innovation
Im DigiLab macht die MTU digitale Innovationen erlebbar
Das DigiLab ist ein Experimentierraum, in dem Mitarbeiter neue Technologien ausprobieren können. Technikkürzel wie AR, VR, KI und IoT werden so mit Leben gefüllt.
Autor: Tobias Weidemann | 5 Min. Lesezeit veröffentlicht am: 06.05.2022
Autor:
Tobias Weidemann
ist seit mehr als 20 Jahren als Journalist und Content-Berater tätig. Er berichtet über Technik- und Wirtschaftsthemen, oft mit Schwerpunkt auf Business-IT, Digitalisierung und Zukunftstechnologien.
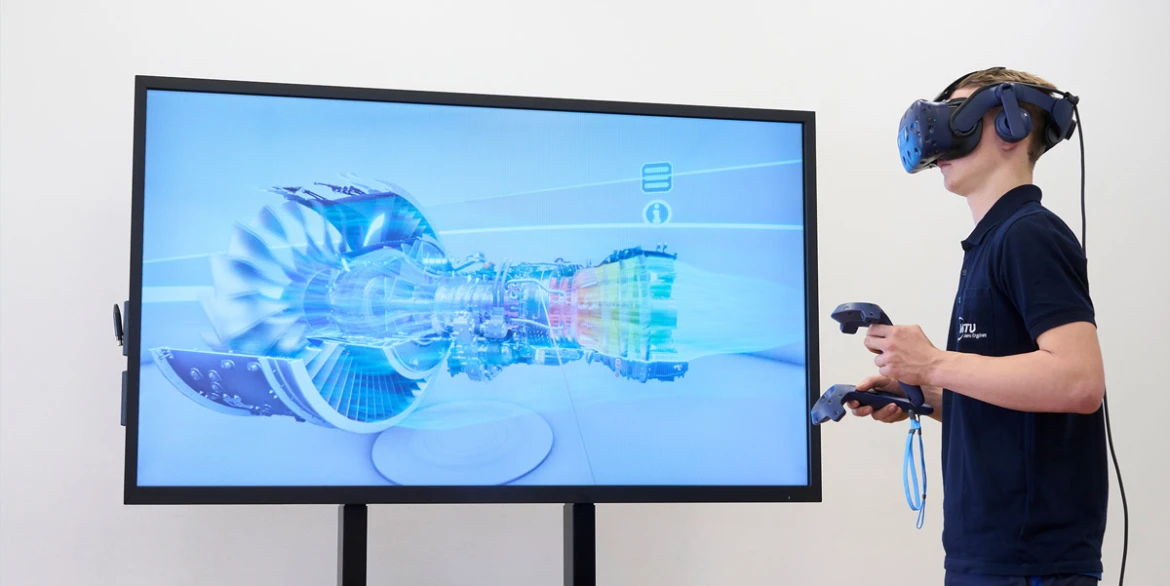
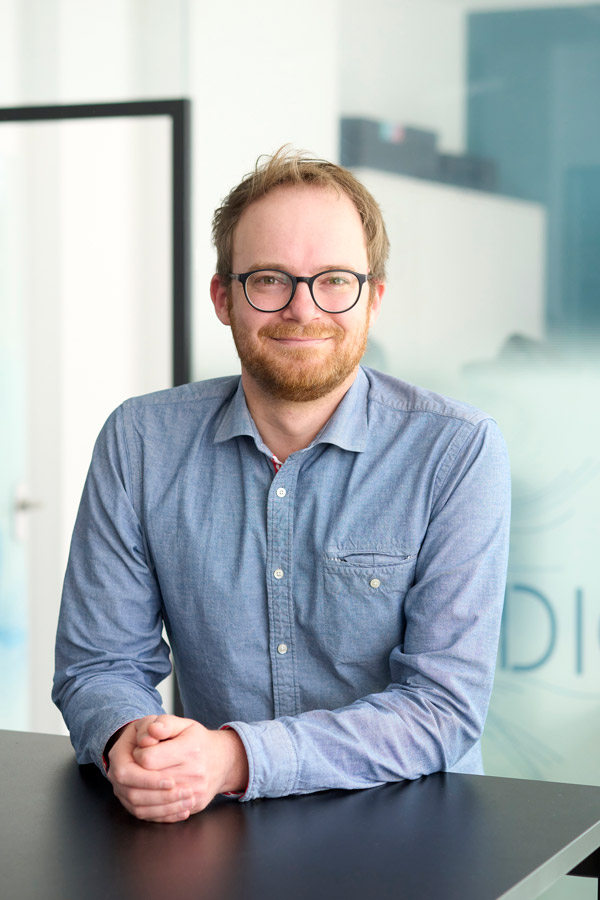
„Wir alle können so Erfahrungen mit neuen Technologien und Trends sammeln, um diese danach gegebenenfalls in den jeweiligen Fachbereich industriell einzuführen.“
DigiLab-Leiter von der MTU Aero Engine
„Das DigiLab ist der Ort, um digitale Innovationen in einem Experimentierbereich ganz praktisch auszuprobieren. Wir alle können so Erfahrungen mit neuen Technologien und Trends sammeln, um diese danach gegebenenfalls in den jeweiligen Fachbereich industriell einzuführen.“ So fasst DigiLab-Leiter Martin Roth von der MTU Aero Engines den Charakter des Digitalization Labs zusammen, das vor gut zwei Jahren am Standort in München entstanden ist.
Das DigiLab ist vollgepackt mit technischen Geräten: ein paar Rechner, einige größere Bildschirme, einen Flatscreen für Präsentationen sowie einige Datenbrillen und zusätzliche Peripheriegeräte. Links daneben ein Rack mit einer Sinumerik-CNC-Maschinensteuerung zur Simulation einer Fertigungsmaschine. Das Equipment bietet vielfältige Anwendungsbereiche und ermöglicht eine realitätsnahe Abbildung von Produktions- und Industrie-4.0-Themen: Vom Testen neuer Sicherheitswerkzeuge und Cloud-Anbindungen über die Digitalisierung älterer Maschinen mit IoT-Devices und Open-Source-Softwarelösungen bis hin zur Analyse von Fehlern, die im Produktionsumfeld auftreten.
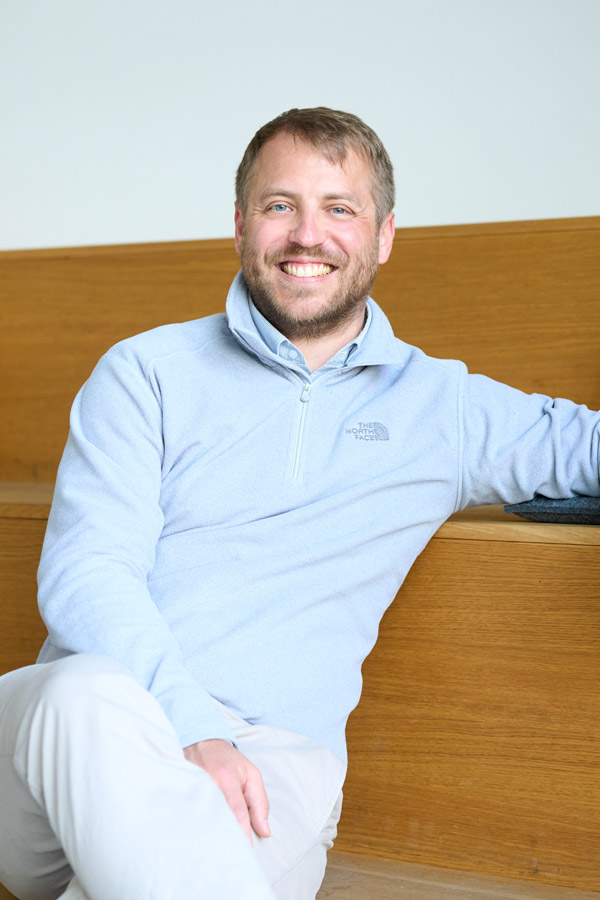
„Wir können hier quasi in einer Art abgesichertem Modus all das ausprobieren, was an Zukunftstechnologien auf dem Markt ist“
Stellvertretender DigiLab-Leiter von der MTU Aero Engine
Experimentieren in einer geschützten Umgebung
Allerdings kommt das DigiLab naturgemäß ohne die Anbindung an MTU-Systeme und ohne die Verwendung der Unternehmensdaten aus. Dadurch muss sich das DigiLab nicht an alle Vorschriften halten, die sonst in der MTU gelten – mit dem Ergebnis, dass Untersuchungen und Projekte flexibler und schneller umgesetzt werden können. Man arbeitet gegebenenfalls mit Dummy-Datensätzen und Simulationen. „Wir können hier quasi in einer Art abgesichertem Modus all das ausprobieren, was an Zukunftstechnologien auf dem Markt ist: Augmented Reality, Virtual Reality, aber auch viele Anwendungen mit künstlicher Intelligenz sowie rund um das Internet of Things (IoT)“, lässt Roths Stellvertreter Michael Bender einige Schlagworte fallen – um gleich zu relativieren, dass es dabei auch darum geht, ganz bodenständig Infrastruktur und IT-Ressourcen zur Verfügung zu stellen. So wolle man Techniken erlebbar machen – und zugleich Berührungsängste abbauen.
Martin Roth und sein Stellvertreter Michael Bender sind zum einen für das DigiLab verantwortlich und zum anderen Ansprechpartner für Interessierte. Ein weiterer Mitarbeiter kümmert sich um die IT-Sicherheit und die Infrastruktur „unter der Haube“. Das DigiLab steht sowohl für die MTU-Mitarbeiter als auch für externe Projektpartner:innen offen – vor Ort, virtuell und kostenfrei. Rund 60 Anfragen ganz unterschiedlicher Art hat das DigiLab in den letzten zwei Jahren erhalten: Mitarbeiter, die neue Soft- und Hardware im Arbeitsprozess ausprobieren wollen, Abteilungen, die mal etwas an der Maschinensteuerung testen wollen, bevor aufwendige Projekte angestoßen werden oder kostbare Zeit in der Produktion beansprucht wird – bis hin zu Betriebsräten, die eine Zukunftstechnologie mal in natura sehen und erklärt bekommen wollen, über die sonst nur diskutiert wird.
Unterstützung bei Tool für das Qualitätsmanagement
Der Pandemie zum Trotz kann das DigiLab in den zwei Jahren seines Bestehens bereits einige Erfolge vorweisen. Beispielsweise hat das Labor dabei unterstützt, ein neues System zum produktions- und standortübergreifenden Qualitätsmanagement einzuführen, eine einheitliche Qualitätsplattform, die nach und nach flächendeckend an sämtlichen MTU-Standorten zum Einsatz kommen wird. Das „Integrated Quality Planning“ (IQP) war eines der Projekte, die als Leuchtturmprojekt im Digitalisierungskontext ausgewählt wurden und die der MTU in Zukunft Effizienzgewinne bringen werden.
Dafür wurden verschiedene bestehende Softwarelösungen evaluiert und auf ihre konkrete Eignung für das Unternehmen getestet – eine Aufgabe, die in dieser großen Dimension eines Industriekonzerns mit umfassenden Vorgaben und Compliance-Regeln alles andere als trivial ist. „Im DigiLab wurde durch intensive Tests mit einer Demoversion des Anbieters sichergestellt, dass das IQS-Tool das kann, was wir uns davon versprechen, dass es für die Rahmenbedingungen des Unternehmens geeignet ist – und nicht zuletzt auch, wie gut es anpassbar ist.“ So habe man hier auch aus dem Homeoffice heraus testen können, „ein Glücksfall, um trotz der Pandemie den Projektzeitplan halten zu können“, so Projektleiterin Alexandra Wacker.
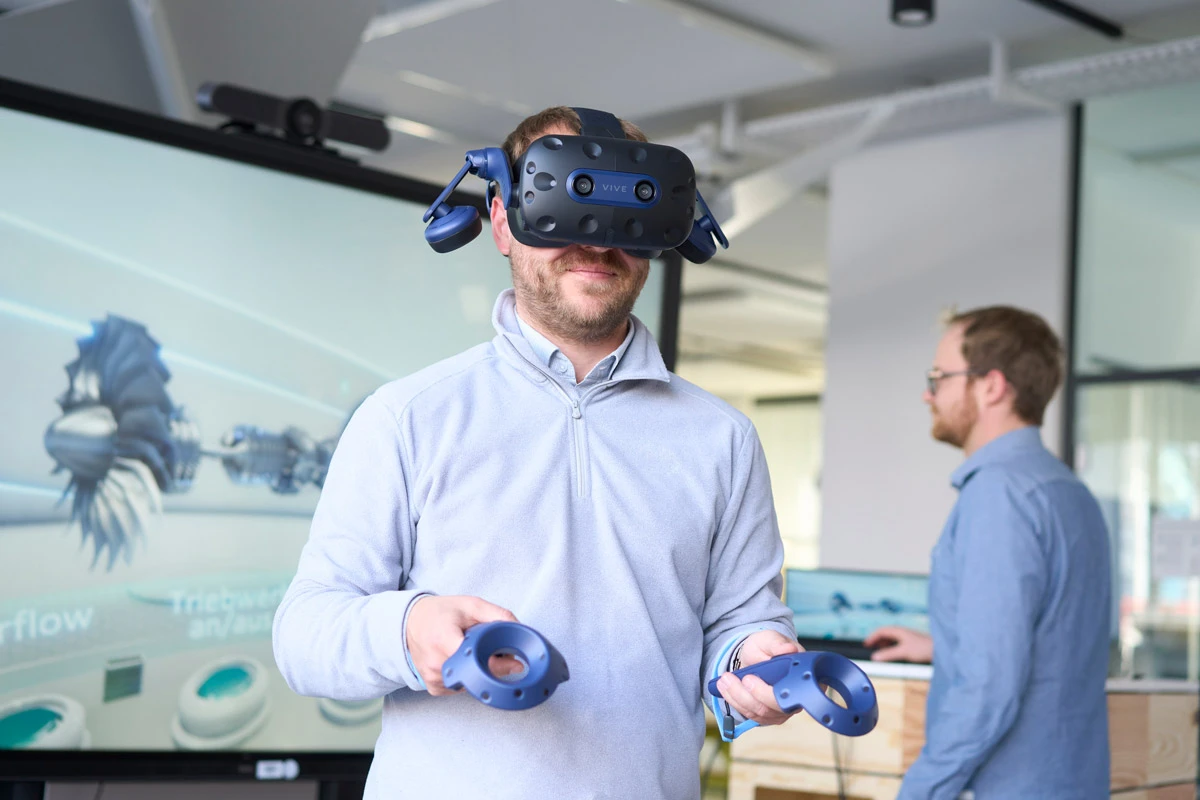
Fachbegriffe kurz erklärt
Der Begriff Künstliche Intelligenz (KI oder AI) bezeichnet Anwendungen, bei denen Maschinen dem menschlichen Denken ähnliche Leistungen erbringen, menschliches Handeln besser verstehen und Problemlösungskompetenzen entwickeln. Hierunter fallen maschinelles Lernen (Machine Learning) sowie Deep Learning, das mit Hilfe neuronaler Netze aktive komplexe Lernleistungen der Maschine ermöglicht.
Das Internet of Things (IoT) ist ein Sammelbegriff für vernetzte Geräte, Maschinen und Anlagen. Ziel ist es, automatisiert relevante Informationen und Betriebsdaten aus der realen Welt zu erfassen, diese miteinander zu verknüpfen und daraus einen Mehrwert zu generieren, um den Anwender zu unterstützen.
Beim Industrial IoT (IIoT) handelt es sich um die Variante, bei der nicht der einzelne Mensch, sondern Industrieanlagen im Mittelpunkt der Betrachtung stehen. Es geht dabei um Prozessoptimierung, Kosteneffizienz und um das Monitoring der Produktion.
Virtual Reality (VR) ermöglicht es den Nutzern, eine virtuelle 360 Grad Welt zu erleben, diese von allen Seiten zu betrachten, sich in ihr zu bewegen und mit dieser zu interagieren. Der Nutzer nimmt seine reale Umgebung hierbei nicht mehr wahr – er hat das Gefühl, in der virtuellen Welt vor Ort zu sein.
Bei Augmented Reality (AR) muss der Nutzer tatsächlich vor Ort sein, denn die reale Welt wird durch virtuelle Inhalte bloß angereichert. Über die betrachtete reale Welt werden in Echtzeit Textinformationen und Grafiken eingeblendet. Im Gegensatz zu VR wird daher bei AR die physische Realität weiterhin wahrgenommen.
„Aus unseren präventiven und reaktiven Qualitätsmethoden wollen wir zukünftig einen systemischen Abgleich zwischen entstandenen und vorhersehbaren Fehlern schaffen. So sollen Mitarbeiter Produktionsfehler einfach dokumentieren und künftig nachhaltig vermeiden können“. Die neue Software unterstützt die Fehlermöglichkeits- und Einflussanalyse (FMEA), eine Strategie, um potenzielle Fehler in Design- und Produktionsprozessen schon zu erkennen und zu bewerten, bevor sie überhaupt passieren. „Wir hatten hierfür in der Vergangenheit eine ganze Reihe von teilweise eigenentwickelten Tools und Workarounds, die sich ergänzten. Doch die Insellösungen werden nun durch eine umfassende Software aus einem Guss ersetzt”, erklärt Wacker.
Grundfunktionen der Triebwerkstechnik erklären
Nicht ganz so umfassend und umfangreich, dafür aber greifbarer, ist ein anderes Projekt, das gerade vor einigen Wochen in Zusammenarbeit mit der Ausbildung fertiggestellt wurde. In Zukunft werden MTU-Auszubildende im Bereich Triebwerkstechnik mit der animierten Darstellung eines modernen Turbofan-Triebwerks geschult. Möglich wird das mit Hilfe einer Virtual-Reality-Brille und dem dazugehörigen VR-Modell, das im Rahmen einer Masterarbeit mit Unterstützung des MTU-DigiLabs in eine Animation überführt wurde.
Das VR-Modell basiert auf der Bauweise des A320neo-Antriebs PW1100G-JM aus der modernen Pratt & Whitney GTF™ Triebwerksfamilie. Es geht dabei vor allem darum, die Grundfunktionen verständlich zu vermitteln, das technische Konzept dahinter plausibel zu machen. Auszubildende können das Triebwerk anschalten, den animierten Luftstrom und die drehenden Teile studieren, die Module einzeln herausnehmen. Neben einer Explosionszeichnung der einzelnen Bauteile stehen Infoboxen mit detaillierten technischen Daten zur Verfügung. Mit jeder Kopfbewegung passt sich das dreidimensionale Bild der Brille an und gibt weitere technische Details des Triebwerks preis.
Seit März kommt das Modell in der Lehrwerkstatt der MTU zum Einsatz. „Schon aus Kostengründen wäre es gar nicht möglich, ein solches reales Triebwerk in die Ausbildung zu stellen“, erklärt Ausbilder Markus Voag. Er sieht aber auch den didaktischen Mehrwert des 3D-Modells: „Wenn junge Menschen schon einmal die Vorteile einer solchen Technik erfahren haben, sind sie möglicherweise auch im späteren Berufsleben offener für Virtual Reality-Anwendungen.“
Für Martin Roth ist das Erlebbar-Machen des Triebwerks ein Paradebeispiel dafür, was das DigiLab im Kampf um die besten Köpfe leisten kann: „Das DigiLab ist angesichts des Fachkräftemangels in vielen Ingenieurfächern ein gutes Argument, um Nachwuchskräften die Attraktivität und Innovationskraft der MTU zu vermitteln und zu unterstreichen, dass wir ein spannender Arbeitgeber sind.“