aviation
A400M engine: MTU’s millimeter precision, five meters off the ground
COVID-19 patient transports, relief supplies for crisis areas, the Kabul air bridge: How the Airbus A400M performs as a multirole transporter—and what MTU does to keep its engines in service.
3 mins reading time published on: 08.12.2021
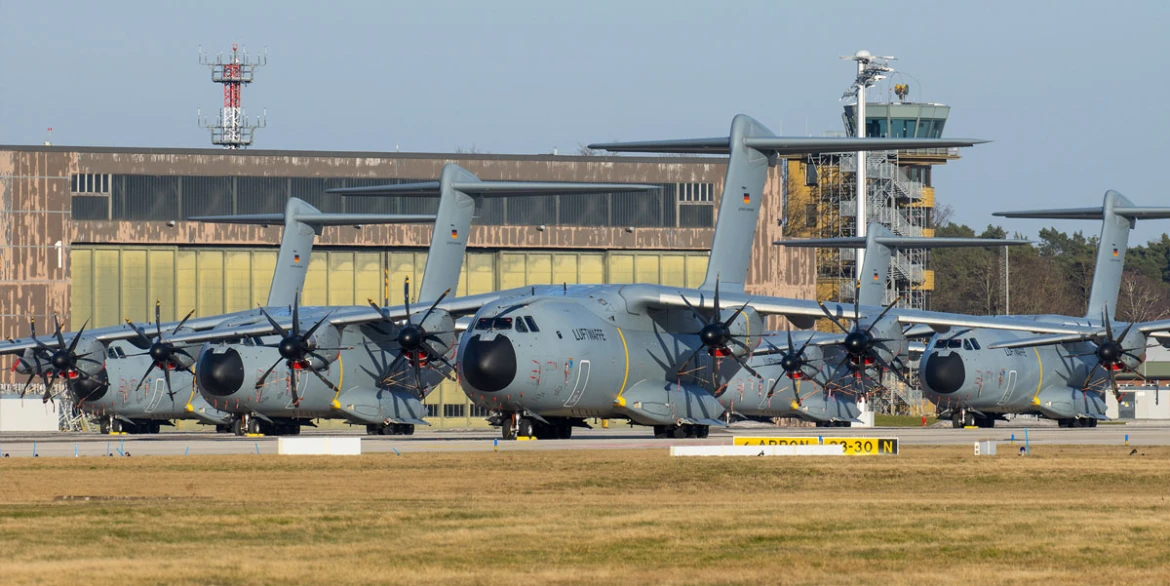
©Lars Hentschel
Through an opening just a few millimeters wide, Stefan Zager feeds the borescope thirty, forty, fifty centimeters into the engine. Next to each other at the end of the device are a tiny light and a small camera. Zager is up a ladder, a good five meters above the hangar floor. To his right is a tablet showing high-resolution images of what the camera is seeing inside the engine: small metal components shaped like gearwheels and surfaces in different tonal gradients.
Zager is a Customer Service Representative for the TP400-D6 engines that power the Airbus A400M, which explains why MTU Aero Engines dispatched him to Wunstorf. Not far from Hannover, this military air base is home to Air Transport Wing 62 of the German Air Force. Zager, who has worked at MTU for 25 years, and his colleague Steffen Eckert are on-site to ensure the A400M’s engines run smoothly. This involves the on-wing check with the borescope.
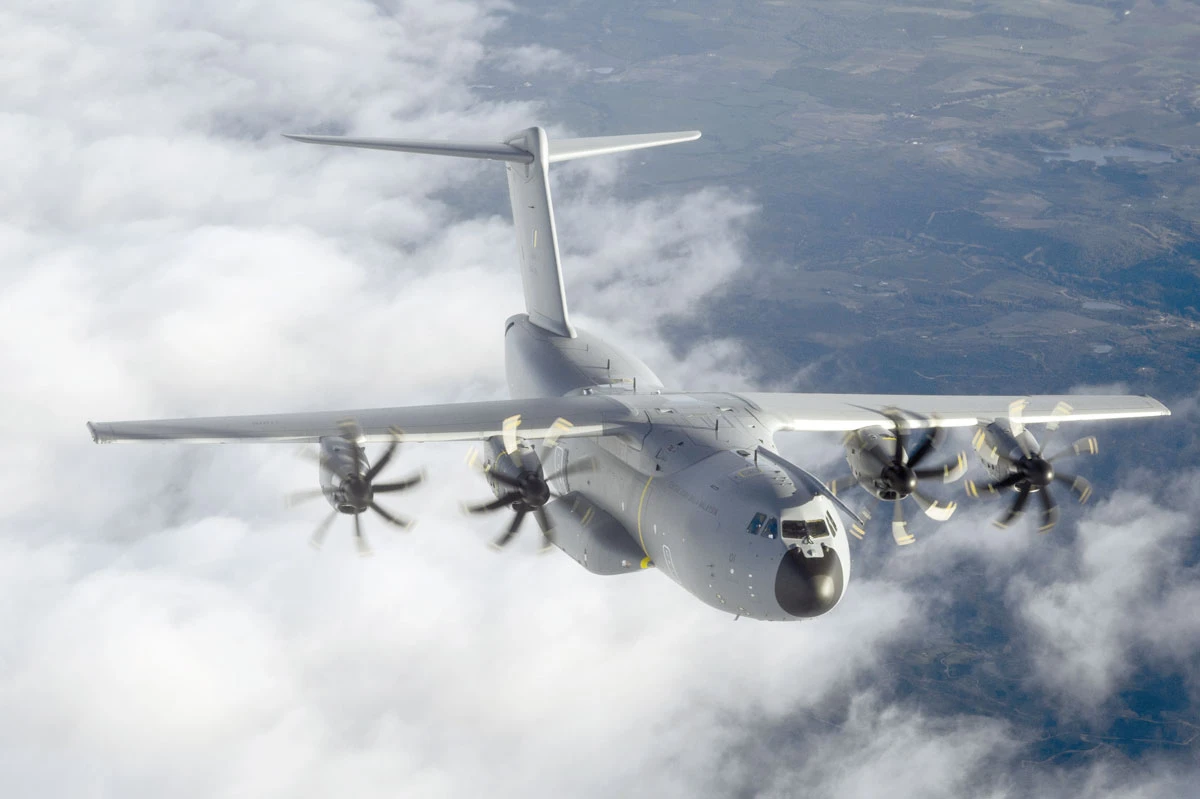
4,000 kilometers carrying a 25 metric tons – and still enough kerosene to keep flying
“This aircraft is designed to handle a vast array of missions,” says Roberto Ungericht, Program Director for the TP400-D6 engine at MTU. “The A400M is the first multirole military transporter truly worthy of the name.” It has already demonstrated its versatility on missions all over the world, for instance in crisis areas in the Middle East and North Africa, transporting patients in Europe at the beginning of the COVID-19 pandemic, and as part of the air bridge to Kabul in summer 2021.
What could be described as a toolbox allows the aircraft to be modified for specific mission scenarios within just a few days. For instance, it might be converted from a troop transporter to a refueler, complete with two additional 7,200-liter tanks in its belly. Its system is designed for the aerial refueling of everything from slow-moving helicopters to high-speed fighter jets. The A400M might also be converted from a medevac—a flying intensive care unit—into a tactical transporter capable of moving a 25-metric ton payload over 4,000 kilometers to a 750-meter dirt runway and still have enough fuel to travel another 930 kilometers.
The trick with the gearwheel
At sea level, each of the four three-shaft engines delivers 10,680 shaft horsepower. That makes the TP400-D6 the most powerful turboprop engine ever built in the Western world. Only the Kuznetsov NK-12 engines, which powered aircraft like the Tupolev Tu-114 made in the former Soviet Union, surpass it. The diameter of the TP400-D6 propeller is also an impressive 5.33 meters.
“TP,” as it is affectionately referred to by the mechanics who work on it, was developed by MTU, ITP Aero, Rolls-Royce and Safran Aircraft Engines as part of the Europrop International (EPI) consortium. MTU is involved in the TP’s medium-pressure compressor, medium-pressure turbine and shaft, and the engine control unit. In addition, MTU handles final assembly of all volume production engines at its Munich location and looks after the TPs mounted on the A400M aircraft operated by the German Air Force. MTU Maintenance Berlin-Brandenburg is home to the world’s only production test stand for A400M engines, which also happens to be the largest production test stand for propeller engines in Western Europe. In other words, every engine that takes to the skies after maintenance has been through the test cell at the Ludwigsfelde site south of Berlin. The first shop visits are scheduled for when the engine has completed between 3,000 and 3,500 flight hours.
A special feature of the TP is that on each wing, one engine rotates clockwise and the other counterclockwise. The two counterclockwise-rotating propeller engines are equipped with an extra gearwheel that changes the direction the propeller rotates. The counterrotation trick ensures equal lift on both wings and thus avoids premature stalling.
Minimally invasive control for efficient flight operations
The job Zager is doing up the ladder also has to do with the wings, or rather with the mounting of engines on them. Demounting and remounting the engines can easily take a week to complete. “All that time, the aircraft remains out of service in the hangar,” Zager says. The millimeter-wide borescope boss provides a minimally invasive shortcut, one that can be taken for scheduled maintenance as well as for ad hoc checks performed because the flight crew noticed something unusual. “This allows us to give the all-clear right away,” Zager says, “or to say that it’s worth taking the engine off the wing.” In this way, Zager’s critical glance through the borescope boss is essential in ensuring efficient flight operations.
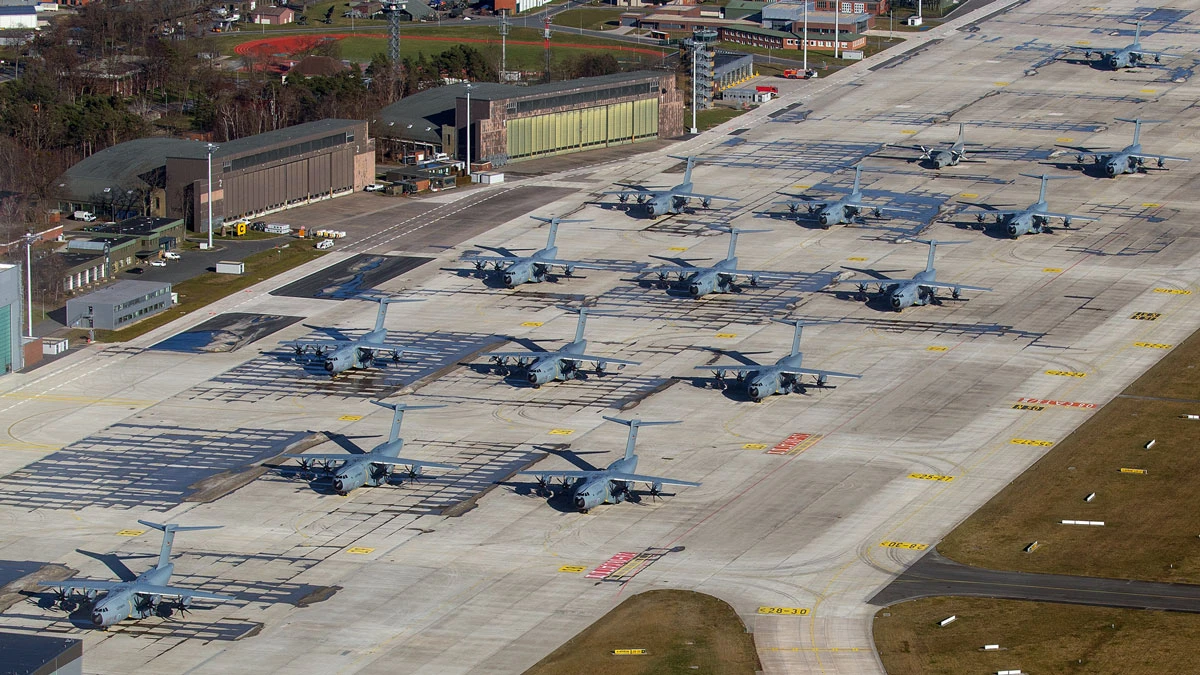
©Lars Hentschel
Air Transport Wing 62: All the Airbus A400Ms of the German Air Force have been stationed at the Wunstorf location with Air Transport Wing 62.