aviation
Triebwerksinstandhaltung passgenau
Triebwerke sind wertvolle Investitionsgüter. Weltweit werden daher jedes Jahr Milliarden US-Dollar in die Reparatur und Instandhaltung investiert. Tendenz steigend: Die Zunahme des Luftverkehrs und neue digitale Techniken machen die Engine-Maintenance zu einem Wachstumsmarkt.
Autorin: Monika Weiner | 11 Min. Lesezeit veröffentlicht am: 01.05.2017
Autorin:
Monika Weiner
arbeitet seit 1985 als Wissenschaftsjournalistin. Die Diplomgeologin interessiert sich vor allem für neue Entwicklungen in Forschung und Technik sowie deren gesellschaftliche Auswirkungen.
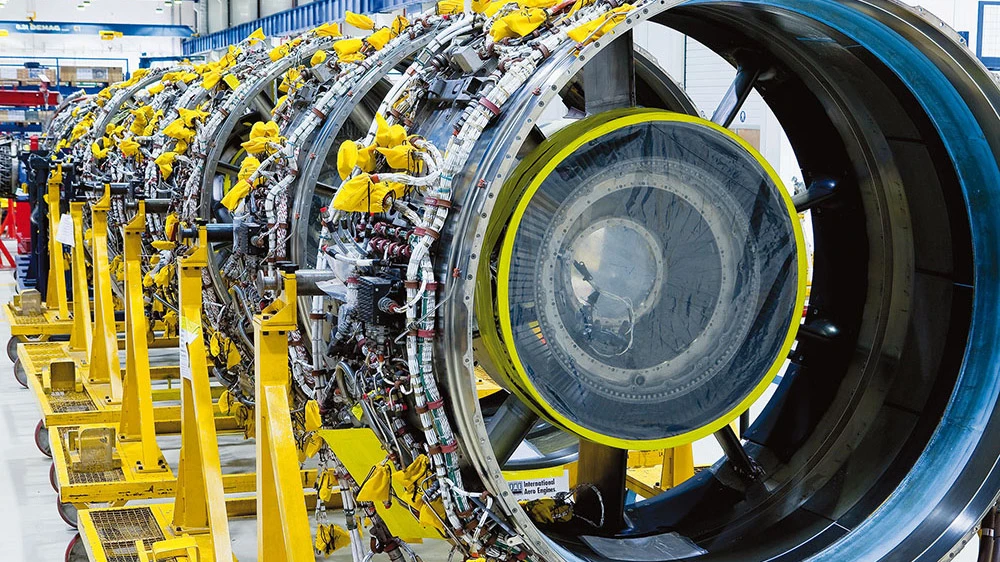
Zu alt zum Fliegen? Triebwerke kommen nur in die Jahre. „Technologisch gibt es keine Altersgrenze“, sagt Leo Koppers, SVP Marketing and Sales bei der MTU Maintenance. „Wir sehen das am V2500. Mittlerweile sind manche dieser Triebwerke schon fast 30 Jahre alt und immer noch voll funktionstüchtig.“
Dafür muss allerdings einiges getan werden, denn natürlich nutzen sich Triebwerke im Flugbetrieb ab. Strenge Sicherheitsbestimmungen schreiben Instandhaltungsintervalle vor; in manchen Einsatzgebieten verschleißen die Bauteile zudem schneller: Fast 25 Milliarden US-Dollar wurden 2015 weltweit für Instandhaltung, Reparaturen und Überholung von Triebwerken – Maintenance, Repair and Overhaul, kurz MRO – ausgegeben. Für 2025 werden 46 Milliarden US-Dollar prognostiziert. Das ist viel Geld für die Airlines, die wegen der großen Konkurrenz unter Kostendruck stehen. Warum es sich für sie dennoch lohnt, immer mehr in ein ewiges – oder zumindest langes – Leben ihrer Triebwerke zu investieren, weiß Dr. Andreas Sizmann, Experte für Zukunftstechnologien und Ökologie der Luftfahrt beim Bauhaus Luftfahrt: „Die Airlines wollen in erster Linie die Verfügbarkeit der Flotte sicherstellen, denn jeder Ausfall ist mit hohen Verlusten verbunden. Gleichzeitig verfolgen sie das Ziel, die Kosten für die Instandhaltung möglichst niedrig zu halten.“
Jeder Triebwerkseigner hat andere Anforderungen
Wie viel ein Flugzeughalter bereit ist auszugeben, hängt von vielen Faktoren ab: Da sind einmal die äußeren Zwänge, wie die vom Gesetzgeber vorgeschriebenen Instandhaltungsintervalle, die eingehalten werden müssen. Wichtig ist aber auch, wie alt die Triebwerke sind, und ob die Maschinen Eigentum der Airline sind und langfristig auch bleiben sollen, oder ob sie geleast sind. Bei eigenen Flugzeugen kann die Airline selbst den Zeithorizont des Flugbetriebs bestimmen. Leasingfirmen, die daran interessiert sind, den Wert der Maschinen zu erhalten, fordern unter Umständen bestimmte Wartungsarbeiten und engere Instandsetzungsintervalle. Fazit: Der Markt ist riesig, aber jeder Kunde ist anders.
Und auch bei den Anbietern von MRO-Services gibt es große Unterschiede: Da sind einmal die Original Equipment Manufacturers (OEMs) – etwa GE Aviation, Rolls-Royce, Pratt & Whitney. Die Originalteile, die sie bieten, sind teuer, erhöhen jedoch den Werterhalt. Für einen Halter, der sein Flugzeug nach zehn bis 15 Jahren noch weiterverkaufen will, ist das ein wichtiges Kriterium. Umfassende Serviceleistungen bieten aber auch die unabhängigen Anbieter wie die MTU Maintenance, die Originalteile einbauen können, aber nicht müssen. Und doch gibt es Gemeinsamkeiten: Alle MRO-Anbieter entwickeln ständig neue Technologien, mit denen sich Instandsetzungsarbeiten optimieren und – wenn sie schon nicht vermeidbar sind – möglichst schnell durchführen lassen.
„Ein vielversprechender Ansatz ist die elektronische Triebwerksüberwachung“, berichtet Koppers. „Dabei messen Dutzende von Sensoren während des Flugs Abgas- und Triebwerkstemperatur, Sprit- und Ölverbrauch, Vibrationen sowie den Druck in Verdichter, Brennkammer und Turbinen. Die Daten können nach dem Flug ausgelesen oder vom Bordcomputer über Satellit zur Bodenstation gefunkt und dort sofort ausgewertet werden. Auf diese Weise lassen sich technische Probleme frühzeitig erkennen, außerdem kann man die notwendigen Instandsetzungsarbeiten besser planen.“ So können die Shop Visits an die tatsächlichen Anforderungen angepasst werden: Ist ein Triebwerk etwa überwiegend in Wüstengegenden unterwegs, wo viel Sand und Staub in der Luft ist, muss es früher in den Engine Shop als eines, das in Nordeuropa oder Nordamerika geflogen wird.
Einsicht Zwei Mitarbeiter der MTU Maintenance Hannover untersuchen ein V2500-Triebwerk mit dem Boroskop.
Immer länger am Flügel
„Insgesamt geht der Trend hin zu immer längeren Wartungszyklen“, betont Koppers. „Das liegt am verbesserten Monitoring, aber auch daran, dass die Technik immer zuverlässiger wird: Das V2500 brauchte bis zu fünf Shop Visits über den Lebenszyklus, neue NextGeneration-Triebwerke wie das PW1100G-JM oder das LEAP werden tendenziell mit drei auskommen können.“ Und weniger Shop Visits bedeuten weniger Standzeiten und geringere Kosten: Für einen kompletten Service muss das Triebwerk ausgebaut und gegen einen Ersatzmotor ausgetauscht werden. Das dauert mindestens acht Stunden. Danach bringt ein Flugzeug das zu überholende Triebwerk in den Engine Shop. Dort stehen Mechaniker bereit, die die Bauteile reinigen, prüfen und im Bedarfsfall ersetzen (siehe So läuft die Instandhaltung eines Triebwerks). Das kann Wochen dauern und kostet Millionen für hochwertige Materialien und Ersatzteile. Viele der komplexen Arbeiten, die dabei anfallen, sind zudem nicht nur technologisch anspruchsvoll, sondern auch reine Handarbeit. Damit ist jeder eingesparte oder in die Zukunft verschobene Shop Visit ein Gewinn.
Beliebig hinauszögern kann man sie freilich nicht: Weil einzelne Komponenten wie Schaufeln und Dichtsegmente extrem beansprucht werden, sinkt im Laufe der Zeit die Leistung des Triebwerks. Mit abnehmendem Wirkungsgrad steigt die Verbrennungstemperatur beziehungsweise der Kraftstoffverbrauch, erkennbar an der höheren Abgastemperatur, im Fachjargon Exhaust Gas Temperature (EGT). Die abnehmende Differenz zwischen der zugelassenen Maximaltemperatur und der Temperatur im Flugbetrieb, die EGT-Margin, zeigt die Notwendigkeit und den Erfolg von Instandsetzungsarbeiten an. Um sie und damit den Wirkungsgrad wieder zu erhöhen, muss beim Shop Visit etwa das Spaltmaß zwischen Schaufel und Einlaufbelag in der Hochdruckturbine verringert werden. Dazu dienen Beläge an der Gehäuseinnenseite oder das Auflöten einer Panzerung auf die Schaufelspitzen.
Kostenoptimierung bei älteren Trieb­werken
Sind die ersten Shop Visits schon teuer, so steigen die Kosten rasant, wenn die Flugzeuge nach 25 bis 30 Jahren das Ende ihres Lebens erreichen. MRO-Provider wie die MTU Maintenance bieten daher für den so genannten Mature Engine Service ein ganzes Portfolio von Lösungen an, die nicht mehr lohnende Instandhaltungskosten vermeiden: Reparatur, Einbau neuer oder gebrauchter Ersatzteile, Zerlegung und Weiterverwertung sowie Leasing von Ersatztriebwerken. Der Kunde hat die Wahl.
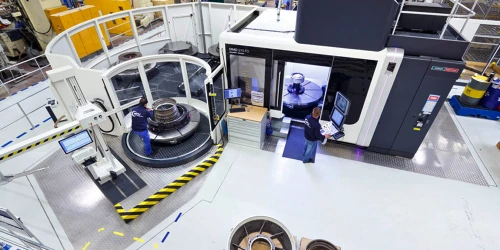
Aus alt mach neu – Reparaturverfahren im Überblick
Reparieren ist meistens günstiger, als ein Bauteil neu herzustellen. Deshalb hat die MTU Maintenance deutlich in die Entwicklung von Reparaturverfahren investiert - mit erstaunlichen Ergebnissen.
„Wirklich entscheidend sind allerdings nicht kurzfristige Einsparungen, sondern der langfristige Erfolg“, betont Koppers: „Wir haben bei der MTU Maintenance ein Konzept der Lifecycle Optimization entwickelt, das die Ökonomie bei der Instandhaltung, den Erhalt des Werts und die Kundenzufriedenheit umfasst. Wir versuchen in jedem Einzelfall die optimale Lösung zu finden.“ Bei einem Triebwerk, das noch zehn Jahre am Flügel bleiben soll, empfiehlt sich vielleicht der Einbau von Originalteilen; bei einem anderen, das nur noch ein paar Tausend Starts und Landungen vor sich hat, sind gebrauchte, reparierte Ersatzteile möglicherweise ausreichend. „Unser Vorteil als Independent-Anbieter ist es, dass wir Originalersatzteile anbieten können, aber nicht müssen. Gleichzeitig helfen wir dem Kunden sicherzustellen, dass das Triebwerk einsatzbereit ist, solange es benötigt wird, und sich am Ende noch für einen möglichst guten Preis verkaufen lässt.“
Trends für die Zukunft
Allen Optimierungsstrategien zum Trotz verschlingt die Maintenance aber immer noch Milliarden – in den letzten Jahren sind die Kosten für die Shop Visits sogar noch gestiegen, weil die Antriebe immer komplexer werden. Betrugen die Instandhaltungskosten für Triebwerke 2007 laut der International Air Transport Association (IATA) noch 42 Prozent der Gesamtwartungskosten, so waren es 2016 bereits 50 Prozent.
Bauhaus Luftfahrt-Forscher Sizmann ist überzeugt: „Der Kostendruck, unter dem die Airlines stehen, wird neue Analyse- beziehungsweise Prüfverfahren hervorbringen. Diese werden dabei helfen, dass Triebwerke künftig noch länger am Flügel bleiben können und sich viele Arbeiten während der normalen Standzeiten direkt am Flughafen durchführen lassen.“ Die Triebwerks-OEMs stellen sich bereits auf diesen Wandel ein, sagt Koppers: „Die Vermeidung von Maintenancekosten wird schon in die Triebwerksentwicklung miteinbezogen, etwa durch modularen Aufbau, um Reparaturen zu vereinfachen, weil man ganze Einheiten austauschen kann.“
Fly-by-hour-Agreement oder Time-and-Material-Agreement?
Maintenance-Unternehmen bieten für Shop Visits verschiedene Servicemodelle an, die dem Kunden helfen, die Kosten überschaubar zu halten.
„In Zukunft werden auch virtuelle Techniken helfen, Kosten und Zeit zu sparen“, prognostiziert Sizmann. „Zurzeit wird zum Beispiel erforscht, welches Potenzial in der Big-Data-Analyse liegt. Kostenvorteile könnten sich dadurch ergeben, dass sich in Zukunft mit Hilfe eines tief integrierten Sensornetzwerks der Zustand eines Triebwerks während des normalen Betriebes immer besser erfassen und auswerten lassen wird, ohne dass es ausgebaut und zerlegt werden muss. Interessant sind auch die Möglichkeiten der „Augmented Reality“, der computergestützten Erweiterung der Realitätswahrnehmung. Die Überlagerung von computergenerierten Zusatzinformationen in Datenbrillen oder Displays kommt in vielen Bereichen von Konstruktion, Montage und Instandhaltung bereits zur ersten Anwendung und hat ihr Potenzial noch nicht ausgeschöpft.“ Vielversprechend sei zudem die additive Fertigung mit für die Luftfahrt zertifizierten 3D-Druckern, mit deren Hilfe sich Ersatzbauteile vor Ort, ohne aufwändige Lagerhaltung oder Logistik fertigen ließen.
Noch ist vieles davon Zukunftsmusik. Aber wer weiß: Vielleicht werden Instandhaltung, Reparatur und Überholung von Triebwerken eines Tages wirklich so einfach, flexibel und schnell, dass sie sich an jedem Flughafen durchführen lassen.