aviation
Blisk-Entwicklung: wie sich Schaufeln und Scheibe fanden
Rotorscheiben im Verdichter mit integrierten Schaufeln machen Triebwerke leistungsfähiger, leichter und sparsamer. Die Erfolgsgeschichte der Blisks begann im Eurofighter-Triebwerk EJ200.
Autor: Denis Dilba | 7 Min. Lesezeit veröffentlicht am: 01.05.2019
Autor:
Denis Dilba
studierte Mechatronik, besuchte die Deutsche Journalistenschule und gründete das digitale Wissenschaftsmagazin Substanz. Er schreibt über verschiedenste Themen aus Technik und Wissenschaft.
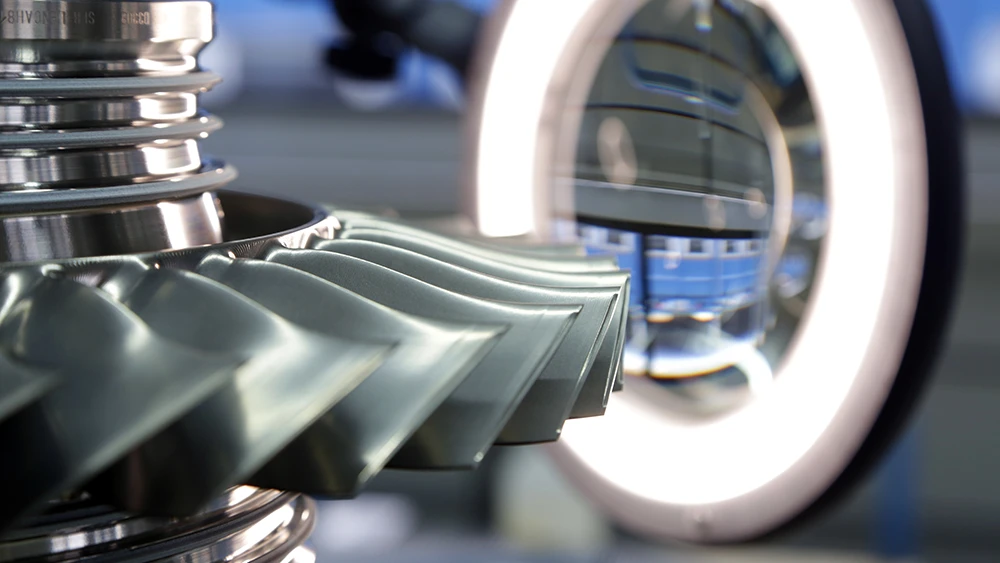
Schaufeln und Scheiben aus einem Stück, so genannte Blade Integrated Disks oder kurz Blisks, sind längst nicht mehr aus Flugtriebwerken wegzudenken. Die Hochtechnologie-Bauteile, die in Verdichtern zum Einsatz kommen, sind zum einen platzsparender und wiegen weniger als konventionelle Rotoren mit Einzelschaufeln, zum anderen ermöglichen sie bessere Schaufel-Aerodynamiken und verringern obendrein auch noch den Montageaufwand. Die Folge: Triebwerke werden insgesamt kompakter, leichter, und verbrauchen weniger Kraftstoff, was wiederum den CO2-Ausstoß senkt und der Umwelt zugutekommt.
- RB199-Entwicklung: das Triebwerk, mit dem alles begann
- Niederdruckturbinen: der Weg zum Weltklasse-Hersteller
- Blisk-Entwicklung: wie sich Schaufeln und Scheibe fanden
- Getriebefan: Wie der Zukunftsantrieb entwickelt wurde
- Additive Fertigung: Schicht für Schicht zum Bauteil
1995, als Arthur Schäffler den vier Eurofighter-Kunden zum ersten Mal den neuen Full-Blisk-Niederdruckverdichter für ihr Jet-Triebwerk EJ200 präsentierte, war die Begeisterung allerdings sehr verhalten. „Es gab sofort heftige Diskussionen“, erinnert sich der damalige Technische Direktor des EJ200-Konsortiums Eurojet an das Treffen in London. Die Vertreter Spaniens, Deutschlands, Italiens und Großbritanniens waren nicht grundlos skeptisch. Zwar kam eine erste Blisk schon damals in einem Hubschraubertriebwerk zum Einsatz. Die Blisks, die ihnen MTU-Mann Schäffler vorschlug, hatten aber einen erheblich größeren Durchmesser als das Helikopterbauteil. „Wir haben uns mit den EJ200-Blisks an vorderster Entwicklungsfront bewegt“, sagt der heute 81-jährige Ingenieur. Notgedrungen, denn um die Lebensdauer-Vorgaben für das EJ200 erfüllen zu können, mussten die MTU-Ingenieure auf die neue Technologie setzen. Die Umfangsgeschwindigkeiten der Rotoren in dem Jet-Triebwerk – und damit die Fliehkräfte – waren so groß, dass die Reibkorrosion bei der konventionellen Einzelschaufel-Technik zum Problem wurde. Dabei bilden sich auf den Oberflächen von Schaufelfuß und Rotornut kleine Grübchen, die zu Rissen und letztendlich zum Schaufelverlust führen können.
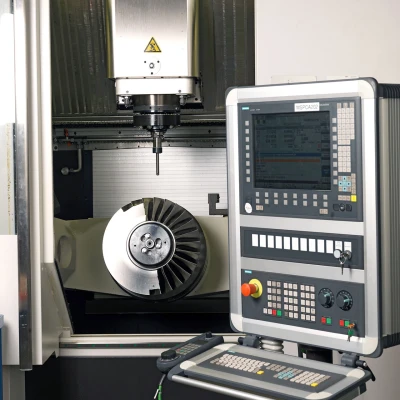
Momentaufnahme: Gut zu sehen, wie diese Blisk aus dem vollen Werkstück gefräst wird.
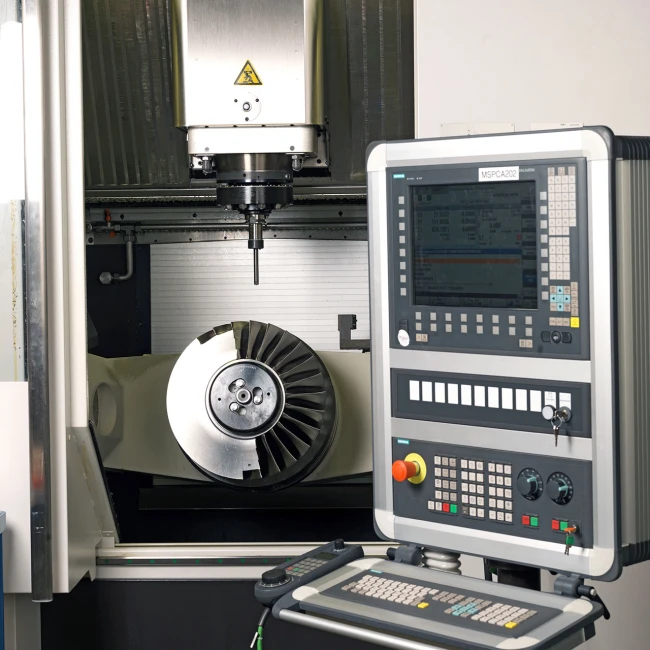
Momentaufnahme: Gut zu sehen, wie diese Blisk aus dem vollen Werkstück gefräst wird.
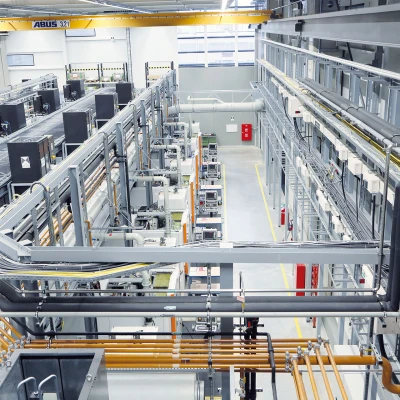
Bliskfertigung auf rund 10.000 Quadratmetern: In München betreibt die MTU eines der größten und flexibelsten Fertigungssysteme für die Produktion von Blisks für Hoch- und Mitteldruckverdichter weltweit.
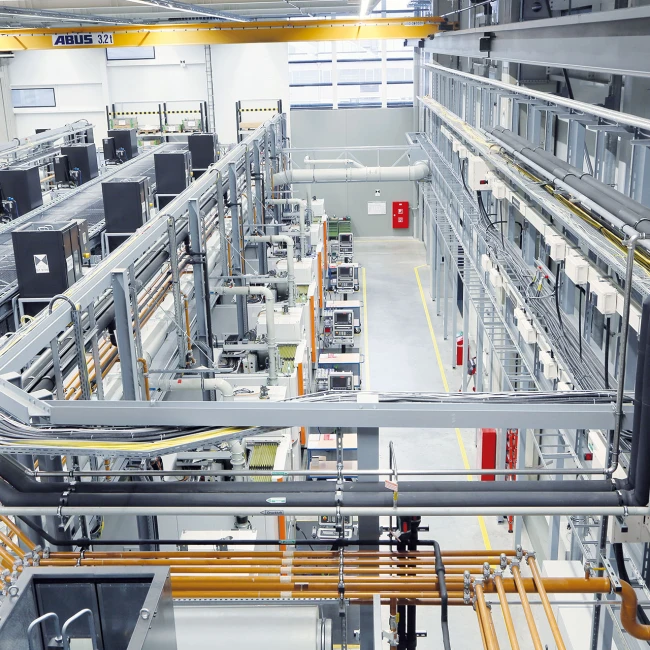
Bliskfertigung auf rund 10.000 Quadratmetern: In München betreibt die MTU eines der größten und flexibelsten Fertigungssysteme für die Produktion von Blisks für Hoch- und Mitteldruckverdichter weltweit.
„Die ersten 85 EJ200-Triebwerke, die im Hochdruckverdichter in Stufe 1 und 2 noch ohne Blisks ausgeliefert wurden, waren deshalb auf 400 Flugstunden Lebensdauer limitiert – 4.000 Stunden waren designseitig vorgesehen“, sagt Christian Köhler, der 1990 zur MTU kam und heute Chief Engineer des EJ200-Programmes ist. Die Blisks behoben das Problem und überzeugten die Kunden vollends von der integrierten Scheibe-Schaufel-Lösung. Bis Anfang 2019 wurden bereits 558 Jets mit den EJ200-Triebwerken ausgeliefert – weitere sind geordert. Die Blisk-Erfahrung der MTU ist dann weiter in einen Experimental-Hochdruckverdichter eingeflossen, der im Rahmen des Technologieprogramms HDV12 aufgebaut wurde und der ziemlich genau in das A318-Triebwerk PW6000 passte. „Damit konnten wir Pratt & Whitney unsere technologischen Fähigkeiten zeigen.“ Heute ist der Hochdruckverdichter mit einigen Änderungen im PW6000 im Serieneinsatz und für die Blisk-Technologie bedeutete dies der Sprung ins zivile Geschäft.
Spezielles Fertigungsverfahren für Blisks mit großen Schaufeln
Klassischerweise werden die Konturen der Schaufeln aus einer massiven Metallscheibe herausgefräst. Je weiter man sich im Triebwerk aber nach vorne bewegt – das heißt, dahin wo die Scheiben kleiner und die Schaufeln größer werden – desto unwirtschaftlicher wird das spanende Verfahren. „Viel teures Material landet hier im Ausschuss, das Fräsen dauert sehr lange“, so Köhler. Die bis zu 20 Zentimeter großen Schaufeln der ersten beiden EJ200-Niederdruckverdichter-Stufen werden daher einzeln geschmiedet und erst anschließend mit dem eigens dafür entwickelten linearen Reibschweißen mit der Scheibe vereint. Die Experten der MTU entwickelten noch ein weiteres Verfahren zur Bliskherstellung: „Mit dem Precise Electro Chemical Machining (PECM) können wir heute auch Blisks aus schwer schweiß- und spanbaren Nickel-Legierungen herstellen“, sagt Köhler. Bei dem Verfahren wird der Blisk-Rohling aus der Legierung unter Verwendung eines flüssigen Elektrolyten mit Hilfe elektrischen Stroms und eines 3D-Abformwerkzeugs gezielt aufgelöst.
„In den kommenden Jahren werden wir
hier bis zu 6.000 Blisks pro Jahr herstellen. Ohne die große Erfahrung, die wir uns über die Jahre erarbeitet haben, und ständiger Sorgfalt wäre das nicht möglich.“
Einer der Vorteile von PECM gegenüber dem Fräsen: Da das Bauteil dabei nicht berührt wird, verschleißen die Werkzeuge auch nicht. Darüber hinaus entfallen durch die wesentlich höhere Abbildungsgenauigkeit der chemisch-elektrischen Methode auch weitere Nachbearbeitungsschritte. Beides spart Kosten ein. Mit dem innovativen Präzisions-Verfahren stellt die MTU im Auftrag von Pratt & Whitney die fünfte und sechste Blisk-Stufe des insgesamt achtstufigen und in kompletter Bliskbauweise ausgelegten Getriebefan-(GTF)-Hochdruckverdichters her. „Zur Fertigung der Titan-Blisks der ersten vier Stufen des GTF-Hochdruckverdichters, die von der MTU konstruiert wurden, haben wir auf dem Münchner Werksgelände eine eigens dafür konzipierte Halle gebaut“, sagt Dr. Stephan Bock, Leiter Vorauslegung zivile und militärische Programme. Große Titan-Blisk-Schaufeln werden hier mittels linearem Reibschweißen einzeln mit der Scheibe verbunden und dann durch adaptives Fräsen angepasst, mittlere und kleine Blisk-Schaufeln aus dem Metall werden aus dem Vollen gefräst.
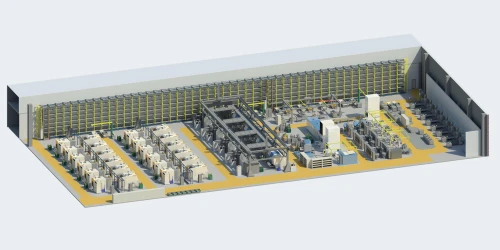
Automatisierte Bliskproduktion
Die Blisks für die Pratt&Whitney GTF™ Triebwerksfamilie werden in einer neu errichteten Fertigungshalle mit einem hohen Automatisierungsgrad produziert. Zur Interaktion ...
Bis zu 6.000 Blisks pro Jahr
Das sogenannte Kompetenzzentrum zur Fertigung von Titan-Verdichter-Blisks ist ein Paradebeispiel der Umsetzung des Industrie-4.0-Gedankens bei der MTU und weltweit die modernste Produktion dieser Art. Die Halle verfügt über einen hohen und in dieser Art weltweit einmaligen Automatisierungs-, Digitalisierungs-, Vernetzungs- und Selbststeuerungsgrad. Auch der hochfunktionale, energieeffiziente Hallenneubau entspricht modernsten Baustandards. „In den kommenden Jahren werden wir hier bis zu 6.000 Blisks pro Jahr herstellen“, sagt MTU-Experte Bock. „Ohne die große Erfahrung, die wir uns über die Jahre erarbeitet haben, und ständiger Sorgfalt wäre das nicht möglich. Die Prozesse müssen extrem stabil sein: Ein Fertigungsfehler an einer einzigen Schaufel kann das gesamte Bauteil unbrauchbar machen.“ Ausruhen könne man sich auf diesen Erfolgen aber nicht, weiß der Experte: „Wir arbeiten bereits an den Blisks der nächsten GTF-Generation.“