good-to-know
Kurz erklärt: Turbinenzwischengehäuse
Turbinenzwischengehäuse sind anspruchsvolle Triebwerkskomponenten. Der AEROREPORT erklärt ihre Aufgabe und zeigt die innovativen Technologien, die dahinter stecken.
Autor Isabel Henrich, Tobias Weidemann | 4 Min. Lesezeit veröffentlicht am: 01.08.2023
Autor
Isabel Henrich ist studierte Politologin und Kommunikationswissenschaftlerin. Bei der MTU steuert sie den redaktionellen Prozess des AEROREPORTs und ist zuständig für die Konzeption und Entwicklung der Inhalte.
Tobias Weidemann ist seit mehr als 20 Jahren als Journalist und Content-Berater tätig. Er berichtet über Technik- und Wirtschaftsthemen, oft mit Schwerpunkt auf Business-IT, Digitalisierung und Zukunftstechnologien.
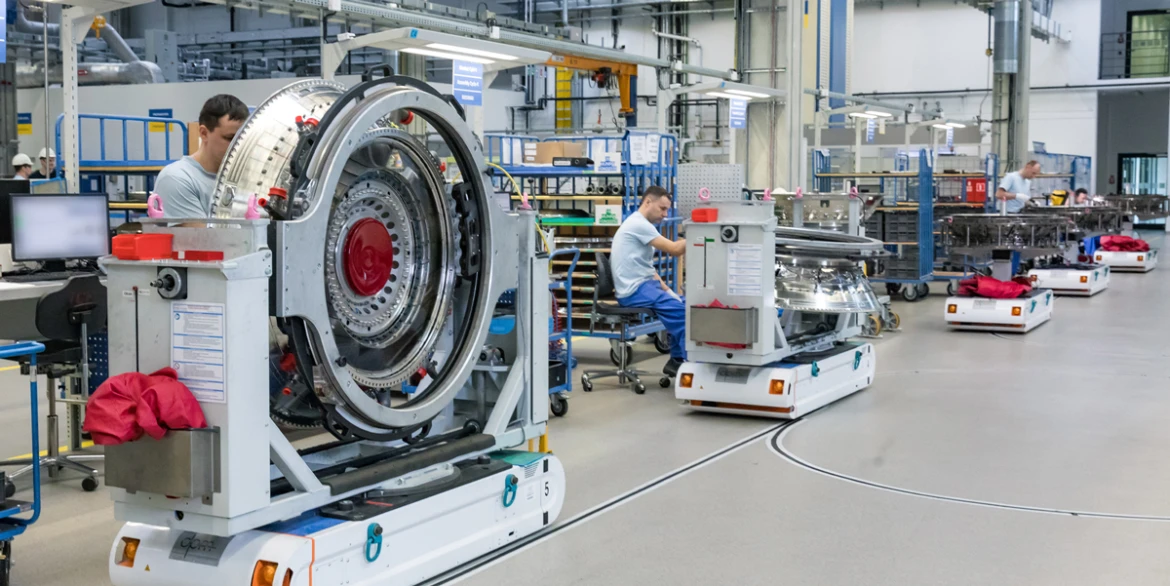
Die MTU entwickelt und fertigt Turbinenzwischengehäuse (Turbine Center Frame = TCF) für Antriebe von Langstreckenflugzeugen. Am Standort in München und bei der MTU Aero Engines Polska entstehen die TCFs des GP7000 (Airbus A380), des GEnx (Boeing 787 Dreamliner und Boeing 747-8) und des GE9X, dem Exklusivantrieb der Boeing 777X.
Die Aufgabe des Turbinenzwischengehäuses im Triebwerk
Turbinenzwischengehäuse bilden den Übergangskanal für das von der Hochdruckturbine in die Niederdruckturbine strömende Heißgas und haben vielfältige Aufgaben: Sie müssen die heißen Gase, die die Hochdruckturbine mit einer Temperatur von über 1.000 Grad Celsius verlassen, mit möglichst geringen aerodynamischen Verlusten zur Niederdruckturbine leiten. Beide Turbinen gilt es mit Kühlluft zu versorgen, deren Zufuhr durch das Turbinenzwischengehäuse erfolgt. Als tragende Struktur nimmt das TCF das hintere Lager der Hochdruckwelle auf und trägt damit maßgeblich zur Spalthaltung in der Hochdruckturbine bei. Gleichzeitig muss die Ölzu- und -abfuhr durch die heiße Struktur sichergestellt werden. Zudem gilt es, große Lasten abzufangen, die zum Beispiel im Falle eines Fan Blade Out, dem Verlust einer Fan-Schaufel, entstehen.
In Summe ist das TCF im Betrieb extremen Belastungen ausgesetzt, wie etwa hoher mechanischer Beanspruchung und hohen Temperaturen. Aufgrund der vielfältigen Aufgaben sind die Anforderungen an die Fertigungsgenauigkeit und Umfangssymmetrie groß.
Meisterstück für das GE9X
Im Juli 2014 hat die MTU die Entwicklungs-, Fertigungs- und Instandhaltungsverantwortung für das TCF im GE9X übernommen. Dieses Triebwerk wird ab 2025 exklusiv die Boeing 777X in die Luft bringen und im Verhältnis von Kraftstoffverbrauch zu Schubkraft das effizienteste Triebwerk sein, das GE jemals auf den Markt gebracht hat. Das GE9X-TCF ist das technologisch anspruchsvollste TCF der MTU.
Innovative Technologien im GE9X-TCF
Basierend auf der Grundarchitektur des GEnx-TCF gibt es beim GE9X-TCF umfangreiche Optimierungen, die Gewicht, Lebensdauer und Herstellbarkeit weiter verbessern. Unter anderem wurden Bauweisen durch additive Fertigung optimiert. Neu sind die ersten voll bionisch ausgelegten Bauteile der MTU: Halterungen für Ölleitungen, sogenannte Brackets. Hier wird eine Gewichtseinsparung von 35 Prozent erreicht. Pro Triebwerk werden drei ins GE9X montiert.
Zukünftige Entwicklungen
Bereits heute bereitet sich die MTU gewissenhaft auf weitere mögliche TCF-Anwendungen vor: Gearbeitet wird an einer weiter verbesserten aerodynamischen Auslegung sowie dem besseren Verständnis der Temperaturverteilung auf den Bauteiloberflächen unter Berücksichtigung der Kühlluftströme.
In enger Kooperation mit GE fanden dazu bei der TU Graz detaillierte experimentelle Untersuchungen an einem eigens dafür eingerichteten Prüfstand statt. Anhand dieser Daten werden Simulationsmodelle validiert und für zukünftige Auslegungen eingesetzt. Daraus lassen sich genauere Aussagen über die Lebensdauer dieser komplexen und hochbeanspruchten Bauteile im Sinne einer gesteigerten Robustheit ableiten.
Fertigung auf höchstem Niveau
Ein TCF besteht aus drei Baugruppen, den Anbauteilen, dem Hub Strut Case (HSC) und der Flow Path Hardware (FPH). Die Flowpath-Hardware (FPH), also die Gussteile, die den gasführenden Kanal bilden, werden bei der MTU in München auf einer Fertigungslinie von insgesamt acht Bearbeitungsmaschinen gefertigt – Maschinen, die mit einem sehr hohen Grad an Individualisierung Teile bearbeiten, fräsen, schleifen, bohren. Mit Hilfe einer weitgehend automatisierten Beladung kann jede der Maschinen mit den Bauteilen und Werkzeugen versorgt werden. Dabei können die meisten Maschinen sämtliche in diesem Kontext benötigten Teile fertigen, was eine bestmögliche Auslastung der Anlage erlaubt.
Zum Einsatz kommen 6-Achs-Bearbeitungsmaschinen mit integriertem WZ-Wechselsystem und passender Messtechnik. Zunächst wird jeweils das Werkzeug mit einem Transportwagen zur mechanischen Bearbeitung gebracht und dort in den Puffer geführt. Dieser Puffer ist zweigeteilt in einen Bauteilbereich und einen Werkzeugbereich. Das Beladen erfolgt entweder manuell oder über ein Beladungssystem, wenn es sich um größere, schwerere Teile handelt. Im Rahmen der Bearbeitung fährt das Bauteil in den Arbeitsraum. Ist der Puffer beladen, vollzieht die Maschine einen Identifizierungslauf und erkennt dabei sämtliche Teile.
Alle Bearbeitungsschritte in einer Maschine
Es folgt das Ausrichten des Bauteils in der Maschine und die Bereitstellung des passenden, vorgesehenen Werkzeugs für die Bearbeitung. Das Werkzeug bearbeitet das Werkstück in den unterschiedlichen vorgegebenen Schritten und schreibt die dazu passenden Prozessdaten. Ist das jeweilige Werkstück fertig, folgt das nächste. Die Abarbeitungsreihenfolge wird dabei über Prioritäten durch die Werkstatt festgelegt, die sich nach den Lieferbedingungen richten.
So arbeiten die Maschinen über längere Zeit vollautomatisch ohne menschliches Zutun gemäß der vorgegebenen Abläufe – so lange bis entweder ein notwendiges Werkzeug fehlt oder bis sämtliche Bauteile bearbeitet und alle Aufträge abgearbeitet sind. Erst beim Fehlen einer der Komponenten für den nächsten Schritt fordert die Fertigungslinie einen menschlichen Bediener an.
Im Blick: Hochgradig automatisierte Produktion
Die nächste Maschinengeneration soll noch selbstständiger agieren: Hier könnten Bauteile bei ausreichend vorhandenem Material über längere Zeit auch zwischen verschieden gerüsteten Maschinen getauscht werden. Das erhöht zum einen die Effizienz einer solchen Anlage und ermöglicht zudem deutlich längere automatisierte Produktionsphasen.
Geboten und sinnvoll ist eine solche Erneuerung aber nicht nur aufgrund technischer Weiterentwicklung, sondern auch weil die Turbinenzwischengehäuse immer größer werden. Denn das GE9X ist nicht nur das größte zivile Triebwerk von GE, es schafft neue Herausforderungen an die Fertigung: Schon heute erreichen TCFs einen Durchmesser von rund 1,5 Metern, beim GE9X sind sie aber noch ein ganzes Stück größer.