people
A flight test engineer works very close to the engine
As Senior Flight Test Engineer at Airbus in Toulouse, MTU expert Tarun Sondhi looks after engines during flight tests. Here he describes his daily routine and what flight tests at minus 30 °C look like.
author: Nicole Geffert | 3 mins reading time published on: 10.07.2023
author:
Nicole Geffert
has been working as a freelance journalist covering topics such as research and science, money and taxes, and education and careers since 1999.
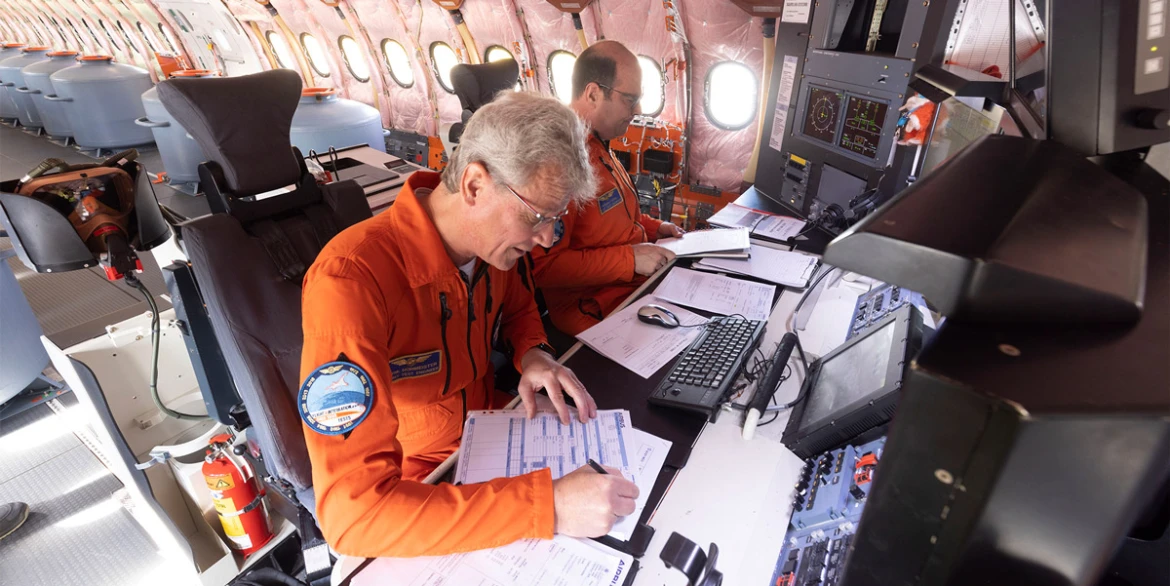
©AIRBUS SAS 2022
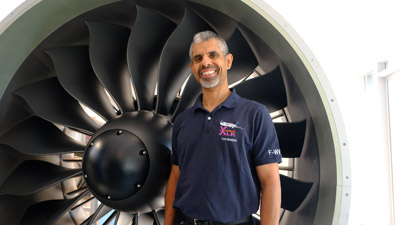
“There’s no such thing as a daily routine—that’s what makes it interesting. But we do have set procedures and processes. Each flight requires careful preparation. The team and I are at the aircraft one hour before every test flight, donning safety clothing such as high visibility vests, helmets and protective shoes. Before boarding the aircraft, I inspect the engines.”
Senior Flight Test Engineer at Airbus’s flight test center in Toulouse
How did you become a senior flight test engineer at MTU?
I studied aerospace engineering at the Technical University of Munich and then started my career at MTU Aero Engines in Munich in 1998. It wasn’t long before I had the opportunity to join the flight test team for the EJ200 Eurofighter engine at what was then EADS in Manching, some 70 kilometers north of Munich. I remember the exciting work out there quite well, with Eurofighters roaring above our heads every day. They used to say that anyone who works there has kerosene in their blood.
So you never got tired of your job in flight testing?
That’s right. No other area of work at MTU gets you as close to the flying engine as flight testing. That’s what fascinates me. It’s also why I didn’t hesitate for a second before joining the TP400-D6 flight test team for the A400M military transporter in 2007. Since 2008, I’ve been working at Airbus’s flight test center in Toulouse, France. In 2014, I transferred from the military to the commercial program. Since then, I’ve been working as an MTU employee in Toulouse to assist Airbus in testing and certifying the PW1100G-JM engine, which powers the Airbus A320neo family.
What does your daily routine look like?
There’s no such thing as a daily routine—that’s what makes it interesting. But we do have set procedures and processes. Each flight requires careful preparation. The team and I are at the aircraft one hour before every test flight, donning safety clothing such as high visibility vests, helmets and protective shoes. Before boarding the aircraft, I inspect the engines. There are no rows of seats. All that space is taken up by things like monitors and a range of measurement devices. Then I start the engine monitoring station (EMS), an electronic device for recording the engine parameters, and prepare everything for recording the engine data.
Are you aboard the aircraft during the test flights?
First Flight A320neo with Pratt & Whitney GTF Advantage. (©Airbus SAS 2022)
No. That’s the job of the engine control engineers, who are also part of our flight test team. They take care of everything related to Full Authority Digital Engine Control (FADEC). Once the aircraft is back on the ground, I obtain the engine data collected and recorded by the EMS during the flight. Evaluating all that data takes quite some time, however. Whenever needed, I have the full support of my MTU colleagues from all disciplines. We also take care of the entire engine documentation, fill in forms and write weekly reports.
What’s been one of your personal highlights on the job?
This spring, we conducted cold-weather tests in Iqaluit in northern Canada. I was aboard the ferry flight to Canada. In Iqaluit, we, the aircraft and the engines were subjected to outdoor temperatures of around minus 38°C. Flight testing aims to demonstrate the systems’ full functionality under extreme weather conditions. I was there for the first time, and it was a week I’ll never forget. We were given special gear to protect us from the extreme cold when we were outside working on the aircraft and the engines.
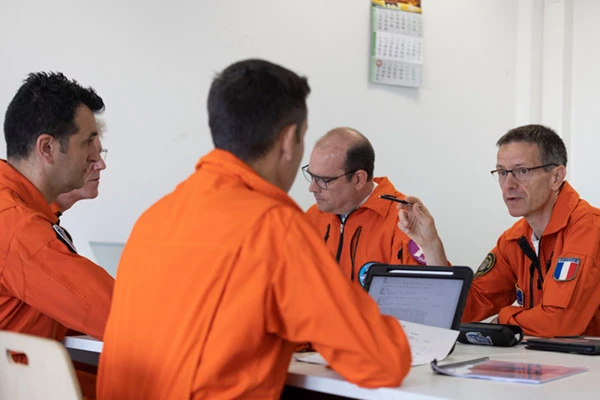
©AIRBUS SAS 2022
A321XLR First flight - check before take off.
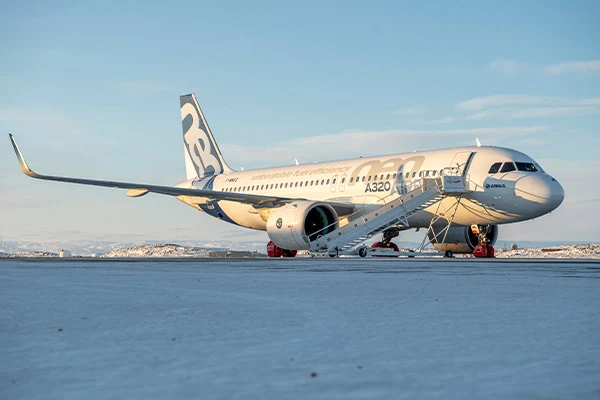
©AIRBUS 2020
A320neo cold weather test at the Iqaluit airport.
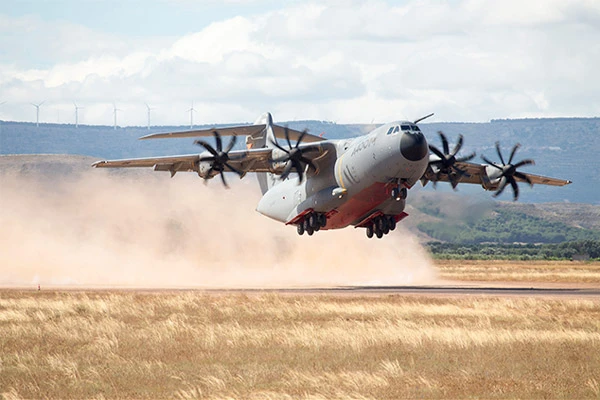
©AIRBUS S.A.S. 2013
Airbus A400M Unpaved Runway Test.
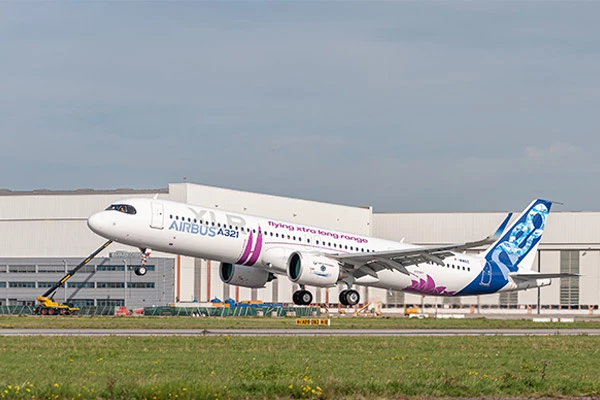
©Airbus 2022 / Stefan Kruijer
First Flight of the second A321XLR test aircraft.
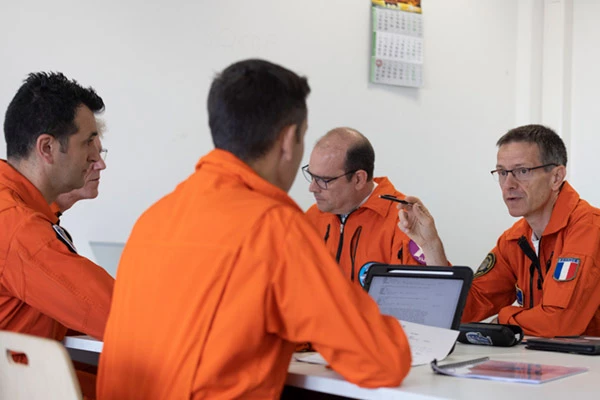
©AIRBUS SAS 2022
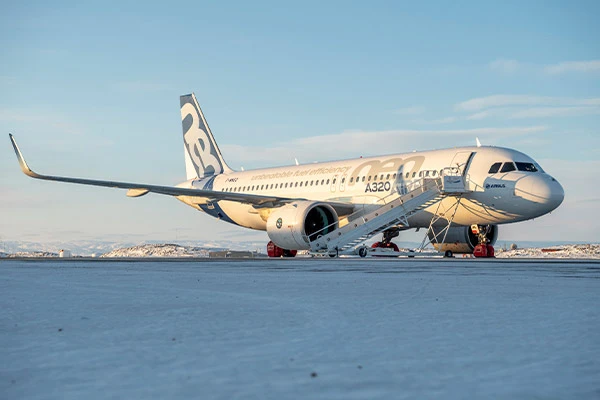
©AIRBUS 2020
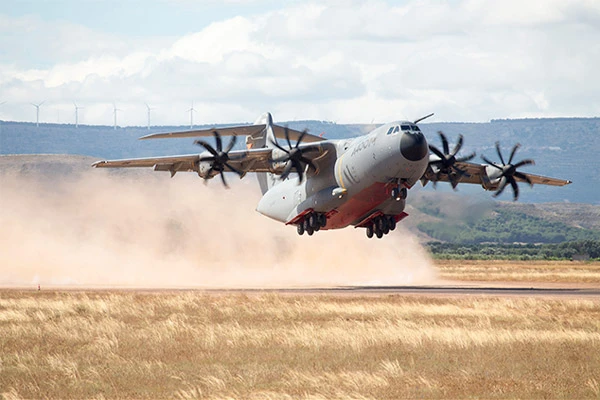
©AIRBUS S.A.S. 2013
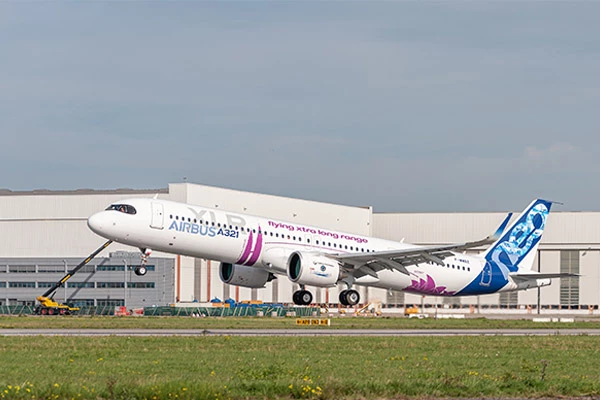
©Airbus 2022 / Stefan Kruijer
Will your services as Senior Test Engineer also be in demand in the future?
Yes, because major modifications to the aircraft or the engine have to be tested and certified in flight. In other words, technological innovations have to pass our flight tests. We’re the first to see the high-tech products our experts develop and manufacture being used in flight.
So, your job never becomes routine?
Never! From my desk, I have a direct view of the building that all the Airbus aircraft park in front of. That means I can see the entire fleet. For many first-time visitors, the huge site dwarfs everything they’ve seen before. Although aircraft taking off and landing have been part of my daily working life for years now, I still look up every time an aircraft starts and takes off.