innovation
Mastermind für die MTU-Produktion
Mit der Einführung eines einheitlichen Manufacturing Execution System (MES) soll die komplette MTU-Produktion zukünftig über ein Leitsystem dirigiert werden.
Autor: Thorsten Rienth | 4 Min. Lesezeit veröffentlicht am: 14.07.2021
Autor:
Thorsten Rienth
schreibt als freier Journalist für den AEROREPORT. Seine technikjournalistischen Schwerpunkte liegen neben der Luft- und Raumfahrtbranche im Bahnverkehr und dem Transportwesen.
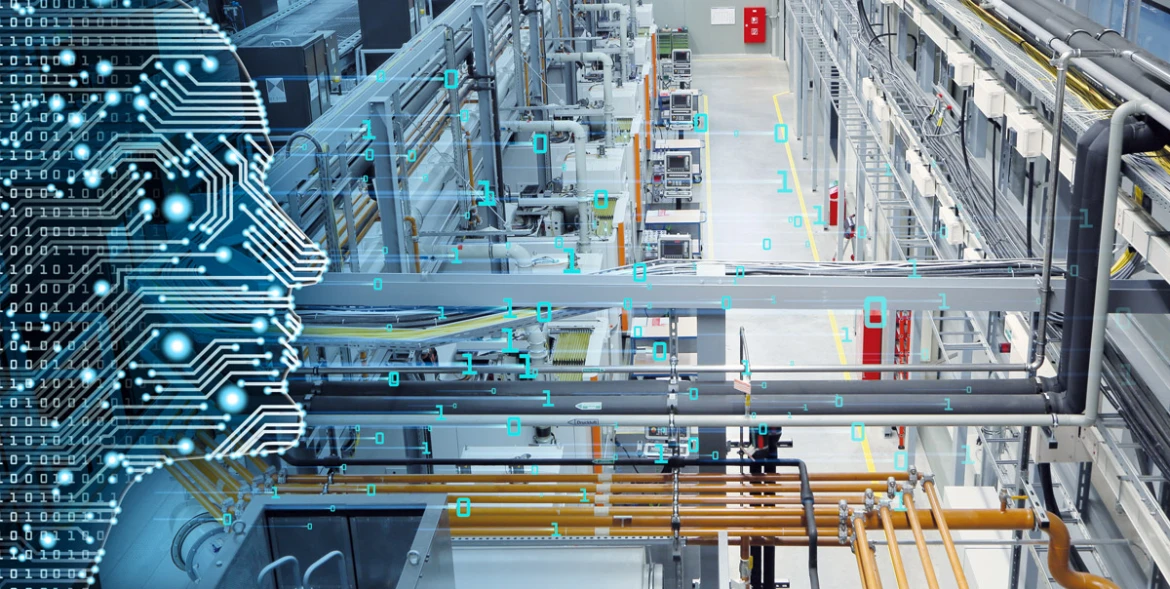
Die Grafik sieht aus, als hätte ein Kind bunte Bauklötze in einem Rechteck hin- und hergeschoben. Grüne, hell- und dunkelblaue, gelbe. Andere in grau oder rosa. Mal ist etwas Platz zwischen ihnen, mal liegen sie eng beisammen. Aber stets sind sie an den Rändern des Rechtecks orientiert. Natürlich hat hier kein Kind gespielt. „Jede Farbe steht für einen bestimmten Maschinenpark, für Fräs- und Schleifmaschinen, für Rüst-, Wucht- oder Lagerflächen“, erklärt Ralf Teufel, Leiter SAP-Manufacturing bei der MTU Aero Engines.
Das Rechteck, auf das er zeigt, stilisiert eine Produktionshalle bei der MTU in München. Hochkomplexe Blisks fertigt Deutschlands führender Triebwerkshersteller unter anderem dort. Das sind Schaufel-Scheiben-Rotoren aus lediglich einem einzigen Stück. Nicht nur sind sie platzsparender und wiegen weniger. Sie machen auch neue Design-Aerodynamiken möglich und verringern den Montageaufwand. Die Kehrseite dieser Medaille: Schier unzählige Arbeitsschritte sind dafür nötig. Ein ganzes Orchester an vor- und nachgelagerten Prozessen und Abläufen will organisiert sein. Hakt einer von ihnen, gerät das Orchester aus dem Ton. Es braucht einen Mastermind, der alles überblickt, der alles im Griff hat. Aber bisher gibt es noch keinen. Als Verantwortlicher für die IT-Systeme in der Fertigung ist Teufel dabei, das zu ändern.
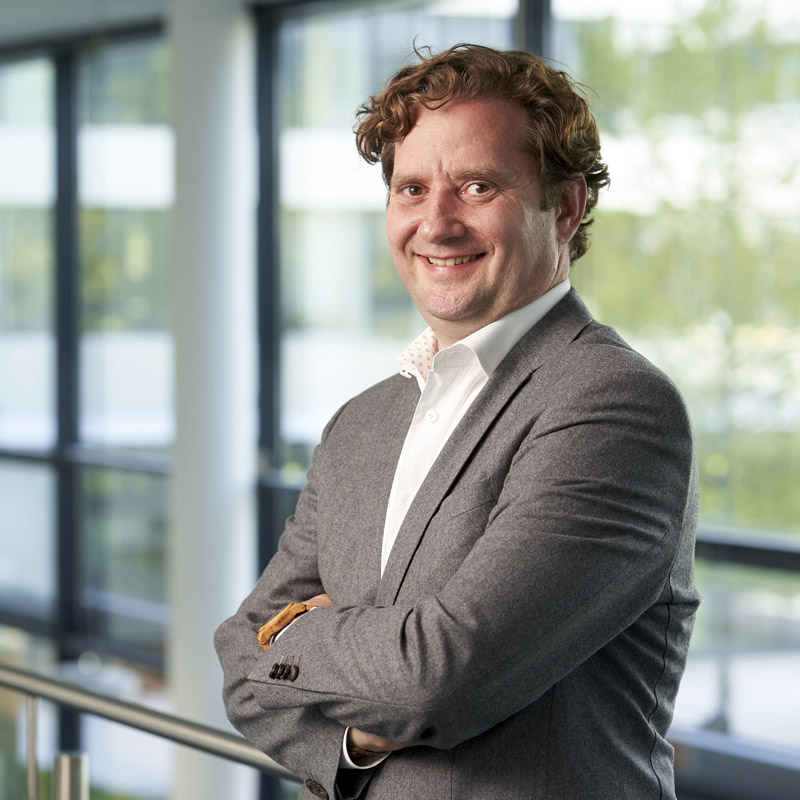
„Meine Diplomarbeit habe ich einst bei der MTU geschrieben – und zwar über die simulierte Pullsteuerung. Dann war ich an verschiedenen Positionen sowohl bei der MTU Polska als auch hier in München in der Supply Chain tätig. Jetzt kümmere ich mich IT-seitig um die MES-Einführung. Vieles fügt sich also nun für mich zusammen. Besonders spannend am MES-Projekt finde ich meinen Wissensgewinn: Ich bekomme enormen Einblick in alle Fertigungsbereiche. Im Gegenzug kann ich ihnen die Perspektive auf den konkreten Nutzwert der IT für ihre Anwendungen geben und an einer gemeinsamen Vision für die Zukunft arbeiten.“
Leiter SAP Manufacturing bei der MTU Aero Engines
Als vorgelagertes Testsystem starten zwei MES-„Piloten“
Management Execution System (MES) heißt der Mastermind. Als Produktionsleitsystem soll es einmal in der Ausbaustufe die gesamte MTU-Produktion dirigieren. Doch die Sache ist komplex. „Je mehr Bereiche und Menschen beteiligt sind, desto heterogener und individueller sind die Bedarfe“, sagt Teufel. „Es geht also um möglichst flexible Lösungen und darum, fachliche Gemeinsamkeiten der zahlreichen Arbeitsschritte zu erkennen und technische Standards zu schaffen.“ Deshalb wird das Großprojekt nicht einfach aufgebaut und eingeschaltet. Stattdessen soll das MES wachsen. Von der Maschine zur Linie. Von der Linie zur Halle. Von der Halle zur kompletten Produktion. Die Blisk-Produktionslinie startet als einer von zwei „MES-Piloten“ sprich: Als vorgelagertes Testsystem, mit dem die MTU ihr MES auf die Bedarfe und Anforderungen der Fertigungslandschaft hin ausgestalten und maßschneidern wird.
Teufel verantwortet das MES-Projekt aus der Digitalisierungsperspektive. Sein fachliches Pendant in der Produktionshalle heißt Bernhard Gürtler. Etwa 6.000 Stunden im Jahr laufen an dessen Linie alleine die Fräsmaschinen. „Ist die für den Arbeitsschritt passende Maschine verfügbar? Das aktualisierte Maschinenprogramm freigegeben und heruntergeladen? Die richtigen Rohteile, Vorrichtungen und Werkzeuge im Zulauf? Und steht auch der passend ausgebildete Mitarbeiter zur jeweiligen Zeit im Schichtplan?“ Natürlich: „Wir haben all diese Ressourcen auf dem Schirm. Wir haben Planungen verfeinert und Sicherungen etabliert.“
Aber der Organisationsaufwand bleibe enorm. „Eine entsprechende MES-Automatisierungsplanung könnte uns da einiges abnehmen und obendrein Stillstandzeiten minimieren.“ Zum Beispiel, weil Bauteil und Vorrichtung zwar an der Maschine sind – aber erst noch ein aktualisiertes Maschinenprogramm aufgespielt werden muss. Auf der anderen Seite könnte das MES für mehrtägige Fertigungsschritte einen teilautomatisierten Dauerbetrieb in greifbare Nähe bringen. „Dann könnten wir, übers MES entsprechend abgesichert, Maschinen vorrüsten und die Maschinenprogramme beispielsweise übers Wochenende abfahren“, skizziert Gürtler.
Ein Toolset für möglichst alle Fertigungsanwendungen
Bislang kommen, historisch gewachsen, MTU-weit zahlreiche verschiedene Fertigungssteuersysteme und Tools zum Einsatz. „Je differenzierter die Lösung, desto höher der Supportaufwand“, sagt Teufel. „Deshalb wollen wir im nächsten Schritt ein einziges Toolset etablieren für möglichst alle Fertigungsanwendungen.“ Mit gleichen Logiken und gleicher Architektur, mit wiederverwendbaren Funktionen und einheitlichen Schnittstellen. Und damit unkompliziert erweiterbar, wenn es neue Fertigungstechnologien oder Triebwerksprogramme einmal nötig werden lassen.
Mehrere Projektteams und Expertengruppen arbeiten daran, fachliche Gemeinsamkeiten zu erkennen und technische Standards für einen möglichst breiten Strauß an Anforderungen zu definieren. Eine „Riesenherausforderung“ nennt Teufel das Vorhaben. „Von der Maschine selbst geht es über die Maschinenanbindung hinauf zum Hallenbetrieb – und von dort wieder zurück zur Feinplanung.“ Für jede Ebene müsse eine standardisierte Lösung entwickelt werden, die wiederum mit allen anderen Ebenen verbunden ist. „Dabei wollen wir die Logik einer kompletten Automatisierung abbilden – uns aber bei den Anwendungen und der Technik nicht von unserer bisherigen Flexibilität verabschieden.“
Mammutaufgabe: Ralf Teufel und Bernhard Gürtler stehen bei Einführung eines einheitlichen Manufacturing Execution System im engen Austausch.
Perspektivisch soll auch die deutlich variantenreichere „MRO“ auf MES-Basis laufen
Im Anschluss an die Pilotprojekte soll das MES in der Serienfertigung für alle ähnlichen Anwendungsfälle mitbetrachtet und angeboten werden. Über verschiedene Anforderungen aus Automatisierungsprojekten soll schließlich flächendeckend in der Fertigung von Neuteilen ein neuer Standard eingesetzt werden. Perspektivisch soll aufs Triebwerks-Seriengeschäft auch die deutlich variantenreichere Instandsetzung auf die MES-Basis wechseln. Auf dem Weg dorthin gilt eine Regel, die auch von den Bauklötzen bekannt sei, sagt Teufel. „Mit jedem Stein wird die Sache diffiziler.“