aviation
Additive Fertigung: Schicht für Schicht zum Bauteil
Mit dem Boroskopauge führte die MTU als einer der ersten Antriebshersteller der Welt die additive Serienfertigung ein. Strategisch goldrichtig: dem neuen Verfahren gehört die Zukunft.
Autor: Denis Dilba | 7 Min. Lesezeit veröffentlicht am: 01.06.2019
Autor:
Denis Dilba
studierte Mechatronik, besuchte die Deutsche Journalistenschule und gründete das digitale Wissenschaftsmagazin Substanz. Er schreibt über verschiedenste Themen aus Technik und Wissenschaft.

Das Boroskopauge ist ein kleines und eher unscheinbares Bauteil. Es passt ungefähr in eine Faust, hat links und rechts zwei seitliche Ausleger mit Loch, eine Öffnung mit silbrigem Gewinde in der Mitte und ansonsten eine matt-gräuliche Oberfläche. Das Anbauteil wird auf das Turbinengehäuse geschraubt und erlaubt es Technikern mit einer Inspektionskamera – dem namensgebenden Boroskop – in das Innere der Niederdruckturbine zu schauen und so den Zustand der Schaufeln zu überprüfen. Die allermeisten Menschen würden schlicht nicht wissen, was sie da vor sich haben, wenn man ihnen das Bauteil präsentiert. Für Dr. Jürgen Kraus allerdings, den Leiter Additive Fertigung bei der MTU Aero Engines in München, hat das Boroskopauge eine ganz besondere Bedeutung. „Damit haben wir den Durchbruch in der additiven Serienfertigung geschafft“, sagt Kraus. Wurden diese Anbauteile früher noch aus dem Vollen gefräst, entstehen sie heute elegant per selektivem Laserschmelzen (Selective Laser Melting = SLM).
Boroskopaugen: sind kleine Öffnungen, durch die Beschaufelungen von Zeit zu Zeit mit einem Boroskop auf mögliche Abnutzungen überprüft werden. Die PW1100G-JM-Boroskopaugen stellt die MTU additiv her.
Dreidimensionale Mikroschweißvorgänge
Gemeinhin wird dieses Verfahren dem breiten Feld des 3D-Drucks zugeordnet. Rein technisch betrachtet handelt es sich dabei allerdings um dreidimensionale Mikroschweißvorgänge. Das 3D-Modell des zu fertigenden Bauteils wird dazu im ersten Schritt am Rechner in einzelne 20 bis 40 Mikrometer dünne Schichten zerlegt. Ein starker Laser schmilzt dann pulverförmigen Werkstoff in einer Baukammer exakt an jenen Stellen auf, die ihm die computergenerierten Bauteil-Konstruktionsdaten vorgeben, und verbindet ihn dadurch mit der Schicht darunter. So werden Bauteile Schritt für Schritt aufgebaut, stets kommt eine Schicht dazu. Experten wie Kraus sprechen daher auch von additiver Fertigung. Mit den Boroskopaugen wird heute die Niederdruckturbine des A320neo-Getriebefans PW1100G-JM ausgerüstet. Die MTU ist damit eines der ersten Unternehmen in der Luftfahrtbranche, bei der die innovative Fertigungstechnik für die Produktion von Serienbauteilen zugelassen ist und bereits eingesetzt wird.
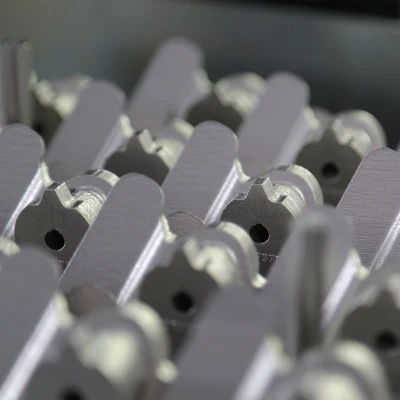
Schicht für Schicht: „wachsen“ von diesen Boroskopaugen gleich mehrere auf einem Träger. Nachdem sie von ihm abgelöst sind, folgt die Endkonturbearbeitung.
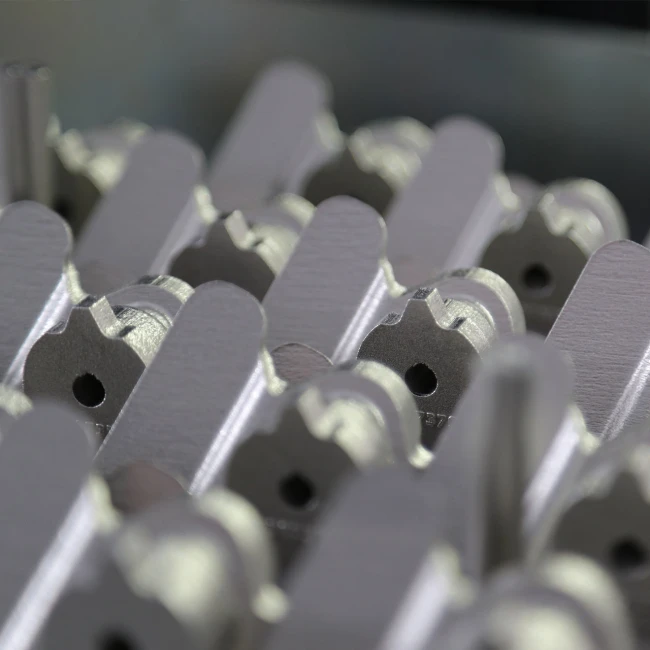
Schicht für Schicht: „wachsen“ von diesen Boroskopaugen gleich mehrere auf einem Träger. Nachdem sie von ihm abgelöst sind, folgt die Endkonturbearbeitung.
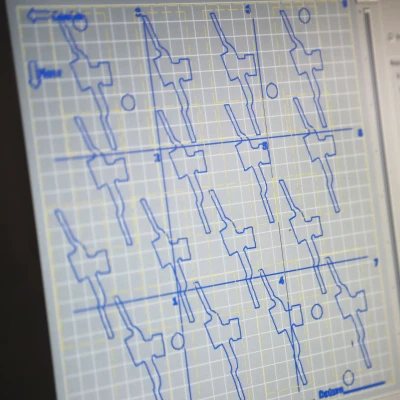
Um viele Ecken: Mit additiven Verfahren können komplexe Bauteilkonturen gefertigt werden, die mit herkömmlichen Verfahren wie Fräsen nur sehr zeit- und materialaufwändig möglich sind.
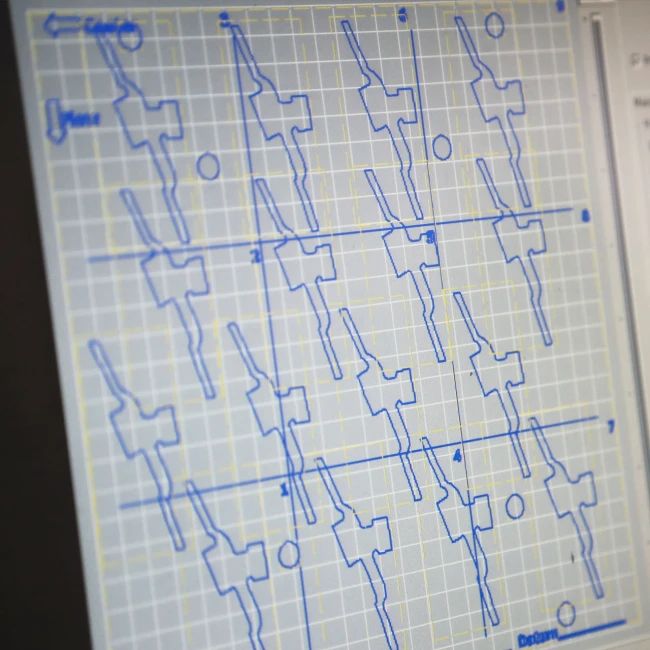
Um viele Ecken: Mit additiven Verfahren können komplexe Bauteilkonturen gefertigt werden, die mit herkömmlichen Verfahren wie Fräsen nur sehr zeit- und materialaufwändig möglich sind.
Beginn mit Werkzeugen und einfachen Rohteilen
Der Weg dahin begann schon früh. Bereits seit den späten 1990er-Jahren beschäftigt sich die MTU mit den additiven Verfahren, in den ersten Jahren zunächst noch theoretisch, dann aber schnell auch praktisch. „Begonnen haben wir mit der Herstellung von Werkzeugen und Urmodellen für den Feinguss sowie einfachen Entwicklungsbauteilen“, erinnert sich Kraus. In der zweiten Phase wurden dann Vorrichtungskomponenten produziert, die bestehende Teile ersetzt haben, etwa Spritzdüsen sowie Schleifscheiben zur Fertigung von Bauteilen. In diese Etappe fallen auch die Getriebefan-Boroskopaugen. „Die einfach aufgebauten und für die unmittelbare Funktion eines Triebwerks unkritischen Bauteile waren ideal geeignet, um zu lernen, wie additive Fertigung in Serie funktioniert – und somit den Weg für komplexere und kritische Teile zu ebnen“, erklärt Dr. Karl-Heinz Dusel, Leiter Additive Fertigung Technologie bei der MTU. Denn neben der reinen Fertigungstechnik musste damals auch die gesamte Prozesskette neu aufgebaut werden.
Mischtest: In der Simulation eines additiv gefertigten Bauteils kann die Homogenität der Elemente im Metall bei additiven Fertigungsverfahren getestet werden.
Da die MTU zuvor Rohteile nur eingekauft und nicht selbst hergestellt hatte, konnten Dusel und seine Kollegen nicht auf vorhandene Prozesse, Verfahren und Strukturen für die Herstellung und Zulassung zurückgreifen. „Allein die Erarbeitung des benötigten Normsystems und die Ermittlung der Werkstoffdaten hat mehr als zwei Jahre in Anspruch genommen“, sagt Dusel. Darüber hinaus mussten auch neue Methoden zur Bauteilprüfung und Qualitätssicherung entwickelt und eingeführt werden. Seit der Prozess sicher steht, arbeitet die MTU daran, ihn schrittweise auch auf komplexere Bauteile und andere Triebwerkstypen zu übertragen. Aktuelle Projekte sind beispielsweise neue bionisch designte und damit besonders leichte Halterungen für Ölleitungen, sogenannte Brackets, und ein additiv gefertigter, steiferer und kostengünstiger Dichtungsträger. Dieser Innenring mit integralen Honigwaben soll künftig im Hochdruckverdichter verbaut werden. Die für die Triebwerksfunktion ebenfalls kritischen Brackets haben eine filigrane geschwungene Form.
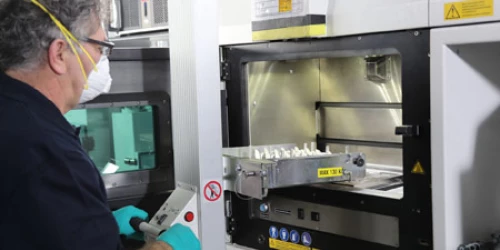
High-Tech Fertigungsverfahren im Einsatz bei der MTU: Additive Fertigung
Additive Fertigung: Als eines der ersten Unternehmen in der Triebwerksbranche stellt die MTU per 3D-Druck Serienbauteile her. Zum Video
Bionisch geformte Leichtbauteile
Ihr neues Design spare ein Drittel des Gewichts ein, ohne dass sich dies negativ auf Festigkeit und Dämpfungseigenschaften auswirke, so Dusel. Additive Bauteile tragen damit zu einer Gewichtsreduzierung des Triebwerks bei, was den Kraftstoffverbrauch und damit den Emissionsausstoß senkt. Bis es soweit ist, werde es aber noch eine Zeit lang dauern: „Solche hochausgelasteten Bauteile müssen in Triebwerkstests validiert werden“, erläutert Kraus. Parallel zu diesen Arbeiten prüfen der Experte und sein Team bereits die Machbarkeit von vollkommen neuen Bauteilen, die in der Next European Fighter Engine (NEFE) und in der kommenden Getriebefan-Generation zum Einsatz kommen könnten. „Für die nächste Generation Triebwerke können wir uns einen Anteil an additiv gefertigten Bauteilen von bis zu 15 Prozent vorstellen“, sagt der MTU-Mann. Ohne das neue Verfahren, soviel sei jetzt schon klar, werde künftig kein Triebwerkshersteller mehr auskommen.
Die MTU hat daher seit Anfang 2018 ihr Engagement im Bereich Additive Fertigung noch einmal intensiviert und eine eigene Abteilung dafür eingerichtet. „Mit der Bündelung aller Aktivitäten von der Auslegung über die Technologieentwicklung bis hin zur Serienfertigung in einer organisatorischen Einheit wollen wir unseren Vorsprung halten und weiter ausbauen“, sagt MTU-Technik-Vorstand Lars Wagner. Jürgen Kraus hat auch schon Ideen wie das geschehen kann: Im nächsten Schritt sollen Leichtbauteile neuentwickelt und gefertigt werden. Es geht um neue Designs, neue Bauteile – denkbar sind Lagergehäuse, Halterungen und Streben – und neue Werkstoffe. Vor allem bei der Herstellung komplexer Bauteile kann das Verfahren seine Stärke ausspielen. „Der additiven Fertigung gehört die Zukunft – jedes optimierte Bauteil macht die Triebwerke noch ein Stück effizienter.“