aviation
A400M-Antrieb: MTU-Millimeterarbeit in fünf Metern Höhe
Covid19-Krankentransporte, Hilfslieferungen für Krisengebiete oder die Kabuler Luftbrücke. Wie der Airbus A400M seine Rolle als Multifunktionstransporter ausspielt – und was die MTU zum Einsatz dessen Triebwerke beiträgt.
Autor: Thorsten Rienth | 3 Min. Lesezeit veröffentlicht am: 08.12.2021
Autor:
Thorsten Rienth
schreibt als freier Journalist für den AEROREPORT. Seine technikjournalistischen Schwerpunkte liegen neben der Luft- und Raumfahrtbranche im Bahnverkehr und dem Transportwesen.
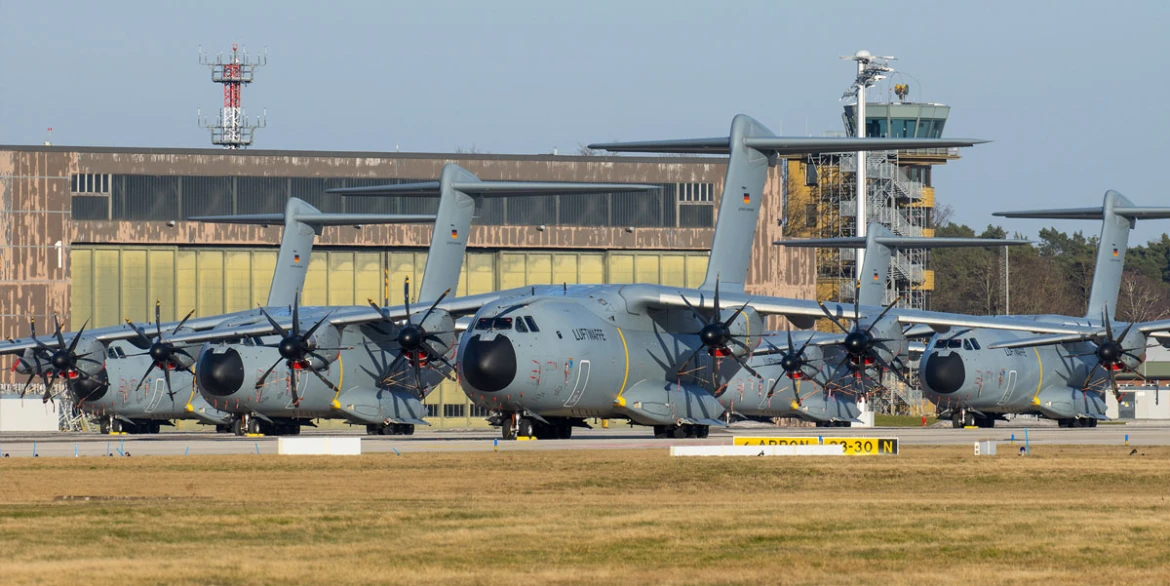
©Lars Hentschel
Gerade einmal wenige Millimeter ist die Öffnung breit. Stefan Zager schiebt das Boroskop hindurch, dreißig, vierzig, fünfzig Zentimeter hinein ins Triebwerk. An der Spitze des Geräts sitzen nebeneinander eine kleine Leuchte und eine kleine Kamera. Rechts neben sich auf der Leiter, gut und gerne fünf Meter über dem Hallenboden, sieht Zager hochaufgelöst auf dem Tablet, was die Kamera im Triebwerksinneren sieht: Kleine Metallkomponenten in Zahnradform und Oberflächen in unterschiedlichen Schattierungen.
Zager ist Customer Service Representative für das TP400-D6-Triebwerk des Airbus A400M. Dafür hat ihn die MTU Aero Engines nach Wunstorf entsandt. Auf dem Militärflugplatz nicht weit von Hannover hat die Bundeswehr ihr Lufttransportgeschwader 62 stationiert. Zager, seit 25 Jahren bei der MTU, sorgt mit seinem Kollegen Steffen Eckert direkt vor Ort dafür, dass die A400M-Antriebe rund laufen. Und dazu gehört eben auch der On-Wing-Check mit dem Boroskop.
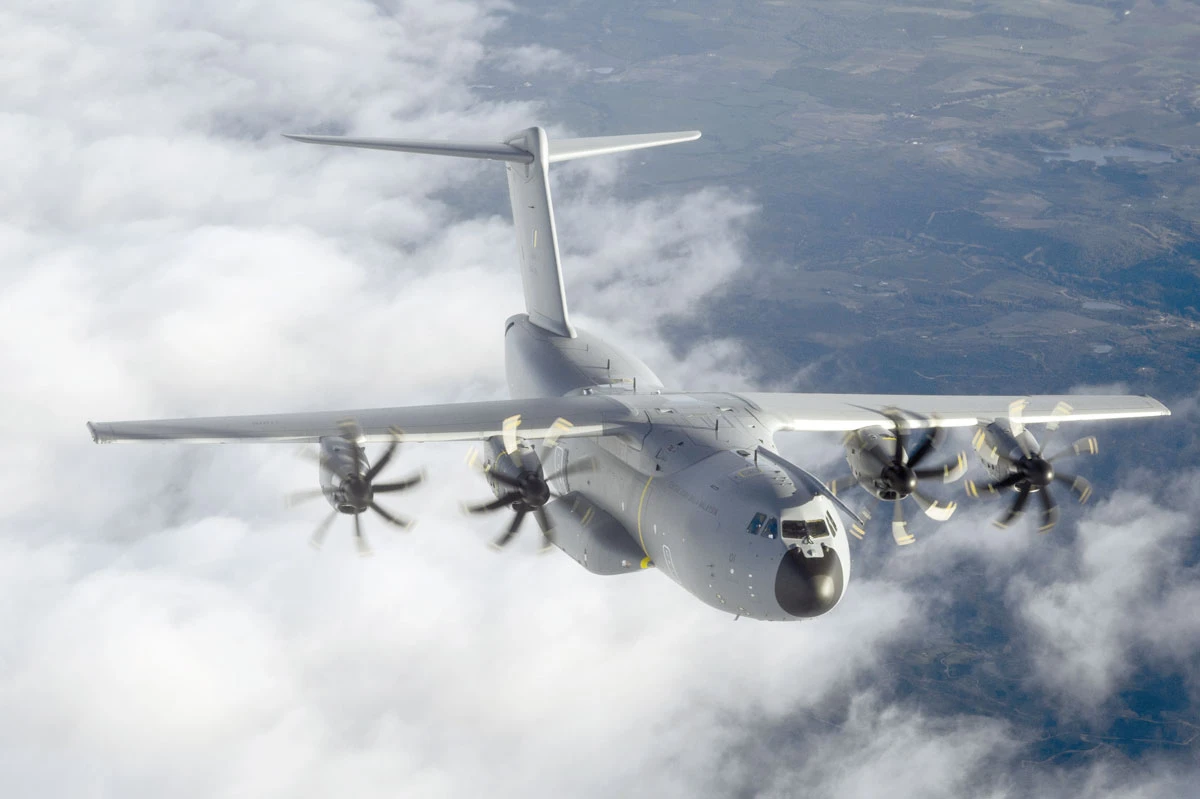
4.000 Kilometer mit 25 Tonnen Nutzlast – und noch genug Kerosin für den Weiterflug
„Das Flugzeug ist für ein extrem breites Einsatzspektrum gemacht“, sagt Roberto Ungericht, der Programmleiter des TP400-D6-Triebwerks bei der MTU. „Die A400M ist das erste multifunktionale militärische Transportflugzeug, das den Namen auch wirklich verdient.“ So zeigte es seine Vielfältigkeit bei weltweiten Einsätzen, etwa in den Krisengebieten im Nahen Osten und in Nordafrika. Oder bei den Krankentransporten innerhalb Europas zu Beginn der Covid 19-Pandemie. Oder bei der Luftbrücke nach Kabul im Sommer 2021.
Einer Art Baukasten gleich lässt sich der Flieger innerhalb von nur Tagen auf spezifische Einsatzszenarien hin umrüsten. Vom Truppentransporter zum Tankflugzeug mit zwei zusätzlichen 7.200-Liter-Tanks im Bauch. Das System ist zur Betankung im Flug von langsam fliegenden Hubschraubern ebenso ausgelegt wie für schnelle Kampfjets. Oder vom „MedEvac“, der fliegenden Intensivstation, zum taktischen Transporter, der 25 Tonnen Nutzlast über 4.000 Kilometer auf eine 750-Meter Sandpiste transportiert – und trotzdem noch Sprit für einen 930-Kilometer-Weiterflug an Bord hat.
Kniff mit dem Zahnrad
10.680 Wellen-PS leistet jedes der vier dreiwellig konstruierten Triebwerke auf Meereshöhe. Damit ist das TP400-D6 das stärkste je in der westlichen Welt gebaute Turboprop-Triebwerk. Nur die Kusnezow NK-12-Triebwerke, unter anderem für die Tupolew Tu-114 aus der ehemaligen Sowjetunion im Einsatz, überbieten es. Der Durchmesser des TP400-D6-Propellers beträgt außerdem stattliche 5,33 Meter.
Für die „TP“, wie die Mechaniker den Antrieb liebevoll nennen, haben sich die MTU, ITP Aero, Rolls-Royce und Safran Aircraft Engines im Konsortium Europrop International (EPI) zusammengeschlossen. Die MTU ist beim TP400-D6 für den Mitteldruckverdichter, die Mitteldruckturbine und -welle verantwortlich sowie an der Triebwerksregelung beteiligt. Dazu kommt die Endmontage aller Serientriebwerke am Standort in München und die Betreuung der an den A400M der Bundeswehr montierten „TPs“. Bei der MTU Maintenance Berlin-Brandenburg steht dafür der weltweit einzige Serienprüfstand für die A400M-Triebwerke. Gleichzeitig handelt es sich dabei um Westeuropas größten Serienprüfstand für Propellertriebwerke. Jedes Triebwerk, das nach seiner Instandsetzung wieder abhebt, hat also vorher eine Schleife durch die Testzelle in Ludwigsfelde südlich von Berlin gedreht. Nach etwa 3.000 bis 3.500 Flugstunden werden die ersten geplanten Shop-Visits anstehen.
Eine Besonderheit der Antriebe: An jedem Flügel dreht ein Triebwerk links-, das andere rechts herum. Die zwei linksdrehenden Propellergetriebe sind mit einem zusätzlichen Zahnrad ausgestattet, um die Drehrichtung auf der Propellerausgangsseite zu ändern. Der Kniff mit der gegenläufigen Ausrichtung sorgt für einen gleichmäßigen Auftrieb an beiden Flügeln und vermeidet damit verfrühte Strömungsabrisse.
Minimalinvasive Kontrolle für effizienten Flugbetrieb
Mit den Flügeln – oder besser: der Aufhängung der Triebwerke daran – hat auch Zagers Einsatz auf der Leiter zu tun. Die Triebwerke von den Flügeln ab- und wieder an zu montieren, brauche schnell eine ganze Woche. „Alles Zeit, in der das Flugzeug nicht einsatzfähig im Hangar steht.“ Der Weg durchs Millimeter-Boroskopauge öffnet eine minimalinvasive Abkürzung. Ob geplanter Maintenance-Einsatz oder ungeplanter Ad-hoc-Check, weil die Flugbesatzung Ungewöhnliches feststellte, spielt dabei keine Rolle. „Entweder, wir können früh Entwarnung geben“, sagt Zager. „Oder es lohnt sich, das Triebwerk wirklich vom Flügel zu nehmen.“ Zagers prüfender Blick durch das Boroskopauge ist daher essentiell um einen effizienten Flugbetrieb gewährleisten zu können.
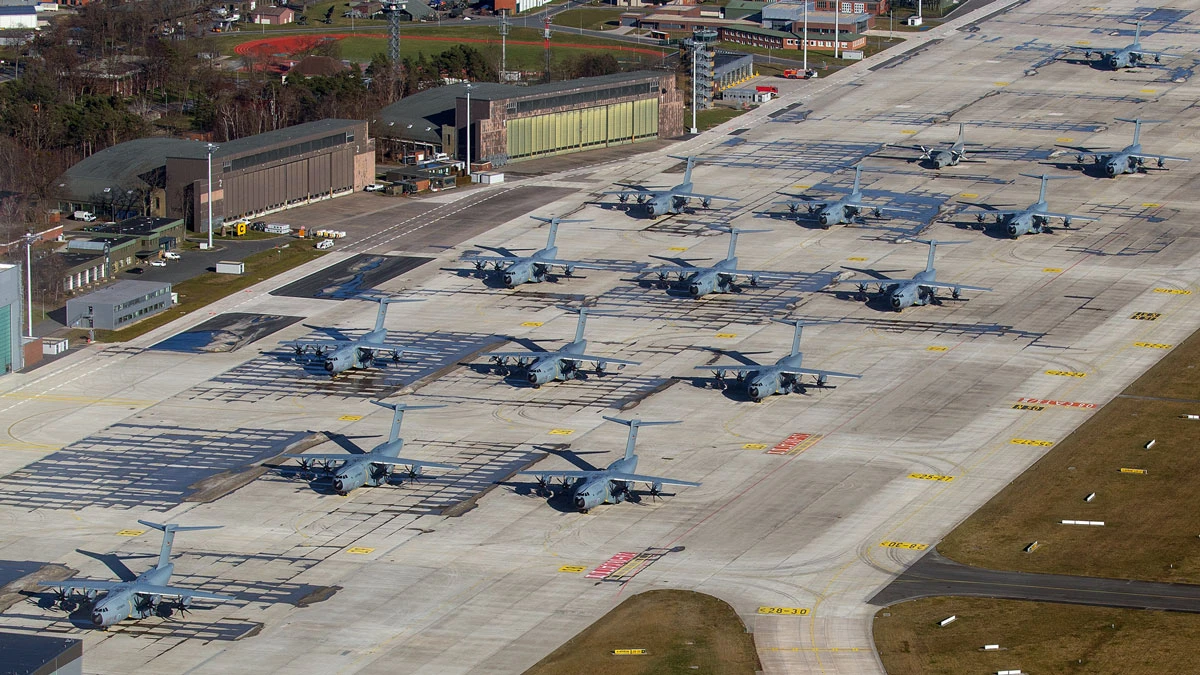
©Lars Hentschel
Lufttransportgeschwader 62: Alle Airbus A400M der Luftwaffe sind bisher am Standort Wunstorf beim Lufttransportgeschwader 62 stationiert.