innovation
Mastermind for MTU production
MTU is rolling out a unified manufacturing execution system (MES) with which the company will orchestrate all its production activities in the future.
4 mins reading time published on: 14.07.2021
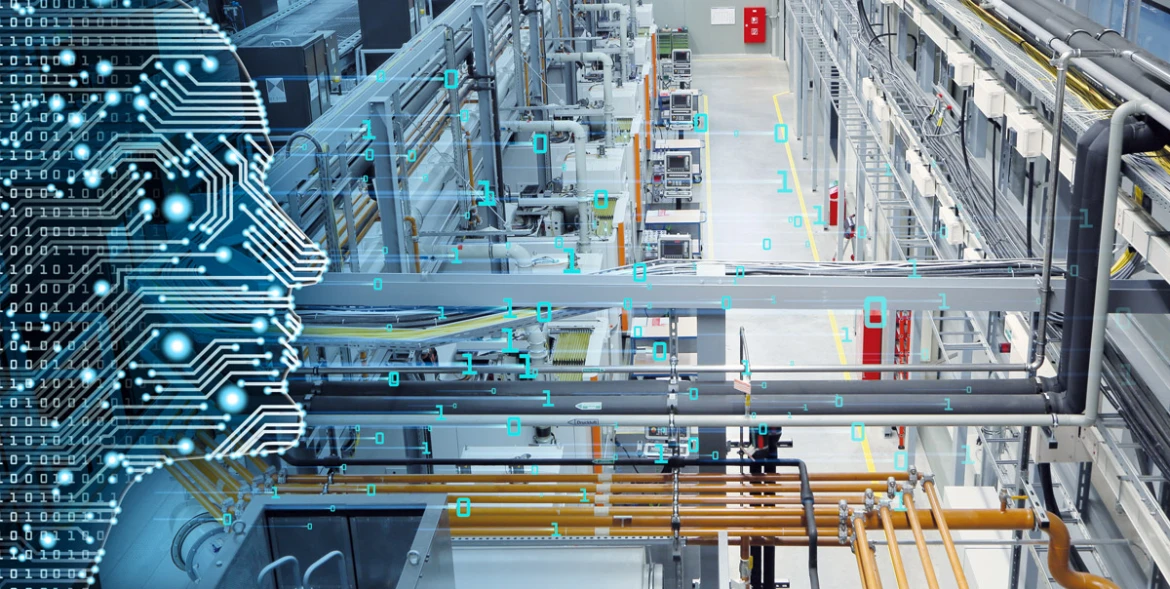
To look at the diagram, you’d think a child had randomly rearranged colored building blocks within a rectangle. Some are green, light blue, dark blue or yellow. Others are gray or pink. Sometimes there’s a bit of space between them, in other instances they are close together. But each one is true to the edges of the rectangle. Of course, this is not the work of a child. “Each color represents a certain piece of machinery—milling and grinding machines, or rigging, balancing or storage areas,” explains Ralf Teufel, head of SAP manufacturing at MTU Aero Engines.
The rectangle Teufel is pointing to is a stylized depiction of a production facility at MTU in Munich. This is where Germany’s leading engine manufacturer produces many things, including highly complex blisks—bladed-disk rotors made from a single workpiece. Not only do these take up less space and weigh less, they also open up new design possibilities in aerodynamics and reduce assembly work and thus costs. The flip side is that producing them takes an almost a seemingly endless number of work steps. A whole ensemble of upstream and downstream processes and sequences needs to be organized. One false note and the whole ensemble is playing off-key. What is needed is a maestro, a mastermind to keep everything under control. And that’s exactly what’s always been missing. But Teufel, who is in charge of IT systems in production, is working to change that.
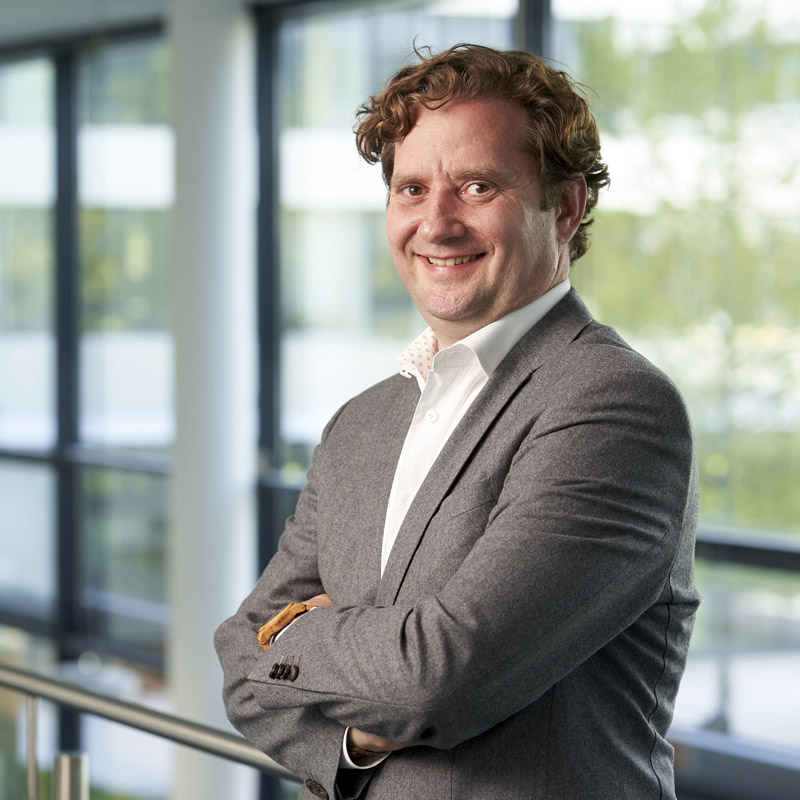
“I was working for MTU back when I wrote my degree thesis, which was on simulated pull control. I went on to hold various supply chain positions, both at MTU Polska and here in Munich. Now I’m in charge of the IT side of the MES rollout, so it’s all coming together nicely for me. What I find most exciting about the MES project is how much I’m learning. I’m gaining real insights into all our areas of production. In return, I can give them a specific idea of how the IT will benefit their applications and together we can craft a vision for the future.”
Head of SAP manufacturing at MTU Aero Engines
Two MES pilot projects launched as upstream test system
Now the mastermind has arrived in the form of a manufacturing execution system (MES). MES will ultimately have the job of directing all of MTU’s production activities. But this is anything but simple. “The more business areas and people are involved, the more diverse and specific the requirements,” Teufel says. “So it’s about finding the most flexible solutions possible, identifying where there is overlap in the specialist areas for the numerous work steps, and establishing technical standards.” This is why there’s more to this large-scale project than simply setting it up and letting it roll. Instead, the idea is for MES to start small and grow from machine to line, line to shop, and shop to all production activities. The blisk production line will become one of two MES pilot projects.” In other words, an upstream test system that MTU will use to develop and tailor its MES to the requirements of the manufacturing landscape.
Teufel is responsible for the digitalization aspects of the MES project and his specialist counterpart in the production facility is Bernhard Gürtler. This facility’s milling machines alone clock up around 6,000 hours of runtime every year. There are any number of questions to consider. Is the right machine free to perform the next work step? Has the updated machine program been approved and downloaded? Are the right raw materials, fixtures and tools lined up? And has the employee with the requisite training been entered in the right slot in the shift schedule? Of course! “We’ve got all these resources on our radar and we’ve refined our planning and put safeguards in place,” Gürtler says.
Nevertheless, Gürtler reports that the organizational effort remains enormous: “The right MES automation plan could lighten our load considerably plus minimize downtimes.” For instance, employees might have the part and fixtures ready at the machine only to find they have to update the machine program before they can get to work. What’s more, MES could bring MTU within reach of partly automated continuous operation for manufacturing steps that take several days to complete. “This would allow us to pre-rig machines and let the machine program run, say, over the weekend, while MES makes sure everything goes according to plan,” Gürtler says.
A toolset for as many manufacturing applications as possible
Over time, MTU started using more and more different tools and production management systems across the company. “The more specialized the solution, the higher the support costs,” Teufel says. “That’s why we now want to establish a single toolset that covers as many manufacturing applications as possible.” It should be consistent in its logic and architecture and offer reusable functions and standardized interfaces. This will make it easy to expand should new manufacturing technologies or engine programs so require.
Several project teams and expert groups are working to identify overlap among domains and to define technical standards for as wide a range of applications as possible. Teufel is aware that this poses a “major challenge”: “It all starts with the machine itself and extends to machinery connections and to facility operation before circling back to detailed planning.” Each level requires a standardized solution that is also compatible with those for the other levels. “Here we want to establish the logic of complete automation, without compromising on our customary level of flexibility when it comes to applications and technology,” Teufel says.
A mammoth task: Ralf Teufel and Bernhard Gürtler work closely together during the rollout of a standardized manufacturing execution system.
Going forward, MES is to underpin the much more varied MRO business
Once the pilot projects are complete, MES will be considered and made available for similar applications in large-scale production. The different requirements identified through automation projects will ultimately lead to the establishment of a new standard for consistent use in the production of new parts. Going forward, MES is to underpin the much more varied MRO business in addition to large-scale engine production. Teufel knows that as MTU gravitates toward this future, it will face the same situation as the child playing with the building blocks: “Each time you add to it, the whole thing becomes more complex.”