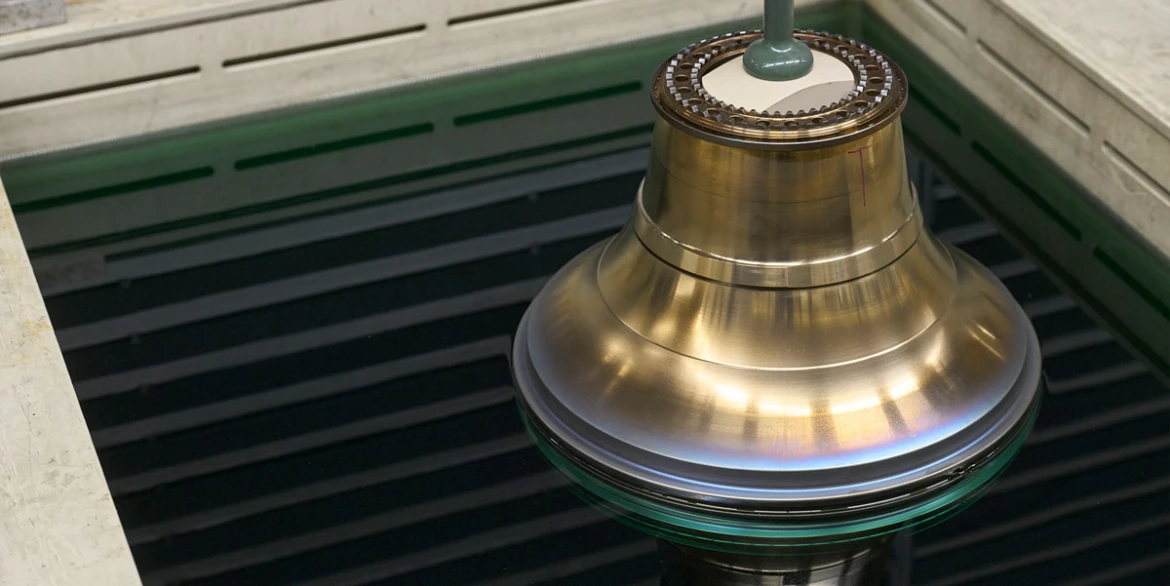
Nur ein leises Surren ist zu vernehmen. Ein kastenförmiger Stahlkoloss gleitet auf Schienen in mehr als zwei Metern Höhe über eine Reihe riesiger, mit Chemikalien gefüllter Kunststoffwannen hinweg. Mit einem kurzen Ruck kommt der Transportroboter genau über dem Nickelsulfamat-Becken zum Stehen. Durch eine Luke im Boden wird nun ganz langsam ein mit zwei Blisks beladenes Gestell abgeseilt. Bei Blisks, die Abkürzung steht für Blade Integrated Discs, werden Schaufeln und Scheiben aus einem Stück gefertigt. Dadurch sind sie nicht nur leichter und stabiler als klassische Verdichterrotoren, sondern haben auch eine bessere Aerodynamik. Die Fertigung ist allerdings auf Grund der anspruchsvollen Geometrie extrem kompliziert.
Zentimeter für Zentimeter tauchen die Blisks in das Nickelbad, am Ende rastet das Gestell mit einem Klick in der Elektrodenschiene ein, die Beschichtung beginnt. Die Spannung zwischen der positiven Anode und der negativen Kathode, mit der die Rotoren verbunden sind, sorgt dafür, dass positiv geladene Nickelionen in der Elektrolytflüssigkeit zum Minuspol wandern und sich dort niederschlagen. „Durch diesen Abscheide-Prozess können wir auf den Schaufelspitzen der Blisks Atom für Atom eine stabile Nickelschicht aufbringen“, erklärt Michael Blümel, zuständig für die Prozessoptimierung in der Galvanik der MTU Aero Engines.
Weltweit einzigartige Beschichtungsanlage für Blisks
Während sich die Nickelatome auf den Spitzen der Schaufeln ablagern, sind die Bauteile ständig in Bewegung: Ein in das Gestell integrierter Elektromotor dreht die Scheiben langsam. „Durch diese Drehung wird die Nickelschicht sehr gleichmäßig. Gleichzeitig können wir während der Bildung ihre Eigenschaften beeinflussen, indem wir gezielt Substanzen einbauen“, ergänzt Blümel. Für die Beschichtung, die gerade aufgetragen wird, rieselt Bornitrid-Sand aus einem Behälter auf die schmalen Schaufelspitzen. Diese scharfkantigen Industriediamanten werden so direkt in die Nickelschicht eingelagert und von dieser teilweise umschlossen und damit festgehalten, es entsteht eine perfekte Panzerung.
„Die galvanischen Beschichtungsanlage ist die einzige weltweit, mit der sich die kompliziert geformten Bisks auf den Mikrometer genau beschichten lassen.“
Leiter der Galvanik bei der MTU
„Die galvanischen Beschichtungsanlage ist die einzige weltweit, mit der sich die kompliziert geformten Blisks auf den Mikrometer genau beschichten lassen“, betont Ali Cimen, Leiter der Galvanik bei der MTU. „Die Panzerung der Schaufelspitzen, sogenannte Blade-Tips, ist enorm wichtig. Sie sorgt dafür, dass sich die Blisks in den harten Belag des Gehäuses, der sie im Triebwerk umgibt, einschleifen können, ohne dass die Bauteile Schaden nehmen. Dank dieser Beschichtung können die Konstrukteur:innen den Spalt zwischen Blisk und Gehäuse minimieren und so den Wirkungsgrad des Triebwerks signifikant erhöhen.“
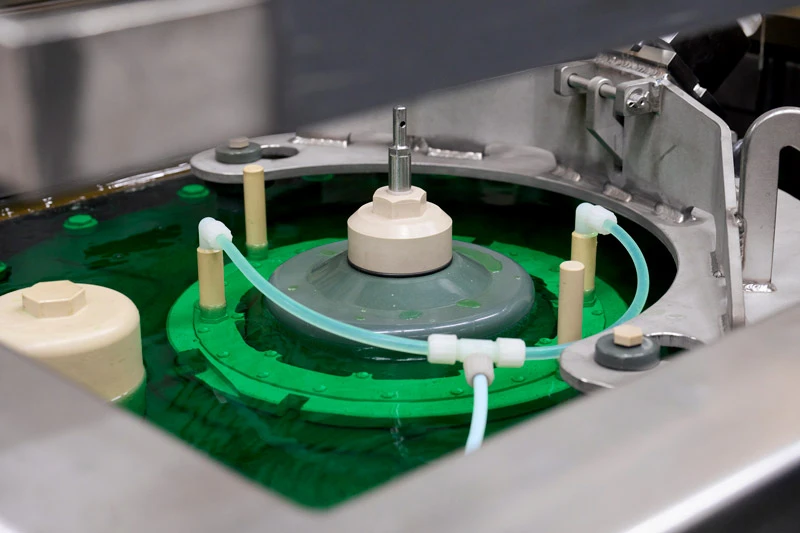
„Stromlos-Nickel“: In diesem Nickelbad werden Bauteile beschichtet, ohne von extern Strom anlegen zu müssen. Dies wird bei Bauteilen angewendet, die eine sehr gleichmäßige und nicht mechanisch nachzuarbeitende (also dünne) Schicht tragen sollen. Hier „badet“ aktuell eine TP400-D6 Blisk in der grün schimmernden Flüssigkeit.
Jahrhundertealte Technologie
Die elektrochemische Beschichtung geht zurück auf ein Prinzip, das Luigi Galvani bereits im 18. Jahrhundert entdeckt hat, als er bei Versuchen mit Froschschenkeln bemerkte, dass diese beim Berühren mit zwei Elektroden aus verschiedenen miteinander verbundenen Metallen zuckten. Technisch genutzt wurde die Galvanik erst zu Beginn des 19. Jahrhunderts zum Vergolden und Versilbern von Metallen.
„Das Faszinierende an der Galvanik ist ihre Vielseitigkeit. Wir können sie im Triebwerksbau einsetzen, um Oberflächen anzuätzen und damit das Gefüge sichtbar zu machen, aber auch, um Korrosionsschutz- und Gleitschichten oder Panzerungen aufzubringen.“
Leiter der Galvanik bei der MTU
Heute ist die Galvanotechnik ein etabliertes Verfahren, mit dem man Werkstücken exakt die gewünschten Eigenschaften verleihen kann: besondere Härte durch Beschichtung mit Chrom, Korrosionsbeständigkeit durch Aufbringen von Platinschichten sowie ein guter Verschleißschutz durch Nickel- oder Dispersionsschichten. Bei allen galvanischen Beschichtungen wird das Metall, das aufgetragen werden soll, an die positive Anode (Pluspol) angeschlossen, während das zu beschichtende Werkstück mit der negativen Kathode (Minuspol) verbunden ist. Je mehr Strom fließt und je länger die Beschichtung dauert, desto mehr Ionen wandern zur Kathode und desto dicker wird die Schicht. Schließt man das Bauteil hingegen an die Anode an, läuft der Prozess genau andersherum: Metallatome an der Bauteiloberfläche lösen sich auf, werden zum Metallion und bewegen sich in der Lösung – weg vom Werkstück – zur Kathode. Auch das wird in der Galvanik genutzt, etwa um Oberflächenfehler von Bauteilen sichtbar zu machen.
In galvanischen Bädern kann daher nicht nur be- sondern auch entschichtet werden. „Das Faszinierende an der Galvanik ist ihre Vielseitigkeit“, betont Cimen. „Wir können sie im Triebwerksbau einsetzen, um Oberflächen anzuätzen und damit das Gefüge sichtbar zu machen, aber auch, um Korrosionsschutz- und Gleitschichten oder Panzerungen aufzubringen.“
Galvanische Prozesse zur Qualitätssicherung
Bei der Fertigung von Blisks spielt die Galvanik immer wieder eine wichtige Rolle: Sobald die Rohlinge die ersten Bearbeitungsschritte durchlaufen haben, werden sie in ein säurehaltiges Becken getaucht, um eine mikrometerdünne Schicht abzutragen. Dieses Beizen aktiviert die Oberfläche. Es folgt ein alkalisches Bad, durch das sich auf den Oberflächen eine blaue Oxidschicht bildet. Diese lässt Korngrenzen im Metall hervortreten. Die Spezialist:innen bei der MTU können auf diese Weise auffällige Muster im Gefüge aufspüren, die auf Schwachstellen hindeuten. Solche Materialfehler sind gefährlich, denn sie können im Flugbetrieb zu Rissbildungen und im schlimmsten Fall zum Zerplatzen der ganzen Scheibe führen. Bei der Sichtprüfung werden daher alle Blisks, die Fehler aufweisen, aussortiert.
Nur Blisks, die alle Stationen der Qualitätssicherung – neben der Gefüge- spielt auch die Rissprüfung eine wichtige Rolle – durchlaufen haben, kommen für die finale Spitzenpanzerung zurück ins galvanische Bad. Damit sich die Nickel-Diamantschicht tatsächlich nur auf den äußersten Spitzen der Schaufeln ablagert, müssen alle anderen Teile abgedeckt werden: „Wegen der komplizierten Geometrie ist das ein aufwändiger Prozess“, erklärt Blümel. Zunächst wird eine schützende Lackschicht auf die Schaufeln aufgebracht und anschließend an den Stellen, die beschichtet werden sollen, wieder entfernt: Um die Oberfläche der Schaufelspitzen freizulegen, benötigen die Expert:innen Skalpell, Lupe und eine ruhige Hand. Am Ende werden die Scheibenkörper mit Halbschalen abgedeckt und jeweils zwei Blisks auf die eigens dafür entwickelten drehbaren Gestelle montiert.
Michael Blümel, Prozessverbesserer in der Galvanik.
Alles weitere läuft vollautomatisch ab: Der Transportwagen nimmt jeweils ein Gestell auf, fährt auf Schienen zum ersten der galvanischen Bäder und lässt seine Fracht dort vorsichtig hinunter. Innerhalb weniger Minuten ätzt Säure eine mikrometerdünne Schicht von den Spitzen der Schaufeln. In einem weiteren Säurebad wird die Oberfläche aktiviert, danach wird die Schaufelspitzenpanzerung aufgebracht. Dieser Vorgang dauert einige Stunden. Wenn er abgeschlossen ist, nimmt der Transportroboter das Gestell wieder auf und transportiert es zu einer Wanne. Diese ist gefüllt mit einem speziellen Lösungsmittel, um den Lack von den Schaufeln zu entfernen. Nach einer abschließenden Sichtprüfung sind die Blisks fertig für die Schlussprüfung und Endabnahme.
Auch bei gebrauchten Triebwerksteilen kommt die Galvanik ins Spiel
Die Galvanik-Bäder werden nicht nur für die finale Beschichtung neuer Blisks genutzt, sondern auch für die Instandsetzung von Triebwerksbauteilen. Durch den häufigen Kontakt mit Sand und Staub in der Luft können sich deren Formen und technischen Eigenschaften im Laufe der Zeit verändern. Will man sie neu beschichten, müssen zunächst alle alten Schichten entfernt werden. Bei der MTU steht hierfür eine Kammer mit einer Hochdruck-Wasserstrahl-Anlage zur Verfügung, in der ein rotierender Strahl mit 3.500 bar auf die Oberflächen trifft. Alternativ lassen sich alte Beschichtungen auch durch chemische Lösungen wieder abtragen. Es folgt eine umfangreiche Säuberung, Entfettung und Aktivierung der Oberflächen. Erst dann kann der galvanische Beschichtungsprozess von Neuem beginnen.
Galvanische Beschichtungen und ihr Einsatzgebiet
In der Galvanik der MTU gibt es etwa 150 verschiedene Bäder, in denen sich Säuren, Laugen und organische Lösungen befinden. Genutzt werden diese Bäder nicht nur für die Beschichtung von Neuteilen, sondern auch, um gebrauchte Bauteile instand zu setzen, deren Geometrie sich durch Vibrationen, Rotation und Verschleiß im Triebwerk verändert hat.
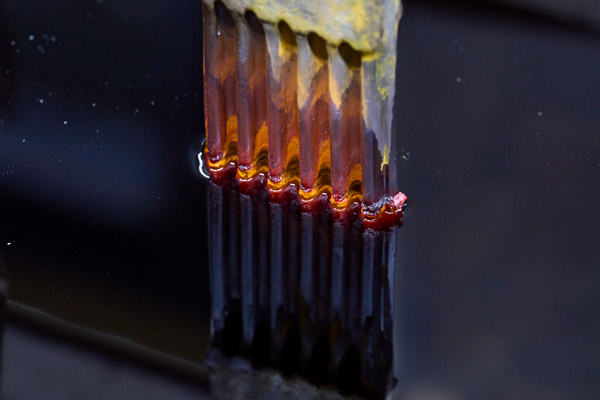
Um den Stromfluss zu gewährleisten, wir hier mit einer im Chrombad hängenden Bleianode gearbeitet.
Verchromen
Zum Verchromen können Bauteile in eine Wanne mit 4.000 Liter Chromsäure eingetaucht werden. Es ist das größte galvanische Becken bei der MTU. Da Chrom sehr harte Schichten bildet, die dazu sehr temperaturbeständig sind, werden sie genutzt, um Triebwerksbauteile wieder in die ursprüngliche Form zu bringen, die hohen Temperaturen und starken mechanischen Beanspruchungen ausgesetzt sind - beispielsweise in Triebwerkslagern.
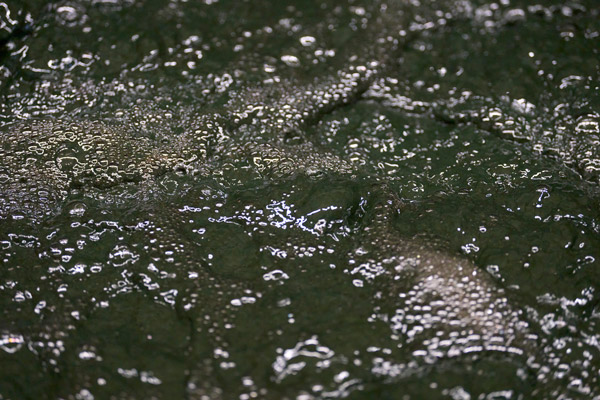
Das Kobaltbad enthält Feststoff, der in die Dispersionsschicht eingelagert wird und dient als Verschleißschutzbeschichtung. Dadurch erscheint das sonst eher rötliche Kobalt hier grünlich.
Beschichtung mit Kobalt
Für eine Beschichtung mit Kobalt werden Bauteile in Kobaltsulfat-Bäder getaucht. In die Kobalt-Beschichtungen, die hier aufgetragen werden, lassen sich auch Feststoffpulver integrieren, die während des Beschichtungsprozesses auf das Bauteil rieseln. Auf diese Weise bekommen die Schichten genau die gewünschten Gleit- und Schleifeigenschaften. Kobalt-Beschichtungen werden beispielsweise für die Instandsetzung von Brennkammer-Gehäusen genutzt.
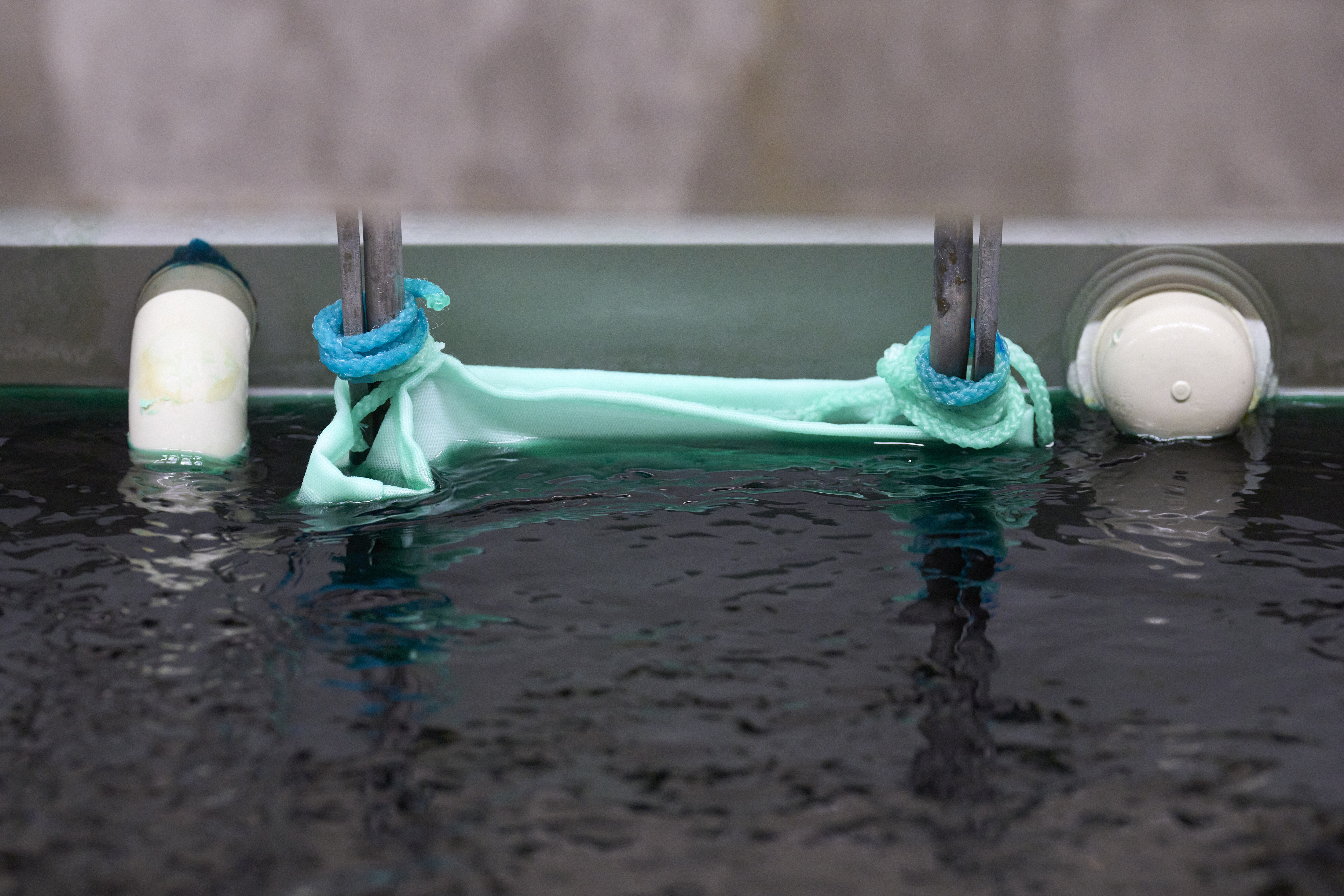
In diesem Nickelsulfamatbad besteht die Anode aus Ni-Plättchen, die den Stromfluss ermöglichen und langsam in Lösung gehen.
Vernickeln
Zum Vernickeln stehen Bäder gefüllt mit Nickelchlorid und Nickelsulfamat bereit. Hier werden Bauteile galvanisiert, die schnell verschleißen und daher Schichtdicken zur Wiederherstellung der ursprünglichen Bauteilmaße von mehreren Millimetern benötigen. Durch den Einbau von Diamantpulver lassen sich Gleit- und Schleifeigenschaften beeinflussen. Die Spitzen von Blisks beispielsweise bekommen durch die Nickel-Diamantbeschichtung eine Panzerung, mit deren Hilfe sie sich optimal in das Gehäuse einschleifen.
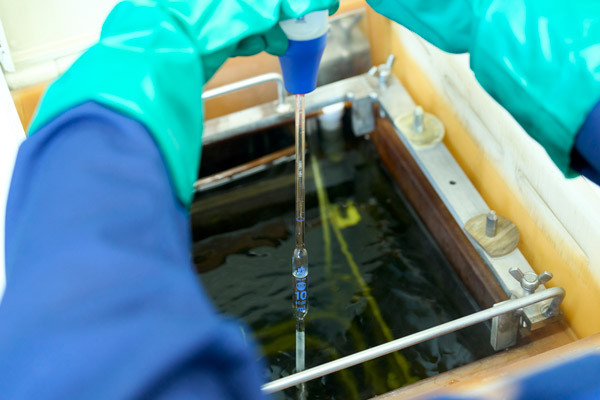
Die leicht gelbe Farbe im Becken deutet auf das Edelmetall Platin hin. Alle zwei Stunden müssen Proben von den Lösungen genommen werden, um den Platingehalt zu überprüfen. Die Proben müssen mit einer Pipette entnommen werden und im kalten Zustand im Labor geprüft werden, da der Platingehalt im erhitzten Bad verzerrte Ergebnisse liefert.
Platinbeschichtung
Für Platinbeschichtungen gibt es Becken mit Platin-Lösungen. Diese werden in mikrometerdünnen Schichten aufgebracht und bieten einen extrem belastbaren Hochtemperatur-Oxidationsschutz. Platinbeschichtungen werden beispielsweise bei der Neuteilfertigung auf die Schaufeln von Hochdruck-Turbinen aufgebracht.