innovation
MTU brush seals now in use in production for space applications
After transferring its brush seal technology to an additive manufacturing application, MTU is enabling components for space applications to be produced with wafer-thin walls.
author: Thorsten Rienth | 2 mins reading time published on: 12.09.2019
author:
Thorsten Rienth
writes as a freelance journalist for AEROREPORT. In addition to the aerospace industry, his technical writing focuses on rail traffic and the transportation industry.
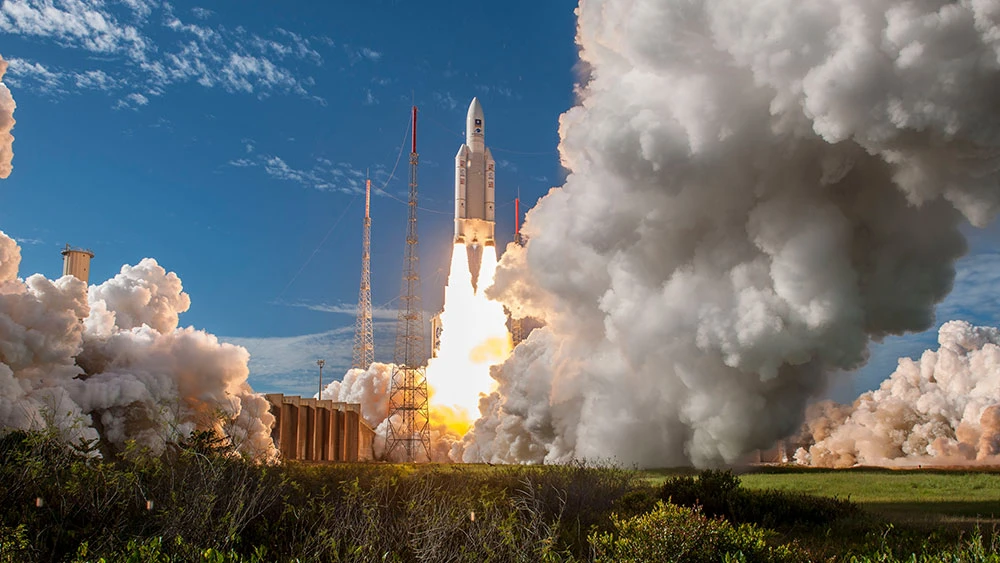
Every last gram counts for the components that Munich-based ArianeGroup GmbH sends up into space. For that reason, they are designed to have wafer-thin walls, often with a sophisticated internal structure. Their design has become so complex, in fact, that conventional processes are barely capable of producing them. For production engineers Dr. Fabian Riss and Dominik Scherer from ArianeGroup, it’s cases like these where 3D printing is the only way forward. This approach is known as design-driven manufacturing.
In this case, the technology involved is a three-dimensional welding process. Rather than milling components from a solid workpiece, additive manufacturing is used to construct them layer by layer using metal, plastic or composite materials in powder form. Coaters deposit extremely thin layers of the powder onto a build platform and a powerful laser then selectively welds the powdered material together at the exact locations specified by the computer-generated component design data. In this way, the component is built upwards layer by layer just a few micrometers at a time, depending on the application.
But even this ingenious technology has its limitations when it comes to thin-walled components for space applications. “With conventional, rigid coaters, contact between the component and the blade often resulted in us having to abort the process,” Riss explains. “Each time that happened meant a scrap part and the loss of valuable production time.”
This is where MTU and its brush seals come in. Composed of thousands of wires measuring just fractions of a millimeter across that have been wound and cut into brushes, they form highly flexible seals for engines as well as steam and industrial gas turbines. Shaped as required, they adapt almost perfectly to the surfaces to be sealed, and yet are extremely robust.
Dr. Stephan Pröstler, Project Manager for Brush Seals at MTU, had an idea: “If we could apply our brush seal technology to the coaters in 3D printing machines,” he thought, “then we might be able to solve the issue we have with the coating blade disrupting production of thin-walled aerospace components.”
ArianeGroup uses the long, thin coater for 3D printing.
It would not be the first time that Germany’s leading engine manufacturer has adapted its sealing expertise for applications in general mechanical engineering, including pumps, machine tools and special machines, the automotive industry, shipbuilding applications or coal mills. MTU has a dedicated development and production department for additive manufacturing, where it produces borescope bosses for the geared turbofan engine family, for example.
Pröstler, an expert in his field, decided to team up with his colleagues from additive manufacturing and a few months later, their joint efforts resulted in a shiny silver component that resembles a flat metal broom without a handle. They took a strip originally intended as a brush seal and turned it into a long, thin coater for 3D printers, including compatible interfaces for installation in ArianeGroup’s machines.
Now, it’s a permanent fixture in production at the company. “The flexible brush coater is extremely durable,” Scherer says. “Using a rigid coating blade, by comparison, would limit the extent to which we could produce the components and we’d be looking at high process development costs.”