innovation
Vollautomatisierter Maskierungsprozess für die MTU-Fertigung
Wie die MTU mit einem Elastomer ihre Oberflächenbearbeitung revolutioniert.
Autor: Thorsten Rienth | 5 Min. Lesezeit veröffentlicht am: 11.01.2022
Autor:
Thorsten Rienth
schreibt als freier Journalist für den AEROREPORT. Seine technikjournalistischen Schwerpunkte liegen neben der Luft- und Raumfahrtbranche im Bahnverkehr und dem Transportwesen.
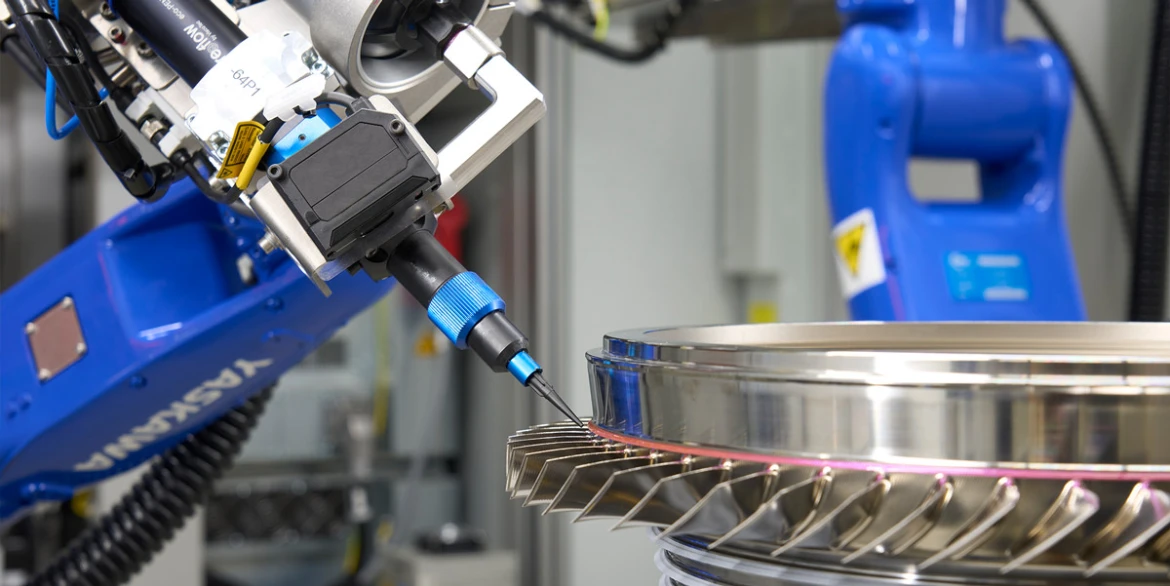
Wenn Thomas Kaltenecker, Fertigungsplaner bei der MTU Aero Engines, Sinn und Zweck der futuristischen Dispenser erklären will, legt er zwei Fotos nebeneinander. Das linke Bild zeigt einen großen Lagerraum. Darin hängen in mehreren Etagen Silikonringe in dutzenden Farben, Formen und Größen über-, unter-, nebeneinander. Im rechten Bild liegen ein paar Kartuschen gefüllt mit einem gelförmigen Elastomer auf einem Tisch. „Unterm Strich erfüllt beides die gleiche Aufgabe“, erklärt Kaltenecker. „Stellen von Triebwerksbauteilen mit Maskierungsmaterial abzudecken, während andere, besonders beanspruchte Bereiche etwa mit einer thermischen Spritzschicht versehen werden. Die Maskierung sorgt dafür, dass die Spritzschicht nicht auf Stellen gerät, die davon freibleiben sollen.“
Die Klebebänder, Silikonringe, Masken oder Metallabdeckungen kleben, ziehen, stülpen und klemmen Kalteneckers Kolleg:innen in Millimeterbruchteilarbeit manuell an diese Stellen. Das Elastomer hingegen tragen die Dispenser vollautomatisch auf die jeweiligen Stellen am Bauteil auf. Die UV-Lampe des Maskier-Vollautomaten härtet das Material in Sekunden. Nachdem die Maskierung den jeweiligen Fertigungsprozess durchlaufen hat, wie etwa das Thermische Beschichten, Kugelstrahlen oder die Galvanik, lässt es sich rückstandsfrei vom Bauteil abziehen.
Kürzere Durchlaufzeiten, verbesserte Qualität und gesenkte Kosten
SpeedMask® von der DYMAX GmbH lautet der Markenname und der Hersteller des dickflüssigen Gels, deren UV-härtende Klebstoffe primär im Bereich der Medizintechnik verwendet werden. Durch Zufall hört Kaltenecker davon. „Sowas müsste uns doch beim Beschichten echt weiterbringen“, habe er gedacht.
Schritt für Schritt beginnt Kaltenecker sich an SpeedMask® zu versuchen. Kaltenecker erprobt Materialmischungen und, noch manuell, Maskiervorgänge. Die ersten Tests laufen vielversprechend. Die Tage, in denen Kaltenecker nicht mehr nur die Produktion plant, sondern auch ein neues Maskierverfahren entwickelt, werden mehr. Parallel laufen Studienarbeiten zum Elastomer-3D-Druck auf Triebwerksteilen. Sie attestieren der Idee technische Machbarkeit und breite Einsatzmöglichkeiten in der MTU-Produktion. Kürzere Durchlaufzeiten, verbesserte Qualität und gesenkte Kosten bringen einen erstklassigen Mehrwert.
Seit gut drei Jahren dreht sich schließlich das Allermeiste in Kalteneckers Arbeitsalltag um SpeedMask® – und, wie er das so erzählt, dreht sich hinter ihm in der Roboterzelle eine Blisk. Die Optik der Maschine hat erkannt, dass es sich um die vierte Stufe eines bestimmten Hochdruckverdichters handelt. Die Steuerung lädt das entsprechende Programm, setzt den richtigen Dispenser auf und fährt ihn in Position. Während der Drehtisch das Bauteil in Rotation versetzt, schwenkt, hebt und senkt, fördert die Dispensereinheit kontinuierlich das Elastomer aus der Kartusche. Hochpräzise wird Material exakt entlang von Kanten aufgetragen, wie es etwa beim Maskieren auf dünnen Blisk-Schaufelspitzen von Nöten ist. Aber auch Bohrungen können aufgefüllt oder Bereiche großflächig maskiert werden. Den Einsatzmöglichkeiten und Variationen sind dank dem Verfahren und dem Vollautomaten kaum Grenzen gesetzt. „Die genaue Form der jeweiligen Abdeckung definieren die jeweiligen Verfahrensparameter, wie etwa die Art des Dispenseraufsatzes, die Entfernung und Winkel des Dispensers zum Bauteil und die Durchflussmenge“, erklärt Kaltenecker. Dann summt das UV-Licht vorbei und härtet das Elastomer aus.
Schließlich kommt ein weiteres Mal die Maschinenoptik ins Spiel: „Sie erkennt zum Beispiel, ob unerwünschte kleine Luftbläschen oder Fehlstellen in der Maskierung sind.“ Die Qualitätskontrolle ist also inklusive – und zahlt nebenbei auf die Nachhaltigkeit ein: „Bislang weisen wir jedes Jahr rund 14.000 Silikonringe noch im Wareneingang aufgrund von Abweichungen zurück. Die landen dann in der Entsorgung.“
Beinahe auf Null-Toleranz maskierte Bearbeitungsbereiche
Im vergangenen Sommer wurde eine wohl weltweit einmalige Prototypenanlage angeliefert, mit der nun das innovative Material zum Maskieren von Turbinenbauteilen vollautomatisiert und effektiv genutzt werden kann. Sie durchlief zunächst die Erprobung, dann wurde die Industrialisierung angestoßen, sprich: Die Maskier- und Aushärteprogramme der ersten Bauteile eingerichtet. So liest sich der noch kurze Auszug aus dem bisherigen Lebenslauf der Maschine, der eigentlich doch ein verhältnismäßig langer ist: „Der Prototyp war sicherlich eines unserer bislang anspruchsvollsten Projekte“, erklärt Pascal Malischek, Mechatronik- und Robotikingenieur beim österreichischen Hersteller Robooptic Systems. „Die gesamte Maschinensteuerung ist in einer Art Modulbauweise mit freien Parametern aufgebaut, damit die MTU die Maskierprogramme selbständig anpassen kann.“
Die Programmierfähigkeit ist aus MTU-Perspektive entscheidend. Mehrere hundert Bauteile aus dem Portfolio durchlaufen während ihrer Produktion oftmals verschiedene Stationen in der Beschichterei. Bisweilen ändern sich im Zuge von Designverbesserungen Bauteilgeometrien. „Da müssen wir einfach schnell und unkompliziert die jeweiligen SpeedMask®-Maskierprogramme anpassen können“, sagt Kaltenecker.
Der Fertigungsplaner verweist auf den Effizienzaspekt hinter der neuen Anlage, im OEM- wie MRO-Geschäft: „Die abzuklebenden Zonen sind mittlerweile derart filigran, dass das händisch nur noch mit enormer Konzentration und Zeit machbar ist.“ Was von Hand bisweilen eine gefühlte Ewigkeit dauere, erledige der SpeedMask®-Roboter in einem Bruchteil davon. „Gerade jetzt mit dem starken Produktionsanstieg der neuen Programme ist das für die Kolleg:innen eine echte Erleichterung.“ Zudem ist das Material mechanisch bearbeitbar. Dadurch lassen sich Bearbeitungsbereiche beinahe auf Null-Toleranz maskieren und auch nahezu beliebige Konturen erzeugen.
Der innovative Maskierprozess hat noch weitere Vorteile: So wird in einigen Fällen die Maskierung nur ein einziges Mal aufgetragen und gleich für mehrere Fertigungsschritte hintereinander eingesetzt. Dies spart ebenfalls erheblich Zeit und Kosten ein. Und im MRO-Sektor könnte die Maschine helfen, maßgeschneiderte Maskierungen für die Reparatur abgenutzter Triebwerksteile zu erstellen.
Das neue Maskierungsverfahren erschließt neue Potenziale in der Triebwerksentwicklung
Schließlich ist da noch ein Aspekt, der sich ganz generell auf die Effizienz von Triebwerken auswirken dürfte. „Es gibt Stellen im Triebwerk, die die Entwickler gerne verbessern würden“, erklärt Kaltenecker. „So manch pfiffiger Gedanke lässt sich aber nicht umsetzen, weil wir die Maskierungen mit den bisherigen Klebebändern, Silikonringen, Masken oder Metallabdeckungen nicht präzise genug hinbekommen.“ Den Einzelfall müsse man natürlich validieren. Aber das passende Verfahren und die passende Maschine, die stünden jetzt zumindest bereit.