innovation
Hydrogen’s journey to an aircraft fuel tank
Virtually emissions-free flight with hydrogen—for this vision to become reality, alongside development of the fuel cell, we also need to promote the building of hydrogen infrastructure.
author: Denis Dilba | 7 mins reading time published on: 05.05.2021
author:
Denis Dilba
holds a degree in mechatronics, is a graduate of the German School of Journalism, and founded the “Substanz” digital science magazine. He writes articles about a wide variety of technical and business themes.
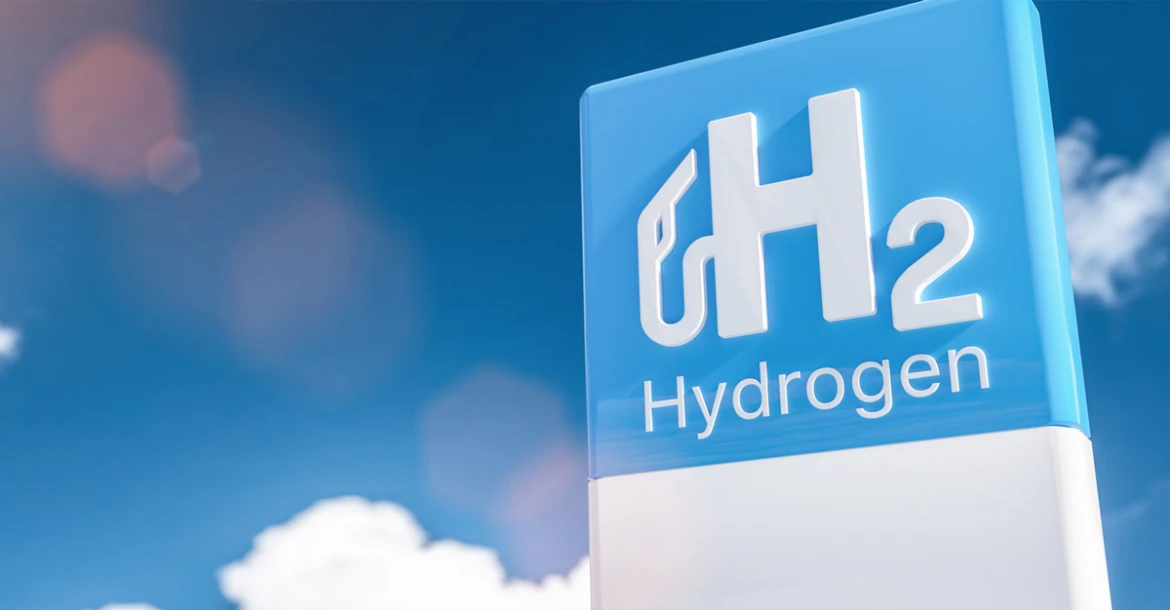
Standing at almost 150 meters tall and with a base of 230 by 230 meters, the Great Pyramid of Giza is not one of the Seven Wonders of the Ancient World for nothing. You would need just under three structures of this size to store around ten million metric tons of kerosene. In the years before the coronavirus pandemic, this was the amount of kerosene that was used for refueling at German airports every year. In a fictional future in which aircraft engines run exclusively on hydrogen, it would take nine of the pyramids to hold all the fuel. In fact, it is very likely that much more space would be needed, as hydrogen storage facilities are supposed to be double-walled with a vacuum in the cavity between them: the hydrogen needs to be kept in a liquid state at minus 253 degrees Celsius. However, storing the liquid hydrogen is just one challenge. The cryogenic fuel of the future would still need to be transported to the airports and then pumped into the aircraft fuel tanks.
- New propulsion systems: Hydrogen is the future
- Integrating hydrogen propulsion into aircraft
- Hydrogen’s journey to an aircraft fuel tank
- How hydrogen propulsion impacts the climate
“Aviation’s demand for hydrogen will be small at the beginning and increase gradually.”
Chief Engineer Flying Fuel Cell at MTU Aero Engines
“Luckily, we won’t need such volumes overnight. Aviation’s demand for hydrogen will be small at the beginning and increase gradually,” says Barnaby Law, Chief Engineer Flying Fuel Cell at MTU Aero Engines. And as far as we can tell today, not every aircraft that takes off in 2050 will have liquid hydrogen in its tank, Law says. For long-haul flights, the tanks would simply be too large. In order to get commercial aircraft with climate-friendly hydrogen propulsion into our skies, building up a suitable infrastructure is at least as important as developing the flying fuel cell and cryotanks and integrating these two components into aircraft. After all, even a hydrogen-powered zero-emissions aircraft is rather useless if it can’t be refueled. Although the industry doesn’t expect the first hydrogen aircraft to be with us before 2035, work has already begun on building the infrastructure.
“First of all, the hydrogen needs to be produced in sufficient quantities.”
Chief Engineer Flying Fuel Cell at MTU Aero Engines
From blue to green hydrogen
“First of all, the hydrogen needs to be produced in sufficient quantities,” Law says. And ideally it should be green—as only when hydrogen is manufactured by electrolysis with CO2-free “green” electricity generated from wind, solar or other renewables does it also cut overall CO2 emissions almost completely. “Green hydrogen is naturally the goal,” Law says, “but to allow only hydrogen produced using renewables at the beginning would ignore intractable global realities.” By no means all countries are in a good position to produce renewable power or have the money to import large quantities of green hydrogen, Law notes, adding that some countries possess large reserves of natural gas. “If these countries don’t participate because it’s cheaper for them to continue with kerosene made from fossil fuels while at the same time neglecting to invest in building up a hydrogen industry and the corresponding logistics chains, then not only will we have squandered a lot of potential for reducing CO2 emissions, but we will have also reinforced these countries’ dependency on fossil fuels.”
In Law’s view, this is why what is known as blue hydrogen should also be considered for use in air transport at the outset. Blue hydrogen starts out as “gray” hydrogen, which is produced from conventional natural gas. The difference is that with blue hydrogen, the CO2 emissions generated during production are captured, and not released into the atmosphere, in a pro-cess known as carbon capture and storage (CCS), Law explains. For a transition phase on the road to 100 percent green hydrogen, he finds this solution acceptable and sensible: “Compared to kerosene from fossil fuels, with blue hydrogen less CO2 escapes directly into the atmosphere, where it is much harder to control than if it’s compressed in a storage facility on the ground.” Moreover, the proportion of blue hydrogen will decrease sharply in the medium to long term, since green hydrogen will become increasingly more cost-effective as production rises. There are also other very interesting “blue alternatives” such as hydrogen produced through methane (natural gas) pyrolysis, whereby carbon is co-produced in solid form and not as gaseous CO2.
Airports need hydrogen in liquid form
According to a recent McKinsey study, in some regions of the world it will be possible to produce green hydrogen at prices that are competitive with gray and blue hydrogen by as early as 2030. The price of green hydrogen is determined first and foremost by the conditions at the production location: “A lot of wind and a lot of sun get more out of the electrolyzers and so increase cost-effectiveness,” explains Dr. Valentin Batteiger, Head of Alternative Fuels at the Munich-based Bauhaus Luftfahrt aviation research institution. As to getting the hydrogen to airports, meanwhile, the nature of the logistics chain depends on the local circumstances at the respective airport. Batteiger cites the example of Frankfurt Airport, where liquid hydrogen would most probably be transported on inland waterways to the nearest port on the river Main, with trucks transporting it from there to the airport in the initial phase up to 2050. Subsequently, as demand for hydrogen increases, a liquid hydrogen pipeline will most likely become economically viable, Law says. Fundamentally, though, he thinks logistics chains would not have to change very much. In other places, rail transport offers an attractive alternative.
Irrespective of the mode of transport, however, the hydrogen will generally be delivered to airports in cryogenic liquid form in cryotanks—because the hydrogen is needed there in liquid form and also because in its gaseous form hydrogen takes up too much volume. Transporting high-pressure hydrogen gas by road would likely take at least ten times more trucks. “Hydrogen liquefaction facilities are generally situated right at the hydrogen production site, as they need a large throughput in order to work cost-effectively, and they can be run there on cheap renewable power.” Returning to the example of Frankfurt Airport, there will be a big liquid hydrogen tank either directly at the port on the river Main or on the grounds of the airport itself. “Where such interim storage facilities are located, and how large they are, depends on many factors,” Batteiger says, “but often the space available at the airport will determine the decision.” At Hamburg Airport, to take another example, Jan Eike Blohme-Hardegen, Deputy Head of the airport’s Environment department, is already planning a hydrogen storage facility for the period after 2040: “From the initial idea through to completion, that’s very much a common timeframe.”
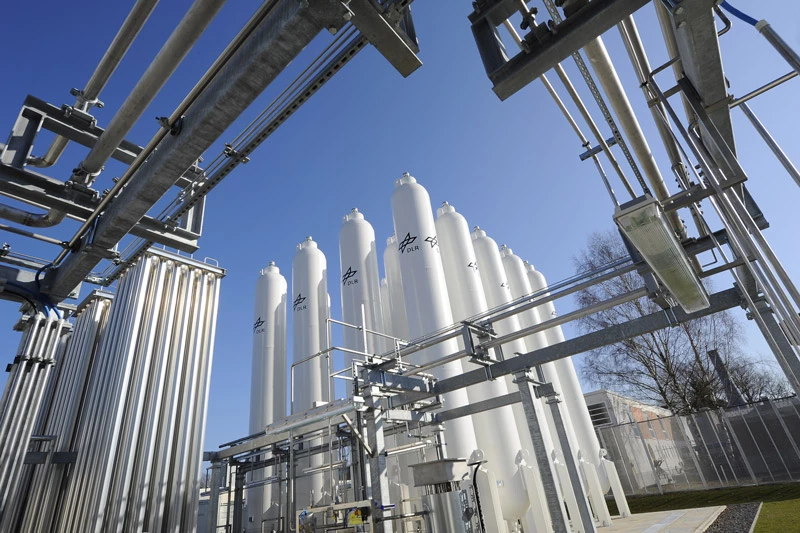
©DLR
Hydrogen supply system: large hydrogen storage systems can be used to reliably cover seasonal peaks in demand.
Reaching cost-effectiveness more quickly with higher hydrogen consumption
That being so, airports across Germany are already engaging with the subject of hydrogen fuel today. “With a hydrogen tank that is three—really closer to four—times the size of the current kerosene tank, we’re coming up against the limits of what’s feasible at our site,” Blohme-Hardegen says. That’s why he’s looking for alternatives, such as a pipeline: “We’re keen to be integrated into the hydrogen supply network, which in the coming decades will also reach the north of Hamburg.” This would mean that the hydrogen storage facility at Hamburg Airport can be smaller, as the hydrogen will be transported to the airport as a gas. Over the next few years there are already plans to build a smaller demonstrator tank with a test liquefaction facility, Blohme-Hardegen says. Hamburg Airport wants to use the boil-off gas—the gaseous phase that forms as a result of heating the liquid hydrogen in the tank—to run a portion of its fuel-cell airfield vehicles with zero emissions.
Increasing hydrogen consumption at the airport in this way makes a lot of sense, says Law. “The more hydrogen that is consumed, the faster the investments in the infrastructure will pay off.” In addition to airfield vehicles, there are also taxi and rental-car fleets and buses that could at least partially be run on hydrogen. Essentially, though, the investments will have to be amortized through the sale of hydrogen, Law says: “If you consume more than 400 kilograms of green hydrogen per day, then it already pays for itself.” This makes hydrogen a viable prospect even for smaller regional airports. As at larger airports, the procedures for refueling aircraft with hydrogen would hardly change, says Markus Bachmeier, Director Sales & Products at the gas specialist Linde: “Trucks with cryotanks will drive the hydrogen to the aircraft. Similarly to how it already works with hydrogen cars today, a hose is then connected to the tank.” The refueling process itself then takes—depending on the size of the aircraft—about the same amount of time as with kerosene.
“This would allow the aircraft to fly emissions-free from Munich to Dubai and back again in the future.“
Director Sales & Products at the gas specialist Linde
Gulf region can be hub for hydrogen air traffic
“It’s important to ensure that the same standards for the technology apply worldwide,” Bachmeier says. This is a precondition for being able to fully utilize the predicted range of the fuel cell aircraft of almost 4,600 kilometers and to refuel again at the destination airport. This would allow the aircraft to fly emissions-free from Munich to Dubai and back again in the future, Bachmeier says. Windy and sunny locations, of which there are many in the Gulf region, will be hubs for hydrogen air traffic, in the opinion of the Bauhaus Luftfahrt researcher Batteiger: “Since the local conditions are ideal for solar power plants, the production of green hydrogen can be set up directly beside the airport, which makes for cheaper, easier logistics.”