people
Digitalization paves the way for predicting tool wear
Pere Massanés Padró is working on a simulation model that enables detailed predictions to be made about tool wear.
author: Thorsten Rienth | 3 mins reading time published on: 01.07.2019
author:
Thorsten Rienth
writes as a freelance journalist for AEROREPORT. In addition to the aerospace industry, his technical writing focuses on rail traffic and the transportation industry.
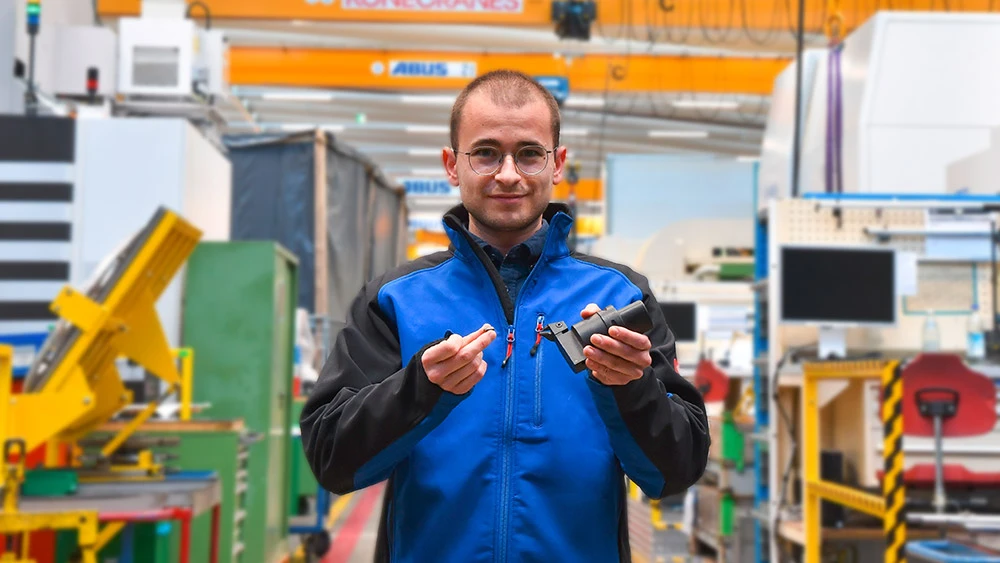
Industrial trial and error sounds like an expression from a time when digitalization was nothing more than a vision of the future. “In some cases, though, there are still no alternatives to this approach, and tool wear is a case in point,” explains engineer Pere Massanés Padró. Determining acceptable process conditions that don’t exceed prescribed wear limits calls for experimentation that requires a monumental amount of time and effort. “The only way to gain a thorough understanding of how tool wear develops is by conducting realistic and time-consuming tests in everyday production scenarios,” he says.
- Using multiphysics simulations to boost efficiency
- A data scientist for the aviation industry of tomorrow
- Digitalization paves the way for predicting tool wear
- Managing digital transformation
- Digital tools help create new, efficient components
- Talking geometries: A common language for more efficient engine development
After all, tool wear does not occur in a uniform manner. Its nature is initially degressive, then somewhat linear, before finally becoming progressive. And, of course, it all depends on the material and cutting speed. The matter is so complex that even today, there are no models advanced enough to incorporate tool wear into the design of tools and production processes. Not even the finite element method (FEM), which is usually the go-to option for solving physical problems in engineering calculations, is sufficient for predicting tool wear in industrial applications.
The consequences of tool wear are far from insignificant. If wear causes the shape of a tool’s cutting face to change, this affects the contour of the workpiece. Surface integrity and process stability both suffer as a result. If such tool wear could be calculated in advance, production engineers could precisely offset it during the process by adjusting the cutting speed, tool angle or feed rate, for example. In the aerospace industry, where machining of nickel- or titanium-based superalloys generates high production costs, the potential offered by reliable tool wear prediction is especially significant.
At the age of 18, Massanés Padró enrolled at the Universitat Politècnica de Catalunya in Barcelona to study mechanical engineering. At 22, he went on to earn a master’s degree in materials engineering. “I decided very early on that I wanted to work abroad, where the career opportunities in my field are more attractive,” he says. And his dream became reality when he saw a position advertised online for a master’s student in MTU’s machining simulation department. After five months working there as a student, MTU offered him a permanent position as an engineer in the same department. “This way, I could continue working on my topic,” Massanés Padró says.
The 26-year-old wants to use a hybrid method to solve the problem of tool wear predictability. This involves rolling analytical, empirical, experimental and numerical approaches into one large simulation model. Massanés Padró’s aim is to link process parameters such as cutting speed, feed rate, cutting depth, tool geometry and tool material with physical outputs such as process forces, temperatures, pressure, stresses and strains in order to predict how tool wear will develop.
Of course, this in itself is still a complex construct. “But one that could be represented in digital form,” Massanés Padró says. It would also dramatically reduce the amount of trial and error involved. “With only a very small number of experimental tests, and with reasonable accuracy, we’ll be able to predict the influence that different process conditions have on tool wear.”