innovation
New propulsion systems: Hydrogen is the future
Whether for sustainable alternative fuels, for carbon-free combustion in the gas turbine, or for the flying fuel cell—MTU Aero Engines has high hopes for hydrogen.
author: Denis Dilba | 6 mins reading time published on: 07.10.2020
author:
Denis Dilba
holds a degree in mechatronics, is a graduate of the German School of Journalism, and founded the “Substanz” digital science magazine. He writes articles about a wide variety of technical and business themes.
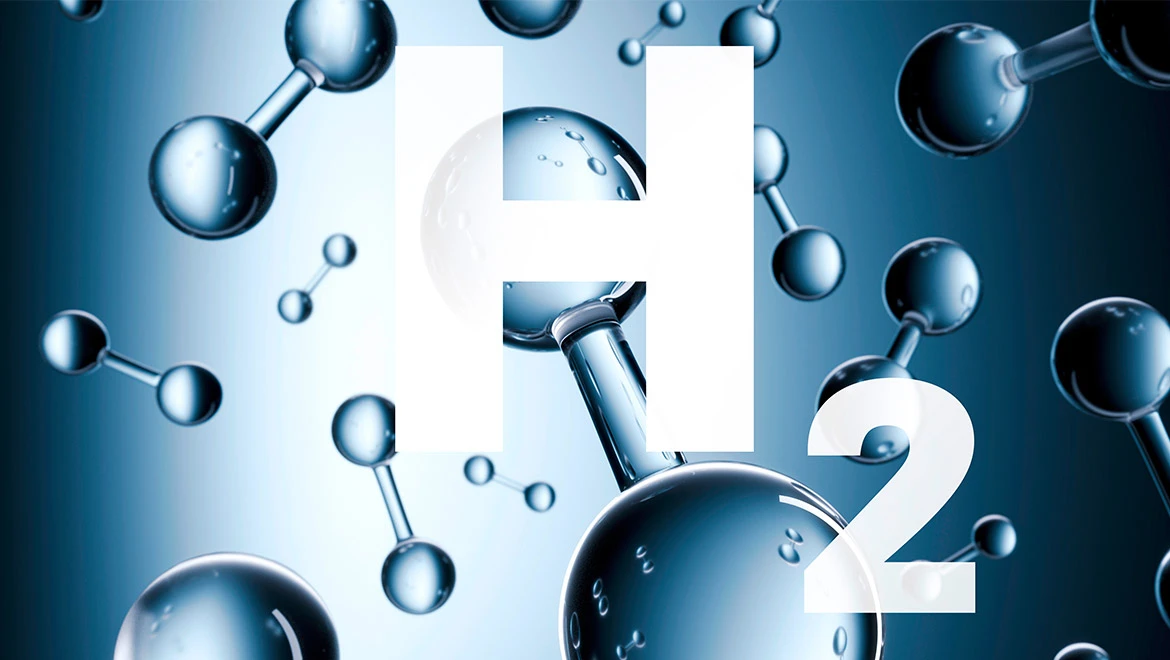
Designed back in the 1980s and sporting an elongated nose and two propeller-driven turboprop engines, the Dornier 228 certainly does not look like the future of aviation. However, if everything goes to plan and the aircraft takes off from the DLR German Aerospace Center’s Oberpfaffenhofen research airport in 2026, it will have a technical revolution on its wing: a fuel-cell powertrain specially developed for aviation applications. “As things stand today, the fuel cell in conjunction with sustainably produced hydrogen offers the greatest long-term potential for realizing virtually emissions-free aviation. That’s our vision for the future,” says MTU’s Chief Operating Officer Lars Wagner. “We believe that a fuel-cell system of this kind could in future provide sufficient power and range to be used as the primary propulsion system for regional, short- and medium-haul aircraft.”
- New propulsion systems: Hydrogen is the future
- Integrating hydrogen propulsion into aircraft
- Hydrogen’s journey to an aircraft fuel tank
- How hydrogen propulsion impacts the climate
It was only logical for MTU Aero Engines to become a development partner in the ambitious fuel-cell project. In August 2020, Wagner and Professor Rolf Henke, Executive Board Member for Aeronautics Research and Technology at the German Aerospace Center (DLR), signed a memorandum of understanding to develop the powertrain for a hydrogen fuel cell. Their objective is to equip the Dornier 228 with a high-performance fuel cell and an electrical, single-sided propeller engine with over 500 kW shaft output, and then put it through its paces in flight tests. Except for water and steam, the powertrain will be completely emissions-free. Up to 80 experts are lined up to work on this pioneering project. “The experience and data acquired in our collaboration, including in the fields of aviation regulation and certification, will prove vitally important to ongoing product development,” Wagner says.
©DLR
©DLR
©DLR
Dornier 228: The twin-engine turboprop aircraft will be equipped with a hydrogen-powered fuel cell and used as a flying testbed.
Improving fuel-cell performance is a must for aircraft applications
Barnaby Law, Chief Engineer Flying Fuel Cell at MTU, is confident that it’s possible to keep the highly ambitious development schedule on track. As fuel-cell technology has matured, driven primarily by the automotive industry, the power-to-weight ratio has improved steadily over the past ten years; at the same time, wider supplier chains have been established. “Overall, that’s a great basis to start further developing the technology for aerospace applications,” he says. Because fuel cells need to be made even more powerful if they are to become the primary propulsion system for aircraft carrying a larger number of passengers and flying over a certain range. Law believes there is no need to fear insurmountable obstacles: “Given that weight reduction is inherently more important in aviation than in the automotive industry, we already know some viable approaches to start optimizing fuel cells,” the fuel-cell specialist says.
Using lighter high-tech materials such as titanium, which is widely used in aviation, helps save weight for instance. It would also be feasible to use the expensive but performance-enhancing catalyst material platinum, even if this would slightly increase the load. But even with the additional costs this involves, the fuel cell is still relatively inexpensive compared to other climate-friendly solutions, Law explains. However, additional technologies are required to enable passenger aircraft powered by fuel cells to fly—first and foremost, the fueling system. Because hydrogen gas occupies such a large volume, even when stored in pressure tanks, aviation applications will use liquid hydrogen cooled to minus 253 degrees Celsius. “You can imagine the tank like a large vacuum flask,” Law says.
Flying Fuel Cell: MTU specialist Barnaby Law, Chief Engineer Flying Fuel Cell, explains the advantages of the fuel cell.
Other green, hydrogen-based technologies are available
However, this concept works only because aircraft use large amounts of hydrogen and flights follow a regular, planned schedule, Law explains. “If you put a liquid hydrogen tank in a car, drove to the airport and returned two weeks later, the tank would be more or less empty.” Aircraft, on the other hand, use the hydrogen before it has a chance to heat up and become gaseous. But there is a catch to the solution, as Law explains: “Looking at it from a purely physical perspective, liquid hydrogen has a volume four times that of kerosene for the same energy content.” In practice, however, this factor is slightly smaller and lies somewhere between three and four. In other words, the longer the route the aircraft flies, the larger the hydrogen tank required. “For distances of up to about 3,500 nautical miles, or just under 6,500 kilometers, it still makes sense to accommodate the tank, with modifications, in the current aircraft configuration. For longer routes, other solutions are better,” the fuel-cell expert explains.
“Potential options are to burn hydrogen directly in the gas turbines or to use sustainable aviation fuels (SAFs), which are produced using the power-to-liquid or sun-to-liquid process,” says Dr. Stefan Weber, Senior Vice President Engineering and Technology at MTU. In theory, it would be possible to make the switch now to burning hydrogen directly, he explains, because the necessary modifications to the geared turbofan (GTF) would be relatively easy to make. However, green hydrogen is not yet available in sufficient quantities. Alternatively, SAFs are attractive because they are “drop-in” fuels, as Weber explains: “Virtually no modifications need to be made in the engines, aircraft or other infrastructure to accommodate them.” These two technologies alone would offer some big advantages: burning hydrogen directly does not produce any CO2 emissions and also prevents particulate emissions. As for SAFs, they close the carbon cycle, thus immediately helping to achieve climate-neutral flight. As combustion of SAFs is cleaner, they also have the potential to generate fewer contrails.
The power-to-liquid process: Renewable energy is used to produce hydrogen, which is synthesized with carbon dioxide to form hydrocarbons and then processed into a liquid fuel.
Faster pace of development required for climate-friendly technologies
In a study published in June 2020, Clean Sky, the largest European research program, estimates that direct-burn hydrogen systems can reduce the global warming effect of flying by between 50 and 75 percent, and SAFs can reduce it by between 30 and 60 percent. The study’s authors believe that the fuel cell has the potential to reduce climate impact by 75 to 90 percent. “Essentially, we need all three technologies,” Weber says. While SAFs are the only option for operating the existing aircraft fleet in a more climate-friendly way, he explains, it is illogical to simply rely on a single solution if even better technologies are available in the long term. The same principle applies to the further development of the GTF. For example, if the water-enhanced turbofan (WET engine) concept is used in conjunction with SAFs, it would offer the potential to drastically cut emissions, even for long-haul aircraft. With this concept, water is evaporated in a heat exchanger in the engine and injected into the combustor. The exhaust heat is used to evaporate the water, which can significantly improve the propulsion system’s efficiency. Moreover, wet combustion prevents NOx emissions almost entirely.
So the evolutionary refinement of the GTF is not over yet either, Weber says, adding that there are still an extra few percent of fuel savings left to achieve. “If you take the Paris Agreement goals seriously and want to keep global warming below two degrees, you come to the conclusion that we need to develop all these greener technologies faster and more aggressively than before—and that’s exactly what we’re doing,” Weber says. “To play its role in this scenario, the flying fuel cell needs to be ready for large-scale deployment by 2040 at the latest.” Fuel-cell expert Law firmly believes that this is possible: “Then we’ll be able to fly away on vacation in an A320-category aircraft with a fuel-cell powertrain.”