innovation
MTU und Fraunhofer: Forschungspartner für Industrie 4.0
Seit zwei Jahrzehnten entwickeln Forscher:innen bei Fraunhofer gemeinsam mit der MTU neue Technologien für Triebwerksbau und Instandhaltung und begleiten die Umsetzung in die Praxis.
Autorin: Monika Weiner | 5 Min. Lesezeit veröffentlicht am: 14.11.2022
Autorin:
Monika Weiner
arbeitet seit 1985 als Wissenschaftsjournalistin. Die Diplomgeologin interessiert sich vor allem für neue Entwicklungen in Forschung und Technik sowie deren gesellschaftliche Auswirkungen.
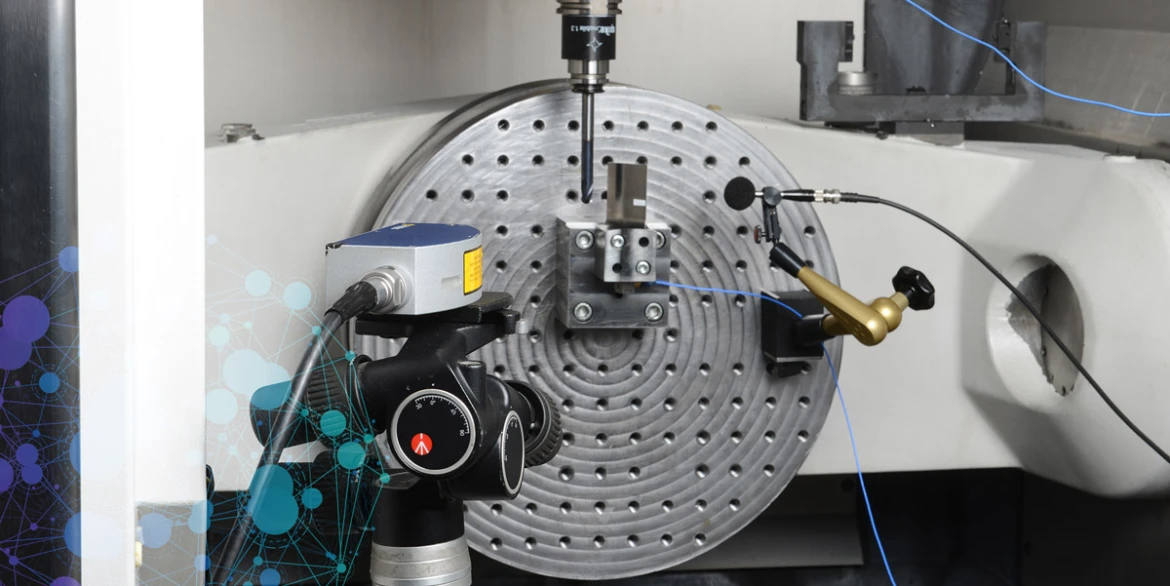
„Die Abläufe während eines fünfachsigen Fräsprozesses zu simulieren, war eine echte Herausforderung“, erinnert sich Dr. Sascha Gierlings, Leiter des Geschäftsbereichs Turbomaschinen am Fraunhofer-Institut für Produktionstechnologie IPT. „Wir können in eine solche Zerspanungsmaschine nicht hineinsehen. Sie ist eine Blackbox: Eingangsgröße ist eine Titanscheibe und etwa 40 bis 60 Stunden später kann die fertig bearbeitete Blisk entnommen werden.“ Um zu erforschen, was in der Blackbox vor sich geht, betreibt das Team der Abteilung Hochleistungszerspanung in der Maschinenhalle des Fraunhofer IPT in Aachen eine fünfachsige Fräsmaschine – das gleiche Modell, das die MTU Aero Engines in München verwendet. Damit wird dem Triebwerkshersteller geholfen, seine Hightech-Produktion abzusichern und weiterzuentwickeln.
- DLR und MTU: Gemeinsam forschen für eine emissionsfreie Luftfahrt
- MTU und Universitäten: Spitzenforschung für Zukunftstechnologien
- MTU und Fraunhofer: Forschungspartner für Industrie 4.0
Die MTU gehört weltweit zu den führenden Herstellern von Blisks. Blade Integrated Disks, kurz Blisks, sind Scheiben aus Titan oder Nickel, an deren Rändern aerodynamisch geformte Schaufeln integriert sind. Diese Verdichterrotoren, die die Luft vom Triebwerkseintritt her komprimieren, haben eine äußerst komplexe Geometrie. In München werden Titan-Blisks mit fünfachsigen Fräsmaschinen aus Rohteilen herausgearbeitet. Die Anforderungen an Materialeigenschaften, Oberflächen und die geometrische Präzision sind hoch und damit auch die Risiken: Sollte sich bei der Qualitätsprüfung herausstellen, dass eine Blisk Fehler aufweist, hätte ein teures Hightech-Bauteil unter Umständen nur noch Schrottwert.
„Selbst kleine Probleme in der Serienfertigung können teuren Ausschuss und damit einen enormen Leidensdruck erzeugen. Die Ursache eines Defekts, einer Unebenheit oder eines Risses muss daher möglichst schnell gefunden und abgestellt werden“, erklärt Dr. Ulrich Retze, Leiter Simulation von Fertigungsprozessen bei der MTU. Doch das Wechselspiel der Kräfte zwischen Werkzeug und Werkstück ist in einer fünfachsigen Fräsmaschine unvorstellbar kompliziert. Retze und sein Team arbeiten daher mit Computerprogrammen, um Ursache-Wirkungs-Zusammenhänge sichtbar zu machen. „Dank dieser Simulationen können wir jetzt in der Produktion ‚Trouble Shooting‘ betreiben und – wenn es Probleme gibt – schnell mögliche Fehlerquellen identifizieren“, betont der Ingenieur. Entwickelt wurde das Programm im Projekt „Virtuelle Fräsprozesse“, in dem die MTU seit zwei Jahren mit dem Fraunhofer-Institut für Produktionstechnologie IPT zusammenarbeitet.
Wenn die fünfachsige Fräsmaschine im Dienst der Wissenschaft eine Blisk fertigt, kann Pascal Kienast von seinem Büro aus jeden Schritt mitverfolgen. In Echtzeit. Drei Jahre hat der Fraunhofer-Ingenieur an den Algorithmen gearbeitet, mit deren Hilfe sich die Informationen aus der Maschine – beispielsweise die Größe und Position des Werkstücks, der Materialabtrag, die genaue Bewegung von Bauteil und Werkzeug – virtuell darstellen lassen. Mit ein paar Klicks kann Kienast sichtbar machen, wo welche Kräfte auftreten, wie und wo sich Schwingungen verstärken, welche Folgen Defekte an der Spindel oder in einem Lager haben und ob der Zustand der Blisk den vorgegebenen Werten entspricht. Die Ergebnisse dieser aufwändigen Forschungsarbeit nutzt jetzt Retzes Team in München.
Und das sei erst der Anfang, betont Gierlings: „Im ersten Teil des Projekts haben wir mit Hilfe der Modellierungen Zusammenhänge sichtbar gemacht und können so die Prozessstabilität unserer Fertigung verbessern. Im nächsten Schritt wollen wir die Software-Tools so weiterentwickeln, dass sie uns effizient bei der Prozessauslegung für neue Bauteilgeometrien unterstützen.“
Wie Simulationen Zeit und Geld sparen
Bisher ist die Umstellung der Fertigung auf eine neue Blisk-Generation aufwändig und mit hohen Kosten verbunden: „Man muss durch Trial and Error die richtigen Einstellungen finden. Dabei entsteht zwangsläufig Ausschuss“, sagt Retze. „Wenn es uns gelingt, die Maschinensteuerung schon im Vorfeld virtuell zu optimieren, können wir viel Zeit und Geld einsparen.“
Bis zum Ende des Projekts, in fünf Jahren, wollen die Ingenieur:innen das Simulationsprogramm sogar noch einen Schritt weiter entwickeln: „Langfristig wird es möglich sein, immer mehr Daten der Fräsmaschinen zu nutzen, um die Serienproduktion zu überwachen, zu steuern und auf diese Weise die Prozessstabilität zu steigern“, prognostiziert Gierlings.
Prototypen-Entwicklung: Im Technikum Blisk entwickeln die MTU und das Fraunhofer IPT die Blisk der Zukunft.
Fast zwei Jahrzehnte gemeinsame Forschungsgeschichte
Die Entwicklung des Virtuellen Fräsprozesses ist nur eines von vielen Kooperationsprojekten: „Die MTU und das Fraunhofer IPT arbeiten schon seit 2003 zusammen und betreiben gemeinsam seit 2017 das „Technikum Blisk“ für Prototypen-Entwicklung“, berichtet Ann-Kathrin Jung, Programmkoordinatorin Technologie-Partnermanagement bei der MTU. „Im Laufe der Jahre kamen dann immer mehr Projekte auch mit anderen Fraunhofer-Instituten dazu.“
So haben Forscher:innen am Fraunhofer-Institut für Lasertechnik ILT untersucht, wie sich Turbinenteile mit Hilfe des Verfahrens Laser Powder Bed Fusion (L-PBF) fertigen lassen: Bei diesem Verfahren wird das Werkstück – wie in einem 3D-Drucker – schichtweise aus Metallpulver aufgebaut und mit einem starken Laserstrahl verschmolzen. Und am Dresdner Fraunhofer-Institut für Fertigungstechnik und Angewandte Materialforschung IFAM entstanden neue, besonders hitzebeständige Titan-Aluminium-Legierungen für den Triebwerksbau. Auf Basis dieser Zusammenarbeit wird derzeit am Hochtemperatureinsatz von IN718 (Nickelbasislegierung) gearbeitet.
Seit Juni 2022 zählt die Fraunhofer-Gesellschaft zu den Centers of Competence (CoC) der MTU und ist damit ein strategischer Forschungs- und Entwicklungspartner. „Das Besondere bei den Fraunhofer-Instituten ist, dass sie nicht nur wichtige Erkenntnisse aus der Forschung beisteuern, sondern diese auch gemeinsam mit unseren Ingenieur:innen in die Praxis umsetzen“, betont Jung. Das neue CoC bekam daher auch den Namen „Industrialization“. „Das CoC Industrialization wertet die Zusammenarbeit zu einer strategischen Forschungspartnerschaft auf dem Gebiet von Produktions- und Industrialisierungstechnologien auf. Konkret will die MTU langfristig und kontinuierlich Forschungs- und Entwicklungsvorhaben durch das CoC begleiten lassen sowie praxisrelevant und zielorientiert die Forschung für zukünftige Triebwerksgenerationen vorantreiben“, heißt es im Vertrag.
Die Fraunhofer Gesellschaft
Die Fraunhofer-Gesellschaft mit Sitz in Deutschland ist die weltweit führende Organisation für anwendungsorientierte Forschung. Mit ihrer Fokussierung auf zukunftsrelevante Schlüsseltechnologien sowie auf die Verwertung der Ergebnisse in Wirtschaft und Industrie spielt sie eine zentrale Rolle im Innovationsprozess.
Die 1949 gegründete Organisation betreibt in Deutschland derzeit 76 Institute und Forschungseinrichtungen. Mehr als 30.000 Mitarbeiter:innen, überwiegend mit natur- oder ingenieurwissenschaftlicher Ausbildung, erarbeiten das jährliche Forschungsvolumen von 2,9 Milliarden Euro. Davon fallen 2,5 Milliarden Euro auf den Bereich Vertragsforschung.
Dialogforen für neue Projekte
Um neue Felder der Zusammenarbeit zu eruieren, finden jetzt regelmäßig Dialogforen statt, bei denen sich Expert:innen von MTU und Fraunhofer austauschen. Beim ersten dieser Treffen 2021 stand das Thema Maintenance, Repair and Overhaul, kurz MRO, im Mittelpunkt. Die Instandhaltung von Triebwerken ist zeit- und arbeitsintensiv – Bauteile müssen zerlegt, inspiziert und wieder zusammengebaut werden. Gemeinsam mit der Smart Maintenance Community, kurz SMC, einem Zusammenschluss von einem Dutzend Fraunhofer-Instituten, will die MTU jetzt untersuchen, wie sich die Instandhaltung der Module mit Hilfe digitaler Techniken effizienter und wirtschaftlicher gestalten lässt.
Bei den Treffen in diesem Jahr stand auch das Themenfeld Flying Fuel Cell auf der Tagesordnung. Diskutiert wurden hier neue Fertigungstechniken und -verfahren, Möglichkeiten der Prozessoptimierung und der Qualitätssicherung sowie spezielle Montagetechnologien, um die Leistung fliegender Brennstoffzellen zu verbessern.
„Die Gespräche in den Dialog-Foren haben gezeigt, dass es über die bisherigen Projekte hinaus zahlreiche Kooperationsmöglichkeiten gibt, von denen die MTU profitieren kann. Das Spektrum reicht von der Entwicklung neuer Materialien und Antriebstechnologien bis hin zu einer effizienteren Instandhaltung von Triebwerken“, resümiert Programmkoordinatorin Ann-Kathrin Jung.