aviation
Instandhaltung gestern und heute bei der MTU Maintenance
Demontage, Reparatur, Montage und Prüfstand: In den Shops der MTU Maintenance hat sich im Laufe von 40 Jahren viel verändert. Eine Zeitreise zurück und Ausblicke in die Zukunft.
Autor: Nicole Geffert, Johannes Angerer | 6 Min. Lesezeit veröffentlicht am: 01.10.2019
Autor:
Nicole Geffert arbeitet seit 1999 als freie Journalistin mit den Themen Forschung und Wissenschaft, Geld und Steuern, Ausbildung und Beruf.
Johannes Angerer Partner der Employer Branding Agentur identifire, stärkt Marken, in dem er die prägenden Geschichten dahinter erforscht und in ansprechenden Formen erzählt, ob als Text, als Video oder in einer Ausstellung.
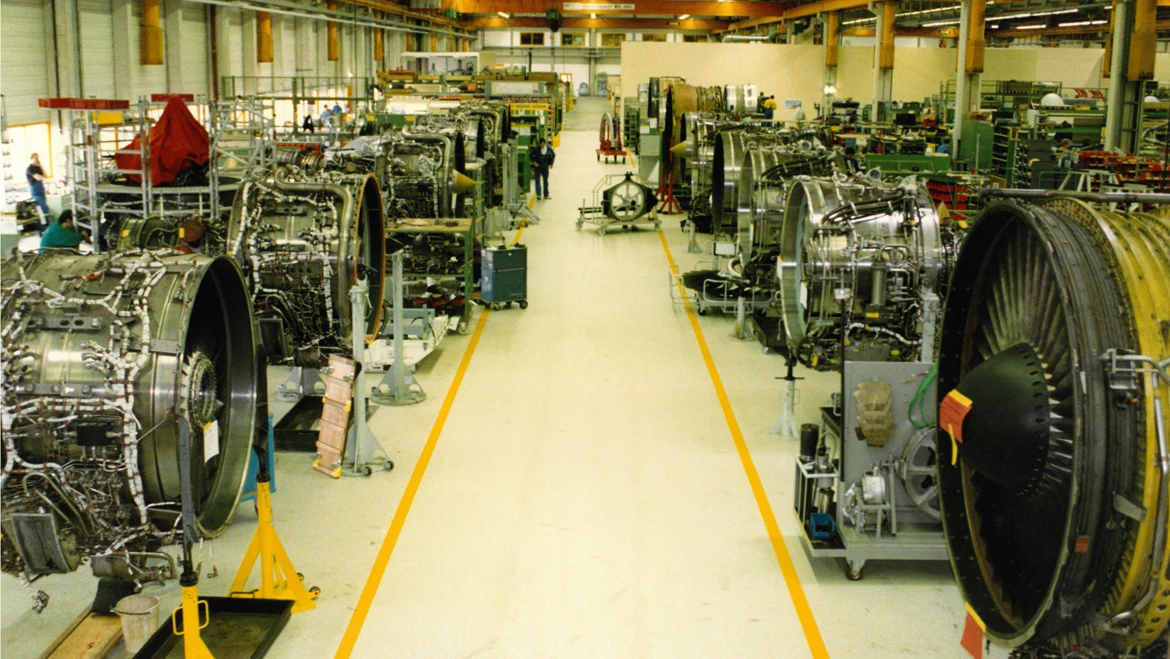
- Vor 40 Jahren wurde die MTU Maintenance gegründet
- Instandhaltung gestern und heute bei der MTU Maintenance
- 40 Jahre
Mit über 18.000 Shop Visits zählt die MTU Maintenance heute zu den Top 5 der weltweiten Dienstleister für die Instandhaltung ziviler Triebwerke. Lässt man die 40 Jahre ihrer Unternehmensgeschichte Revue passieren, entdeckt man neben Innovationen auch Bewährtes. So sind gestern wie heute beispielsweise bei der Demontage einer Niederdruckturbine (NDT) am Anfang eine große Anzahl Schrauben erst zu lösen, dann abzuschrauben.
In den 1980er Jahren kamen dabei Knarre und Ringschlüssel zum Einsatz. Auf dem Schreibtisch an der Station lagen die Arbeitskarte für die anstehenden Schritte und daneben ein Zettel. Dieter Schmotz, seit 1981 Triebwerksmechaniker bei der MTU Maintenance Hannover, erinnert sich: „Die Arbeitsanweisungen wurden Schritt für Schritt erledigt. Nach jedem einzelnen Schritt wurde auf dem Zettel notiert, was gemacht wurde. Abschließend kamen Datum, Unterschrift und der Mitarbeiterstempel hinzu. Dann ging es zurück zum Modul, das Werkzeug wurde in die Hand genommen und weitergemacht.“
Und was hat sich verändert? Erst einmal die Werkzeuge. Zum Beispiel ersetzten Luft- und Akkuschrauber die Knarre. Ein versierter Mechaniker konnte damit die NDT in der Hälfte der Zeit auseinanderbauen. Verschwunden sind zudem Papier und Schreibarbeit – fast. Denn von Hand datieren, unterschreiben, abstempeln – auch diese Abläufe tragen heute noch zur hohen Qualität und Zuverlässigkeit in den Shops der MTU Maintenance bei.
Doch die meisten Prozesse wurden im Laufe der Zeit angepasst und kontinuierlich verbessert. Ein Top-Instandhalter ruht eben nicht. Längst hat die Digitalisierung in den Shops der MTU Maintenance unter dem Motto „MRO 4.0“ Einzug gehalten und wird gelebt.
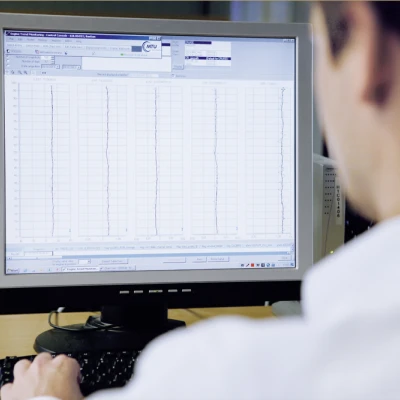
Unter Beobachtung: Das Engine Trend Monitoring der MTU Maintenance ermöglicht eine umfassende Überwachung der Triebwerksparameter.
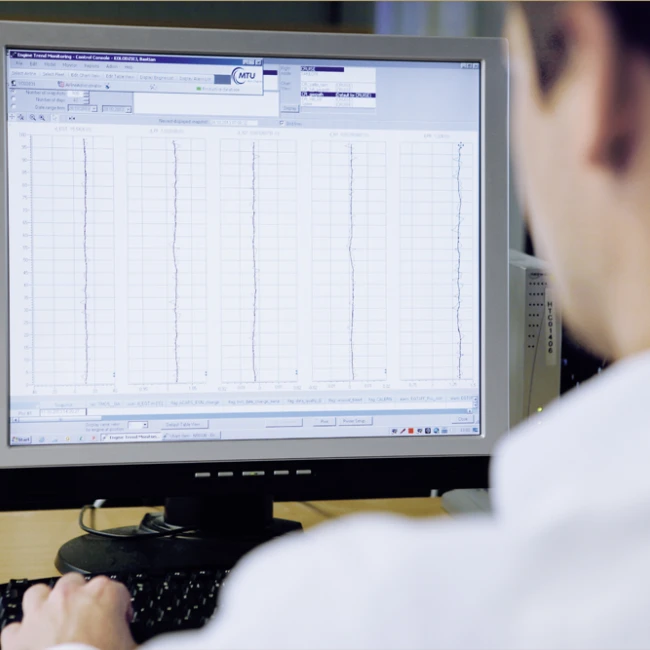
Unter Beobachtung: Das Engine Trend Monitoring der MTU Maintenance ermöglicht eine umfassende Überwachung der Triebwerksparameter.
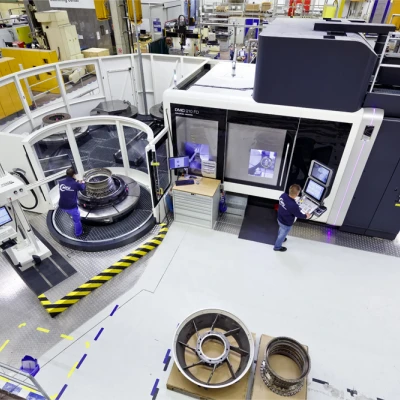
Spezialist für Reparaturen: Mit ihren Verfahren erzielt die MTU Maintenance weltweit einzigartige Reparaturtiefen und lange Triebwerkslaufzeiten am Flügel.
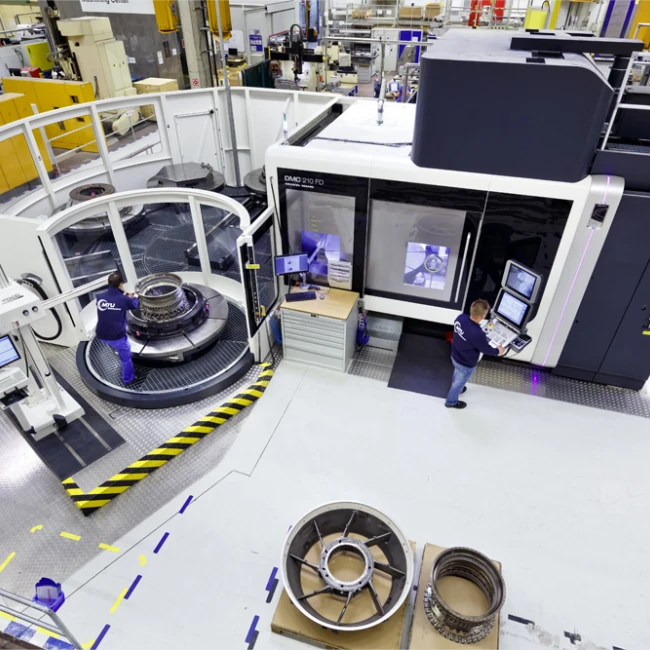
Spezialist für Reparaturen: Mit ihren Verfahren erzielt die MTU Maintenance weltweit einzigartige Reparaturtiefen und lange Triebwerkslaufzeiten am Flügel.
Computergestützt lassen sich technische Probleme an Triebwerken heute erkennen, lange bevor sie den Flugbetrieb stören oder aufwändige Reparaturen nach sich ziehen. Das Engine Trend Monitoring der MTU Maintenance ermöglicht eine umfassende Überwachung der Triebwerksparameter durch eine MTU-eigenentwickelte Monitoring-Software. Und ein Blick in die Zukunft zeigt, dass Advanced Analytics und maschinelle Lernverfahren künftig eine automatisierte Analyse großer Datenmengen ermöglichen werden. Damit lassen sich genaue Vorhersagen über den Zustand der Triebwerke am Flügel treffen. Triebwerksinstandhaltungen können so bis hin zu den Modulen immer besser geplant und die Kosten für die Airlines verringert werden.
Oberste Prämisse der MTU Maintenance ist stets, die Instandhaltungskosten von Triebwerken sowie deren Ausfallzeiten zu minimieren. Das gilt für jeden Shop Visit – sei es, dass das Triebwerk zur Herstellung seiner vollständigen Leistung (Performance Restorations) in den Shop kommt oder aber Bauteile mit begrenzter Lebensdauer (Life Limited Parts) ausgetauscht oder Triebwerksteile repariert werden müssen.
Die Reparaturbereiche in den Shops kann man nicht verfehlen. Denn wo Metall bearbeitet wird, spielt das große Geräuschorchester. „Früher war das noch deutlich lauter“, sagt Rudolf Glembozky. Der gelernte Werkzeugmacher arbeitet seit 1982 in der Instandsetzung der MTU Maintenance Hannover. Er berichtet am Beispiel eines Turbine Mid Frame (TMF)-Liners, eines runden Blechteils mit einem Durchmesser von etwa 150 Zentimetern, wie dessen Reparatur früher ablief.
Ein Kollege aus der vorigen Abteilung brachte das zu reparierende Teil und stellte es zu den anderen im Wartebereich. Was besonders eilig war, bekam einen roten Aufkleber. Eine typische Reparatur war das Wechseln der vier Verbindungsflanschen: alte abstechen, neue aufschweißen und genau ins Maß bringen. „Doch als erstes mussten wir das Teil auf die Maschine bringen. Vorrichtung gab es keine. Also haben wir den Liner oft zu zweit oder zu dritt mit Muskelkraft auf die Maschine gehoben.“
Tausende von speziellen Vorrichtungen ersetzten mit der Zeit die Muskelkraft. Sehr viele davon haben die Mitarbeiter der MTU Maintenance selbst erfunden. Ob Haltevorrichtung, Schutzplane oder Spezialmessinstrument, vieles davon erleichtert auch heute noch die Arbeit.
Keine Frage, Reparieren ist nach wie vor eine Kernkompetenz der MTU Maintenance. Doch ihre Expertise geht über die reine Instandhaltung inzwischen weit hinaus. Umfassende Serviceleistungen über den kompletten Lebenszyklus eines Triebwerks sind heute das Spezialgebiet der MTU Maintenance weltweit. Das Flottenmanagement ist hierfür ein Beispiel. Die MTU-Experten entwickeln für jedes einzelne Triebwerk einer Flotte passgenaue MRO Lösungen und optimieren so die Verfügbarkeit der Triebwerke für die Airlines.
Oder der Service Triebwerksleasing. In der zeit- und kostensensiblen Luftfahrtbranche nutzen immer mehr Fluggesellschaften die Möglichkeit, Flugzeuge und Triebwerke zu leasen. So wird die Flexibilität erhöht und zusätzliches Kapital freigesetzt, welches sonst in Ersatztriebwerke investiert werden muss. Die MTU Maintenance Lease Services bietet deshalb den Airlines kurz- und mittelfristiges Verleasen von Triebwerken, die SMBC Aero Engine Lease hingegen langfristige Lösungen. Beide Firmen sind Joint Ventures mit der japanischen Sumitomo Corporation.
links: Auf dem Prüfstand der MTU Maintenance Zhuhai wird ein V2500-Triebwerk für Testläufe vorbereitet.
rechts: Kontrollraum eines Prüfstands bei der MTU Maintenance. Nach der Instandsetzung muss jedes Triebwerk auf den Prüfstand.
Zurück in den Shop. Zum Abschluss einer jeden Instandhaltung kommt das Triebwerk auf den Prüfstand. Frank Reimchen, Arbeitsplaner am Prüfstand der MTU Maintenance Hannover, geht auf eine kleine Zeitreise in die 1990er Jahre: Bei einem Prüflauf „fuhren“ damals zwei Mechaniker das Triebwerk. Ein Mitarbeiter vom Engineering und einer von der Qualitätssicherung achteten auf die Messwerte. Die 30 wichtigsten Werte zeigte ein Monitor monochrom grün an.
Über eine klobige Eingabekonsole steuerte ein Teammitglied den Messrechner. Den zeitlichen Verlauf bestimmter Werte zeichnete ein 8-Kanal-Linienschreiber auf. Wollte man andere Werte, musste man Kabel umstöpseln und das Gerät neu eichen. „Unser damaliger Qualitätsingenieur, Hans Holpert, traute dem Messrechner nicht ganz. Er rechnete deshalb oft während eines Laufes die Performance mit dem Taschenrechner nach. Die Formeln hatte er alle im Kopf. Unglaublich.“
Um die Jahrtausendwende wurde ein Prüflauf nur noch zu dritt durchgeführt. Das machte vor allem die rasante Entwicklung der Mess- und Computertechnik möglich. Die Prüftechniker sahen nun auf acht Farbmonitoren alle relevanten Werte auf einen Blick. Den zeitlichen Verlauf speicherte das System viermal pro Sekunde automatisch im „History Buffer“. Das moderne System zeigte die Messwerte nun automatisch im Band der Grenzwerte an.
Und heute? Aktuelle Triebwerke sind Hochleistungscomputer, die sekündlich aus unzähligen Messfühlern viele Megabyte an Daten liefern. Reimchen: „Das RB211 war ganz analog, 1989 kamen das PW2000 und V2500. Diese Triebwerke lieferten pro Sekunde über zwei Datenleitungen je 12,5 Kilobyte. Das moderne PW1100G-JM hat drei Ethernet-Leitungen mit je 100 Megabit pro Sekunde.“
Bereits 2007 investierte die MTU Maintenance Hannover in eine neue Testzelle. Das Großtriebwerk GE90 mit seinen 115.000 Pfund Schub stand dabei im Fokus. Die Testzelle wurde mit Weitsicht gebaut und gleich auf 150.000 Pfund Schub ausgelegt. Auch die MTU Maintenance Zhuhai ist mit ihrer Testkompetenz ganz weit vorn und kann auf ihrem hochmodernen Prüfstand ebenfalls Triebwerke bis zu 150.000 Pfund Schub testen.
Und wie schaut die Zukunft aus? Computersimulationen entwickeln sich rasant, einzelne virtuelle Triebwerkstests sind möglich. Aber die werden in absehbarer Zeit eine Testzelle nicht ersetzen. Deshalb kommt auch bei EME Aero – einem Joint Venture mit Lufthansa Technik, das 2020 an den Start geht – jedes Triebwerk auf den Prüfstand. Im polnischen Aviation Valley nahe des Flughafens von Rzeszów entsteht aktuell eines der größten und fortschrittlichsten MRO-Servicezentren für die Getriebefan‑Triebwerke der P&W GTF-Triebwerksfamilie. Und auch der Prüfstand wird neue Maßstäbe setzen.