innovation
Beschichtungen in Triebwerken: Thermische Verfahren
Mehr als die Hälfte aller Triebwerksbauteile werden thermisch beschichtet. Dutzende verschiedene Werkstoffe stehen hierfür zur Verfügung, die mittels unterschiedlichster Verfahrensvarianten aufgebracht werden.
Autorin: Monika Weiner | 5 Min. Lesezeit veröffentlicht am: 06.11.2023
Autorin:
Monika Weiner
arbeitet seit 1985 als Wissenschaftsjournalistin. Die Diplomgeologin interessiert sich vor allem für neue Entwicklungen in Forschung und Technik sowie deren gesellschaftliche Auswirkungen.
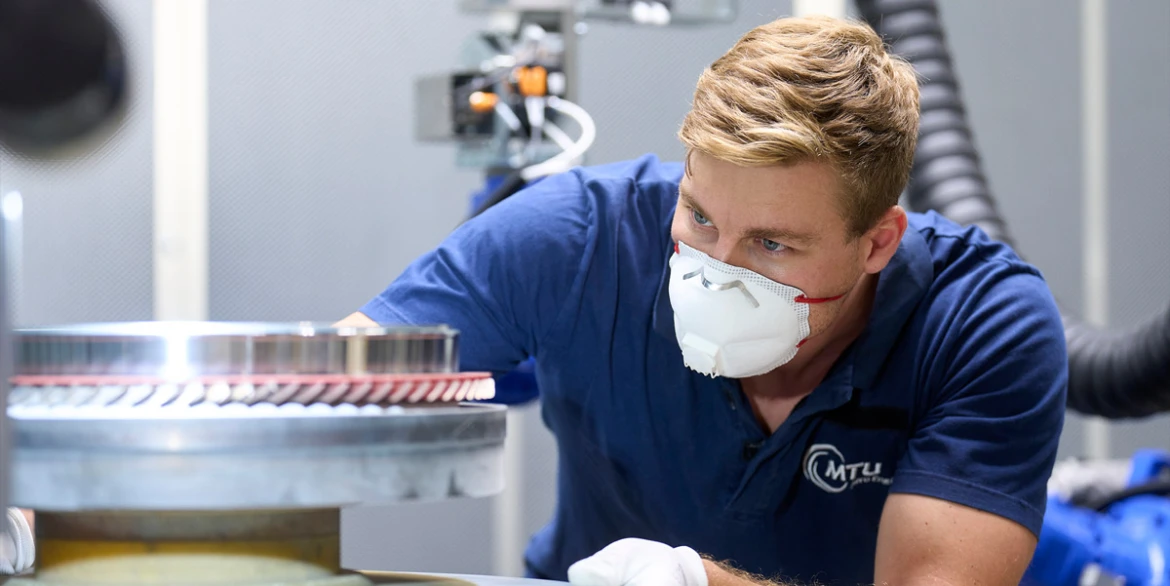
Mehr als 50 Prozent aller Triebwerksbauteile werden mit Beschichtungen veredelt. Allein beim Thermischen Spritzen sind die Variationsmöglichkeiten enorm: So gibt es etwa das Flammspritzen, das Hochgeschwindigkeitsflammspritzen, das Lichtbogendrahtspritzen oder das Plasmaspritzen. Diese können mit unterschiedlichen Brennern und mit verschiedenen Gasen betrieben werden. Als Beschichtungsmaterialien kommen Hart- und Weichmetalle, Legierungen, Keramiken und Verbundwerkstoffe zur Anwendung. „Die Kunst besteht darin, aus einer Vielzahl von Materialien und Verfahren das Richtige auszuwählen.“, berichtet Stefan Schneiderbanger, Leiter Produktionsentwicklung Beschichtungen bei der MTU Aero Engines.
Individuelle Lösungen statt Patentrezepte
Beschichtungen können hauchdünn oder mehrere Millimeter dick aufgetragen werden. Sie können porös, dicht, spröde oder weich sein und sogar Komponenten enthalten, die als Schmiermittel wirken. „Es gibt keine Patentrezepte, nur individuelle Lösungen: Jede Beschichtung muss zum Werkstoff passen und auf ihn abgestimmt sein. Nur so bekommt man am Ende genau die Oberflächenbeschaffenheit, die für eine spezifische Anwendung benötigt wird“, erläutert Schneiderbanger.
Doch wie findet man eine solche Lösung? Schneiderbanger erinnert sich noch gut an den Tag, als ein Konstrukteur ihm von einem drohenden Verschleiß der Outer Air Seals in einem Triebwerk berichtete, das gerade entwickelt wurde. Diese Shroud-Segmente befinden sich in ringförmiger Anordnung in der Niederdruckturbine und werden während des Betriebs mit hohem Druck gegen einen Kolbenring gepresst. Durch den Druck können sich Verbindungen zwischen den Berührungsflächen der beiden Metallbauteile bilden, die dann etwa durch Vibrationen wieder aufreißen und das Material schädigen. Um diesen Schwing-Reib-Verschleiß (Fretting) zu eliminieren, musste eine Beschichtung gefunden werden, die den direkten Materialkontakt verhindert sowie ein Verfahren, mit dem sich diese mit hoher Präzision aufbringen lässt, sodass die Bauteile nicht mehr maßgeblich nachgearbeitet werden müssen. Mehr als hundert Proben beschichtete Schneiderbangers Team, bis exakt die gewünschten Werte für Haftfestigkeit, Härte, Porosität und Oxidgehalt erreicht waren. Ein Jahr lang dauerte die Entwicklungsarbeit, bevor die Shroud-Segmente serienmäßig beschichtet und in die Triebwerke eingebaut werden konnten. Doch die Mühe hat sich gelohnt. „Wenn keine Probleme auftreten, dann haben wir unseren Job gut gemacht“, resümiert Schneiderbanger.
Thermische Beschichtungen in Serie
Solche Erfolge sind nur möglich, wenn die Vorgaben, die das Entwicklungsteam erarbeitet hat, auch tatsächlich in der Serienproduktion erfüllt werden. Zuständig dafür ist Dr. Andreas Jakimov, Leiter der Arbeitsvorbereitung Thermisches Spritzen und sein Team: “Uns stehen 14 Produktionsanlagen für die thermische Beschichtung zur Verfügung. Die Mitarbeiter:innen in der Werkstatt müssen das ganze Spektrum der thermischen Beschichtungsverfahren bedienen, daher ist es wichtig, für jedes Bauteil exakte Vorgaben zu entwerfen.“
Aufgebracht werden all diese thermischen Beschichtungen hinter verschlossenen Türen, in hermetisch abgeriegelten Kammern und gesteuert durch Computer. Erst wenn der Beschichtungsprozess vollständig abgeschlossen und die Luft wieder rein ist, öffnen sich die Türen. Die Bauteile sind dann bereit für den nächsten Fertigungsschritt.
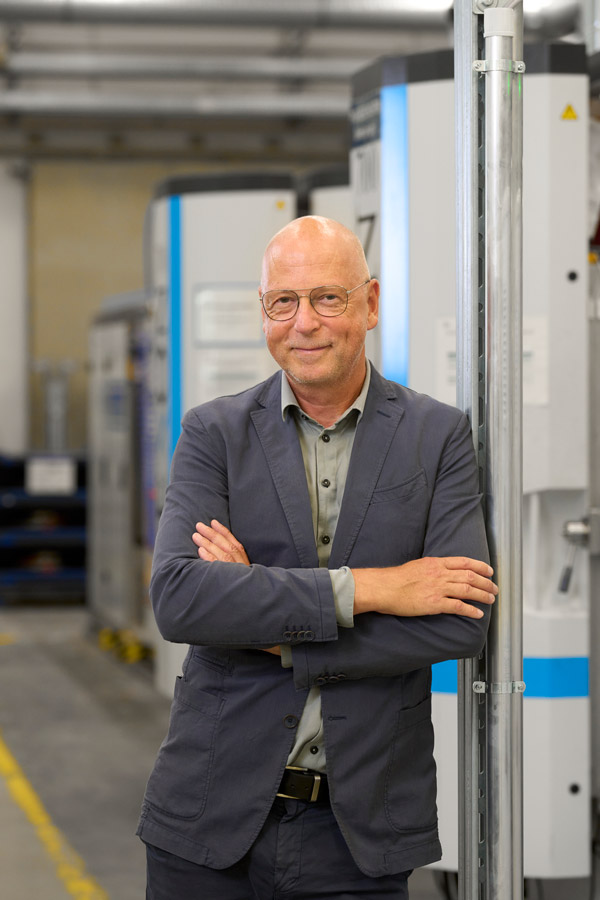
„Die Erosionsschutzschicht ERCoat® – eine Eigenentwicklung der MTU – verlängert das Leben der Triebwerksschaufeln, wenn diese einem Bombardement von Sand und Staub ausgesetzt sind.“
Leiter der Arbeitsvorbereitung PVD
Veredelung im luftleeren Raum
Im Gegensatz zum Thermischen Spritzen werden mit der sogenannten PVD-Technologie (Physical Vapor Deposition) dünne Schichten im Mikrometerbereich abgeschieden. Beim PVD gehen die Teile zunächst in den luftleeren Raum, denn Luftmoleküle würden das Aufbringen einer PVD Schicht, zum Beispiel als Erosionsschutz für Blisks (Blade Integrated Disks) im Verdichter, stören. Da bei Blisks nur die Schaufeln, nicht aber die Scheiben mit der Erosionsschutzschicht versehen werden sollen, decken Verfahrensprofis die Scheiben mit metallischen Schutzhüllen ab, wenn sie die Blisks auf Gestelle montieren. Nur die Schaufeln ragen noch aus der Maskierung heraus, wenn die Gestelle in Vakuumkammern geschoben und die Türen verriegelt werden. Eine Pumpe saugt die Luft aus der Kammer, dann wird ein Schutzgas eingeleitet und das Gestell mit den Blisks beginnt sich zu drehen.
Als erstes trifft ein Ionenstrahl auf die Oberflächen, der diese reinigt und physikalisch aktiviert. Für den eigentlichen Beschichtungsprozess wird dann ein Lichtbogen gezündet, der das Beschichtungsmaterial, eine Chromplatte, zum Verdampfen bringt. Hohe elektrische Spannungen entladen sich – ähnlich wie Blitze bei einem Gewitter. Der metallische Dampf kondensiert anschließend auf der Bauteiloberfläche und bildet eine nur mikrometerdünne kristalline Schichtlage. Im nächsten Schritt erzeugt der Lichtbogen einen Dampf aus einer Chrom-Aluminium-Legierung. Die Metallionen verbinden sich mit dem hierfür eingeleiteten Stickstoff aus der Kammer-Atmosphäre zu Metallnitrid, das sich nun als weitere dünne Keramikschicht niederschlägt. Es folgen weitere Schichten – immer wieder Metall und Keramik im Wechsel – bis die gewünschte sogenannte Multilayer-Schicht aufgebaut wurde.
„Der Schichtaufbau sorgt dafür, dass die Schutzschicht, dank der Keramik, sehr stabil ist, gleichzeitig aber, durch die Metalllagen, eine gewisse Plastizität besitzt. Das hat den Vorteil, dass die Beschichtung weniger rissanfällig ist“, erklärt Dr. Achim Meier, Leiter der Arbeitsvorbereitung PVD. „Die Erosionsschutzschicht ERCoat® – eine Eigenentwicklung der MTU – verlängert das Leben der Triebwerksschaufeln, wenn diese einem Bombardement von Sand und Staub ausgesetzt sind.“ Die Partikel wirken auf die Oberflächen wie ein Sandstrahlgebläse. Für Airlines, deren Flugzeuge oft in Gebieten mit einem hohen Sand- und Staubanteil in der Luft fliegen, ist Erosion ein echtes Problem: Die Form der Schaufeln verändert sich bereits innerhalb relativ weniger Flugstunden. ERCoat® verringert die Erosion und spart damit Instandhaltungskosten.
Die Nachfrage nach dem Erosionsschutz hat in den letzten Jahren deutlich zugenommen. Derzeit wird bei der MTU der Fertigungsbereich PVD ausgebaut. Künftig werden in einer neuen Halle mehrere PVD-Beschichtungsanlagen inklusive der Vor- und Nachbearbeitung zur Verfügung stehen. Die Kapazität in der Endausbaustufe ist ausreichend, um pro Jahr tausende von Blisks für Triebwerke zu beschichten.