people
Neue Werkstoffe für die Antriebe der Zukunft
Nachhaltige Antriebe erfordern fortschrittliche Materialien: Darüber sprechen Dr. Jörg Eßlinger, Senior Consultant Materials, und Dr. Inga Stoll, Leiterin Werkstofftechnik bei der MTU.
Autorin: Nicole Geffert | 6 Min. Lesezeit veröffentlicht am: 14.09.2022
Autorin:
Nicole Geffert
arbeitet seit 1999 als freie Journalistin mit den Themen Forschung und Wissenschaft, Geld und Steuern, Ausbildung und Beruf.
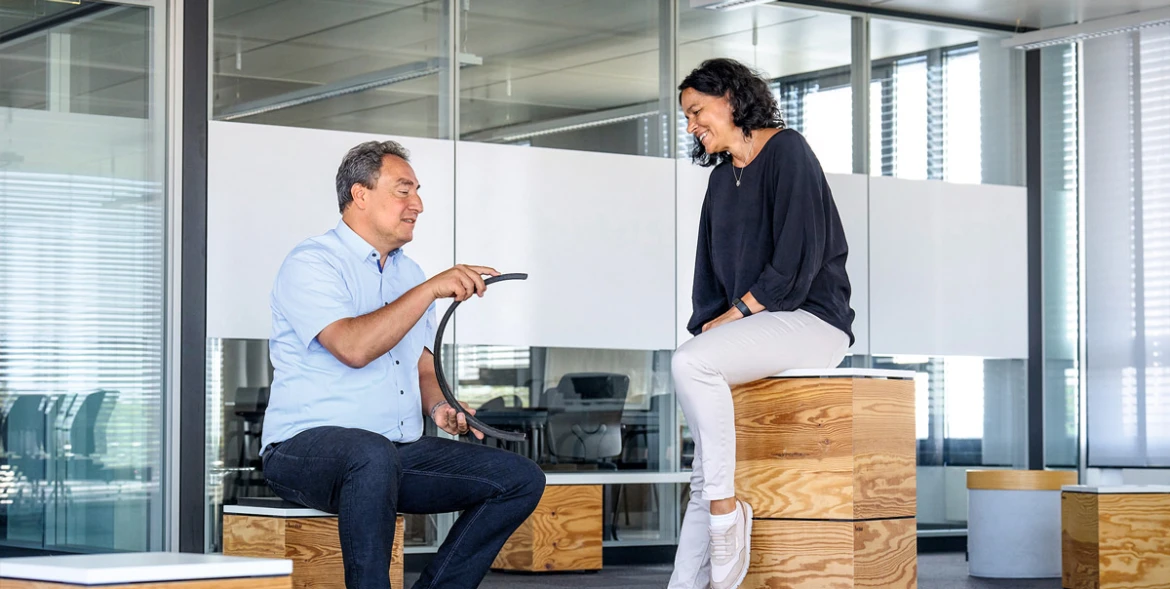
Der Bedarf an innovativen Werkstoffen und Beschichtungen für Triebwerksbauteile ist enorm. Aktuelle Antriebe mit MTU-Technologie, wie der hocheffiziente Getriebefan (GTF), werden weiterentwickelt und mit nachhaltigen Kraftstoffen betrieben, neue Hochleistungstriebwerke für militärische Anwendungen sind zudem zu entwickeln. Parallel dazu treibt die MTU Aero Engines die Entwicklung revolutionärer Antriebskonzepte voran, mit denen die Klimawirkung weiter drastisch reduziert werden kann. Das erfordert auch fortschrittliche Materialien mit neuen Funktionalitäten. Vor welchen Herausforderungen stehen die Werkstoffexpert:innen der MTU?
Jörg Eßlinger: In den vergangenen mehr als 50 Jahren haben vor allem metallische Werkstoffe, wie Nickel und Titan, dazu beigetragen, dass die Triebwerke leichter und sparsamer wurden. Diese Werkstoffe werden stetig weiter optimiert für noch effizientere künftige Antriebe. Im GTF der zweiten Generation soll der thermische Wirkungsgrad des Kerntriebwerks weiter verbessert und gleichzeitig die Profitabilität in Produktion und Betrieb gesteigert werden. Die Materialien müssen extrem hitzeresistent sein, dazu leicht, langlebig und robust. Dabei ist vor allem auch darauf zu achten, dass sie sich prozessstabil, wirtschaftlich herstellen und reparieren lassen.
Inga Stoll: Wir haben für den GTF der zweiten Generation bereits jetzt die besten Werkstoffklassen im Fokus, etwa Einkristalle, spezifische Schutzschichten, hochtemperaturbeständige Scheibenmaterialien sowie Werkstoffe in additiv hergestellten Bauteilen. Auch verbessern wir unsere analytische Beschreibung der Materialien. All dies erlaubt, Leichtbaupotenziale, Temperatureinsatzgrenzen und Lebensdauern voll auszunutzen.
Jörg Eßlinger: Auch für militärische Antriebe gilt: Die Anforderungen an das Material sind nur mit speziellen Hochleistungswerkstoffen zu schaffen. NEFE, die Next European Fighter Engine, verlangt noch höhere Maßstäbe. Um Performance und Leistungsdichte sicherzustellen, sind Leichtbau und Werkstoffe für höchste Temperaturen sowie spezielle Beschichtungen für die Bauteile gefragt.
Inga Stoll: So werden hier beispielsweise faserverstärkte Werkstoffe und Pulvermetalle benötigt. Dazu sind von unserer Seite und von unseren Partnern umfangreiche Investitionen erforderlich, um diese Materialien für unsere Anwendungen hinsichtlich Eigenschaften und Herstellung zu optimieren, weiterzuentwickeln und zu qualifizieren. Wichtig ist zudem, die langwierigen Entwicklungen rechtzeitig zu starten.
AEROREPORT: Einsatztemperatur, Gewicht und wirtschaftlichstabile Herstellung – welche Anforderungen müssen noch berücksichtigt werden?
Inga Stoll: Zusätzlich müssen Werkstoffe gut zu reparieren sein, um für die MTU-Kunden die Maintenance-Kosten zu reduzieren. Bereits im Werkstoffdesign haben wir immer auch die Reparaturfähigkeit des Materials im Blick. Unser Anspruch ist, dass unsere Kunden mit ihren Triebwerken lange fliegen können. Das richtige Material mit dem optimalen Oberflächenschutz kann die Lebensdauer eines Bauteils um den Faktor zwei bis drei erhöhen. Beschichtungen machen den Werkstoff überhaupt erst einsatzbar in einer solch anspruchsvollen Umgebung wie dem Triebwerk.
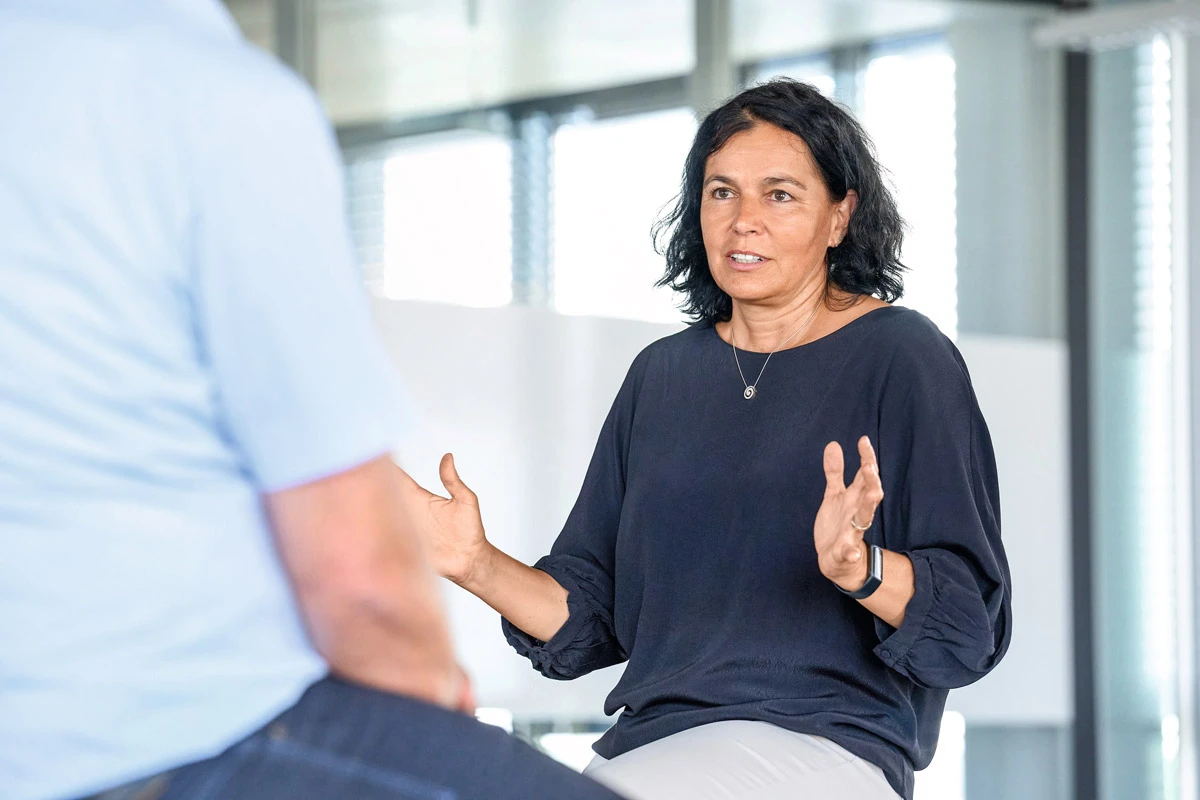
„Wir haben für den GTF der zweiten Generation bereits jetzt die besten Werkstoffklassen im Fokus, etwa Einkristalle, spezifische Schutzschichten, hochtemperaturbeständige Scheibenmaterialien sowie Werkstoffe in additiv hergestellten Bauteilen.“
Leiterin Werkstofftechnik bei der MTU
Jörg Eßlinger: Die Relevanz von Beschichtungen wird noch weiter zunehmen. Bereits heute sind mehr als 60 Prozent der Bauteile im Triebwerk beschichtet als Schutz gegen hohe Temperaturen, Abrieb, chemische Angriffe und Erosion. Wenn die Leistungsdichte im Triebwerk künftig noch weiter zunimmt und sich parallel die Lebensdauerforderungen erhöhen, können die Materialien das nur mit besseren, leistungsfähigeren Beschichtungen meistern.
AEROREPORT: Die MTU arbeitet bereits an revolutionären Antriebskonzepten für die Zukunft. Welche Herausforderungen ergeben sich dabei für die Werkstoffe?
Inga Stoll: Die Anforderungen der Zukunft könnten höher nicht sein. Nehmen wir als Beispiel den Water-Enhanced Turbofan. Hier wird unter anderem Wärmeenergie und Wasser aus dem Abgasstrom rückgewonnen, das Wasser mittels eines Dampferzeugers verdampft und in die Brennkammer eingespritzt. Die Materialien sind also einer feuchten Umgebung ausgesetzt. Die beschleunigte Korrosion durch den deutlich erhöhten Wasserdampfgehalt sollte keineswegs unterschätzt werden. Jegliche Korrosion beeinträchtigt die Funktion eines Bauteils. Wir müssen herausfinden, welche speziellen Beschichtungen zum Schutz der Werkstoffe erforderlich sind.
Jörg Eßlinger: Der hohe Anspruch gilt auch für das MTU-Antriebskonzept der Flying Fuel Cell. Hier stehen nicht hohe Temperaturen im Vordergrund, stattdessen sind mit dem Konzept vor allem die Elektrifizierung und der Einfluss von Wasserstoff verbunden, der für Materialien nicht unkritisch ist. Wir bekommen es mit neuartigen Komponenten zu tun, etwa die Bauteile der Brennstoffzelle selbst, und mit für den Flugtriebwerksbau neuen Werkstoffen und deren Funktionen. Das sind beispielsweise Magnete, kryogener Wasserstoff, aber auch elektrochemische Fragestellungen. In einer Brennstoffzelle reagieren mitgeführter Wasserstoff und Sauerstoff aus der Luft unter Abgabe elektrischer Energie. Es entsteht Wasser. Wasserstoff und Sauerstoff – das klingt erst einmal harmlos. Aber wenn Wasserstoff ins Material eindringt, droht Versprödung. Deshalb arbeiten wir intensiv daran, wie groß der Einfluss ist und wie die Materialien geschützt werden können.
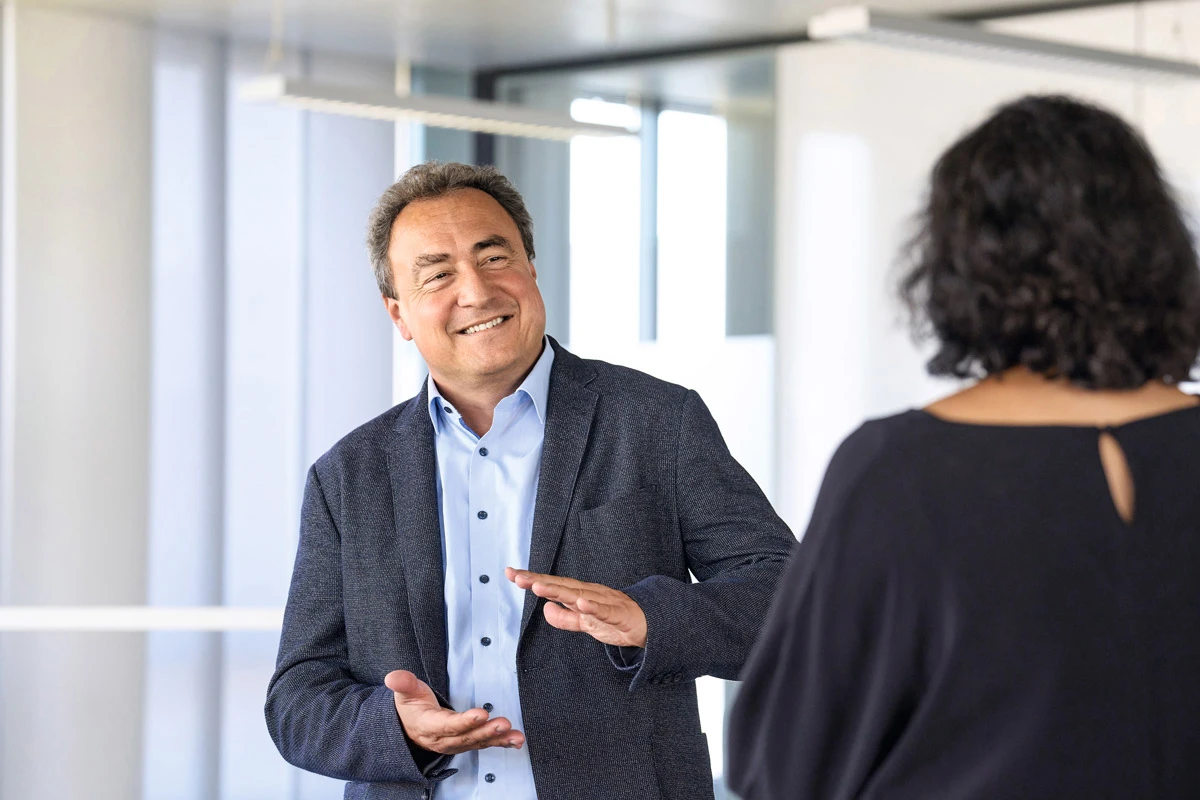
„Um die Entwicklung zu beschleunigen und die hinsichtlich Technik und Wirtschaftlichkeit optimalen Ergebnisse zu erzielen, ist der Einsatz von Simulationsverfahren essenziell. Insbesondere bei Entwicklung und Beurteilung der Werkstoffqualität sowie bei der Gestaltung der Herstellverfahren hat die MTU damit bereits sehr gute Erfahrungen gemacht.“
Senior Consultant Materials bei der MTU
AEROREPORT: Was wären das für Werkstoffe?
Inga Stoll: Ich denke hier etwa an spezielle Polymere, Schichten und Funktionswerkstoffe, zum Beispiel mit elektrisch-magnetischen Eigenschaften oder als Sensoren. Sie sind ebenso wie die neue Atmosphäre, die im Triebwerk herrscht, alles andere als Standard für uns. Es geht dann auch um die erforderlichen Qualifizierungen dieser Materialien und auch hier um eine stabil-wirtschaftliche Herstell- und Reparierbarkeit. Gerade für neue Werkstoffe und Beschichtungen müssen die Sicherheitsnachweise bis ins kleinste Detail erbracht werden.
AEROREPORT: Die luftfahrtspezifischen Anforderungen sind ja sehr hoch.
Jörg Eßlinger: Genau. Die Qualifizierung neuer Materialien und ihrer Funktionen für die kommerzielle Fluganwendung sind sehr anspruchsvoll. Faktoren, wie hohe mechanische Belastungen, lange Haltbarkeit und Schadenstoleranz, spielen eine Rolle. Unterschiedliche Kunststoffe, Verbundwerkstoffe, Metalle, Magnete, Katalysatoren, Folien sowie Beschichtungen, mit denen wir arbeiten werden, sind in der jeweiligen Funktion teilweise neu für die Anwendung in Flugtriebwerken. Außerdem müssen wir die neuen Werkstoffe testen, zum Beispiel wie sie in einer feuchten, auch aggressiven Atmosphäre funktionieren. Solche Testmöglichkeiten bauen wir auf. Mit dem neuen MTU-Bauteiltestzentrum sind wir bereits hervorragend aufgestellt und unsere Partner aus Forschung und Dienstleistung unterstützen nach Kräften. Es gibt viel zu tun.
Inga Stoll: Umso wertvoller ist, dass wir auf ein starkes Netzwerk bauen können. Unsere Kooperationen mit Hochschulen, Forschungsinstituten und Herstellern sind wichtig, um Know-how, Investitionen und Risiko zu teilen. Vor allem in der Entwicklung setzen wir auf Partner, die aktiv an neuartigen Werkstoffen und eigenen Herstellverfahren arbeiten. Der Einsatz von Faserverbundwerkstoffen hat uns beispielsweise schon zu Zulieferern aus Branchen wie der Textilindustrie geführt, mit denen die MTU bislang wenig vernetzt war. Wichtig für uns ist die anwendungsnahe Entwicklung. Wenn die MTU in zehn Jahren einen neuartigen Werkstoff einsetzen will, müssen die Forschungsaktivitäten konsequent an den Bedarfen des Endproduktes ausgerichtet sein.
Jörg Eßlinger: Dabei gilt es keine Zeit zu verlieren. Um die Entwicklung zu beschleunigen und die hinsichtlich Technik und Wirtschaftlichkeit optimalen Ergebnisse zu erzielen, ist der Einsatz von Simulationsverfahren essenziell. Insbesondere bei Entwicklung und Beurteilung der Werkstoffqualität sowie bei der Gestaltung der Herstellverfahren hat die MTU damit bereits sehr gute Erfahrungen gemacht. Schlüssel sind hier die Vernetzung von mehreren, in verschiedenen Größenskalen wirkenden Simulationen sowie der Mut zur Anwendung neuartiger Methoden. Aber auch bei den Qualitätsbewertungen in der Serie kommen zukünftig zunehmend digitale Verfahren zum Einsatz.
AEROREPORT: Welche sind das?
Jörg Eßlinger: Ein Beispiel ist die MTU-Deep-Learning-Software ‚Neuronal Analysis Tool to evaluate rapid‘, kurz Natter. Sie klassifiziert mit Hilfe künstlicher Intelligenz in bisher nicht bekannter Schnelligkeit Mikroskopaufnahmen von Metallen. Das erspart tagelange Bildbearbeitung am PC. Für die Digitalisierung der Werkstofftechnik braucht es Spezialist:innen, die über interdisziplinäre Fähigkeiten in den Bereichen Werkstoffe und Informatik verfügen. Wir sind froh, dass wir unsere Teams verstärken konnten und ausgezeichnete Expert:innen an Bord geholt haben.