innovation
Innovatives Montagesystem für den MRO-Shop von EME Aero
Weltweit einzigartig ist das Hightech-Montagekonzept, das MTU-Spezialist:innen aus München für den MRO-Shop von EME Aero realisiert haben.
Autorin: Nicole Geffert | 6 Min. Lesezeit veröffentlicht am: 07.07.2021
Autorin:
Nicole Geffert
arbeitet seit 1999 als freie Journalistin mit den Themen Forschung und Wissenschaft, Geld und Steuern, Ausbildung und Beruf.
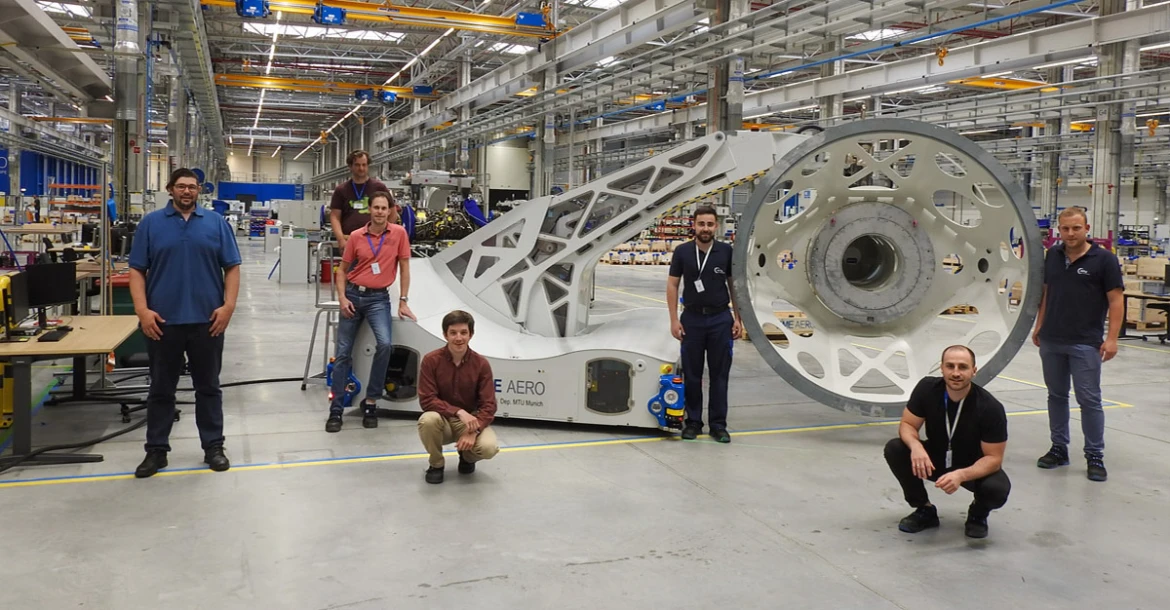
Die eine oder andere schlaflose Nacht gab es, keine Frage. Denn der Zeitdruck war enorm und die Aufgabe hatte es in sich: Für den Shop von EME Aero, das Joint Venture von Lufthansa Technik und der MTU Aero Engines im polnischen Jasionka, sollte in nur drei Jahren ein komplett neues Hightech-Montagekonzept entwickelt und realisiert werden, das eine Instandhaltung der Pratt & Whitney GTF™-Triebwerke auf höchstem Niveau gewährleistet.
Dieses Mammut-Projekt war der perfekte Auftrag für die Spezialist:innen vom Produktions- und Anlagenservice der MTU in München. „Wir hatten bereits die weltweit einzigartige GTF-Endmontagelinie am MTU-Standort München mit entwickelt. Konkrete Ideen für ein innovatives Montagekonzept für die Maintenance hatten wir bereits im Kopf und auf Papier“, erinnert sich Stefan Hofner, Konstruktion Fertigungshilfsmittel bei der MTU, stellvertretend für die ganze Mannschaft. Im Projektteam arbeiten Kolleg:innen aus verschiedensten Abteilungen und Fachbereichen zusammen. „Diese interdisziplinäre Vernetzung ermöglicht es uns, solch ein Projekt in der geforderten Kürze realisieren zu können“, so der Konstrukteur.
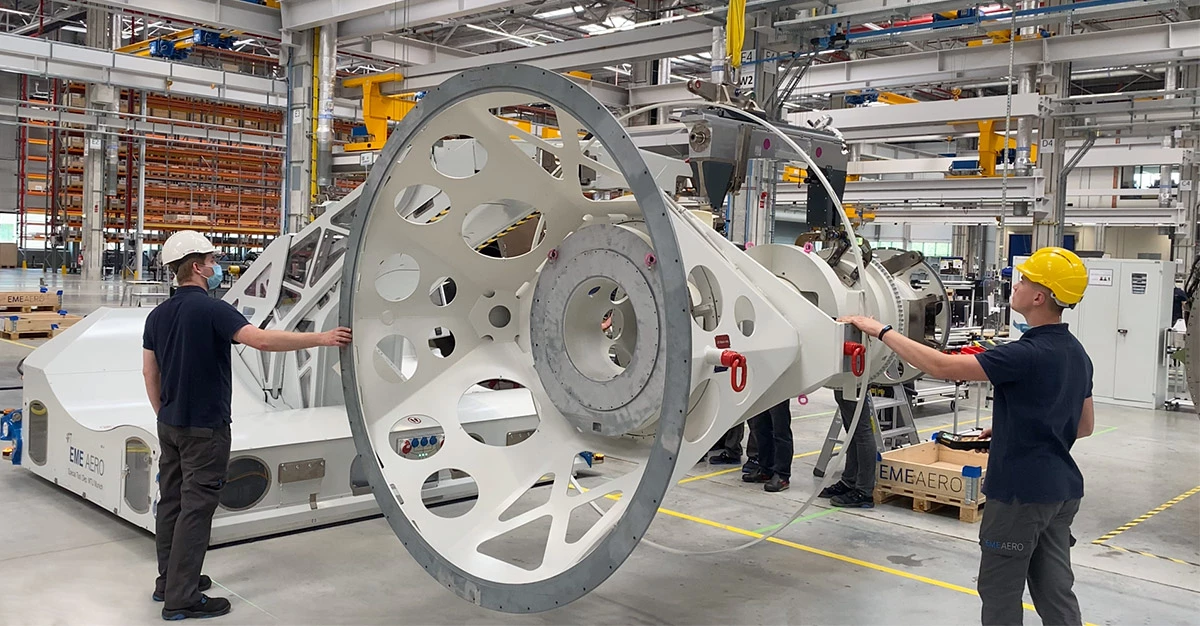
Hightech-Montagekonzept: In Rekordzeit entwickelten MTU-Spezialisten ein Montagekonzept für die Instandhaltung der Getriebefan-Triebwerke im MRO-Shop von EME Aero.
Das innovative Konzept der MTU-Expert:innen überzeugte, sie bekamen den Auftrag und legten los. „Es gibt bei der Planung von MRO-Shops immer die Grundsatzfrage: Bewegen sich die Triebwerke oder bewegen sich Werkzeuge und Personal?“, erläutert Hofner. Diese Frage der Shop-Philosophie – durchläuft das Triebwerk eine Montagelinie oder wird es an einer einzigen Station, dem Triebwerk-Dock, instandgesetzt – kann stets unterschiedlich beantwortet werden. Sie hängt auch damit zusammen, wie viele Triebwerke pro Jahr instandgesetzt werden – im Falle einer großen Anzahl an Shop Visits an baugleichen Triebwerken bietet sich die Linien-Philosophie an. „EME Aero musste sich nicht zwischen Montagelinie und einzelnen Triebwerk-Docks entscheiden. Mit unserem Montagekonzept kann der Shop die Vorteile beider Welten flexibel nutzen“, sagt Hofner.
Keine Störungen im Gesamtfluss
„Flexibel“ ist das Stichwort: Anders als bei klassischen Flowlines basiert das Montagesystem des Münchner Projektteams nicht auf fest installierten Strukturen, wie beispielsweise dem in der MRO üblichen Überkopf-Triebwerksaufhängungssystem. Stattdessen werden die Antriebe an bodengebundenen, frei beweglichen Trägern angebracht, die in die Produktionslinie hinein- und aus dieser herausbewegt werden können, ohne den Gesamtfluss zu stören. Highlight des Konzepts sind zwei Systeme: Die Komplettzerlegung erfolgt in der Linie am Mobile Transport and Overhaul System (MTOS), die Teilzerlegung hingegen wird im Dock des Fixed Overhaul Systems (FOS) durchgeführt.
„Das MTOS besteht aus einem ferngesteuerten Wagen, mit dem das Triebwerk von einer zu nächsten Station gefahren und ergonomisch positioniert werden kann“, erläutert Hofner. „An jeder Station `wartet´ das passende Werkzeug und das spezialisierte Personal für die anstehenden Arbeiten. Das ist sehr effizient im Falle hoher Volumen im Shop.“ Beim FOS hingegen bleibt das Triebwerk an einer Station, also im Triebwerk-Dock. Hofner: „Die Werkzeuge werden nach Bedarf angeliefert, Personal entsprechend angefordert. Das FOS eignet sich etwa für geringere Stückzahlen und kleineren Spezialreparaturen.“
„Da das fest installierte FOS dieselbe Schnittstelle wie das fahrbare MTOS verwendet, ermöglicht das einen flexiblen Wechsel der Triebwerke zwischen den beiden Systemen. Das standardisiert Abläufe und spart Zeit.“
Konstruktion Fertigungshilfsmittel bei der MTU
Flexibler Wechsel, standardisierte Abläufe
Sobald ein GTF-Triebwerk in den Shop von EME Aero kommt, wird der Montageträger per Hallenkran an dem Triebwerk angebracht. Der Montageträger, auch Shuttle genannt und vergleichbar mit einem Adapter, ist das Herzstück des ganzen Konzepts. Mit ihm lässt sich das Triebwerk in allen Bauzuständen vom Kran entweder in die Montagesysteme hineinheben oder herausheben. Der Montageträger ist also die Schnittstelle zwischen Triebwerk und dem MTOS und FOS. Ohne weitere Rüstarbeiten vornehmen zu müssen, lässt sich das Triebwerk nun für zahlreiche Arbeitsschritte unkompliziert montieren oder zerlegen. „Da das fest installierte FOS dieselbe Schnittstelle wie das fahrbare MTOS verwendet, ermöglicht das einen flexiblen Wechsel der Triebwerke zwischen den beiden Systemen“, sagt Stefan Hofner. „Das standardisiert Abläufe und spart Zeit.“ Sollte sich der Arbeitsumfang sich am FOS beispielsweise vergrößern, kann das Triebwerk problemlos vom MTOS übernommen werden.
Von allen Seiten Zugang zum Bauteil
Da der Shop von EME Aero ein Neubau ist, musste das MTU-Projektteam auf keine baulichen Gegebenheiten oder vorhandenen Strukturen Rücksicht nehmen. Auch das Triebwerkportfolio ist klar definiert. EME Aero ist auf die Instandhaltung von GTF-Triebwerken spezialisiert. Das PW1100G-JM wird bereits instandgesetzt, für das PW1500G erfolgt noch in diesem Jahr die MRO-Fähigkeit. Auch hier haben die MTU-Spezialist:innen mit Weitsicht agiert.
Denn das Montagesystem ist für die GTF-Familie adaptierbar. So muss das PW1500G nicht ein eigens für diesen Triebwerkstyp errichtete Montagesystem durchlaufen, sondern kann in der für das PW1100G-JM genutzten Montagelinie abgewickelt werden. Entsprechend entwickelte das Team für verschiedene GTF-Triebwerke individuelle Montageträger. „Das liegt an den unterschiedlichen Aufhängepunkten der Triebwerke“, erläutert Hofner. Das zu bearbeitende Triebwerk wird stets zentral am Kerntriebwerk aufgehängt. Die Module lassen sich so ohne weitere Unterstützung komplett ab- und anbauen. Die individuellen Montageträger ermöglichen standardisierte Arbeitsprozesse in allen Stationen, unabhängig davon, welcher Triebwerkstyp gerade vorliegt. Dadurch, dass die Triebwerke aufgehängt werden, kommen die Mechaniker:innen mit ihren Werkzeugen von allen Seiten an die zu bearbeitenden Bauteile. Zudem ist der Aufbau im MTOS höhenverstellbar. So lässt sich ergonomisch arbeiten.
Technische Highlights hat das MTU-Projektteam auch für die Modul-Montage entwickelt. An sogenannten Wendeständen können die Module so positioniert werden, wie es die Mechaniker für ihre Arbeit benötigen. Die Wendestände werden per Akku betrieben, somit liegen keine Kabel im Weg. Und auch die zentralen Toolings im Modulbereich sind so ausgelegt, dass sowohl die Triebwerke des Typs PW1100G-JM als auch die des Typs PW1500G damit bearbeitet werden können.
„Wir führen diese beiden Bereiche bei der MTU zusammen – und von diesem Vorteil profitieren das Unternehmen und seine Kunden.“
Konstruktion Fertigungshilfsmittel bei der MTU
Wie ist es dem Team gelungen, in nur drei Jahren sein Konzept erfolgreich umzusetzen? Hofner: „Als Abteilung für Werkzeugbau der MTU vereinigen wir zwei wichtige Bereiche, für die es in der Regel separate Spezialist:innen gibt: den klassischen Anlagen- und Maschinenbau und das Know-how der Triebwerksmontage. Wir führen diese beiden Bereiche bei der MTU zusammen – und von diesem Vorteil profitieren das Unternehmen und seine Kunden.“
Noch ist das Montagekonzept im MRO-Shop von EME Aero einzigartig – aber vielleicht nicht mehr lange. Die MTU Maintenance Zhuhai baut derzeit einen zweiten Standort für die Instandsetzung der Pratt & Whitney GTF™-Triebwerke auf. Und auch dort ist das Montagekonzept der Münchner Expert:innen bereits im Gespräch.
Einmalige Fertigungstechnologie für die PW1100G-JM-Neubaumontage
Eine weltweit einmalige Fertigungstechnologie steckt in der Neubaumontage des A320neo-Antriebs PW1100G-JM am MTU-Standort in München. Seit 2016 werden dort 30 Prozent aller PW1100G-JM in Serie endmontiert. Üblicherweise erfolgt der Zusammenbau eines Triebwerks mit Hilfe von Kranen, die an Deckenschienen laufen. In München hatte man eine komplett neue Idee: Die Montage wird bodengeführt organisiert. Das dafür entwickelte System besteht aus bis zu 16 ferngesteuerten Wagen, die sich, je nach Montagefortschritt passend gekoppelt, fließbandähnlich entlang der Montagelinie bewegen. Das Stichwort heißt: getaktetes Fischgrät. Insgesamt gibt es acht Montageschritte, von der Seite her stoßen die vormontierten Komponenten und Module dazu. Das System ist besonders effizient, flexibel – und nachweislich erfolgreich. Das Konzept mit den Wagen haben die MTU-Expert:innen jetzt auch in das Hightech-Montagesystem für die Instandhaltung der Pratt & Whitney GTF™-Triebwerke im Shop von EME Aero erfolgreich integriert. Lesen Sie hier mehr dazu …