good-to-know
Deicing aircraft: Combatting frost with showers and lasers
Icy wings interfere with aerodynamics and pose a threat to safety. In the future, a new laser technique could make deicing aircraft faster and more efficient.
author: Denis Dilba | 5 mins reading time published on: 10.11.2020
author:
Denis Dilba
holds a degree in mechatronics, is a graduate of the German School of Journalism, and founded the “Substanz” digital science magazine. He writes articles about a wide variety of technical and business themes.
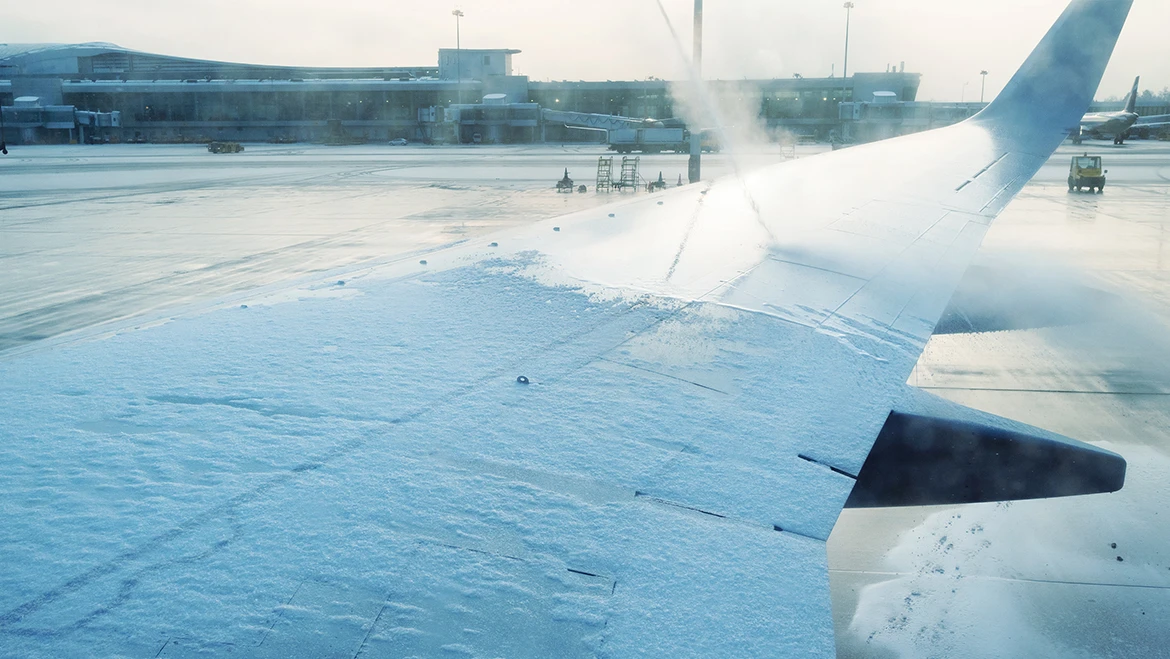
On cold fall and winter days, aircraft sometimes need the same thing people do: a hot shower. The difference is that passenger aircraft get a shower of water mixed with glycol if the wings are covered in ice and snow, if not before, because that has a negative impact on aerodynamics. Even if the layer of frost on the wings is just a few millimeters thick, it can significantly increase air resistance, which in turn decreases lift. If the wings—and especially the leading edges—become severely iced up, the aircraft may even stall and thus get into serious difficulty. Then there’s the weight issue: a five millimeter layer of frost covering the wings of an Airbus A320 can weigh up to 375 kilograms, which also significantly increases fuel consumption. It follows that passenger aircraft scheduled to fly in cold conditions are deiced prior to takeoff as a matter of course.
During the last deicing season from October to April, this procedure was performed 5,291 times at Munich Airport alone. From the point of view of the deicer manufacturers, that constituted a bad winter: the year before, that figure was 10,572—almost exactly twice as high. But even if future winters were to become still milder and aircraft remained frost-free on the ground, the problem remains of how to deice the wings during flight. This is generally done during descent, when aircraft leave their cruising altitude—at which air temperatures can be as low as minus 50 degrees Celsius, even in summer—and dip into more humid layers of air. On the ice-cold outer shell of an aircraft, water droplets freeze solid incredibly fast. Developing protective systems capable of removing such ice deposits while also inhibiting the buildup of ice during flight has therefore been a top priority for aviation researchers for a long time. Since the 1930s, various technologies have been developed to protect propellors, rotors, engine inlets, wings and tail assemblies from ice.
New anti-ice technologies must meet exacting requirements
Many smaller propellor aircraft are equipped with inflatable rubber boots, for instance on the wing leading edges. As the boots expand, the ice breaks off. Large passenger aircraft tend to employ hot air bled from their engines and carried via tubes to the leading edges of the wings. Although very effective, this method reduces engine performance. Individual electric wing heaters are more efficient, but these require batteries that make the aircraft heavier. This means that there is great demand for optimized technical solutions that can reduce—or ideally entirely prevent—the buildup of ice during flight while consuming less power than the options available today. And there is no shortage of ideas, including water- and ice-repelling microstructures that can be worked into films stuck onto the wing surface or integrated directly into the wings themselves. Work also continues into mechatronic systems designed to dislodge ice using high-frequency vibrations.
Conventional deicing of aircraft
1. First step: Deicing: The nozzle sprays the aircraft with diluted deicer heated to approx. 80 degrees Celsius. Ice and snow melt.
2. Second step: Anti-icing: The nozzle sprays the aircraft with a different, more viscous, undiluted and unheated deicer.
This protects against new ice buildup.
3. The windows are electrically heated.
4. For long wings, hot air from the engines is directed to the front edge of the wings.
5. Deicer is sprayed directly onto the wings from the nozzle on the swiveling arm.
However, none of these ideas has yet become a commercial application for passenger aircraft. “The requirements are exacting: any solution must be able to withstand mechanical strain such as erosion caused by sand, insects and other contaminants, vast fluctuations in temperature and especially high-energy UV radiation,” says Tim Kunze, Group Manager Surface Functionalization at the Fraunhofer Institute for Material and Beam Technology IWS in Dresden. In collaboration with Airbus and TU Dresden, his team has developed a promising laser treatment for surfaces, reaching two goals at once: It creates a micro-nano structure that is more resistant to the buildup of ice and causes the ice to fall off on its own once it reaches a certain thickness. And using such structures in combination with electric heating systems makes deicing more energy-efficient.
Change in lift caused by ice buildup
Ice formation on aircraft: Ice impairs aerodynamics, especially through reduced lift, while also increasing air resistance and the weight of the aircraft. Ice buildup describes the deposits of ice or frost on aircraft that can happen both in flight and on the ground.
“Direct laser interference patterning (DLIP) has the potential to reduce the use of environmentally harmful deicing agents on the ground, lower fuel consumption and shorten the time passengers have to wait while aircraft are being deiced.”
Lasered microstructures offer great deicing potential
“Direct laser interference patterning (DLIP) has the potential to reduce the use of environmentally harmful deicing agents on the ground, lower fuel consumption and shorten the time passengers have to wait while aircraft are being deiced,” Kunze says. He also points out that flying weight would also drop because aircraft could be equipped with smaller electric heating devices. “This is bound to interest an aviation industry striving to become more electric,” Kunze says. At the beginning of October, the journal Advanced Materials Interfaces published details of comparison tests on miniature wings. The tests showed that ice disappears up to 90 percent faster from DLIP surfaces than from untreated surfaces equipped with the same heating capacity. Kunze says that untreated surfaces would need five times more heating capacity to achieve the same result. Project partner Elmar Bonaccurso, materials scientist at Airbus, is satisfied with the lab test results: “Now we have to show that DLIP surfaces perform under real conditions.”
To achieve this goal, flight tests using an Airbus A350 equipped with DLIP surfaces have been underway for two years. “The microstructure remained stable,” Bonaccurso says. He hails this as a major, if only partial, success: “We’re looking for an additional chemical coating for the DLIP structure that will make it even more effective,” Bonaccurso explains, adding that only then will the technology be ready for use. Meanwhile, Kunze and his team are optimizing the commercial viability of the DLIP process in collaboration with laser manufacturers. Neither researcher is willing to speculate about when DLIP surfaces could enter production. “We’re still in the predevelopment stage and will first have to see that through before we can reliably predict any kind of timeframe,” Bonaccurso says. “But in the spirit of reducing the environmental impact, we’re naturally working as quickly as possible.”
Anti-icing technologies
Previous anti-icing systems for passenger aircraft have mainly been based on bleeding hot air from the engines. The following are a selection of more efficient solutions that are in the pipeline:
©Frauenhofer
©Frauenhofer
©Frauenhofer
Ice-repelling films
Just as water rolls of a lotus leaf, ice cannot build up on films with certain microstructures. The Fraunhofer Institute for Interfacial Engineering and Biotechnology IGB is using plasma processes to add such ice-repelling surfaces to polyurethane films. One of the challenges is to find a durable adhesive capable of attaching these films to aircraft wings for years at a time.
©Frauenhofer
©Frauenhofer
©Frauenhofer
Direct microstructuring
Another method of making ice-repelling surfaces—here, the microstructures are built directly into the wing material. The Fraunhofer Institute for Material and Beam Technology IWS uses a process known as direct laser interference patterning (DLIP). According to Fraunhofer IWS researchers, DLIP is a cost-effective way of producing particularly complex microstructures, and flight tests have already yielded positive results.
©Villinger GmbH
©Villinger GmbH
©Villinger GmbH
Electrically heated paint
Villinger GmbH, an Austrian company specializing in anti-ice technology, is developing paints equipped with semi-conductive polymers to make them heatable. These are already being used on small aircraft. The Fraunhofer Institute for Manufacturing Engineering and Automation IPA is pursuing a similar idea: heating layers of carbon nanotubes located beneath protective paint to prevent ice from building up on the surface.
©DLR
©DLR
©DLR
High-frequency vibration
Engineers at the German Aerospace Center (DLR) want to literally shake off the ice problem. To do this, they are using actuators to subject icy wings to targeted high-frequency vibrations. The ice then breaks loose and falls off. This technology is said to be more efficient than the bleed-air systems commonly used in passenger aircraft, and several business jets already rely on it to deice their tail assemblies.