good-to-know
Tank systems in aircraft: More than just containers
Before takeoff, aircraft must be refueled. But where is the kerosene actually stored? How does the distribution of the tanks affect performance? And how do the requirements differ for alternative fuels? AEROREPORT provides answers to the most important questions.
author: Monika Weiner | 7 mins reading time published on: 05.07.2023
author:
Monika Weiner
has been working as a science journalist since 1985. A geology graduate, she is especially interested in new developments in research and technology, and in their impact on society.
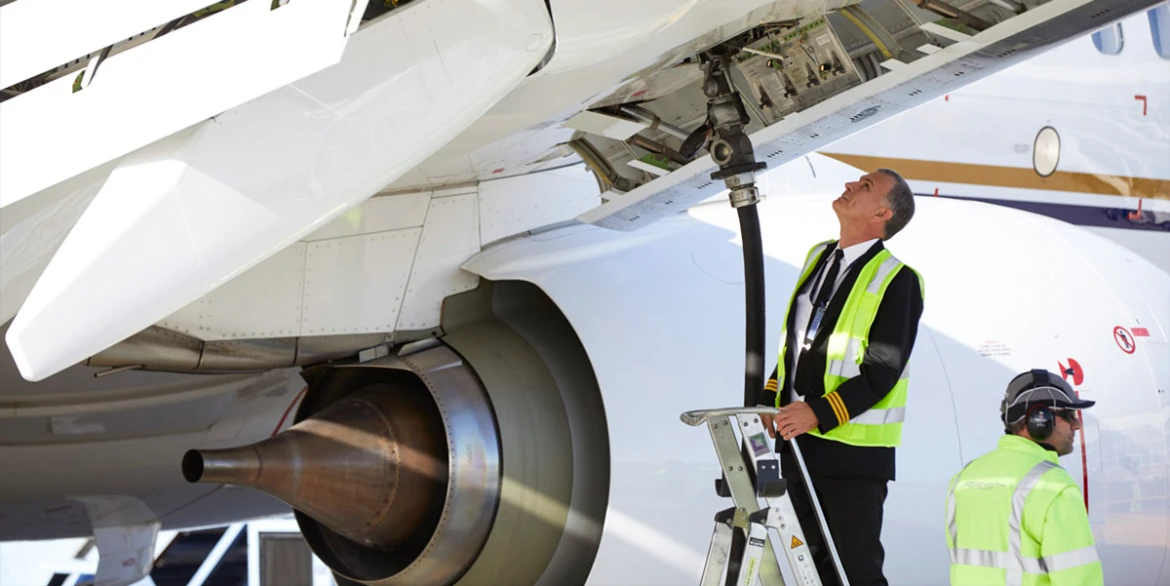
©Lufthansa Technik AG
Where does the fuel go? Cavities become tanks
During aircraft refueling, up to 800 kilograms of kerosene—that’s almost 1,000 liters—flow into the tanks every minute. Commercial aircraft can hold numerous metric tons of fuel: the Airbus A380 can carry some 254,760 kilograms. If this fuel were stored exclusively in the fuselage, as is normal in small propellor aircraft, it would eat up an enormous amount of storage space. And it would make the aircraft structure heavier: during flight, the force of gravity pulls the fuselage downward, while the force of lift pushes the wings upward. The heavier the fuselage and the lighter the wings, the greater are the stresses that the connecting components, the wing roots, must withstand. The only way to minimize these stresses is to shift as much weight as possible to the wings. That makes the wings an ideal place to transport kerosene.
How much fuel is pumped into the tanks depends on the planned flight route. The on-board computer calculates the required quantity, always in accordance with this rule: as much as necessary and as little as possible. To avoid unnecessary weight, the quantity of fuel carried is exactly enough to get the aircraft to its destination plus a safety reserve in case the flight takes longer, for example because congestion at the destination airport delays the landing.
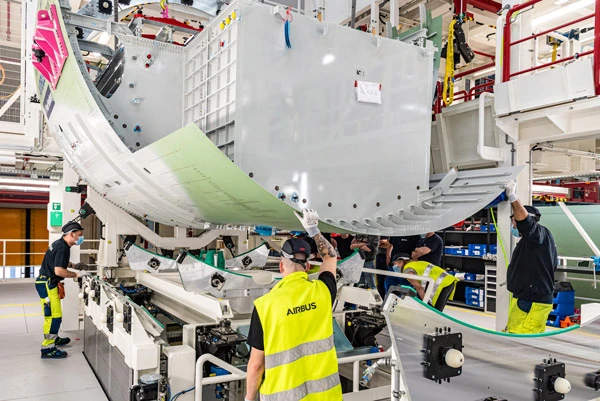
©Airbus - Stefan Kruijer
First Delivery Premium AEROTEC delivers first RCT Rear Center Tank for the A321XLR to Airbus.
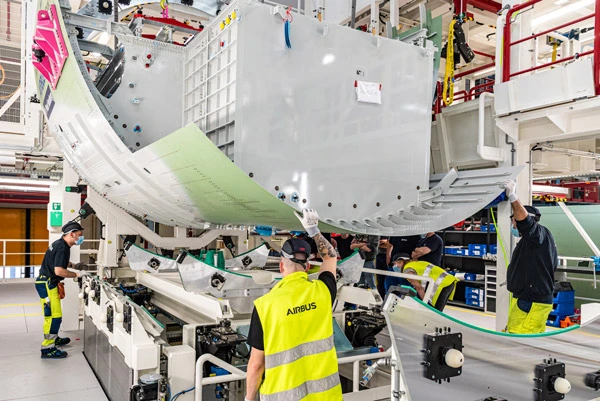
©Airbus - Stefan Kruijer
What tanks are there?
To save weight, the designers of large commercial aircraft have dispensed with steel or plastic tanks and instead use the cavities in the wings. Because these tank systems are integrated into the structure, they are called integral tanks. Depending on the wing design, an aircraft will feature several such tanks, which are sealed with a special sealant and interconnected via a system of pumps and fuel lines. A basic distinction is made between inner tanks, which are located close to the fuselage, and outer tanks, which are located close to the wingtips. Fighter jets follow the same principle of integral tanks, with inner tanks often also used as ballistic protection in the wing.
Some aircraft, for example the Boeing 747, also have a fuselage tank located between the wings under the floor of the passenger cabin. The new Airbus A321XLR, a narrowbody with a record range of 8,700 kilometers, will also be equipped with a fuselage tank: this “rear center tank” is an integral part of the aircraft structure and has a capacity of 12,900 liters.
Long-haul aircraft usually also have an additional trim tank in the tail assembly. This helps stabilize horizontal position during flight: as the fill level and thus the weight of the wing tanks decreases, the aircraft’s center of gravity shifts to the rear; fuel can be pumped forward from the trim tank to compensate.
A321 XLR Worksharing Mapping
Which tank is filled first?
As a general rule, the outer tanks are filled first and emptied last. There’s a simple reason for this: according to the law of the lever, the mass at the wing tip acts most strongly to counteract the load due to lift, thus minimizing the stresses at the wing root. The ideal distribution of fuel among the various tanks is automatically regulated by the on-board computer and shown on a display in the cockpit. The pilot and copilot can make manual readjustments using the tank selector switch. During flight, filling the feed tanks, also known as collector tanks, is the top priority because they supply the engines.
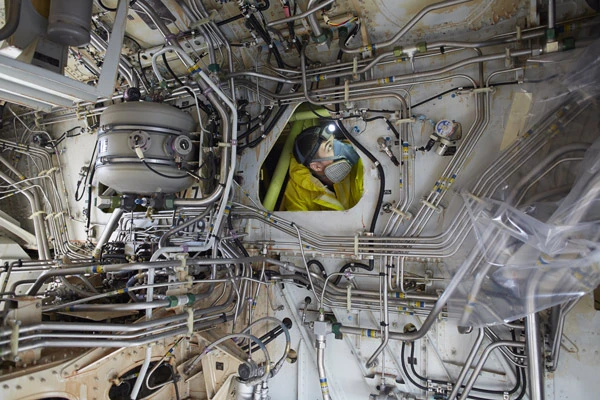
©Lufthansa Technik AG
Control: A mechanic, who not only has to be slim and agile but also not afraid of tight spaces, inspects the tank.
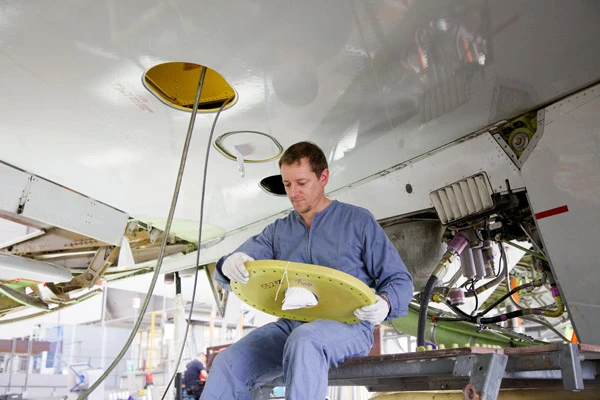
©Lufthansa Technik AG
Cavities become tanks: The wings are an ideal place to transport kerosene.
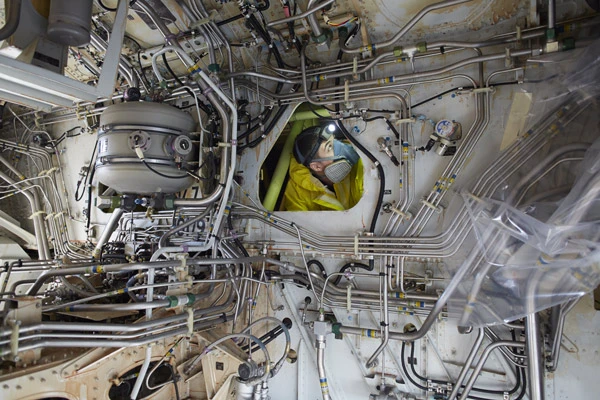
©Lufthansa Technik AG
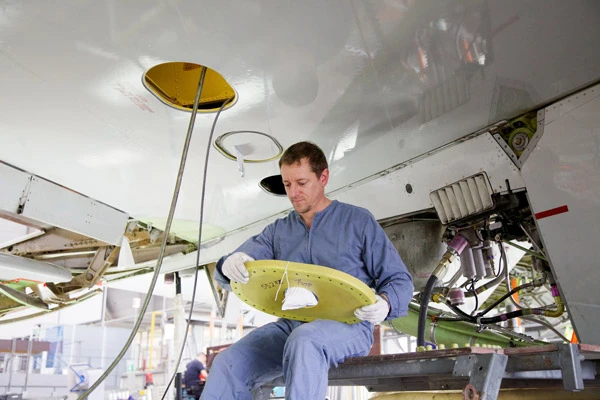
©Lufthansa Technik AG
Why regular inspections are important
The oscillations and vibrations of the wings during takeoff and landing, as well as during flight, for example when flying through turbulence, also put stress on the tank seals. If any leaks are noticed either during the routine check before takeoff or during major inspections, which usually take place at night, an immediate inspection is required. This calls for all the kerosene to first be drained and the tank system ventilated. Only then can a mechanic inspect the tanks. These specialists must not only be slim and agile but also have no fear of tight spaces: they climb inside the integral tanks via openings in the underside of the wing known as manholes to perform a detailed visual inspection in search of damage and seal any leaks.
Challenges in operation: Avoiding damage
During the flight, kerosene is pumped from the tanks to the engines. Commercial aircraft are equipped with a tank ventilation system to avoid a build-up of negative pressure, as this would block the further supply of kerosene. The flight speed forces air through the system’s air intakes to form an air cushion on the fuel in the tank. This not only reduces the evaporation of the fuel, but also supports the work of the pumps.
Water can condense out of the air entering the tanks, and microbes can colonize and multiply in the moist environment that this creates. The result is biofilms that can penetrate the smallest cracks, attack aluminum alloys, and cause corrosion damage. The biomass of such films can also enter the pumps and valves, leading to faults. Biocide additives in kerosene prevent the growth of such microorganisms. The latter nonetheless become a problem especially when an aircraft is stationary for a longer period of time—as was often the case during the coronavirus pandemic. As a result, some tanks had to be specially cleaned before the resumption of flight operations.
How will we fly tomorrow? New fuels sometimes require new designs
Alternative fuels are set to help make the aviation of the future climate-neutral. At engine and aircraft manufacturers, airport operators and airlines, researchers are working on new solutions for propulsion systems, aircraft designs, and infrastructure.
Sustainable aviation fuels, or SAF for short, are an alternative to kerosene, which is derived from fossil fuels. These fuels can be produced from renewable raw materials or with the help of renewable energy sources, carbon dioxide, and hydrogen. Initial tests show that flight operations and infrastructure can be converted to SAF without a problem if certification for the respective aircraft type is available. Using 100 percent SAF without aromatics will probably require adjustments to tank systems, for instance the seals.
Switching to hydrogen would require completely new refueling systems: gaseous hydrogen is rather unsuitable for aviation because it requires extremely large and heavy pressure vessels, which must withstand several hundred bar. Cooling the hydrogen and transporting it in liquid form is a better option. This cryogenic fuel requires special tanks with thermal insulation designed for relatively low pressures of between two and ten bar. Technically, cylindrical or round shapes are best for meeting these requirements, but these are difficult to integrate into the wings. That’s why engineers are already working on new aircraft designs. And the maintenance processes and infrastructure at the airport, including the logistics of making the fuel available, would also have to be redesigned to accommodate hydrogen supply.
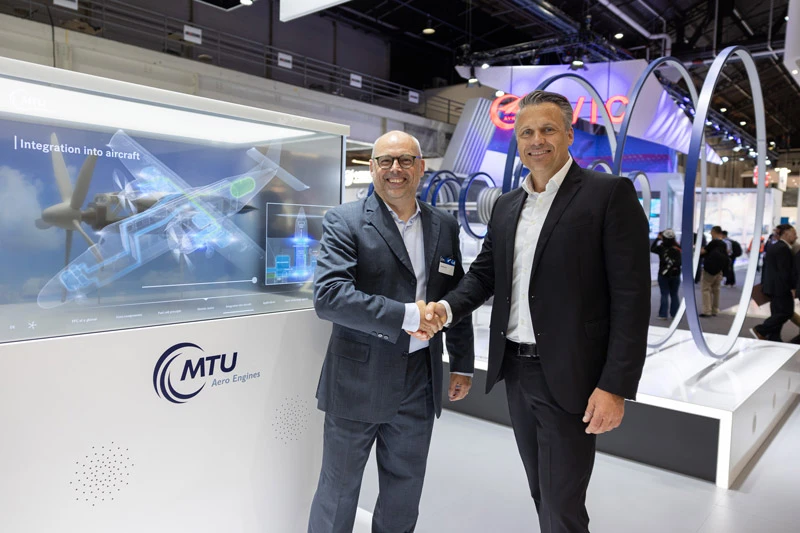
Barnaby Law, Chief-Engineer Flying Fuel Cell™ of MTU Aero Engines (l.) and Markus Staudt, Vice President and Head of Business Development Export, Defence & Hydrogen of MT Aerospace announced the cooperation at Paris Air Show.
A fuel system for liquid hydrogen
MTU Aero Engines is working with aerospace company MT Aerospace to develop a complete liquid-hydrogen fuel system for commercial aviation. The system consists of tanks, sensors, heat exchangers, valves, safety systems, and controls. The first system is to be tested at MT Aerospace in Augsburg before the end of the year. The aerospace company’s experts are responsible for the cryogenic hydrogen storage and supply system, additively manufactured heat exchangers, the sensors, and system integration. The safety system, the control system, and the valve technology are part of MTU’s work package. In terms of system technology, the LH2 fuel system could, with slight modifications, also be used for direct hydrogen combustion in aircraft gas turbines.
The first application is to be MTU’s Flying Fuel CellTM (FFC). In the FFC, hydrogen reacts with oxygen from the air to form water, thereby releasing electrical energy. A highly efficient electric motor then uses this energy to drive the propellor via a gearbox. The FFC does not produce any emissions of CO2 or NOx or particulates—its only emission is water. It thus reduces the climate impact of aviation by as much as 95 percent—i.e., to virtually zero. And since the propellor is then the sole source of propulsion noise, the FFC will also help achieve massive noise reductions.