people
Managing digital transformation
Falk Hinderberger is digital transformation manager at MTU Aero Engines. His job is to connect the analogue and digital worlds.
author: Thorsten Rienth | 3 mins reading time published on: 01.08.2019
author:
Thorsten Rienth
writes as a freelance journalist for AEROREPORT. In addition to the aerospace industry, his technical writing focuses on rail traffic and the transportation industry.
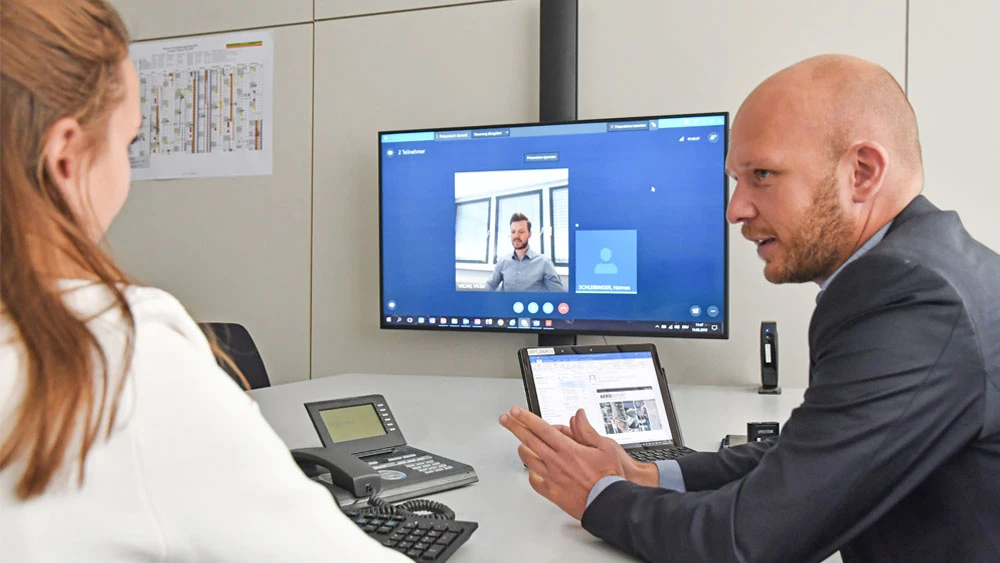
Henry Ford, the man who revolutionized the industrial production of automobiles, is reputed to have once exclaimed: “If I had asked people what they wanted, they would have said faster horses.” Now, industry is facing a change of similar magnitude to the one in Ford’s time. But today, the change doesn’t concern the assembly line per se. Instead, it’s all about making business processes digital. This has given rise to a brand-new job profile: the digital transformation manager—which is the title printed on Falk Hinderberger’s business card.
- Using multiphysics simulations to boost efficiency
- A data scientist for the aviation industry of tomorrow
- Digitalization paves the way for predicting tool wear
- Managing digital transformation
- Digital tools help create new, efficient components
- Talking geometries: A common language for more efficient engine development
The 32-year-old is digital transformation manager at MTU Aero Engines. “Our job is to connect the analogue and digital worlds,” he says before describing his role in more detail: “It’s about identifying where the potential for digitalization lies, bringing business units and IT together, and ultimately translating this into end-to-end solutions that add real value.”
Hinderberger studied International Business in Aalen and Reutlingen, during which he completed placements abroad in Mexico, Thailand and Russia. After completing his studies, he started working at a management consultancy firm and was often involved in digitalization projects in the automotive sector, with a focus on developing digital strategies and designing digital business models.
He joined MTU Aero Engines last fall, where he has been busy driving forward the digital transformation of the company’s commercial business ever since. “We want to improve workflows, learn more from our existing data and evaluate new IT technology with a view to rolling it out,” he says. One of the projects Hinderberger is currently working on involves improving the accuracy of forecasts for spare parts requirements, something that has the potential to make a huge difference at the company.
After all, engine components are often highly sophisticated, made of high-end materials and quickly add up to the cost of a mid-range car. This means they tie up a great deal of capital in the form of inventory. What’s more, the procurement chains for such components are very long, with lead times of up to 18 months.
Hinderberger thinks it’s unlikely that a purely computer-based algorithm for forecasting future requirements will be developed any time soon. “Future requirements depend on so many different factors, which spare parts planners have to be weighing up all the time. These range from weather and environmental influences, to a component’s useful service life since the last engine overhaul, to trends in the flight movements of airline fleets and the oil price.” What effect does a falling oil price have on the useful service lives of existing fleets? Would it maybe make sense for airlines to continue operating older, slightly less fuel-efficient aircraft for longer than planned? What would that mean for their spare parts requirements?
“Ten or 15 years ago, advanced data analysis and big data technologies weren’t available to us. But now, by tapping into the insights they provide, we are increasingly able to support our colleagues in spare parts requirement planning to make their decision-making processes more transparent,” Hinderberger explains. “Once the department has specified the process and the parameters, we then translate them into requirements for an IT tool—ideally one that already exists.”
Like fitting together the pieces of a big puzzle, the process involves linking data with research step by step in order to reach the ultimate goal: to have a digital system in place that enables proactive spare parts planning with optimized inventory levels.