people
Technical customer training: trust through transparency and expertise
Yannic Düring, Customer Service Manager, and Christoph Garms, Power Plant Engineer at MTU, explain how MTU uses technical customer training to help airline customers better understand the interplay between individual maintenance activities.
author: Thorsten Rienth | 2 mins reading time published on: 03.07.2024
author:
Thorsten Rienth
writes as a freelance journalist for AEROREPORT. In addition to the aerospace industry, his technical writing focuses on rail traffic and the transportation industry.
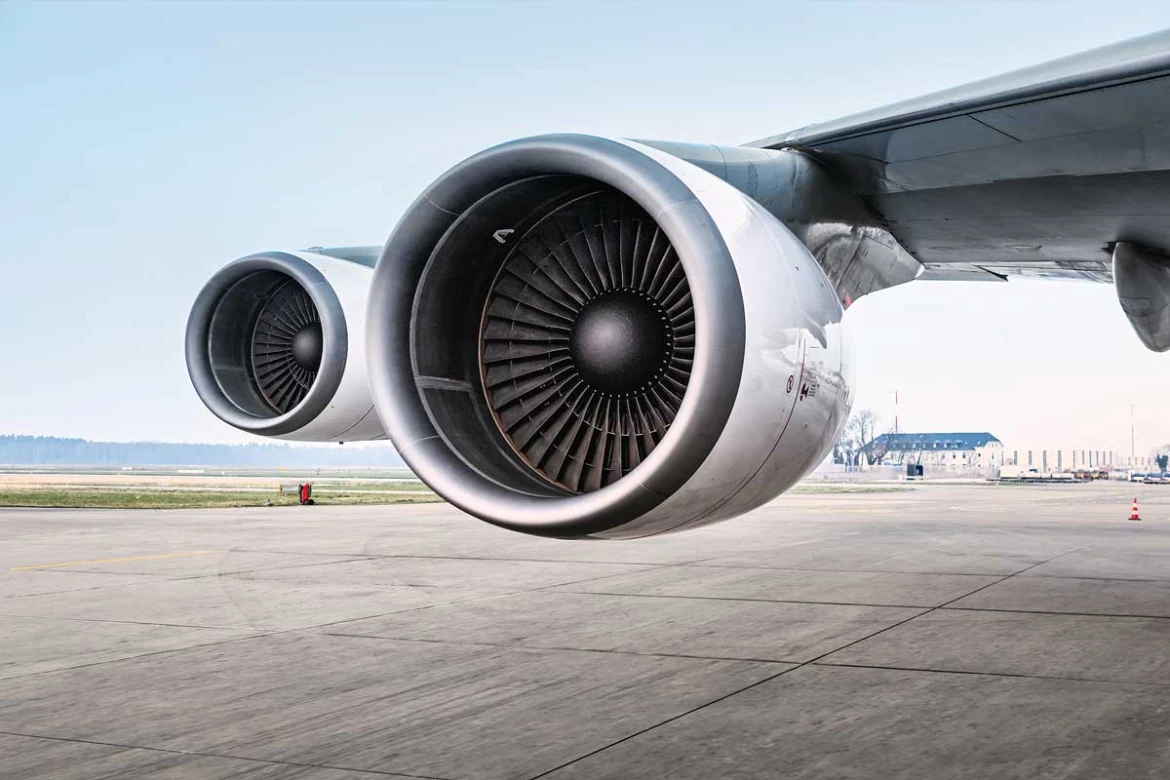
- Michael Schreyögg talks about current trends within the engine maintenance world
- On-site service: Mobile teams for urgent engine repairs
- MTU Maintenance: Training Programs Worldwide
- Technical customer training: trust through transparency and expertise
AEROREPORT: Mr. Düring, isn’t it somewhat counterproductive to bring airline representatives to the engine training course in Hannover? Next thing you know, they’ll be overhauling their engines themselves!
Yannic Düring: I’m not too worried about that. For one thing, any airlines that wanted to do that would’ve built up the necessary competencies a long time ago. For another, a two-day training course isn’t nearly enough to be able to carry out even small repairs with the necessary care and safety. To put that in perspective, training to be an aircraft maintenance engineer in Germany takes three years. Our technical customer training is about something completely different.
The idea was born during an airline visit to MTU Maintenance Canada in Vancouver. Customer representatives had occasionally taken part in internal training courses there, just to get a better understanding of some technical issues. Then the question arose as to whether we could offer something similar for the CF6-80 engine. We were of course happy to do that. A short time later, we had eight engineers from five airlines standing in the MTU Maintenance Hannover shop.
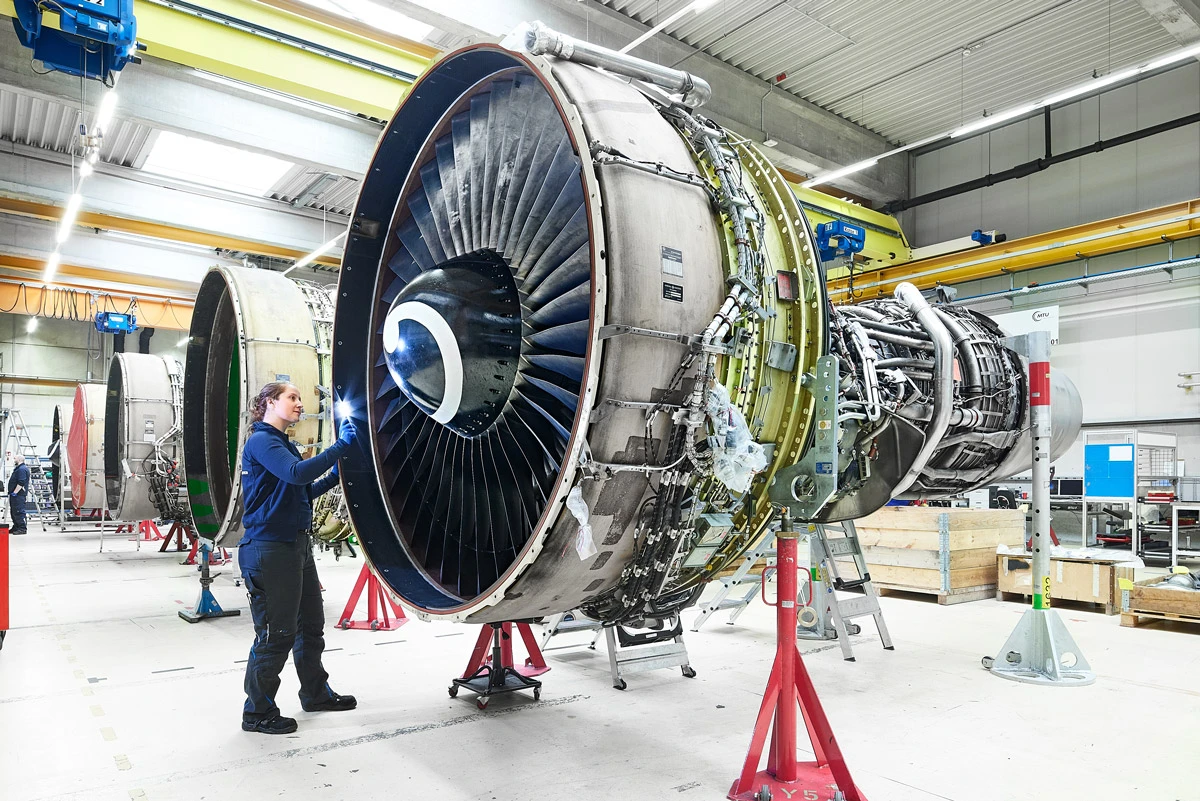
Complex MRO solutions: Airlines think primarily from a fleet or aircraft perspective. The training should help them to better understand the engine perspective.
„We’ve been repairing the CF6-80 engine in Hannover for over 35 years, so we know very well which repairs make technical and financial sense in which situations.“
Customer Service Manager at MTU Maintenance Hannover
AEROREPORT: What exactly is the goal of a course like this?
Christoph Garms: Anyone who works in the technical area of an airline thinks first and foremost from a fleet and airplane perspective. Naturally, their expertise can hardly extend down to the engine component level or even how those components interact in specific airline operations. But it’s precisely this expertise that’s important in order to be able to accurately assess and evaluate ongoing operations and maintenance costs. The resulting common understanding facilitates communication in both directions.
Let’s say you bring your car in to have the tires changed. The mechanic, who’s a good mechanic, calls you from the shop and says, “Listen, we jacked up the car and happened to notice that the brake shoes are pretty worn down. Should we change them now, too?” That’s how you save the customer time and money.
AEROREPORT: And you apply this approach to aircraft engines, too?
Düring: Exactly. We’ve been repairing the CF6-80 engine in Hannover for over 35 years, so we know very well which repairs make technical and financial sense in which situations. What other work might it make economic sense to carry out while the engine is already here in our shop? Or are there any signs of wear that let us deduce possible problems that may only occur after a few more hours of flight, so we can offer preventive solutions? We want to be very transparent with our customers about why we need to carry out certain repairs. At the same time, by sharing our expertise in this way, we want to underpin the confidence and trust the airline has in us, so that they’ll also choose our repair services for their next fleet.