aviation
MTU Maintenance was founded 40 years ago
In 1979, MTU launched its MRO business – MTU Maintenance – to provide aftermarket services for commercial engines. We take a look back to when the first engine arrived for a shop visit.
author: Nicole Geffert, Johannes Angerer | 4 mins reading time published on: 01.09.2019
author:
Nicole Geffert has been working as a freelance journalist covering topics such as research and science, money and taxes, and education and careers since 1999.
Johannes Angerer partner of the employer branding agency identifire, strengthens brands by researching the formative stories behind them and telling them in appealing forms, whether as text, video or in an exhibition.
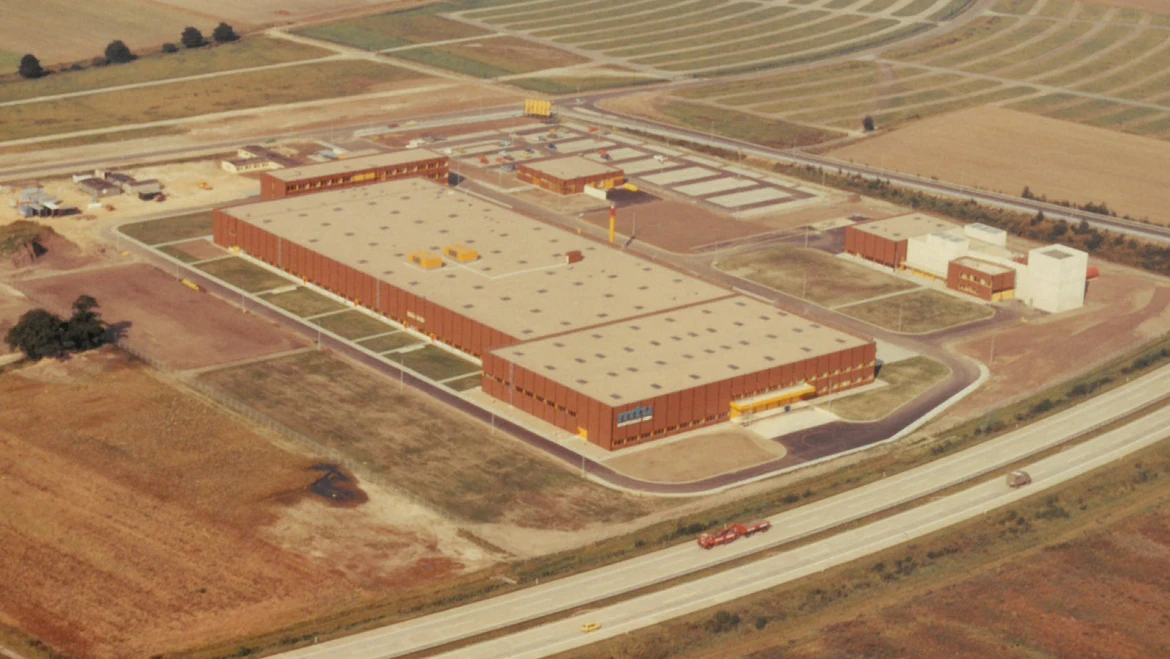
- MTU Maintenance was founded 40 years ago
- Engine MRO past and present at MTU Maintenance
- 40 Years
Up until the 1970s, air travel was considered a pure luxury. In 1977, a worker on a standard wage in Germany took home 710 Deutsche Mark per month. Back then, a return flight from Frankfurt to New York in peak season cost 2,400 Deutsche Mark. But that was set to change. As commercial aviation really began to take off in the 1970s, flying started to become increasingly affordable. And with this momentum came a rising demand for maintenance services for commercial engines.
At MTU München (now MTU Aero Engines AG), this development became a much‑discussed topic for the executive board as they considered how the company could benefit from it. Until then, MTU’s main activity had revolved around military applications, with the company specializing in the engines powering the Tornado and other military aircraft. But now the company was considering branching out into maintenance and repair activities for commercial engines such as the General Electric (GE) CF6 powering the first Airbus A300, the Boeing 747 and McDonnell Douglas DC-10-30.
While very few airlines at the time had the know‑how and equipment needed for this work, MTU did – thanks to its expertise in military programs.
“In 1976, we carried out our first studies into the feasibility of commercial MRO activities at MTU and visited facilities in the USA,” says Franz Weinzierl, who headed up sales and marketing at MTU Maintenance Hannover until 2002 and is now retired. He was the project manager in charge of setting up MTU’s commercial maintenance business. A market analysis delivered promising results: a maintenance facility in Western Europe could meet the needs of 67 airlines with around 1,250 engines. The investment would be extremely high – 30 million Deutsche Mark for the initial equipment alone. But this was undoubtedly the right time to secure a firm foothold in the market.
So, in 1979, MTU decided to begin maintenance operations for commercial engines and industrial gas turbines, and established MTU Maintenance as a new business alongside its existing development, production and military maintenance activities. Given its close proximity to the airport, Hannover‑Langenhagen was the logical choice for the location. “At the time, the federal state of Lower Saxony was really keen to create highly skilled employment opportunities in the region to help northern Germany catch up in the high‑tech sector,” Weinzierl explains.
On November 14, 1979, MTU Maintenance Hannover was established as a wholly owned subsidiary of MTU. It was a greenfield development. “Before the ground was first broken, I stood in the field and watched a farmer as he went up and down with his plow,” Weinzierl recalls. Test stands, workshops and administrative buildings quickly started to spring up on the construction site, where a sign read: “A plant for aircraft engine maintenance is under construction here. We are hiring.” Word soon spread in the area. Jörg Schenkemeyer, a young precision engineer, was one of the applicants at the time. Before he and other new specialists could start, they received part of their training at MTU in Munich.
Late in the summer of 1981, machinery was delivered and set up in the shop. Employees assembled welding booths und workbenches, while tooling and specialist equipment and gantries for commercial engine maintenance were located at the end of the hall. The first orders came from MTU in Munich, where airfoils for GE were repaired.
Employees shared many “historic” moments back in these early days, such as the time when they gathered with Wolf Birner, former operations manager, to celebrate the arrival of a new 5-axis vertical turning machine. The first order was a flange for a compressor rear frame – a thick cowl that encases the combustor – that had to be turned to exactly the right dimensions. The machine operator began the turning operation and then almost immediately stopped again. He stooped, picked up the first chip and placed it in Birner’s hand. “We ought to keep this one,” he said. And yes, it is still around today, mounted in resin.
On November 5, 1981, limousines pulled up outside. Out stepped Birgit Breuel, Minister of Economy and Transport in Lower Saxony at the time, and representatives of local government, who had arrived for the official opening of the first MTU Maintenance site. The ceremony took place in the test facility, where the visitors marked the occasion with MTU management, former CEO Manfred Holz and senior employees.
At the end of 1981, things took off in the shop. The Hapag-Lloyd airline, which primarily operated charter flights to tourist destinations around the Mediterranean, entrusted the young company with its CF6-50 commercial engines, and the CF6-80 for the Boeing 767 completed test runs in the newly established test stand. In addition to that, orders for the maintenance of RB211-22B/524 engines and the LM2500 gas turbine filled the books.
Schenkemeyer still clearly remembers the day in November 1981 when a Unimog truck stopped in front of the shop. It was transporting a CF6-50 operated by Hapag-Lloyd Flug – the first complete engine that the MTU Maintenance team was set to repair. “Almost all of the 200 colleagues gathered to see this huge piece of machinery in the shop. We gazed at the engine as if in awe. This was our future.”