aviation
MTU Maintenance Service Centre Australia: A decade of success
The MTU Maintenance site in Perth is the only on-site provider of engine services in the South Pacific and an important part of MTU’s global service network.
12.2024 | author: Nicole Geffert | 6 mins reading time
author:
Nicole Geffert
has been working as a freelance journalist covering topics such as research and science, money and taxes, and education and careers since 1999.
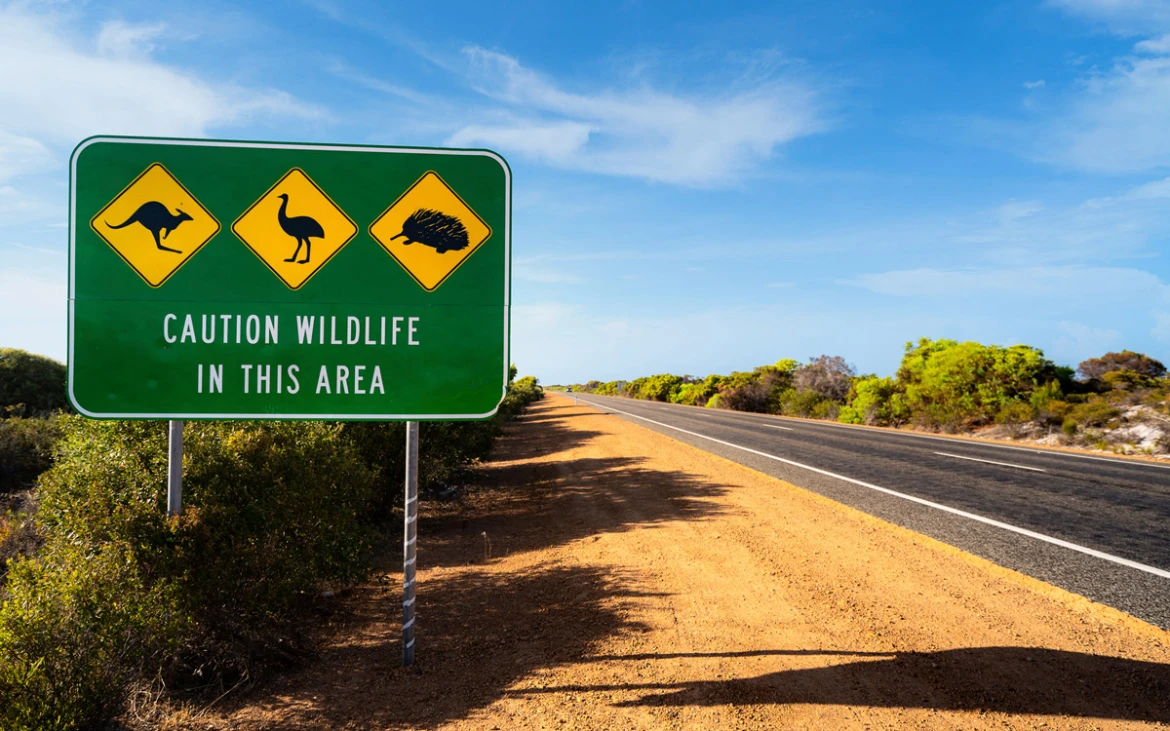
©gettyimages
Perth, the capital of Western Australia, is known not only for its 19 city beaches on the Indian Ocean and its sunny climate but also for its dynamic economy and innovative strength. With two million inhabitants, it is often described as the most remote metropolis in the world; the next biggest city, Adelaide, is 2,136 kilometers away. “Here, you get on a plane to go to your best friend’s birthday party,” says Sebastian Moerl, Managing Director of MTU Maintenance Service Centre Australia. Back home in Germany, if he told people he was going to fly a similar distance—say, from Hamburg to Lisbon—just for a party, they wouldn’t believe it.
In Perth’s boomtown environment, MTU Maintenance Service Centre Australia has successfully established itself as an independent provider of services for industrial gas turbines (IGTs) and aircraft engines. Founded in 2014, this up-and-coming member of the global MTU service network is celebrating its tenth anniversary this year. “Back then, MTU recognized that having a local presence on the Australian continent was an essential step in convincing potential customers of MTU Maintenance’s expertise and range of services,” Moerl says. In 2016, he was asked to relocate to Australia and set up an IGT service center in Perth.
Extractive industries are an indispensable sector of the country’s economy, accounting for almost one-quarter of gross domestic product. Alongside coal and iron ore, liquefied natural gas (LNG) and lithium are now more in demand than ever. That makes Australia an attractive market for services relating to IGTs, which are used in mines, at LNG terminals, and on onshore and offshore platforms.
Recipe for success: Mutual trust and personal relationships
To take on his new role, Moerl journeyed south across the equator to Australia, a continent he had never visited. As soon as he arrived, he spent 200 days on the road exploring the market, making contacts, and, above all, getting a feel for the local mentality. “The people here in Australia set store by mutual trust, personal relationships, and direct contact,” he says. His networking paid off, and MTU’s expertise won people over.
After MTU acquired its first major IGT customer, the growing team took the strategic step of moving into an office at Perth Airport. Lars Klein from MTU Maintenance Berlin-Brandenburg’s mobile field service team was the first IGT specialist to be brought in to conduct maintenance work. Others would soon follow. “There was a kind of start-up feeling to it for all of us,” Moerl recalls—and the team’s particular brand of optimism hasn’t diminished to this day. The service center in Perth has developed into a specialist for Level 2 services for the LM2500™ and LM6000™ IGTs in the General Electric (GE) LM™ series.
MTU Maintenance: With a global network of engine experts, MTU Maintenance ensures around the clock that aircraft are always in the air with minimum downtime and maximum availability—cost-effectively and always to the highest quality standards.
You may also be interested in following content
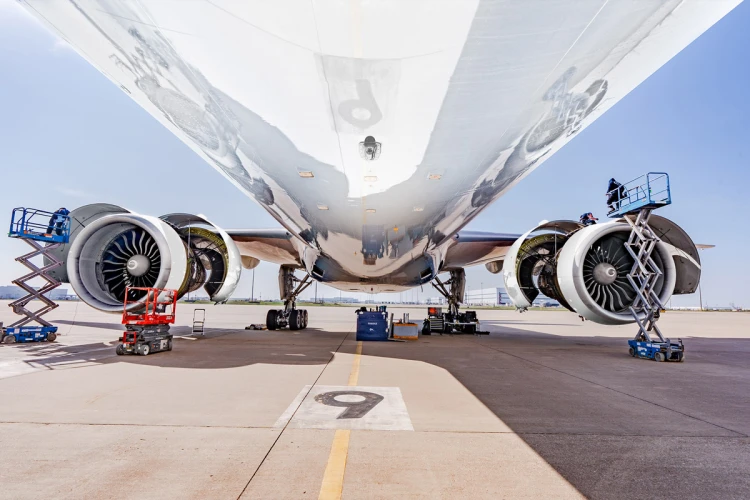
On-site service: Mobile teams for urgent engine repairs
MTU has set up shops around the world for urgent repairs. The mobile teams carry out repairs on the wing or at the airline. They can handle even complex challenges: from borescope inspections and top case repairs to the replacement of entire modules.
Airlines want fast and flexible repair services
Then came the coronavirus pandemic: Australia sealed itself off from the rest of the world and imposed entry bans and strict quarantine measures. But IGT customers in Australia could still rely on MTU and on support from the mobile field service team in Perth. “MTU’s strategy of building a global service network for its customers once again paid off,” says André Sinanian, Manager of MTU Maintenance Berlin-Brandenburg. “We have even set up a new central unit specifically for this purpose, which will manage the global network of MRO service teams and drive forward their expansion.”
On-site services are one of MTU Maintenance’s strengths. At OSS locations across the globe, mobile MTU teams specialize in carrying out repairs on the customer’s premises to ensure smooth operation. “In response to increasing cost pressure, airlines wanted smaller, more targeted repairs so they could operate their fleets cost-effectively. And this trend is continuing,” knows Xaver Schmid, who is responsible for expanding MTU’s global on-site services (OSS) business.
With the pandemic pushing up demand from airline customers for fast, flexible services, the ambitious MTU team in Perth was entrusted with new challenges when MTU decided to expand some of its global IGT service centers into aviation service centers. For the MTU team in Perth, that meant building up new capabilities and expanding their customer service. Their activities focused on GE CF34-10E engine maintenance, demand for which was high.
“This makes MTU the only on-site provider of engine services in the entire South Pacific.”
Managing Director of MTU Maintenance Service Centre Australia
Global standards and local excellence
Teams of MTU experts from Ludwigsfelde supported their Australian colleagues by training them on everything from borescope inspections and top-case repairs on high-pressure compressors to the replacement of entire modules. “The quality and safety requirements in aviation are even more complex than they are for maintaining industrial gas turbines,” Schmid says. “MTU guarantees that its customers will enjoy the same high level of quality at every MTU location worldwide.” To that end, Schmid has a global quality manager on his team who is responsible for the overarching quality standards across the entire OSS network.
The MTU team in Perth did everything right. In early 2023, the site was approved by the Australian Civil Aviation Authority CASA as a Part 145 repair station for the CF34-10E. “This makes MTU the only on-site provider of engine services in the entire South Pacific,” Moerl says. Soon after, in April 2023, the Perth team completed its first on-wing repair mission for two CF34-10E engines.
A joint effort
The MTU network thrives on the transfer of know-how and mutual support. This was also the case at the end of October, when the Australian team had to carry out a hot section repair on a CF34-10E for a customer. A borescope inspection revealed a crack in the combustion liner. With the help of colleagues from MTU Maintenance Berlin-Brandenburg, who flew out to the site to provide support, they dismantled the high- and low-pressure turbines to gain access to the defective combustion liner in the combustor. The defective combustor was then sent to the shop in Ludwigsfelde for repair. After the crack was fixed, the combustor returned to Perth. A team from Ludwigsfelde was again on-site to support the subsequent assembly of the combustor and the two turbines, taking this opportunity to train the Australian colleagues and expand their skills.
At MTU in Perth, all signs point to further growth
And that was just the beginning. The on-site business in aviation opened the door to new customers. “The feedback we’re getting from customers is very good,” Schmid says. “That’s why we’ll be continuously expanding our expertise at the Perth site so that aircraft engine maintenance becomes an attractive business segment in its own right.” The Perth team plans to step up its cooperation with CF34 customers and further expand the service. Mutual support within the MRO network, especially from MTU Maintenance Berlin-Brandenburg as an experienced partner, is also a mainstay. “The team in Perth is getting the support it needs to reach the next stage of growth,” Schmid says.
That includes the network-wide implementation of a special IT tool featuring a customer portal—a professional interface with customers that makes responding to them even faster. Whether IGTs or aircraft engines, the mobile team’s motto is simple: act quickly, flexibly, and reliably whenever the customer requires service. “We may still be a small site, but we place just as much emphasis on first-class service,” Moerl says.
So at MTU in Perth, all signs point to further growth. The range could expand to include the CFM56-7 engine, for which customers are signaling demand. “Australia is an attractive market, and one where people do a lot of flying,” Schmid says. There is also continued high demand for IGT services. The MTU team in Perth performs maintenance all over Australia, often in remote areas and under extreme climatic conditions.
Today, the team has 18 experts who all love their job. Together, their boundless passion and commitment is driving the site’s expansion. Their unique spirit and their vision of building something big go hand in hand with their awareness of being a part of the global MTU service network and an important member of the MTU family. Moerl hits the nail on the head when he says: “We’re all pulling together.”