innovation
Mit Track & Trace das gesamte Produktionsnetzwerk im Blick
Bei der MTU sorgt Track & Trace für die Echtzeit-Lokalisierung sämtlicher produzierter Bauteile. Das bringt schon jetzt deutlich mehr Transparenz und Effizienz.
Autor: Tobias Weidemann | 5 Min. Lesezeit veröffentlicht am: 31.05.2022
Autor:
Tobias Weidemann
ist seit mehr als 20 Jahren als Journalist und Content-Berater tätig. Er berichtet über Technik- und Wirtschaftsthemen, oft mit Schwerpunkt auf Business-IT, Digitalisierung und Zukunftstechnologien.
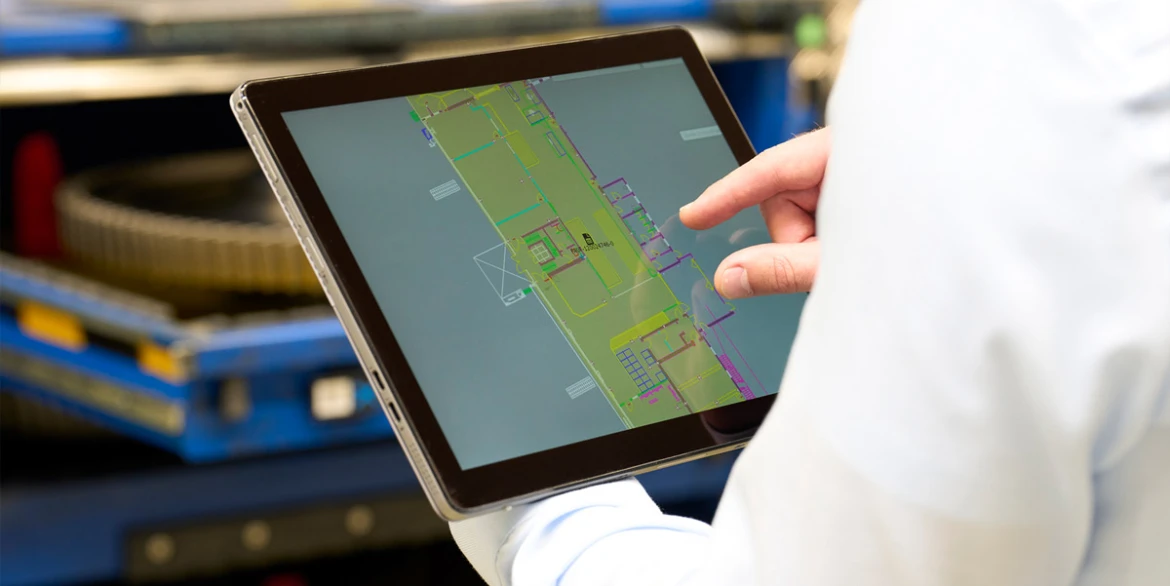
Wo genau befindet sich ein bestimmtes Bauteil, das individuell gefertigt wurde, was ist mit einem dringenden Fertigungsauftrag und wo waren nochmal die übrigen Baugruppen eines bestimmten Triebwerks, das im Rahmen einer Instandhaltung zerlegt wurde? Den kompletten Überblick über sämtliche produzierte Teile und Reparaturvorgänge auf dem Werksgelände zu behalten – und das in Echtzeit – das ist das Ziel eines Projekts, das die MTU Aero Engines seit anderthalb Jahren vorantreibt. Das Unternehmen arbeitet daran, eine umfassende Track-&-Trace-Lösung einzurichten, mit der sich nicht nur jederzeit Transparenz über die Fertigungsvorgänge auf dem Werksgelände schaffen lässt, sondern die mittelfristig dank Digitalisierung und Automatisierung von Prozessen auch einen Effizienzgewinn für den Materialfluss und die Produktion bringt.
Doch was genau steckt hinter Track & Trace? Die deutsche Übersetzung „Verfolgen und Aufspüren“ beschreibt die beiden Komponenten des Themas schon recht gut. Es geht um die bestmögliche Transparenz in der Intralogistik, also um die Transportvorgänge auf einem Werksgelände, aber auch darüber hinaus. So sollen jederzeit einzelne Bauteile oder Bauteilgruppen, aber auch ganze Triebwerke nachverfolgt werden können und der damit verbundene Fertigungsfortschritt automatisiert protokolliert werden. „Diese Informationen hatte man in der Vergangenheit immer nur mit einem gewissen Zeitversatz und auch nicht immer in dieser Zuverlässigkeit wie heute“, erklärt Lucas Burgey, Projektleiter am Standort in München. Mitarbeiter:innen buchten zwar Arbeitsschritte und Transportvorgänge manuell in die entsprechende Software, aber die dort hinterlegten Statusdaten waren manchmal nicht im Einklang mit der Realität oder einfach verzögert – etwa weil eine Gitterbox oder ein Container aus Platzgründen woanders hingestellt worden war oder sich etwas im Versandprozess ergeben hatte, das durch die Software nicht abgebildet wurde.

Transparenz in der digitalen Fabrik: Martin Roth und Lucas Burgey treiben das Projekt voran.
Standorterkennung und Auffinden in Echtzeit
Ende 2020 begannen die Planungen für das Logistik-4.0-Projekt, in dessen Rahmen für die Echtzeit-Lokalisierung eine Vielzahl an Sendern, sogenannten Ankern, in den Produktionshallen verbaut wurde. Gestartet wurde am Standort in München zunächst nur mit einer einfachen Standorterkennung von Gitterboxen und Schubladenkisten, verbunden mit der Information, ob der Behälter voll oder leer ist – „einfach um erste Erfahrungen mit der Technik zu sammeln“, wie Burgey erklärt. Nach einer ausführlichen Analyse entschied man sich für ein Ultrawideband (UWB)-System, eine Nahbereichsfunktechnik, die über eine zentimetergenaue Präzision verfügt und somit den Anforderungen der MTU gerecht wird.
Das Betriebssystem Kinexon OS ist das eigentliche Herzstück der umfangreichen Anwendungen rund um Track & Trace. Es führt sämtliche Lokalisierungsdaten zusammen – kombiniert sie mit den Grundrissen der Produktionshallen und den Plänen des Werksgeländes sowie mit den hinterlegten Produktionsdaten und –regeln. Da all das über einen handelsüblichen Internet-Browser angezeigt und gesteuert werden kann, stehen alle Funktionen sowohl auf dem Desktop-PC als auch auf dem Tablet oder Dienst-Smartphone in der Anlage zur Verfügung. „Eine Funktionalität auch für die Hosentasche, ohne dass dafür spezielle Industriegeräte erforderlich sind“, fasst es Martin Roth, Projektleiter aus IT-Sicht, zusammen.
Neben der Software spielen die Empfänger, sogenannte Tags, die Hauptrolle in dem System. Da gibt es einfache UWB-basierte X-Tags, die etwa die Größe eines USB-Sticks oder Feuerzeugs haben und zur zielsicheren Ortung beispielsweise an einer Schubladenkiste, einer Palette oder einem Kommissionierwagen befestigt werden können. Daneben sollen in Zukunft auch komplexere und intelligentere Tags zum Einsatz kommen, die zusätzliche Informationen bereitstellen.
„All das funktioniert nicht nur in der Fertigung, sondern bringt insbesondere auch im Instandhaltungs- und Reparaturgeschäft entscheidende Vorteile. Denn dieses ist naturgemäß deutlich volatiler und daher weniger gut planbar.“
Projektleiter am Standort in Hannover bei der MTU
Unterstützung auch in der Triebwerksinstandhaltung
„All das funktioniert nicht nur in der Fertigung, sondern bringt insbesondere auch im Instandhaltungs- und Reparaturgeschäft entscheidende Vorteile. Denn dieses ist naturgemäß deutlich volatiler und daher weniger gut planbar“, weiß Yannick Dix, der als Projektleiter am Standort in Hannover für die dortige Implementierung des Systems verantwortlich ist. Bei der MTU Maintenance werden regelmäßig Triebwerke in tausende Einzelteile zerlegt und repariert, bevor dann wieder ein funktionierendes Triebwerk daraus wird. „Bei einem solchen Prozess laufen viele Anforderungen bisher noch analog und mit Papier ab“, weiß Dix. „Wir starten mit dem Tracking von Transporthilfsmitteln, die für den Transport und die Bereitstellung von kommissionierten Triebwerksbauteilen in der Montage eingesetzt werden.“ In Zukunft sollen hierfür auch autonom fahrende Transportwagen zum Einsatz kommen, die ihrerseits mit speziellen Tags ausgestattet sein werden. Außerdem ist geplant, gängige Tools und die größeren Baugruppen der zerlegten Triebwerke ebenfalls mit einem Tag zu versehen, um heute anfallende Suchzeiten signifikant zu reduzieren.
„Das beginnt mit dem Tracking der Vorrichtungen und Bearbeitungswerkzeuge, geht weiter mit der Reparaturauftragsverfolgung und endet noch lange nicht mit der Ressourcenverwaltung.“
Projektleiter bei der MTU Aero Engines
Track & Trace ist erst der Anfang
Sind die UWB-Anker, so der Fachbegriff für die Sendeeinheiten, erst einmal montiert, kann die MTU hierauf aufbauend eine Vielzahl von weiteren Internet-of-Things-Anwendungen planen und standortbezogene Dienste in der Produktion umsetzen. „Das beginnt mit dem Tracking der Vorrichtungen und Bearbeitungswerkzeuge, geht weiter mit der Reparaturauftragsverfolgung und endet noch lange nicht mit der Ressourcenverwaltung“, erklärt Martin Roth. In den nächsten Monaten plant das Unternehmen daher, nach und nach alle weiteren MTU-Standorte flächendeckend mit der Lokalisierungstechnik auszustatten.
„Dank der Echtzeitinformationen und der gesammelten Daten können wir zukünftig Logistikkonzepte entlang der gesamten Versorgungskette effizienter steuern und planen.“
Projektleiter bei der MTU Aero Engines
Vielfältiger soll mittelfristig auch die Tracking-Technologie werden. Zwar ist UWB auf dem Werksgelände besonders genau und treffsicher, setzt aber das flächendeckend verbaute Ankernetz voraus. Doch auch zwischen verschiedenen Standorten oder darüber hinaus muss das Unternehmen zuweilen wissen, wo sich etwa ein Triebwerk befindet. Das geht mit Hilfe von Bluetooth-Daten und klassischen GPS-Diensten. Die so gewonnenen Standortdaten lassen sich ebenfalls in dem KINEXON OS System verarbeiten und bringen dem Unternehmen so wertvolle Informationen. „Das neue System ist Teil einer größeren Automatisierungs- & Digitalisierungsstrategie“, fasst es Burgey zusammen und denkt schon einige Schritte weiter: „Dank der Echtzeitinformationen und der gesammelten Daten können wir zukünftig Logistikkonzepte entlang der gesamten Versorgungskette effizienter steuern und planen. Dies betrifft nicht nur die Bauteile der MTU, sondern auch Hilfsmittel wie Werkzeuge, Vorrichtungen und sonstiges Material, das die MTU für ihre Wertschöpfung benötigt.“
Die standortbezogenen Dienste optimieren so Laufzeiten, reduzieren Kosten und ermöglichen die Optimierung und Kontrolle von Prozessen in der Produktion – „mit einem hohen Grad an Automatisierung und wachsender Intelligenz dank immer mehr Daten aus verschiedenen Quellen“, wie es Roth beschreibt. Man habe bereits eine hohe zweistellige Zahl an weiteren Use Cases, die mehr oder weniger komplex sind. „Die übergeordnete Vision besteht darin, die physische und digitale Welt ohne menschliches Zutun miteinander zu koppeln, sodass Supportprozess, wie Transport- oder Bestellprozesse, automatisch initiiert und protokolliert werden – ein echter Zeit- und Effizienzgewinn für alle Beteiligten", erklärt Dix. Auch wenn es bis zu den vorausschauenden Analysen und einem weitgehend autonomen Materialfluss noch ein weiter Weg ist, ist die Ankertechnologie somit die Grundlage für eine Vielzahl spannender Use Cases auf dem Weg zur digitalen Fabrik.