innovation
New data management system for engine test data
For the past 40 years, the measurement database has provided developers and engineers at MTU with valuable services. Now a large-scale operation is under way to build the next-generation database.
author: Thorsten Rienth | 4 mins reading time published on: 08.06.2021
author:
Thorsten Rienth
writes as a freelance journalist for AEROREPORT. In addition to the aerospace industry, his technical writing focuses on rail traffic and the transportation industry.

Around 1980, a group of engine and software developers at MTU Aero Engines put their heads together. There had been some major innovations in two areas that significantly impacted their work: computers had just made a huge leap in performance and were being widely adopted in engine development, and test stands were being equipped with a new generation of sensors. Never before had it been possible to record engine data in such detail. Now a database was needed to merge these two systems.
The engine and software developers opted for a file structure with binary containers. Computer programs use this format to structure data for further processing or to optimize storage for certain data fields, the smallest unit of a dataset. Dr. Fabian Bayerlein, an IT project manager and developer, explains the main disadvantage with this: “The stored data is highly fragmented and it sometimes takes days to run comprehensive analyses of engine test runs.”
Of course, the MTU measurement database has grown in step with advances in technology over the past 40 years. “We greatly expanded storage capacity, multiplied access speeds and implemented new programming interfaces,” Bayerlein says. But a further disadvantage remained: “The choice of architecture that was made back then really limits the options for combining measurement data with higher-level metadata.”
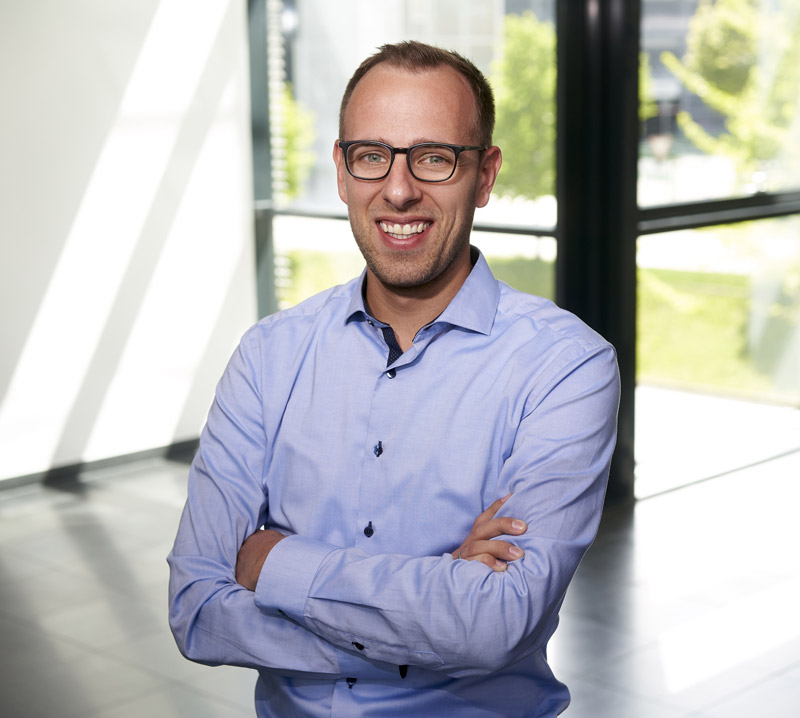
“What brought me to MTU was an EU research project I worked on while completing my studies in 3D metal printing at TU Munich; the project’s outcome is now in productive use at MTU. That means MDM2020 is already the second project I’ve worked on where I don’t just program software, but also see every day how it connects directly to technical applications. I really enjoy the in-depth communication with the users in the department and finding solutions together in an atmosphere of trust.”
IT project manager and developer at MTU Aero Engines
Access to measurements from all departments in just seconds
The trouble is that this kind of data linkage is absolutely essential for modern engine development. Michael Kern, a calculation engineer who works in engine performance calculation, gives this example: in a turbine, some physical values can be measured directly, such as pressure at the component inlet. “But other values, such as an engine’s thermal efficiency, are determined through analysis calculations. These analyses are based on complex engine models that draw on a great many measurements.” The developers have to set hundreds or even thousands of measurements in context. “With the current measurement data management system, it takes a huge amount of effort to set the values—because it takes so much effort to access them in the first place.”
That’s why, together with Kern, Bayerlein began to establish a standardized and central management system for test data. In their project, which goes by the name MDM2020—short for “measurement data management 2020”—they and their team are working across departments and disciplines on nothing less than building a completely new MTU measurement data management system.
The aim is, first, to facilitate the simplest possible acquisition of the measurements from all tests and test runs and, second, to give developers the easiest possible access to them with the tools they already have. The development team will have to build most of it from scratch. There is no blueprint they could use for orientation. These kinds of IT-based solutions bolster the efficiency of MTU’s design processes and, with it, the company’s competitiveness.
Standardization meets customized tools in engine development
Their approach turns the previous, decades-old strategy upside down. “Instead of each department accessing the file structure directly, we’re working on a server-based database with a wide range of interfaces for searching metadata,” Bayerlein says. The structure uses an open source software that runs on an established standard. “This provides a solid foundation while also enabling the technical departments—from engine performance calculation to aeroelastics to structural mechanics—to connect to it with their requirements, which, particularly in engine development, can be very distinct.”
In which measurement channels of a particular prototype engine were temperatures of 500 degrees Celsius exceeded in test runs? Which measurement series were conducted with a particular combination of hardware and software and which sensors were used? Bayerlein and the team also want to channel conventional measurement data searches, for instance for long-term performance assessments in MRO, through the same interfaces. How do certain readings from a particular engine change over its service life? And how high was the share of particularly high speeds during that service life? Value by value, the developers want to create an ever more finely meshed network of measurement efficiencies, relationships and ratios—and then draw valuable conclusions from them in designing the next generation of engines.
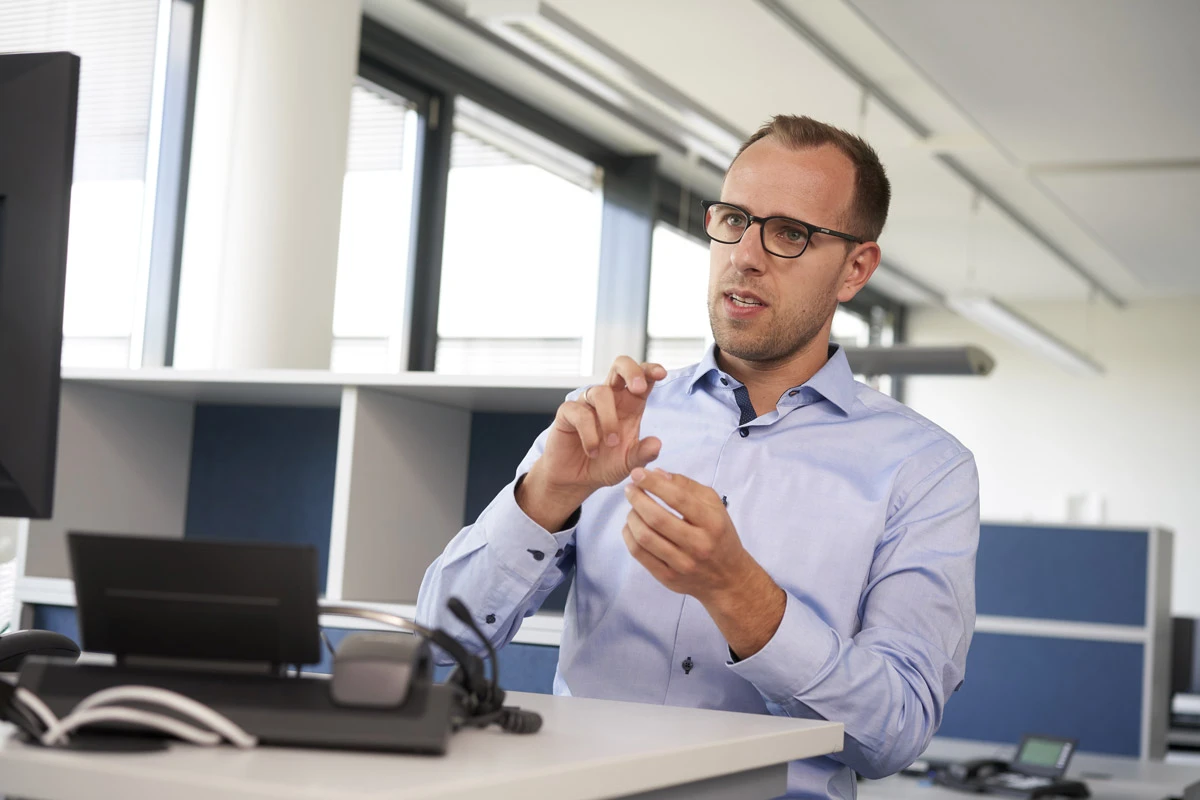
Interdisciplinary teamwork: A full team from various departments has been enlisted to help Fabian Bayerlein establish a standardized management system for test data.
Data hub for OEM and MRO business
The route to this goal sometimes follows the road, even in aviation. In creating this measurement data management system, MTU is cooperating with a number of partners, including some German automotive manufacturers. A cross-industry consortium has been working with standardized measurement data management systems for several years now. “We’re taking advantage of features that have already been implemented, and thus also tested, and adapting them for use in our system,” Bayerlein says. In return, the partners get the opportunity to use the MTU-specific features in their own applications.
MDM2020 can be thought of as a data hub. “Let’s say an overhauled engine completes acceptance testing at MTU Maintenance Zhuhai: we want the data from that to benefit our colleagues in repair development at MTU Maintenance Hannover, for instance, or the developers who are working on the next engine generation in Munich.”
The framework for this kind of data hub is currently being designed. The new measurement data management system is set to go into operation sometime in 2022, succeeding its predecessor. Bayerlein says that the architecture could also certainly be expanded to include applications beyond testing and engine development, should any such requirements materialize.
MDM2020
Data hub: MDM2020 collects the data from all tests and test runs, and prepares it in a way that gives all departments and partners access to the information they need.