innovation
Innovatives Montagesystem für die PW800
Die MTU geht bei der (De-)Montage für die Instandhaltung des PW800-Triebwerks neue Wege.
Autor: Tobias Weidemann | 6 Min. Lesezeit veröffentlicht am: 03.07.2024
Autor:
Tobias Weidemann
ist seit mehr als 20 Jahren als Journalist und Content-Berater tätig. Er berichtet über Technik- und Wirtschaftsthemen, oft mit Schwerpunkt auf Business-IT, Digitalisierung und Zukunftstechnologien.
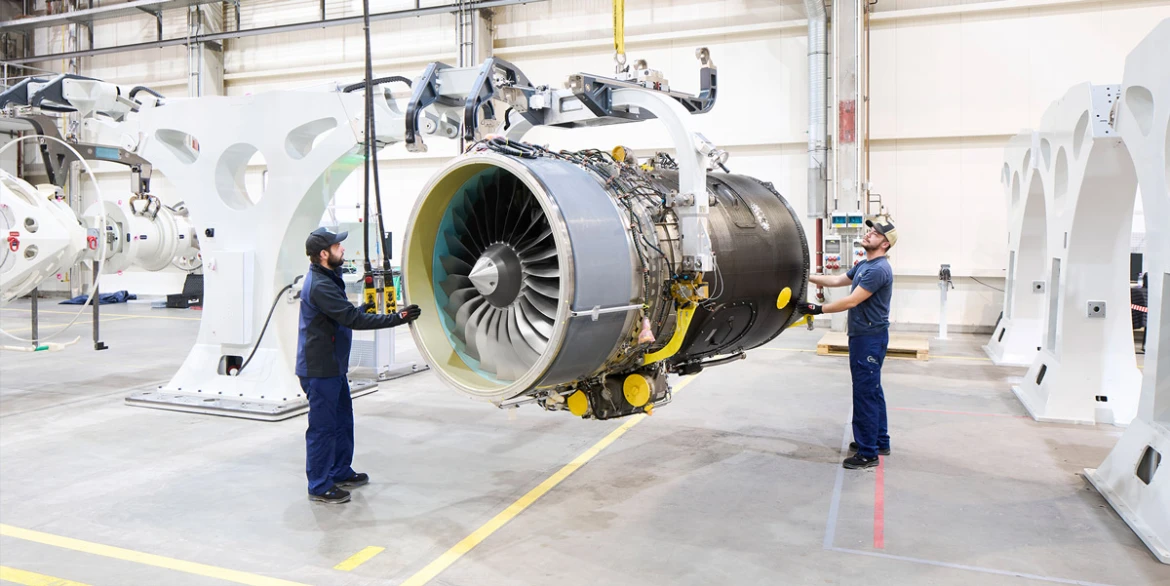
Wenn ein Triebwerk in die Instandsetzung muss, ist das nicht nur ein Vorgang, der bis ins kleinste Detail geplant wird, sondern es ist auch eine buchstäblich schwere Angelegenheit, bei der keines der Teile beim Zerlegen, Drehen, Begutachten und gegebenenfalls Reparieren beschädigt werden darf. Mehrere Tonnen wiegt ein Triebwerk, immerhin mehrere hundert Kilogramm schwer sind die einzelnen Module. Um an ihnen arbeiten zu können, muss jedes Modul aus der Horizontalachse, in der das Triebwerk liegt, in die Vertikalachse gedreht werden – und das ohne Beschädigungen zu riskieren.
PW800: Antrieb für Langstrecken-Business-Jets
- Das PW800 ist Teil der PurePower®-Familie von Pratt & Whitney und bietet erhebliche Verbesserungen bei Kraftstoffeffizienz, Emissionen und Betriebskosten.
- Es ist für Langstrecken-Business-Jets, Regionalflugzeuge und Narrowbodies konzipiert.
- Die MTU trägt zur Entwicklung und Fertigung der Niederdruckturbine und des Hochdruckverdichters bei.
- Einsatz in Gulfstream G400, G500, G600 und Dassault Falcon 6X.
Abläufe für die Instandsetzung – sogenannte Shop-Floor-Konzepte – gibt es viele und die Entscheidung für eine bestimmte Lösung wird abhängig von der Fallzahl und dem Umfang der möglichen Instandhaltungsschritte getroffen. Mal wird das Triebwerk dazu auf einem zentralen Triebwerksdock positioniert und dort Schritt für Schritt bearbeitet, mal durchläuft es eine Montagelinie mit mehreren Stationen.
Auch für die Antriebe der Business Jets Gulfstream G500 und G600, die PW814GA und PW815GA von Pratt & Whitney Canada, musste ein solches Konzept her. Denn im Laufe 2024 erfolgt erstmals die Instandsetzung des ganzen Triebwerks bei der MTU Maintenance Berlin-Brandenburg, die Niederdruckturbine des Antriebs wird dort bereits seit einigen Jahren instandgesetzt. Die Entscheidung fiel auf ein stationäres System mit einer weltweit einzigartigen Form – und das hat mit einer Besonderheit des Triebwerks zu tun. Denn das PW800 verfügt über die gleiche Kerntechnologie wie die Pratt & Whitney GTF™ Triebwerksfamilie. Gerade einmal zwei Standorte weltweit setzen das PW800 instand – einer der beiden wird die MTU Maintenance Berlin-Brandenburg in Ludwigsfelde sein.
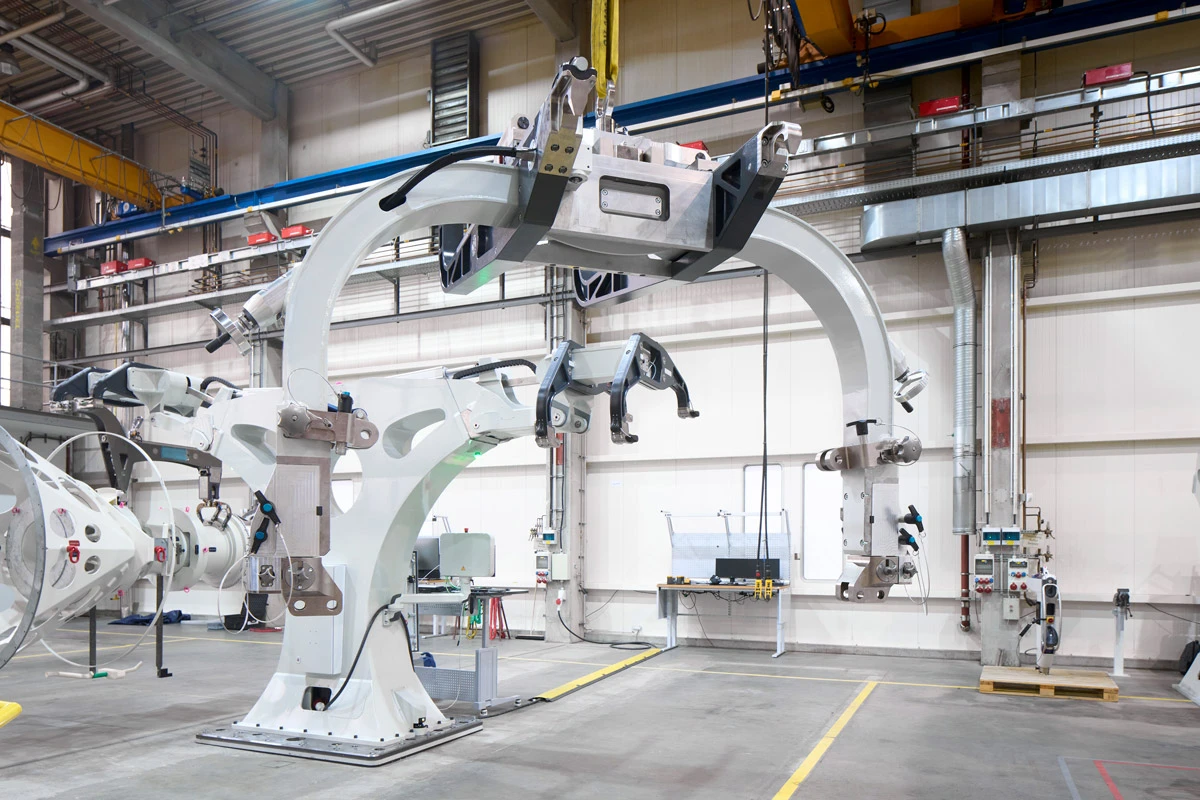
Fixed-Overhaul-System next generation: Beim FOSng handelt es sich um ein T-förmiges Dock, an dessen beiden Seiten jeweils ein Triebwerk eingehängt werden kann, sodass sich beide gleichzeitig bearbeiten lassen.
Standortübergreifend zur individuellen Lösung
Das FOSng (Fixed-Overhaul-System next generation), so der Name des ausgewählten Montage- und Demontage-Systems, ist eine standortübergreifende Teamleistung, die von der MTU Maintenance Berlin-Brandenburg über zwei Jahre intensiv mit den Kolleg:innen der Konstruktion aus der MTU Aero Engines in München entwickelt wurde. Die Entscheidung fiel auf eine Weiterentwicklung des FOS-Montagekonzepts, das bereits vor einigen Jahren für EME Aero im polnischen Jasionka, ein Joint-Venture der MTU mit Lufthansa Technik, entwickelt wurde. Das Konzept gewährleistet dort die Instandhaltung von GTF-Triebwerken und kommt in gleicher Form auch bei der MTU Maintenance Zhuhai zum Einsatz.
„Die Alternative wäre die Anschaffung einer Montage-Bay-Lösung von Pratt & Whitney Canada (P&WC) gewesen“, berichtet Dr. Nico Koppold, Leiter Process Engineering Operations am Standort in Ludwigsfelde. Doch das System, das die MTU-Expert:innen bei P&WC in West Virginia in Augenschein genommen hatten, hätte eine ungefähr doppelt so große Fläche belegt und auch von der Höhe nicht mit den vorhandenen Kransystemen der Halle zusammengepasst.
„Wir haben uns daraufhin die komplette Zerlegung des PW800-Triebwerks angeschaut und festgestellt, dass es sinnvoll ist, ein neues Montage- und Demontagekonzept zu entwickeln“, erklärt Benedikt Lechner, Prozessingenieur für die Montagesysteme bei der MTU in München. Dabei stellte sich schnell heraus, dass sich eine Lösung anbietet, bei der das Triebwerk an einem zentralen Ort aufgehängt wird, komplett von oben mit dem Kran zugänglich ist und umfassend instandgesetzt werden kann.
Gute Anpassbarkeit durch universelle Schnittstelle
Beim FOSng handelt es sich um ein T-förmiges Dock, an dessen beiden Seiten jeweils ein Triebwerk eingehängt werden kann, sodass sich beide gleichzeitig bearbeiten lassen. Es ist für Gewichte bis 5,5 Tonnen pro Seite ausgelegt – ausreichend für zwei PW800-Triebwerke. Dabei fällt das FOSng im Vergleich zum Vorgänger höher und breiter aus, sodass auch größere Triebwerke bearbeitet werden könnten. Positiver Nebeneffekt ist der gewonnene Platz zwischen Triebwerk und FOSng-Ständer, der ein ergonomisches Arbeiten ermöglicht.
Auch ein Mehr an Flexibilität war gewünscht: „Während die bisherigen FOS-Systeme für die GTF-Triebwerksfamilie ausgelegt sind, wollten wir mit dem FOSng ein System für unterschiedliche Narrowbody-Triebwerkstypen schaffen, das sich damit auch für verschiedene MRO-Standorte der MTU eignet und dort jeweils an das vorhandene Triebwerksportfolio anzupassen ist“, erklärt Stefan Hofner, Konstrukteur für Montagesysteme bei der MTU in München. Triebwerksspezifisch ist hier lediglich das Shuttle, also die Verbindung zwischen Triebwerk und FOSng.
Aus diesem Grund hat das FOSng eine universale Schnittstelle, an der sich verschiedene individuell angepasste Adapterplatten anbringen lassen, „eine mechanisch sehr simple, aber dafür instandhaltungsarme und wenig empfindliche Lösung“, erklärt Hofner. Wenn die Platte angebracht ist, kann der Kran mit dem Shuttle-Prinzip arbeiten, das sich bereits bei der ersten FOS-Generation bewährt hat. Dabei fährt der Transportwagen das Triebwerk in die Instandhaltungshalle und positioniert es unter dem Deckenkran. Am Kran ist bereits das passende Adapter-Shuttle angebracht, das am Triebwerksgehäuse befestigt wird. Er hebt das 1,5 Meter hohe Triebwerk vorsichtig aus dem Wagen und hängt es an einen der Träger des FOSng. Beide Triebwerksseiten können unabhängig voneinander nach oben und unten in die optimale Position bewegt werden, um den Mechaniker:innen die Möglichkeit zu geben, in einer ergonomischen Haltung am Triebwerk zu arbeiten. Dabei können sie das Triebwerk nicht nur in den gewünschten Winkel, sondern auch auf die gewünschte Arbeitshöhe fahren.
Das FOSng-System
- Entwicklung: Über zwei Jahre intensive Zusammenarbeit zwischen MTU Maintenance Berlin-Brandenburg und MTU Aero Engines
- Design: T-förmiges Dock für gleichzeitige Bearbeitung zweier Triebwerke.
- Kapazität: Ausgelegt für Gewichte bis 5,5 Tonnen pro Seite.
- Smartlifter: Intelligenter Kranhaken, hebt und dreht Lasten bis 750 Kilogramm.
Vorteile:
- Reduziert Vorbereitungszeit auf eine halbe Stunde.
- Anpassbar an verschiedene Triebwerkstypen und MRO-Standorte.
- Optimale Arbeitsbedingungen für Mechaniker durch Höhenverstellbarkeit.
Smartlifter als stimmige Ergänzung zum System
Ein zentrales Element, das für eine intelligente Arbeitsunterstützung sorgt, ist der am Kran angebrachte Smartlifter – ein „intelligenter Kranhaken“, der an einzelne Module des Triebwerks andockt und Lasten bis zu 750 Kilogramm heben und drehen kann. „Der smarte Greifarm lässt sich auf jede Vorrichtung für jede Triebwerksvariante spezifisch adaptieren und erkennt dabei automatisch, welches Tooling gerade angebaut ist und welches Modul dementsprechend am Haken hängt“, erklärt Hofner.
Sobald der Smartlifter mit einer Vorrichtung verbunden wird, nimmt er die dazu passenden Einstellungen vor und kann so die Kranöse programmbasiert positionieren. Zudem erkennen Sensoren die Gewichte und Schwerpunktlagen der leeren beziehungsweise beladenen Vorrichtung. „Primäres Ziel ist, dass die Mechaniker:innen bestmöglich im Montage- und Demontageprozess unterstützt werden, Fehler vermieden werden, das Triebwerk nicht ungünstig belastet wird und keines der Bauteile beschädigt wird“, erklärt Koppold. „Der Smartlifter ist für uns ein wichtiges Element neben den ganzen Tools, um den Montage- und Demontageprozess möglichst schnell, einfach, fehlerfrei und effizient durchzuführen.“
FOSng als Modell für andere MTU-Standorte
Ende 2023 wurde das FOSng-System nach einer Probephase in Ludwigsfelde installiert und nach und nach mit einem Trainingstriebwerk in Betrieb genommen. Parallel dazu absolvieren Teams von Befundern, Monteuren und Zertifizierern bei Pratt & Whitney Engine Services in Savannah, Georgia und Dallas, Texas, die erforderlichen Schulungen, um anschließend in Bridgeport, West Virginia, Arbeiten am PW800-Triebwerk durchzuführen. Sie kennen sämtliche Bauteile und die Reihenfolge des Auf- und Abbaus, haben tiefe Einblicke in die Besonderheiten des Triebwerks und die damit verbundenen Instandhaltungsprozesse. „Durch das leichtere Handling und die Höhenverstellbarkeit lässt sich die Vorbereitungszeit auf eine halbe Stunde reduzieren“, so Koppold.
Schon heute plant der Standort Ludwigsfelde ein zweites FOSng. Mittlerweile sind 18 FOS-Systeme insgesamt bei der MTU im Einsatz, weitere geplant. Geschaffen hat die MTU mit der neuen innovativen Instandhaltungslösung aber auch reichlich Know-how, das man anderweitig nutzen und an die jeweiligen Erfordernisse anpassen kann.
Eine Blaupause für andere MRO-Standorte und eine Erfolgsgeschichte ist das FOSng also in jedem Fall – aber vor allem eine, bei der das Wissensmanagement innerhalb des Unternehmens zwischen Instandhaltung und Betriebsmittelkonstruktion entscheidend für den Erfolg war.
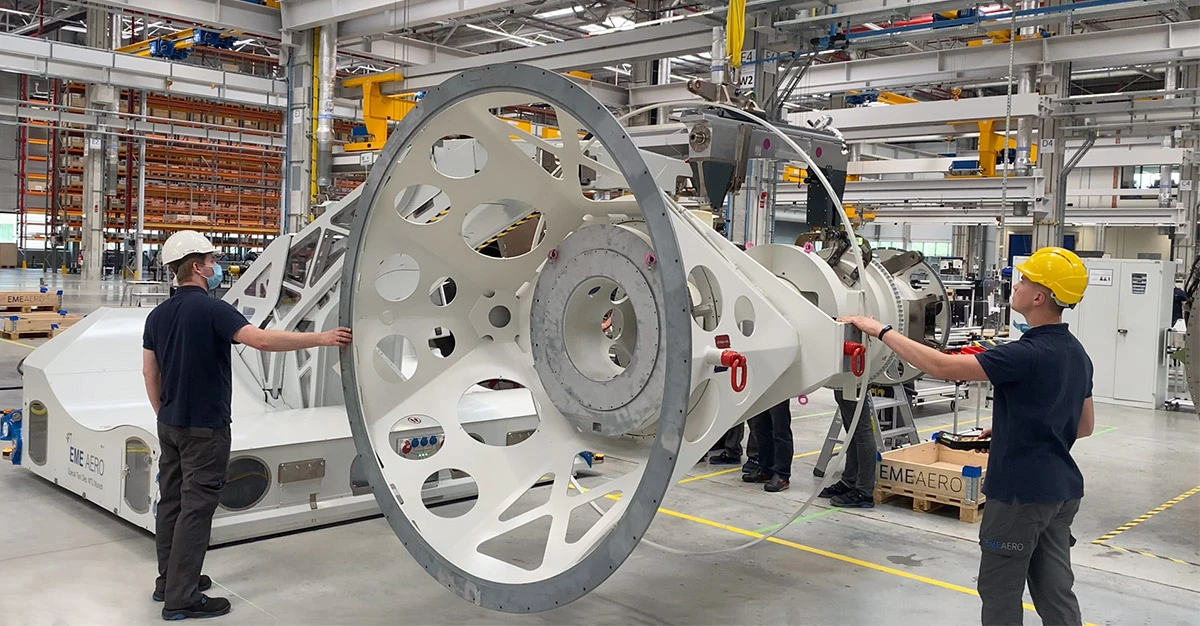
Hightech-Montagekonzept: In Rekordzeit entwickelten MTU-Spezialisten ein Montagekonzept für die Instandhaltung der Getriebefan-Triebwerke im MRO-Shop von EME Aero.