aviation
RB199 development: the engine that started it all
MTU had to overcome several challenges to get the Tornado engine performing as it should—and built up invaluable knowledge in the process.
author: Denis Dilba | 7 mins reading time published on: 03.03.2019
author:
Denis Dilba
holds a degree in mechatronics, is a graduate of the German School of Journalism, and founded the “Substanz” digital science magazine. He writes articles about a wide variety of technical and business themes.
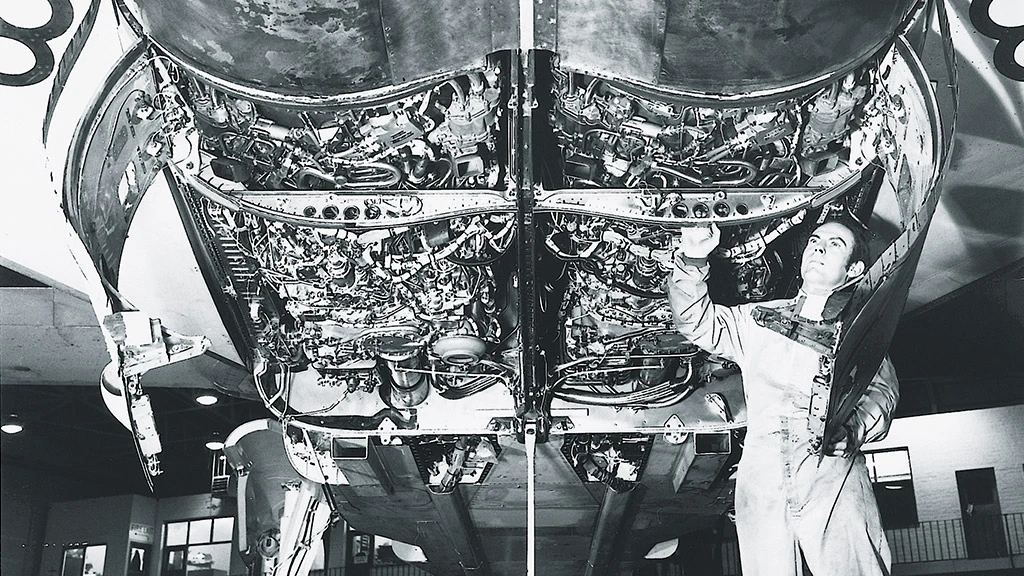
“Without the RB199, there would be no MTU Aero Engines.” This one sentence underlines the importance the development of the Tornado engine had for MTU. But this alone does not do justice to this pioneering achievement. Because no other story illustrates quite as effectively what MTU had been about since day one: using high-caliber technical ingenuity to push the boundaries of what’s possible—in short, to innovate. Back at the start of RB199 development in 1969, this was known as engineering ingenuity, says engine developer Arthur Schäffler. This savvy was absolutely necessary in order to master the challenges MTU engineers faced back then with the new jet engine, notes 81-year-old Schäffler, who was part of RB199 development from day one and whose career would take him all the way to the role of technical director for Eurojet.
“The mission requirements for the Tornado could hardly have been any bigger,” remembers Schäffler. “On the one hand, the multirole fighter had to intercept enemy aircraft at Mach 2.2, on the other master operations at low altitude.” And of course the jet should be able to take off and land on short runways. In other words, the RB199 not only had to generate a great deal of thrust while being as lightweight as possible—and consume low amounts of kerosene and enable peak acceleration in a short timeframe—it also had to have a thrust reverser. The idea was to have a three-shaft engine with 12 compressor stages, with a compressor pressure ratio of 23:1 and a turbine inlet temperature of some 1,300 degrees Celsius. “Considering what was state of the art back then, this was a massive leap in both of these respects,” Schäffler says.
Together with Rolls-Royce and Fiat (today Avio Aero), MTU began developing and producing the RB199 in 1969 to power the Tornado multirole fighter jet.
Grown-up challenge for the young MTU
Schäffler remembers how the Turbo-Union consortium, a joint venture between Rolls-Royce (40 percent), Fiat (20 percent) and MTU (40 percent) that was founded specifically to build the RB199, eagerly set about work. The division of labor meant that the MTU team, made up of engineers from Daimler-Benz and MAN Turbomotoren GmbH, “landed a major deal considering what they knew at the time,” says Schäffler. “We were responsible not only for the medium- and high-pressure compressors, the medium-pressure turbine and thrust reverser, but also for the internal air and oil system for cooling and lubricating the highly stressed casing and channeling cooling air to the turbine blades. Such technological requirements were not the only uncharted territory for MTU. Up until that point, the Munich-based company and its predecessors had mainly manufactured licensed engine parts and had never had the responsibility for developing such major portions itself. “Being solely accountable for an assembly also meant we were under a fair amount of psychological pressure,” Schäffler says.
The modest performance of the first RB199 test run met with long faces among Schäffler and his colleagues. “The efficiency was considerably below par,” he says. While the medium-pressure compressor quickly attained “very satisfactory” performance, the high-pressure compressor ran into complex problems. These included the relatively thick rotor blades of the rear stages—which were made from heavy nickel alloys—expanding significantly slower than the casing under fast-changing operating conditions such as acceleration and deceleration. This meant that over long phases, the radial clearance became too large. The result was reduced performance parameters for the high-pressure compressor and an impermissible lowering for the aerodynamic stability threshold. “It was a long time before we found a design that successfully slowed the expansion of the casing,” Schäffler says. At least all the engine manufacturers were in the same boat at that stage, says the engineer. “The clearance problem was not well known—we just had to accept the long time it took to find a solution.”
Failing the bird strike test
Just as surprising was the discovery that the surface of the blades for all rear stages of the high-pressure section was much too rough. “This meant that the system wasn’t achieving its full aerodynamic potential,” Schäffler says. Here too, it would be years before they succeeded in manufacturing the thumbnail-sized blades in a suitable quality. Another thing Schäffler remembers very well is how the blades had to be redesigned after the first bird strike test: “The bird passed through the low- and medium-pressure compressors without doing much damage before completely destroying the high-pressure compressor.” Compared to the other issues with the RB199, Schäffler says this was easy to fix: “When we made the blades for the high-pressure compressor’s first rotor stage, we simply extended the chord length by some 30 percent. The strengthened blades subsequently withstood the strike, as did the downstream stages,” Schäffler says. Step by step, MTU developed valuable knowledge in all areas.
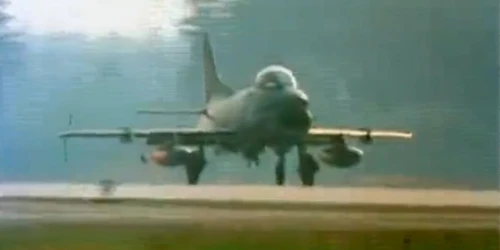
RB199: a multi-purpose engine for a multirole fighter
Originally developed with multiple new operational characteristics, the Tornado was a challenging build. The only way to fulfill the exacting mission requirements was a collaboration between Rolls-Royce, Fiat and MTU to form the Turbo-Union consortium. To the video
“Even though the journey was sometimes arduous and caused us to curse regularly, the grasp of the overall system that we gained over this time proved extremely useful to MTU,” Schäffler says. Schäffler’s time also saw an innovative leap in engine control technology. In the fall of 1987, the analog regulator first used for the RB199 was replaced with a much more reliable, flexible and amenable digital control unit, the DECU 2000. The model was superseded in 1995 by the DECU 2020 featuring improved processors. “This control unit was in production until 2003 and successfully employed by the German and Italian air forces,” Schäffler says. Around 700 were made, “but I couldn’t tell you the exact number,” he laughs. But this is not the case when it comes to the number of RB199 engines built. “There were 2,504,” Schäffler says. “And many are still in service.” Schäffler says he is of course proud of the RB199, which despite all its challenges did ultimately became one of MTU’s major successes.
The 81-year-old, who until a few years ago still gave introductory courses to MTU employees on how jet engines work, says he was lucky to be employed at MTU. “It was the ideal life for an engineer.”