people
Using multiphysics simulations to boost efficiency
Fritz Hoffmeister is developing a multiphysics simulation model that will enable a complex electrochemical machining process to be digitally mapped in full for the very first time.
author: Thorsten Rienth | 3 mins reading time published on: 01.05.2019
author:
Thorsten Rienth
writes as a freelance journalist for AEROREPORT. In addition to the aerospace industry, his technical writing focuses on rail traffic and the transportation industry.
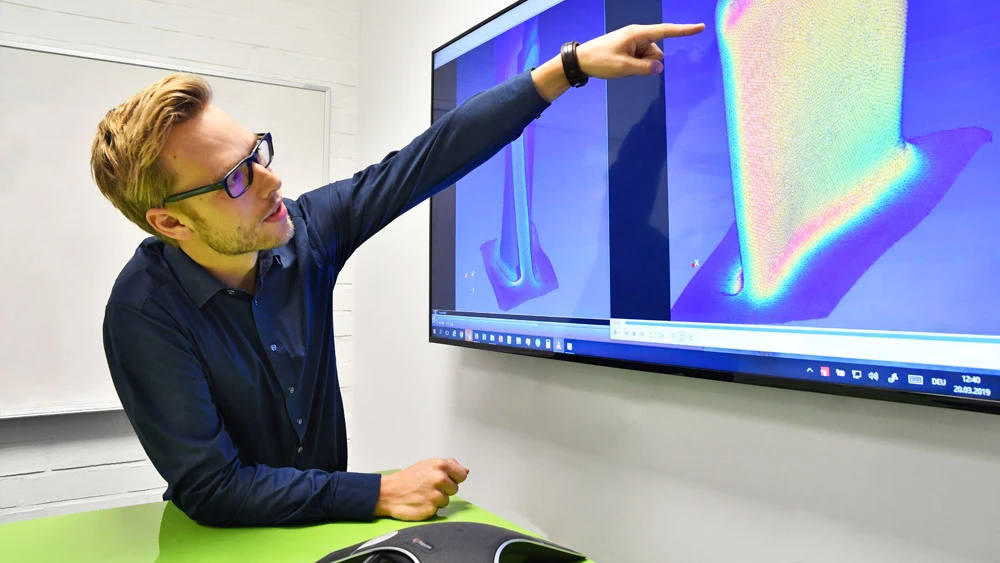
The screen shows two metal workpieces: a small, round one on the left, and a larger oblong-shaped one on the right. Small dots dart between them, resembling a swarm of wasps in a nest. While some take the shortest path, others go the long way—from the upper end of the oblong metal workpiece right around the back of the small round one, for instance. The dots in the swarm represent ions in an electric field.
- Using multiphysics simulations to boost efficiency
- A data scientist for the aviation industry of tomorrow
- Digitalization paves the way for predicting tool wear
- Managing digital transformation
- Digital tools help create new, efficient components
- Talking geometries: A common language for more efficient engine development
Acting as minute atom-sized shuttles, the ions dissolve metal from the workpiece. In this process of electrochemical dissolution, the tool used—which serves as the cathode—experiences essentially no wear, offering a revolutionary approach to machining the high-strength materials used to produce engine airfoils. Subtractive machining of such metals would result in tool wear so extreme that it would render the whole process too expensive.
Electrochemical machining, or ECM for short, offers up many questions: Which working current at which feed rate achieves the best geometric results? How does the current density affect the hydrogen generated in the process and the surface quality of the workpiece? And, what effect does the pressure of the electrolyte flow actually have on all that anyway? “In the past, we always had to rely on trial and error to answer these questions,” Hoffmeister explains.
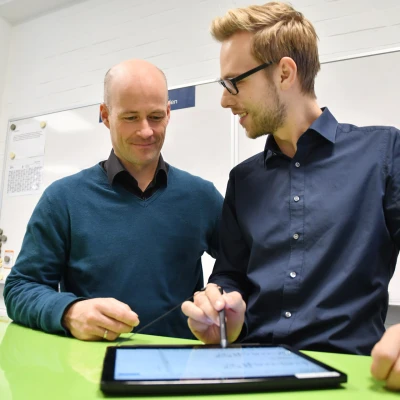
A simulation model is set to digitally map all the different interdependencies that occur in the electrochemical machining of engine airfoils.
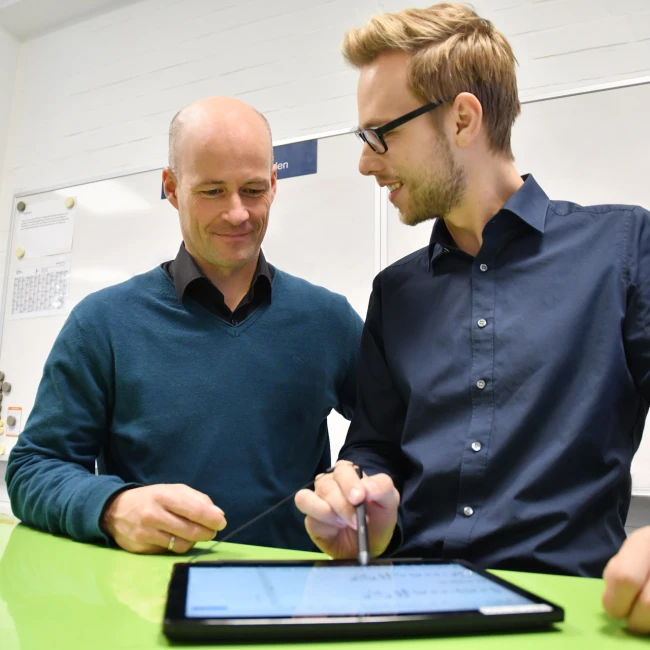
A simulation model is set to digitally map all the different interdependencies that occur in the electrochemical machining of engine airfoils.
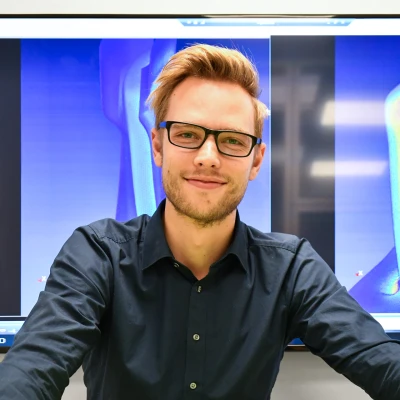
The 29-year-old wrote his master’s thesis on multiphysics simulation of the electrochemical machining process, and it was this paper that first brought him to MTU.
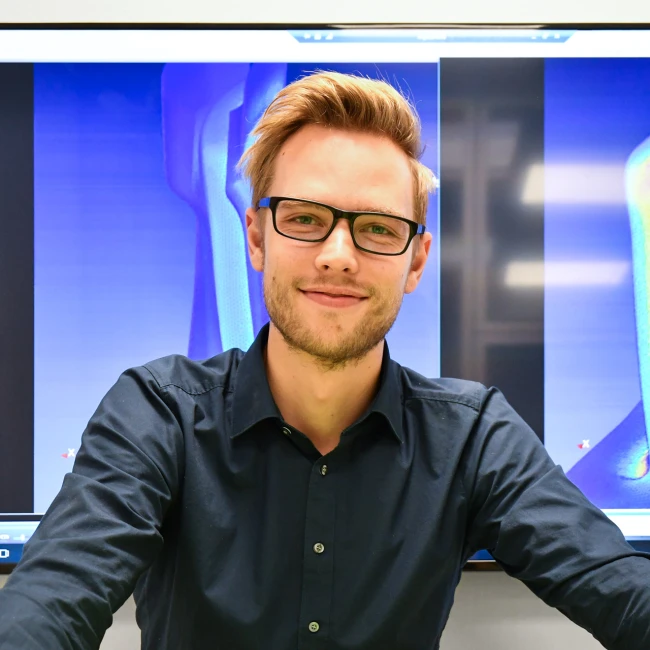
The 29-year-old wrote his master’s thesis on multiphysics simulation of the electrochemical machining process, and it was this paper that first brought him to MTU.
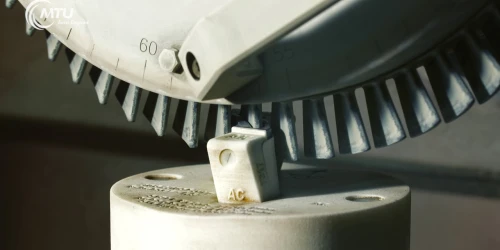
High-tech manufacturing process in use at MTU: Electrochemical machining
Electrochemical machining, or ECM for short, is a generic term that covers a group of various electrochemical metal removal processes. They all remove material based on the anodic dissolution of the metal during electrolysis. To the video
Out of necessity—because there was no other way. This approach commanded a huge amount of time and effort: Setting up and running the test, then measuring the part. Changing a couple of parameters. Starting again from the top, and then again from scratch for every new part. All the experience MTU has gained with this process naturally helps to speed things up, but Hoffmeister, who has just turned 29, is looking for a much shorter way to achieve the same results. He asked himself, “What if we were able to simulate all these interactions with micrometer precision?”
To answer that, Hoffmeister opted to take the multiphysics simulation route: “We’re developing a simulation model that incorporates chemical reactions, heat transfer, multi-phase fluid flow and the electric field. Essentially, by simulating current flow, we can calculate the material removal rate and consequently the final geometries with extreme precision. Put simply, we feed the geometries of a new component into a supercomputer and run through the iterations in a virtual environment. It already works well in 2D, but 3D simulation will be essential for industrial application. We’re working hard on that.”
Hoffmeister earned his bachelor’s degree in mechanical engineering before going on to complete his MSc in computational engineering and simulation at Munich University of Applied Sciences. During his studies, Hoffmeister worked at a company in the automotive industry, where he was responsible for calculating vehicle crash and airbag simulations—the latter using multiphysics. It was his master’s thesis—“Numerical simulation of 3D electrolyte flow and the fully coupled 2D multiphysics of the ECM process”—that brought Hoffmeister to MTU.
And it’s no coincidence that the title of his paper reflects exactly what Hoffmeister does at MTU today. As his master’s thesis was nearing completion, MTU offered him a permanent position at the company, which he gladly accepted.