aviation
Blisk development: How blade and disk became one
With the space-saving and lighter rotor disks in the compressor with integrated blades, engines consume less fuel. The blisk success story began in the Eurofighter EJ200 engine.
author: Denis Dilba | 7 mins reading time published on: 01.05.2019
author:
Denis Dilba
holds a degree in mechatronics, is a graduate of the German School of Journalism, and founded the “Substanz” digital science magazine. He writes articles about a wide variety of technical and business themes.
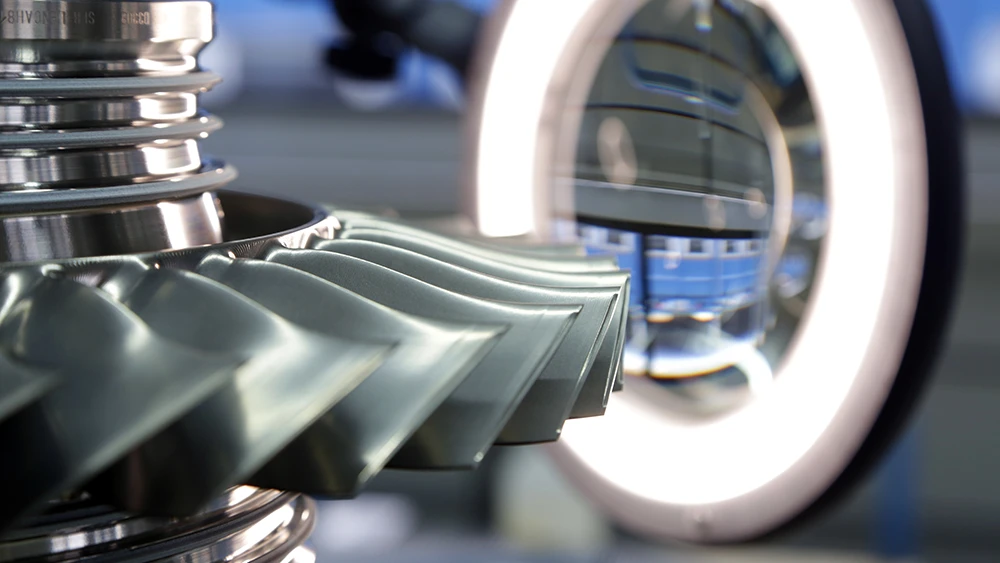
Blades and disks from a single piece—so-called blade integrated disks, or blisks for short—have long been a fixture in aircraft engines. The high-tech components, which are used in compressors, not only save space and weigh less than conventional rotors with individual blades, but they also permit better blade aerodynamics. Furthermore, they reduce assembly work and thus costs. As a result, engines become more compact and lighter overall and consume less fuel, which in turn reduces CO2 emissions and benefits the environment.
In 1995, when Arthur Schäffler first unveiled the new full-blisk low-pressure compressor to the four Eurofighter customers for their EJ200 jet engine, the response was less than enthusiastic. “Heated discussions broke out immediately,” recalls the then Technical Director of the EJ200 consortium Eurojet, thinking back to that meeting in London. The representatives from Spain, Germany, Italy and the United Kingdom had some grounds for their skepticism. Although a first blisk had already been used in a helicopter engine back then, the blisks that MTU’s Schäffler was proposing had a much greater diameter than the helicopter component. “With the EJ200 blisks, we’d gone out to the very frontier of development technology,” says the engineer, who is now 81 years old. Driven there by necessity, the MTU engineers were forced to try the new technology in order to fulfill the service life requirements for the EJ200. The high rotational speeds of the rotors in the jet engine—and thus the centrifugal forces—were so great that fretting corrosion became a problem for the conventional individual blade technology. Fretting corrosion here refers to the formation of little pits on the surfaces of the blade root and rotor groove, which can lead to cracks and ultimately to loss of the blade.
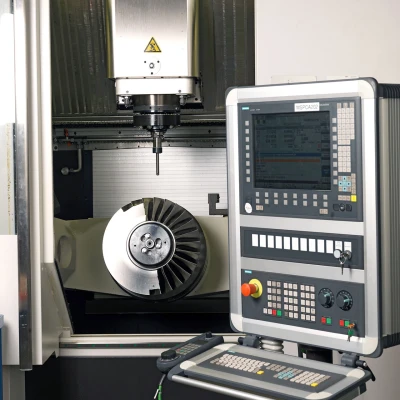
Snapshot: Good to see how this blisk is milled out of a single workpiece.
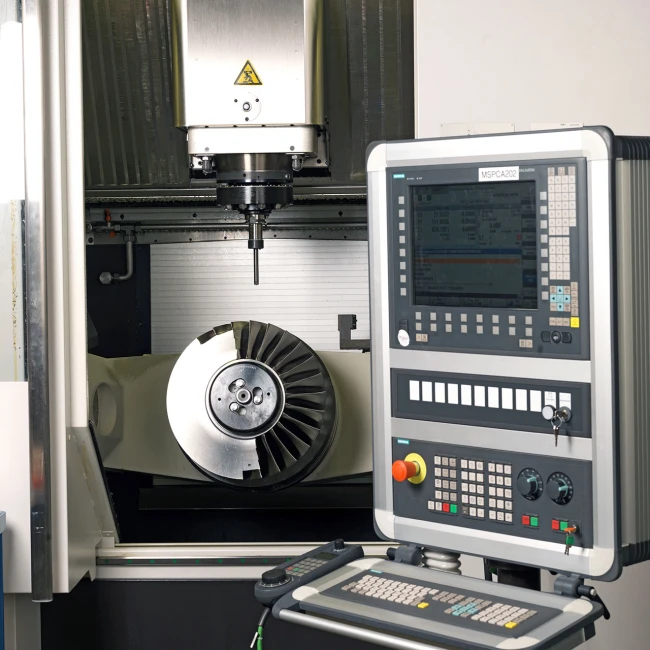
Snapshot: Good to see how this blisk is milled out of a single workpiece.
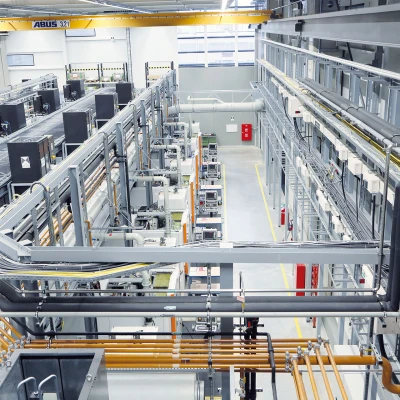
Blisk production on about 10,000 square meters: In Munich, MTU operates one of the world’s biggest and most flexible manufacturing facilities for producing blisks for high- and medium-pressure compressors.
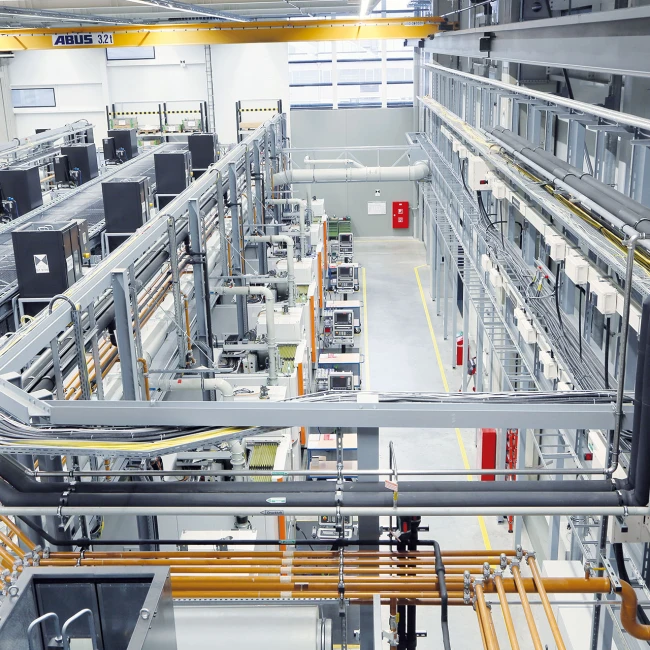
Blisk production on about 10,000 square meters: In Munich, MTU operates one of the world’s biggest and most flexible manufacturing facilities for producing blisks for high- and medium-pressure compressors.
“The first 85 EJ200 engines that were delivered without blisks in the high-pressure compressor in stages 1 and 2 were thus limited to 400 flight hours—whereas the design had planned for 4,000 hours,” says Christian Köhler, who joined MTU in 1990 and is today the Chief Engineer of the EJ200 program. The blisks resolved the problem and fully convinced the customers of the integrated disk-blade solution. By the start of 2019, 558 jets had already been delivered with the EJ200 engines—and more are on order. MTU’s blisk experience was then further utilized in an experimental high-pressure compressor that was developed as part of the HDV12 technology program and which fit more or less exactly into the PW6000 engine for the A318. “This allowed us to show Pratt & Whitney our technological abilities,” Köhler says. With a few modifications, the high-pressure compressor is a standard component in the PW6000 today, and for blisk technology this represented the leap into commercial business.
Innovative blisk manufacturing
In the classic method, the contours of the blades are milled out of a solid metal disk. However, the further forward you move in the engine—that is, where the disks get smaller and the blades bigger—the less economical the machining process becomes. “A lot of expensive material winds up in scrap, and the milling takes a very long time,” Köhler explains. Measuring up to 20 centimeters in size, the blades of the first two EJ200 low-pressure compressor stages are therefore forged individually and only then joined to the disk in a linear friction welding process developed especially for this purpose. The experts at MTU subsequently developed a further technique for blisk manufacturing: “With precise electrochemical machining (PECM), we’re now able to manufacture blisks even from nickel alloys, which are difficult to weld and to machine,” says Köhler. In the technique, the blisk blank is dissolved out of the alloy using a liquid electrolyte, an electric current and a 3D molding tool.
„Over the coming years, we’ll be manufacturing up to 6,000 blisks per year here. Without all the experience that we’ve built up over the years and our constant watchfulness and care, that would not be possible.”
One of the advantages of PECM over milling is that because they make no contact with the component during the process, the tools do not experience wear and tear. Moreover, due to the much higher reproduction precision of the chemical-electrical method, there is no need for further post-processing steps. Both these factors reduce costs. Using the innovative precision technique, MTU manufactures on behalf of Pratt & Whitney the fifth and sixth blisk stages of the Geared Turbofan™ (GTF) high-pressure compressor, which has eight stages in total and is laid out fully according to blisk design. “To manufacture the titanium blisks of the first four stages of the GTF high-pressure compressor, which were designed by MTU, we built a specially designed production facility at the Munich site,” says Dr. Stephan Bock, Senior Vice President for Advanced Commercial and Military Programs. At this facility, large titanium blisk blades are joined individually to the disk by means of linear friction welding and then adjusted using adaptive milling; meanwhile, small and medium-sized titanium blisk blades are milled from a single piece.
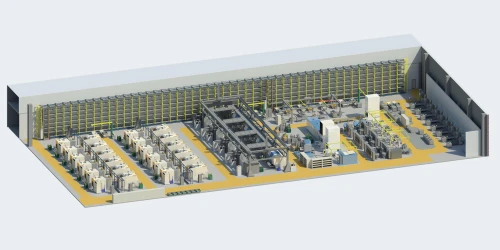
Automated blisk production
Blisks for the Pratt & Whitney GTF™ Engine Family are produced in a new and highly automated manufacturing hall. To the interaction ...
Up to 6,000 blisks per year
The center of excellence for manufacturing titanium compressor disks is a prime example of the implementation of Industry 4.0 thinking at MTU and the most state-of-the-art production facility of its kind in the world. It contains a high degree of automation, digitalization, connectivity, and self-controlling that is unique worldwide. The highly functional, energy-efficient new factory building also meets the latest in modern building standards. “Over the coming years, we’ll be manufacturing up to 6,000 blisks per year here,” says MTU expert Bock. “Without all the experience that we’ve built up over the years and our constant watchfulness and care, that would not be possible.” The processes have to be extremely stable: one manufacturing defect on a single blade can render the entire component unusable. However, Bock believes this is no time for MTU to rest on its laurels: “We’re already working on the blisks for the next GTF generation.”