innovation
Industrie 4.0: Wie Deep Learning die Bildanalyse beschleunigt
Für die Werkstoffentwicklung oder zur Qualitätsprüfung mussten Metallographen oft tagelang Mikroskop-Aufnahmen am PC bearbeiten. Die MTU-Software „Natter“ verkürzt diese Zeit auf Minuten.
Autor: Denis Dilba | 5 Min. Lesezeit veröffentlicht am: 07.12.2020
Autor:
Denis Dilba
studierte Mechatronik, besuchte die Deutsche Journalistenschule und gründete das digitale Wissenschaftsmagazin Substanz. Er schreibt über verschiedenste Themen aus Technik und Wissenschaft.
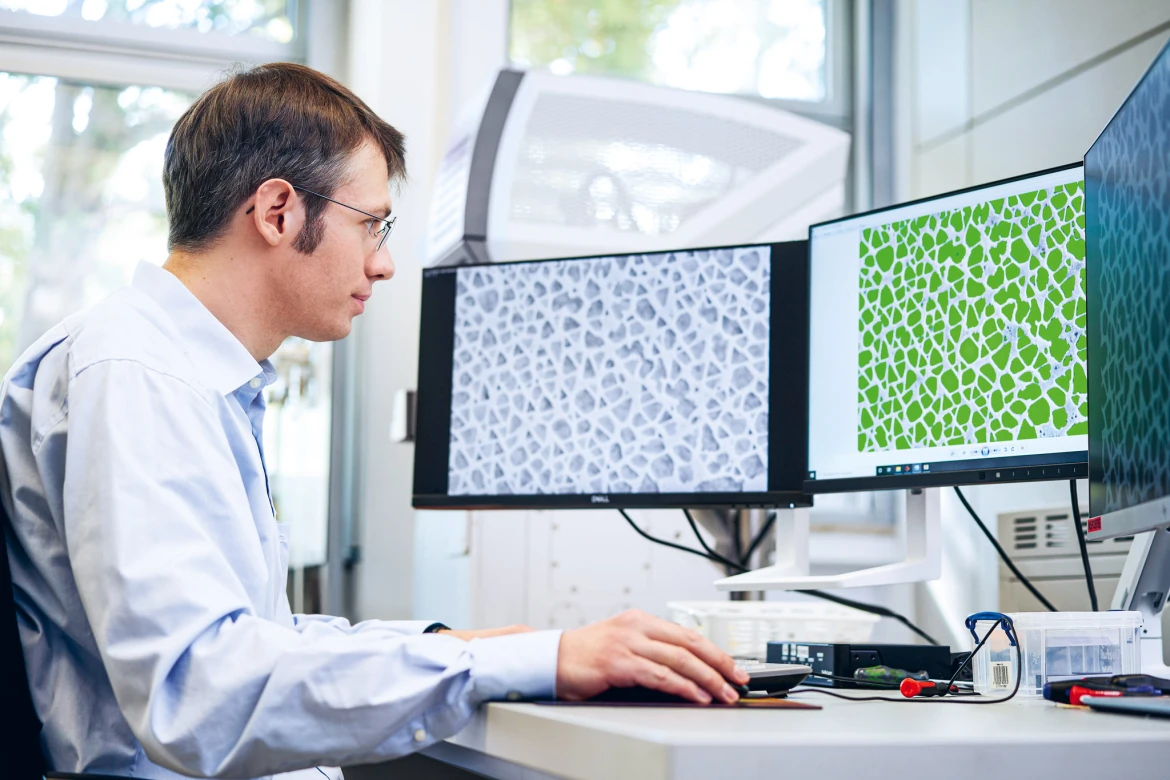
Wer Julian von Lautz und Dr. Hendrik Kramer bei einem Arbeitsgespräch oberflächlich zuhört, könnte durchaus auf die Idee kommen, dass die beiden Ingenieure gerade einen Besuch im Reptilien-Zoo planen. Da fallen Namen wie „Python“ und „Anaconda“, und immer wieder erwähnen sie auch eine „Natter“ – die sehr schnell sein soll. Informatiker wissen bereits bei den ersten beiden Stichworten, dass es sich hier nicht um Schlangen, sondern um die Programmiersprache „Python“ und dessen Toolkit „Anaconda“ handelt. Aber „Natter“? „Steht für ‚Neuronal Analysis Tool to evaluate rapid‘ und beschreibt eine neue Deep-Learning-Software, die die Bildanalyse in der Metallographie zur Werkstoffentwicklung, Qualitätsprüfung und Schadensanalyse auf ein vollkommen neues Level hebt“, klärt Dr. Hendrik Kramer auf, der in dem Team Werkstoffanalytik/Metallografie bei der MTU Aero Engines in München unter anderem für die Bildanalyse zuständig ist. Der Werkstoffexperte hat Natter zusammen mit Julian von Lautz, bisher Leiter der Schadensanalyse, und weiteren Kollegen von der Idee in die Anwendung gebracht. „Zugegeben, wir hatten erst den Namen Natter, dann haben wir die Beschreibung dazu gebastelt.“
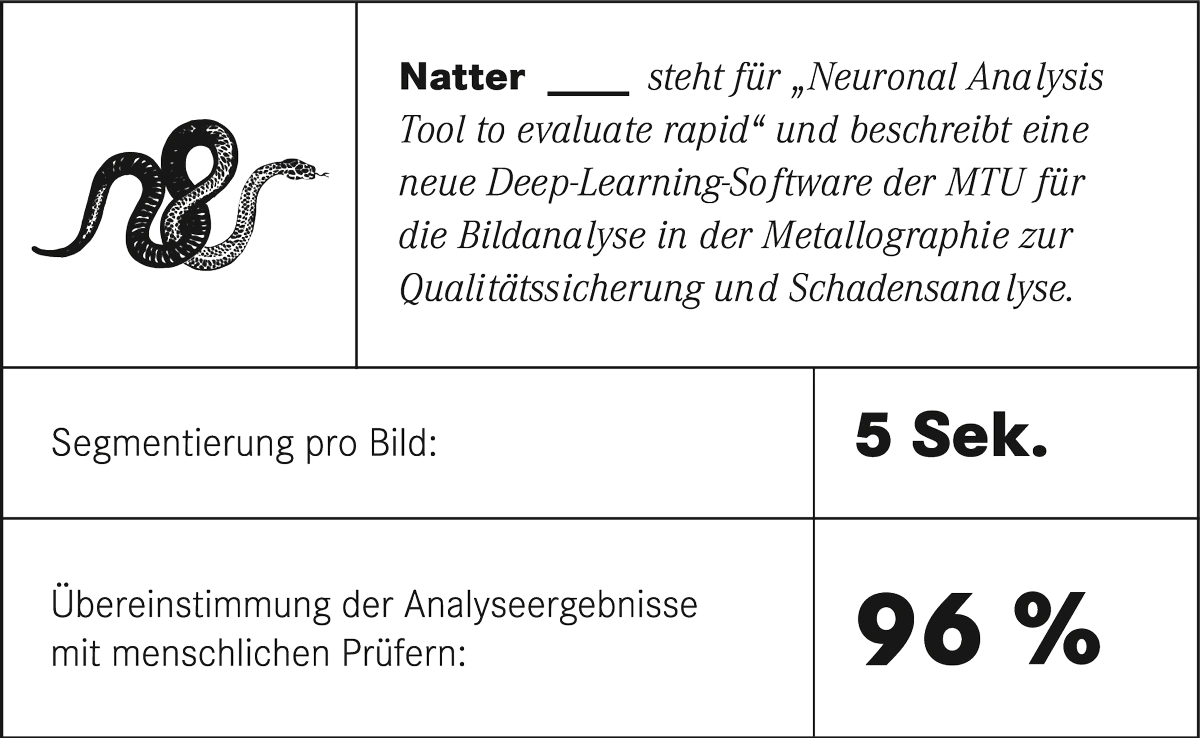
Sowohl das Kürzel als auch seine Erklärung treffen aber auf den Punkt: Ähnlich, wie die Vertreter der weltgrößten Schlangenfamilie mit ihrem blitzartigen Biss Beute schnappen, klassifiziert die MTU-Software mit Hilfe von künstlicher Intelligenz (KI) in bisher nicht bekannter Schnelligkeit Mikroskop-Aufnahmen von Metallen. Hochrelevant ist das insbesondere in der Werkstoffentwicklung, Qualitätsprüfung oder Schadensanalyse, wo Natter bereits erfolgreich für Nickelbasislegierungen zur Anwendung kommt. Hier entscheidet beispielsweise der prozentuale Anteil, der in dem Metall ausgebildeten Werkstoffphase ɣ‘, über die Güte der Werkstoffeigenschaften bei hohen Temperaturen. Die Herausforderung bei der Analyse dieser Mikrostruktur-Bilder: Bisher musste sie teilweise noch mühsam per Hand durchgeführt werden. Im ersten Schritt teilt dabei ein Computerprogramm jeden Pixel je nach seinem Grauwert in hell oder dunkel ein und rechnet deren Flächenanteile zusammen.
Bildanalyse mit Biss
Der Wunsch nach einer automatisierten Bildanalyse war schon lange groß
„Je nach Werkstoff müssen dabei auch noch einige Sonderregeln befolgt werden, etwa, dass man zusammenhängende helle oder dunkle Flächen nur ab einer bestimmten Größe und Form zählt oder abhängig davon, wie weit entfernt andere Flächen auftreten“, erklärt Bildanalyse-Experte Dr. Kramer. Das Ergebnis der alten Software ist ein Bild mit einer groben Vorauswahl von hellen und dunklen Bereichen – das dann ein Metallograph überprüft und verbessert. Der Vorgang, bei dem die Experten per Hand einzelne Flächen hinzufügen, wegklicken oder gar nachzeichnen, dauert beispielsweise eine halbe Stunde. „Da ein gesamter Analyseauftrag 60 Bilder umfassen kann, saßen unsere hochausgebildeten Metallographen manchmal eine knappe Woche am Rechner und klickten sich die Finger wund“, sagt Dr. Kramer. Die Idee und den Wunsch, diesen Vorgang mit Hilfe von KI zu automatisieren, gab es daher schon seit Jahren. Fast genauso lange waren allerdings die für dieses Problem nötigen Machine-Learning-Algorithmen nicht leistungsfähig genug.
Erst als von Lautz und Dr. Kramer vor gut drei Jahren auf eine spezielle Deep-Learning-Methode stießen, die kurz zuvor entwickelt wurde, kam die automatisierte Bildanalyse in Reichweite. Sie konzipierten kurzerhand eine studentische Masterarbeit, die schnell darüber Aufschluss bringen sollte, ob der Ansatz tatsächlich ihr Problem lösen konnte. „Dass die neue Methode funktionieren wird, stand schon nach rund zwei Monaten Programmierarbeit fest“, erinnert sich von Lautz. Mit der nötigen sauberen Dokumentation, der weiteren Optimierung des Programmcodes und der Vorbereitung der Trainingsdaten haben sie ein gutes Jahr benötigt, um Natter fertig für den Einsatz zu machen, so die beiden MTU-Ingenieure. „Insbesondere den Aufwand für die Datenvorbereitung bei solchen Methoden sollte man nicht unterschätzen“, sagt Dr. Kramer. Für das Training der Deep-Learning-Software, nutzten sie 2400 Bildpaare, bei denen die richtigen Lösungen zu den jeweiligen Aufgabenstellungen schon bekannt waren. Rund 2.000 davon zum Lernen, die restlichen 400, um den Trainings-Fortschritt zu prüfen.
Natter verbessert die Bildanalyse-Performance um mindestens 90 Prozent
Das Heraussuchen der Bildpaare habe dabei nur einen Teil der Arbeit ausgemacht, so der Bildanalyse-Experte. Mindestens ebenso aufwendig sei es gewesen, die Daten auf ein einheitliches Format zu bringen: „Die Aufnahmen stammen von verschiedenen Mikroskopen, sind unterschiedlich belichtet und zugeschnitten und haben unterschiedliche Auflösungen.“ Bis Natter mit dem Training auf einem einheitlichen Datensatz beginnen konnte, habe es mehrere Monate gedauert. Eine Mühe, die sich mehr als gelohnt hat: Die per KI automatisierte Bildanalyse braucht pro Bild gerade mal fünf Sekunden. Das Analyse-Ergebnis entspricht mit einer Genauigkeit von etwas mehr als 96 Prozent dem von menschlichen Prüfern. „Die Rechenzeit von Natter fällt damit nicht mehr ins Gewicht“, sagt Dr. Kramer. Trotzdem gehen die MTU-Ingenieure konservativ davon aus, dass ein Experte noch jedes automatisch ausgewertete Bild sichten und dann vielleicht jedes zehnte Bild nochmal von Hand kontrollieren muss.
„Selbst mit dieser Annahme braucht Natter anstatt 30 Minuten aber nur drei Minuten pro Bild“, sagt von Lautz. „Das ist ein Performance-Zuwachs von mindestens 90 Prozent.“ Und eine enorme Arbeitserleichterung für die Metallographen, die statt einer Woche nun nur noch zwei bis drei Stunden benötigen und so mehr Zeit für andere Aufgaben haben, beispielsweise die Entwicklung von neuen Werkstoffen. Die MTU sei mit der Umsetzung dieser automatisierten Bildanalyse damals ihrer Zeit voraus gewesen, so der Schadensanalyse-Leiter. „Zukünftig arbeiten wir daran, dass mit Natter neben Nickelbasislegierungen noch mehr Werkstoffe beurteilt werden können.“ Die beiden MTU-Ingenieure denken aber bereits noch weiter: „Grundsätzlich ist mit der neuen Methodik alles, was mit Bildverarbeitung zu tun hat, gut lösbar. Vor allem wenn das Problem nicht mathematisch beschrieben werden kann, aber es viele Trainingsdaten gibt“, sagt Dr. Kramer. Die Anwendung müsse nicht zwangsläufig in Bereich der Metallographie liegen. Von Lautz etwa ist davon überzeugt, dass solche KI-Verfahren mittel- bis langfristig zu einem virtuellen Assistenten für Luftfahrt-Ingenieure führen werden.
„Wie moderne KI-Diagnose-Programme Ärzten heute schon auf Röntgenbildern der Lunge automatisch Metastasen anzeigen, werden diese Geräte uns Ingenieuren helfen, den Blick bei Analysen und Prüfungen nur auf die relevanten Stellen richten zu müssen“, sagt von Lautz. So könne mit der gleichen oder einer höheren Qualität mehr in weniger Zeit geprüft werden. „Gerade in der Luftfahrtbranche, wo Sicherheit immer Trumpf ist,“, so der MTU-Experte, „gehört solchen KI-Lösungen die Zukunft.“