aviation
Additive manufacturing: Printing a component, layer by layer
With the borescope boss, MTU became one of the world’s first engine manufacturers to have implemented industrial-scale additive production. It was the perfect strategic move: this new process is the future.
author: Denis Dilba | 7 mins reading time published on: 01.06.2019
author:
Denis Dilba
holds a degree in mechatronics, is a graduate of the German School of Journalism, and founded the “Substanz” digital science magazine. He writes articles about a wide variety of technical and business themes.

- RB199 development: the engine that started it all
- Low-pressure turbines: The path to world-class manufacturer
- Blisk development: How blade and disk became one
- Geared Turbofan: How the engine of the future was developed
- Additive manufacturing: Printing a component, layer by layer
The borescope boss is a small and seemingly insignificant component. Just about able to fit inside a person’s fist, it has lateral extensions to the left and right, each with a hole. The middle of the boss has an opening with a silver-colored screw thread, and the rest of its surface has a grayish matte finish. Once screwed onto the turbine center frame, this accessory allows technicians to look inside the low-pressure turbine with an inspection camera—the borescope—and thus to check the condition of the blades. Most people would simply have no idea what they were looking at if someone showed them the component. However, for Dr. Jürgen Kraus, Head of Additive Manufacturing for MTU Aero Engines in Munich, the borescope boss holds a very special significance. “With it, we have made the leap to industrial-scale additive production,” says Kraus. While in the past these accessories were milled from a solid block, today they are elegantly printed through the use of selective laser melting.
Borescope bosses: are small openings that admit a borescope so that the blades can be checked every now and again for wear and tear. MTU manufactures borescope bosses for the PW1100G-JM using an additive process.
3D microwelding processes
This process is generally classified under the broader field of 3D printing, but from a strictly technological standpoint, it involves 3D microwelding processes. In this method, the 3D model of the component is “sliced” on a computer into individual layers measuring 20 to 40 micrometers thick. A powerful laser then melts material in powder form within a construction chamber exactly at the locations specified by the computer-generated component design data, joining it to the layer below. In this way, components are built up, layer by layer, with new layers continually being added. Experts such as Kraus, therefore, speak of additive manufacturing. Today, the low-pressure turbines in the A320neo’s Geared Turbofan™ PW1100G-JM are being outfitted with the borescope bosses. MTU is thereby one of the first companies in the aviation industry to have received regulatory approval for the use of this innovative technology in volume production of components, and one of the first to have implemented it.
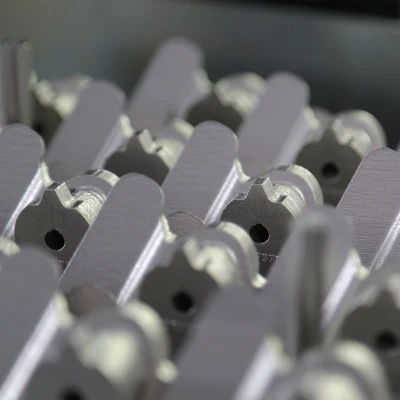
Layer by layer: is how multiple borescope bosses “grow” on a substrate. After they have been removed from the base, then it’s time to machine them to near net shape.
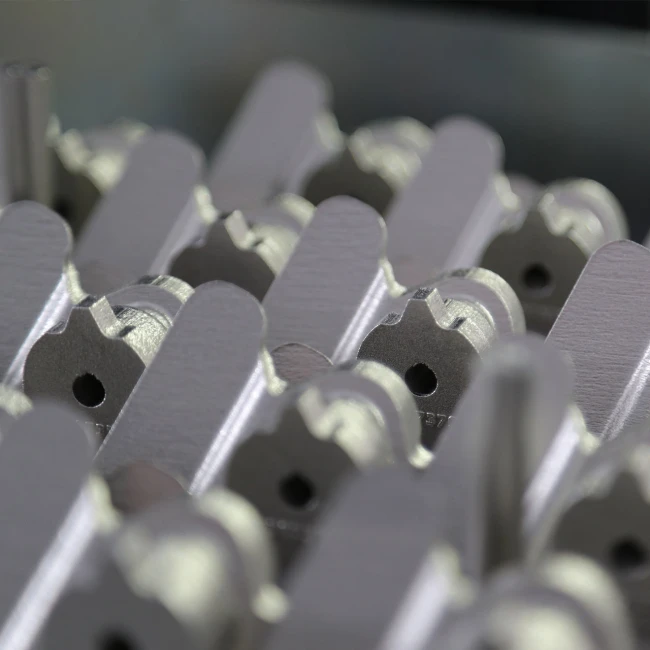
Layer by layer: is how multiple borescope bosses “grow” on a substrate. After they have been removed from the base, then it’s time to machine them to near net shape.
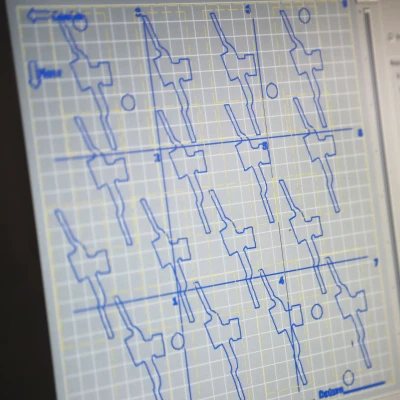
No rough edges: Additive techniques make it possible to manufacture complex component contours that conventional methods, such as milling, can achieve only with a huge amount of time and materials.
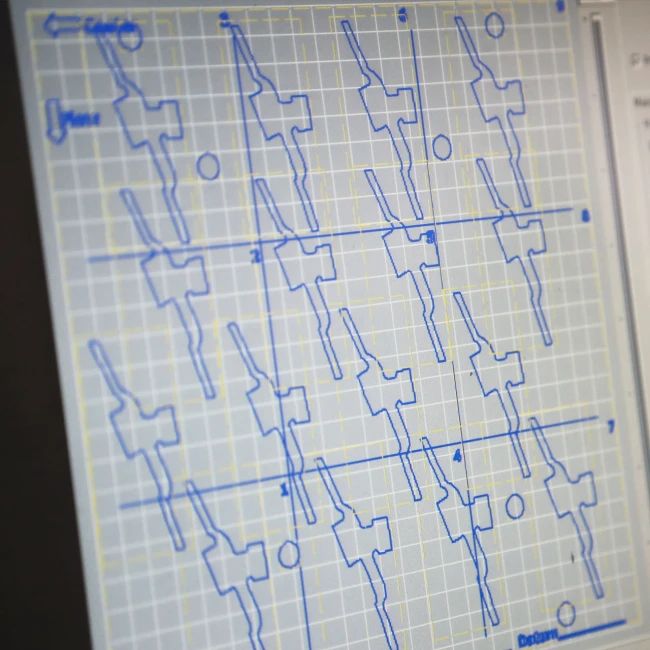
No rough edges: Additive techniques make it possible to manufacture complex component contours that conventional methods, such as milling, can achieve only with a huge amount of time and materials.
Starting with tools and blanks
MTU took the first step on this path very early on, starting work on the additive process as far back as the late 1990s. In the early years, the company focused on theoretical aspects, but quickly shifted to practical applications. “We began with the production of tools and master forms for precision casting, along with simple development parts,” Kraus recalls. In the second phase, the company produced fixture components to replace already existing parts, such as spray nozzles and grinding wheels used for manufacturing components. It was during this period that Geared Turbofan™ borescope bosses were developed. “These simple components, which are not critical to the immediate functioning of an engine, were ideal for exploring how additive manufacturing could work in volume production—thus paving the way for using it to manufacture components that are more complex and more critical,” explains Dr. Karl-Heinz Dusel, Senior Manager Additive Manufacturing Technology at MTU. For in addition to the manufacturing technology in and of itself, at that time the entire process chain also had to be rebuilt from scratch.
Mixing test: In additive manufacturing techniques, simulations can be used to test the homogeneity of the elements in a component’s metal.
Up to that point, MTU had only bought blanks, and had not manufactured them itself; as a result, Dusel and his colleagues were not able to fall back on already existing processes, procedures or structures for the manufacturing process or the securing of regulatory approval. “Simply working out the necessary norming system and calculating the material data took more than two years,” says Dusel. Moreover, it was necessary to develop and implement new methods for component testing and quality assurance. With the process now firmly established, MTU is working step by step to implement it with more complex components and other engine types. Current projects include, for example, new bionically designed and thus especially lightweight brackets for oil lines, and a stiffer, more cost-efficient seal carrier produced with additive manufacturing. This inner ring with integrated honeycombs will be installed in the high-pressure compressor in the future. The brackets, which play an equally critical role in the engine’s function, have a curved, filigree form.
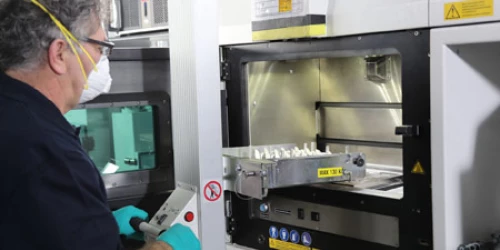
High-tech manufacturing process in use at MTU: Additive manufacturing
Additive manufacturing: MTU is one of the first companies in the aero engine industry to 3D print production parts. To the video
Bionically formed lightweight components
The new design has made it possible to cut the weight of the component by a third, without interfering with its strength or damping characteristics, according to Dusel. Hence, additive components help reduce engine weight, which reduces fuel consumption and therefore emissions. It will be a while before this point is reached, however. “Components such as these that are subject to intense stresses must be validated in engine performance tests,” Kraus explained. While this work is being carried out, his team and external experts are already conducting feasibility studies on completely new components that could be utilized in the Next European Fighter Engine (NEFE), and in the coming generation of Geared Turbofans™. “For the next generation of engines, we can envision using additive manufacturing for up to 15 percent of the components,” says Kraus. It is already clear, he continues, that in the future, engine manufacturers will not be able to survive if they don’t implement the new process.
For that reason, starting at the beginning of last year, MTU has stepped up its commitment to additive manufacturing by establishing a separate department. “By clustering all activities from design and technology development to volume production in one organizational unit, we aim to maintain our lead and pull even further ahead,” says Lars Wagner, the MTU COO. Kraus already has an idea as to how all of that could work out: the next step is to develop and manufacture new lightweight components. It is necessary to come up with new designs, new components—which could conceivably include bearing housings, brackets and struts—and new materials. The advantages of the new process can be seen particularly in the manufacture of complex components. “The future lies with additive manufacturing—every optimized component makes an engine a bit more efficient,” Kraus says.