innovation
Geared Turbofan: How the engine of the future was developed
The first preliminary studies into a geared turbofan were begun by Pratt & Whitney, MTU and Fiat Avio in the 1990s. Today, the innovative technology sets standards and brings substantial reductions in fuel, CO2 and noise.
author: Denis Dilba | 10 mins reading time published on: 01.05.2019
author:
Denis Dilba
holds a degree in mechatronics, is a graduate of the German School of Journalism, and founded the “Substanz” digital science magazine. He writes articles about a wide variety of technical and business themes.

For decades, MTU has been working on ways to make aircraft engines consume less fuel, produce lower emissions and become quieter. The golden rule has always been that to fulfill the ambitious goals of tomorrow, you must push them through the development process the day before yesterday. This requires not only farsightedness and confidence in your own expertise, but also excellent partners and a good measure of courage. When this balance is right, you can achieve the goals of the future. A perfect example of this is the Geared Turbofan™ (GTF), into which virtually all innovations of the past decades have gone.
- RB199 development: the engine that started it all
- Low-pressure turbines: The path to world-class manufacturer
- Blisk development: How blade and disk became one
- Geared Turbofan: How the engine of the future was developed
- Additive manufacturing: Printing a component, layer by layer
From ADP to ATFI to GTF
Back in the 1990s, American manufacturer Pratt & Whitney began working with MTU and the former Fiat Avio on initial preliminary studies for a geared turbofan engine under the project name Advanced Ducted Propulsor (ADP). However, the project was not further pursued for commercial reasons. But over the years that followed, rising kerosene prices coupled with customer demand for quieter engines that produced lower emissions led to a re-evaluation of the geared turbofan concept’s market potential. At the start of the 2000s, the investigations were resumed with the Advanced Technology Fan Integrator (ATFI). This demonstrator consisted of a propulsion system with a reduction gearbox between the fan and the low-pressure turbine and was tested based on a PW6000 core engine. In addition to the three ADP partners, Pratt & Whitney Canada were now also working on the project. And so engine manufacturer Pratt & Whitney laid the foundation for its patented Geared Turbofan™ program, which officially launched in 2008. At roughly the same time as the test phase of the ATFI, the MTU engineers developed a new high-pressure compressor as part of the Engine 3E project. For the layout and computation of the six-stage HDV12 compressor, a numerical 3D Navier-Stokes flow solver was used for the first time. As a result, the component achieved a high overall pressure ratio of almost 11.
The HDV12 was to form the basis for the high-pressure compressor of the PW6000 engine for the Airbus A318—and subsequently, like the ADP and ATFI demonstrators, to pave the way further for the Geared Turbofan™. Its core development started in 2005, when the partners decided to develop and test a demonstration engine. The initial tests of the overall system in 2007 immediately yielded very positive results with regard to the functionality of the critical components. However, it was also clear that the new engine overall had one big area of improvement left: further development would pay off only if it created a whole Geared Turbofan™ engine family. Convinced by the concept, Pratt & Whitney and MTU systematically invested further in the entire process chain so as to permit the creation of geared turbofans of different thrust classes. Just one year later, the Geared Turbofan™ took off for the first time on flight tests.
Engineering courage pays off
With the two major MTU workshares, the high-speed low-pressure turbine and the first four stages of the eight-stage high-pressure compressor engineered in blisk design, the engine of the future already achieves a very high degree of efficiency today. The impressive result: fuel consumption and carbon dioxide emissions are reduced by 16 percent each, and the noise footprint by 75 percent. And as fewer compressor and turbine stages are needed, not only are the engines lighter, but maintenance costs decline as well, because fewer components are exposed to the hot gas. For the key GTF component, the high-speed low-pressure turbine, MTU won two German innovation awards. Germany’s leading engine manufacturer is the only company in the world to have mastered this technology. The patience and perseverance was worth it: as well as representing a technological quantum leap, the Geared Turbofan™ concept has also been a major commercial success.
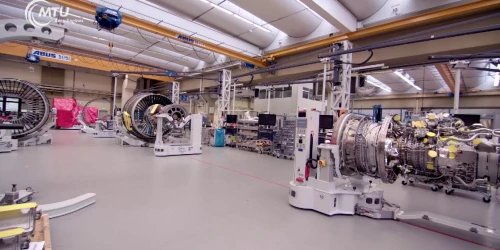
Floor-based assembly system
MTU Aero Engines’ final assembly line for the PW1100G-JM engine powering the A320neo is the only one of its kind in the world. To the video
Today, Airbus offers the GTF for the A320neo and the A220 (formerly Bombardier C Series), Mitsubishi has it in their MRJ, and Embraer has it in the new E-Jets of the E-170 and E-190 families. Moreover, Irkut wants the GTF for the MC-21. At present, a total of 80 airlines worldwide have ordered more than 8,000 of the GTF engines. More new MTU innovations have gone into the current version, such as the first additively manufactured components and brush seals. In addition, MTU has looked after a third of the entire final assembly for the A320neo PW1100G-JM engine since the end of 2016. To this end, MTU invested some 20 million euros in a track-guided assembly line system, which was developed in-house and is unique worldwide. “What we’ve achieved of course makes us proud, but nobody at MTU should rest on these laurels,” emphasizes Dr. Jörg-Michael Henne, Senior Vice President Engineering and Technology at MTU. Overall, the GTF has the potential to reduce fuel consumption and CO2 emissions by up to 40 percent.
Further development already being prepared
For instance, it would be possible to achieve even lower fan pressure ratios step by step over the coming years, which would further increase the bypass ratio—from the current 12:1 to as much as 20:1 by 2035. Moreover, MTU’s engineers are working on further improving the core engine’s thermal efficiency by increasing the pressure and temperature ratios. This will involve increasing the overall pressure ratio well beyond its current value of about 50:1, while dramatically reducing the amount of cooling air needed.
And for 2050 and beyond, MTU is already devising initial studies, concepts and ideas in collaboration with universities and other research institutes: “We need revolutionary approaches that must go beyond today’s technologies, and above all else, we need new aircraft architectures,” says Dr. Stefan Weber, Senior Vice President Technology & Engineering Advanced Programs at MTU. Among the options under review for the engine are the use of highly efficient heat engines with extremely high pressures or the integration of recuperative elements to improve the thermodynamic cycle. Shielded propellers or fans distributed around the fuselage are also possibilities. In addition, there are technological solutions such as alternative fuels and steps toward turbo-electric flight, without which future targets cannot be met.
All improvements always have the same goal: improve efficiency and thereby minimize fuel consumption, emissions and noise. The engine of the day after tomorrow has long been in the starting blocks—and MTU is already taking responsibility today for moving aviation toward emissions-free flight.